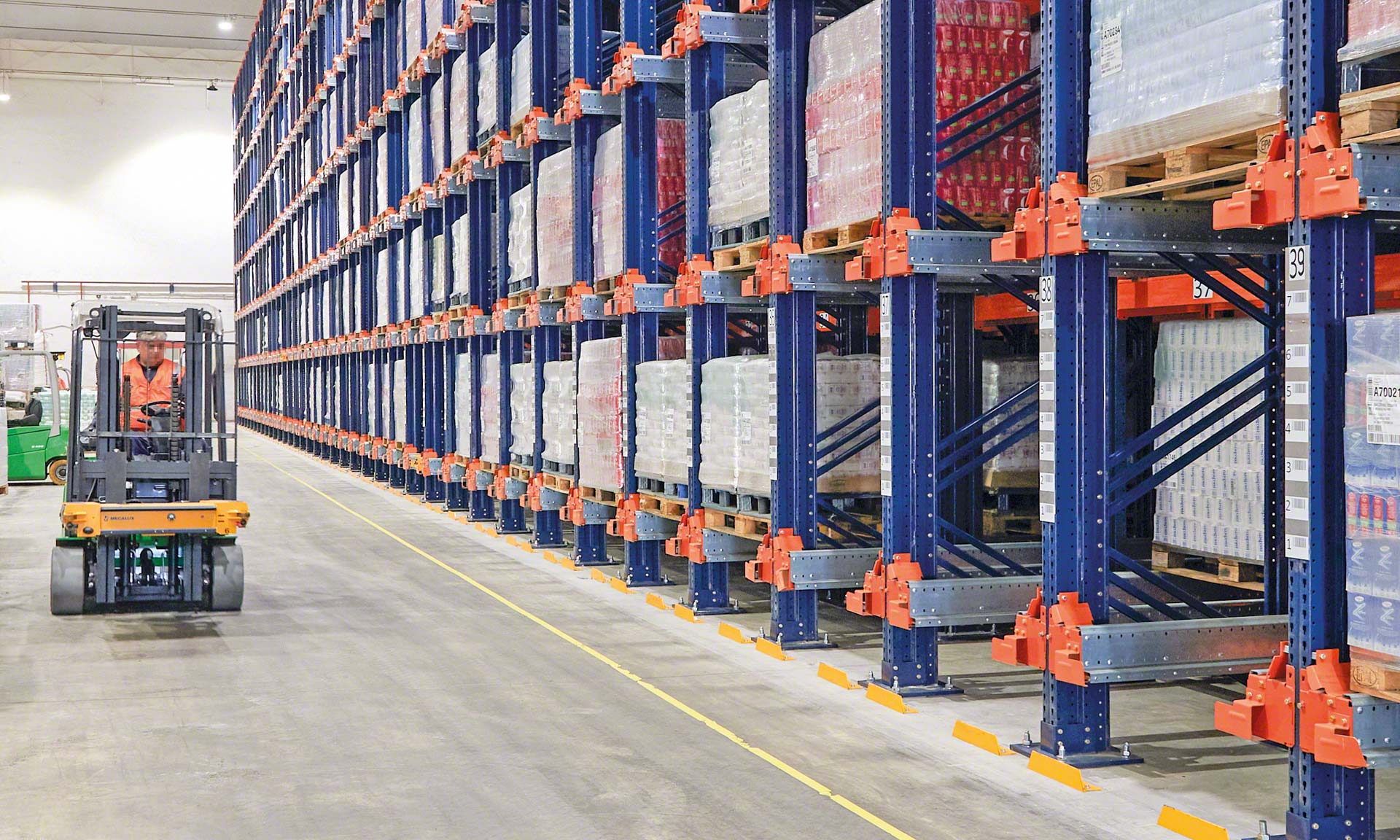
Sugar and sweetener distributor Eridania boosts capacity by 180%
The company, a leading Italian sugar and sweetener distributor, has installed the Pallet Shuttle system to store and ship 1,750 pallets a day and expand capacity by 180%.
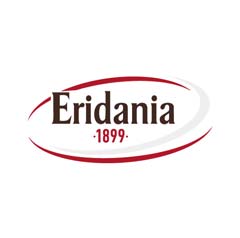
Eridania, a leading distributor of sugar and sweetener in Italy, has modernised the logistics operations of its production plant in Russi. The company has installed the semi-automated Pallet Shuttle to ship 1,750 pallets a day carrying finished goods and increase capacity by 180%.
Eridania: natural, additive-free products
Founded in Genoa in 1899, Eridania is a leading distributor of sugar and sweetener in Italy. Based in Bologna, it has a modern sugar packing plant in Russi, where it packages over 130 million tonnes of product every day. Sustainability and productivity are key pillars of the company’s business development strategy. Eridania is part of the Cristal Union group, one of Europe’s top distributors of sugar, alcohol and bioethanol, with more than 2,500 clients in 100 countries.
CHALLENGES
|
SOLUTION
|
BENEFITS
|
---|
Eridania, a leading distributor of sugar and sweetener, has modernised its facility in Russi (northern Italy) to sustain the heightened pace of work seen in recent years. The company is currently the number one sweetener brand in Italy. It boasts a 29% share of the overall sweetener and sugar market and a notable 34% share in the sugar-only segment.
One thing that characterises a food business like Eridania is the need to keep products in perfect condition. The 200 SKUs it stores call for effective turnover management. “For us, it’s essential to organise our goods in line with the FIFO method and store them taking into account their best-by date,” says Alessandro Sabbadini, Head of Warehousing, Procurement and Shipping at Eridania.
In outfitting its warehouse, Eridania knew it needed a high-density storage system. “We had several logistics requirements. They included optimising storage space, mainly in height and reducing material handling times. And it was impossible to meet these logistics demands with drive-in racking,” says Sabbadini.
After assessing different options, Eridania and Mecalux concluded that the best option would be the semi-automated Pallet Shuttle. This automated storage and retrieval system (AS/RS) features an automatic shuttle car that moves pallets inside the racking.
One of the Pallet Shuttle’s advantages is its ability to maximise storage space: “We can house large quantities of products — significantly more than when we stacked pallets on top of each other. We’ve gone from storing 2,000 to 5,600 pallets,” says Sabbadini.
Another priority for Eridania was earthquake protection: “The AS/RS is engineered to support the very heavy products we manage, considering the seismic activity typical of our region and the associated forces the structure has to withstand,” says Sabbadini. The seismic racks adhere to the highest earthquake protection design standards for these types of structures. They are reinforced to endure any potential ground motion in the region.
Semi-automated, high-density storage
With the semi-automated Pallet Shuttle system, Eridania has expanded storage capacity by 180% in the same space. To optimise the existing surface area, Mecalux installed a massive block of racking measuring nearly 1,000 m². The racks’ 14.5-metre-deep channels can accommodate 5,355 pallets, each weighing 1,000 kg.
“We’ve allocated the Pallet Shuttle system to storing finished goods ready for distribution, namely pallets containing sugar and sweetener. Every day, we ship a large number of products to our clients, primarily mass-scale distributors,” says Sabbadini.
In addition to maximising space, the Pallet Shuttle system streamlines the flow of goods. Operators position the electric shuttle car at the entrance of any channel and the vehicle inserts or removes the pallets with complete autonomy. “We’re thrilled with the new AS/RS. It loads and unloads the sugar and sweetener with remarkable speed,” says Sabbadini. This solution has enabled the Italian company to increase the number of hourly storage and retrieval cycles performed, cutting lead times.
The automatic shuttle enables the putaway of 750 pallets a day, equivalent to approximately 450 tonnes of sugar and sweetener. Likewise, the system expedites the daily shipment of 1,000 pallets carrying finished products to Eridania’s clients. To execute all Pallet Shuttle movements and functions, operators use a tablet with an intuitive interface.
Logistics operations prepared to sustain production
Eridania’s new AS/RS in Russi is the epitome of efficiency in the sugar distribution sector. The Pallet Shuttle system has increased storage capacity by an impressive 180%. Moreover, automation has provided the agility and speed necessary to support the daily distribution of 450 tonnes of sugar and sweetener.
The Pallet Shuttle is a high-density storage solution tailored to foster Eridania’s growth and business expansion in the coming years.
With the Pallet Shuttle system, we’ve streamlined management of sugar and sweetener. Plus, we’ve reduced goods handling times. We chose Mecalux because of its positive references and excellent reputation in the market.
Ask an expert