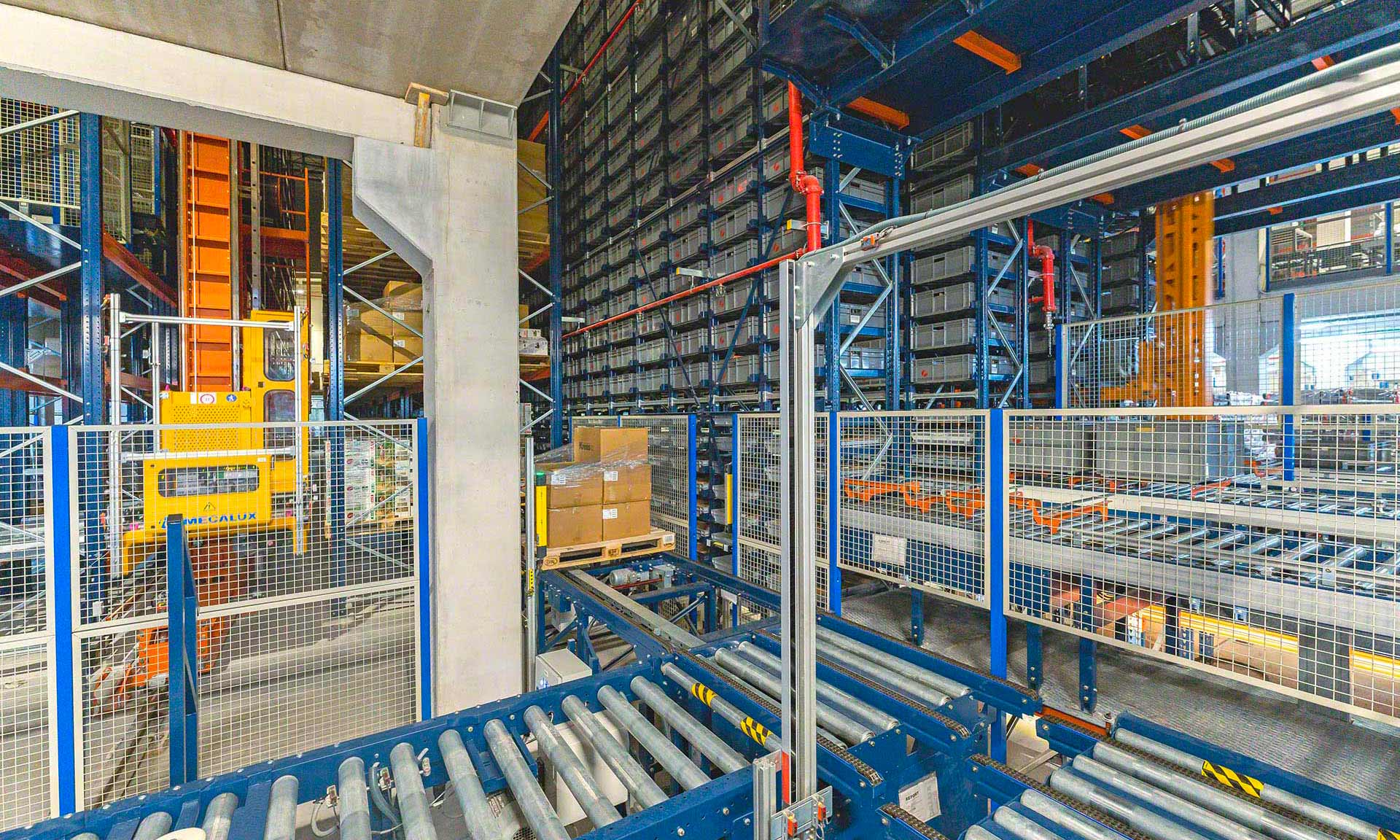
Aghasa Turis: tripled storage capacity and a 27% increase in prepared orders
Automation has made picking 15% faster in the new Aghasa Turis centre
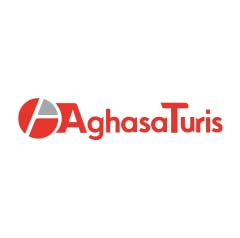
To successfully break into the world of e-commerce and serve all its customers without delay, Aghasa Turis has moved to a new logistics centre in Leganés, near Madrid, Spain. There, during the initial phase, it has tripled its storage capacity and raised the number of orders prepared by 27%. To boost efficiency and speed in storage and picking tasks, the hardware and industrial supplies company has outfitted its centre with the latest technology. Likewise, the Easy WMS warehouse management system from Mecalux constitutes a comprehensive logistics solution for the firm, as this WMS provides simultaneous and synced supervision of the two automated solutions (one for boxes and another for pallets) and of the area with pallet racks.
Move to a new logistics centre
Aghasa Turis, which dates back to 1940, is a hardware and industrial supplies business with over 25,000 SKUs in stock from leading brands such as Olfa, WITTE, Hailo and Eagle, among others.
Darío Alonso, General Manager at Aghasa Turis, affirms, “We consider ourselves a link in the supply chain; this is very much ingrained in us. We have to be up to the task cooperating vertically with our suppliers and customers, but also in a cross-cutting way with our logistics partners, service companies, carriers, etc. At Aghasa Turis, both collaboration and integration are fundamental.”
In recent years, the firm has adapted to changes in consumer trends, promoting online sales and an omnichannel strategy. Aghasa Turis’s General Manager explains, “We don’t sell online as such; instead, we enable customers from more traditional sectors to do so. We’ve been in business for over 80 years, and during that time, we’ve never stopped changing and reinventing ourselves to be able to continue working with our customers.”
Aghasa Turis was forced to revamp its entire logistics system when its sales rose. Its old logistics centre in Boadilla del Monte (Madrid), equipped with an automated system for boxes and an area with pallet racks, lacked the storage capacity to house all the SKUs. Determined to improve its logistics operations, Aghasa Turis moved to a new, larger logistics complex (8,000 m2) in Leganés, just a few km from its former centre. With the new facility, it has already tripled its storage capacity, and it plans to double its current capacity.
The company’s General Manager was adamant that the warehouse be fitted with cutting-edge technology to improve flexibility and immediacy, as well as efficiency in order picking. Aghasa Turis’s entire logistics strategy revolves around a single objective: to deliver 95% of the orders in less than 24 hours.
“You can’t manage a facility with 25,000 SKUs without digitising it completely or automating it as much as possible. More and more, we need that effectiveness that technology brings us. I can’t imagine it being done any other way,” contends Darío Alonso.
Logistics centre characteristics
The logistics centre consists of two attached automated storage and retrieval systems (AS/RS): one for pallets with 1,708 locations and another (miniload) for boxes with capacity for 11,024 unit loads. A space next to the AS/RS for boxes has been set aside for future expansion when required by the business. Just beside this area, Mecalux has set up a manual storage zone with pallet racks and picking shelves.
The sizes of the two automated systems are identical: 52 m long and 22 m high. The difference lies in that the solution for pallets has a single aisle with double-deep racking (two pallets are placed in each location), and the solution for boxes features two aisles with single-deep shelving.
Both systems are divided into two floors with different operations. The upper floor (ground level) is where entries take place (pallets are received and boxes set to enter the miniload system are filled). On the lower floor (at a level of -3.4 m), orders are prepared and dispatched.
The AS/RS for boxes houses small products (primarily hardware and tools), while the solution for pallets holds larger goods (such as hoses and irrigation and gardening materials). Meanwhile, the picking shelves are reserved for smaller, high-turnover items, and the pallet racks accommodate bulkier products that cannot be stored on pallets, such as ladders.
Aghasa Turis’s new logistics centre has increased the number of orders prepared by 27%, just what it has been designed to do. The centre has three distinct working areas in which this operation is carried out: picking shelves, a pick station in front of the AS/RS for pallets and another two pick stations near the miniload system.
Additionally, the company has implemented Mecalux’s Easy WMS warehouse management system to control its 25,000 SKUs in real time. This software, connected to Aghasa Turis’s Kriter ERP, organises all processes taking place at the logistics centre — both automated and manual — to achieve the greatest possible productivity. “After analysing other WMSs, we saw that Mecalux’s Easy WMS met all our needs. This WMS is perfectly integrated with the warehouse control systems (WCS) for the AS/RS,” highlights Darío Alonso.
Upper floor: entries
Here, palletised goods are unloaded from the delivery lorries. Immediately afterwards, operators separate the products and sort them by SKU, size and turnover to determine whether they should be stored in one of the automated solutions or on the manual racks.
Easy WMS then decides on a location for each item. For example, in the AS/RS, high-consumption products are placed on the ends of the racks to streamline their entries and exits. For pallets that need to be broken down, a working area has been set up for operators to place the goods in boxes, which will eventually be put on the incoming conveyor of the miniload system. Operators follow instructions from Easy WMS to perform this task more quickly and without making mistakes.
This floor also has a direct sales and collection counter. This area stores orders to be directly picked up by customers at the warehouse.
Lower floor: picking
Orders are prepared on the lower floor of the Aghasa Turis centre. To dispatch them in less than 24 hours, several systems that facilitate picking have been set up in five different areas:
- Pick stations for the AS/RS for boxes. There are currently two stations where 11 orders are simultaneously prepared, as well as a space set aside for a third workstation.
- Pick station for the AS/RS for pallets. Located in front of this system, operators can prepare up to seven orders at the same time here.
- Manual picking shelves. These offer direct access to the goods, which is indispensable for easy product handling.
- Live channels on the lower level of the AS/RS for pallets equipped with a pick-to-light system.
- Two areas with manual live channels for boxes and pallets, also fitted with pick-to-light devices.
At the pick stations for the AS/RS for boxes and pallets, the operation itself is very similar because the orders are prepared according to the product-to-person method. As the goods arrive automatically at the workstations by means of a screen, Easy WMS shows operators how many items to pick in addition to the remaining quantity of product, thus tracking inventory in real time. Operators then sort the items they have removed into boxes (each corresponding to an order) located behind them. To facilitate their work, put-to-light devices have been installed. These show operators the boxes in which they should place each item and the quantity required. This way, orders are prepared quickly and without error.
At the manual picking shelves and live channels of the AS/RS for pallets, meanwhile, picking is carried out in line with the person-to-product criterion, whereby employees follow instructions from Easy WMS via radiofrequency scanners. Using a cart with four locations (each associated with an order), operators travel along the manual picking shelves or the live channels of the AS/RS for pallets, picking the goods and sorting them into orders. These carts are also outfitted with put-to-light technology to simplify and expedite the work of the operators. Aghasa Turis’s General Manager enthuses, “Thanks to the help of Easy WMS and the pick- and put-to-light systems, in this first phase, we’ve increased our picking speed by 15%. With the adjustments being made and the start-up of the second phase, which we expect to be operational by 2022, we’ll triple our order prep capacity compared to our figures for 2019.”
Furthermore, it is possible for an order to be made up of items from different areas in the facility. In that case, Easy WMS directs them to be prepared separately in each particular zone; they are then brought together and consolidated in front of the loading docks (there is one dock on each level).
Lastly, the centre has a multitude of screens located throughout that logistics managers can use to check the order status information provided by Easy WMS (number of pending orders, number of orders being prepared and where, etc.). This allows managers to plan tasks in advance and make decisions that improve picking.
“We need software that’s robust, flexible, scalable and ready to interface with our systems and those of other companies. Easy WMS meets all these requirements and is integrated with the various areas in our warehouse,” notes Darío Alonso.
Packaging and dispatch
As critical operations in the Aghasa Turis facility, packaging and dispatch have been organised and planned accordingly. Two work areas have been set up:
- Orders containing small items. These orders, prepared at the pick stations for the automated storage systems or in the manual picking zones, are sent to an area comprising 17 live conveyor channels. Boxes that make up a single order are placed in one of the channels and then moved to one of the four packing and labelling stations.
- Orders containing large items. Prepared in the live channels at the lower level of the AS/RS for pallets or on the manual pallet racks, these orders are packaged and labelled in a reserved area near the loading docks.
Whichever the case, Multi Carrier Shipping Software intervenes in the packing process. This extension of Easy WMS automates order dispatch management.
Easy WMS tells the operators which items to pack, and the workers place them inside the cardboard boxes according to their weight and size. Thus, for example, if an order contains multiple items, they can be placed in a single box for easy transport or in various boxes if appropriate. Multi Carrier Shipping Software generates a packing list specifying the number of items each order contains.
The vast majority of orders prepared at the Aghasa Turis logistics centre consist of small items, so the packaging and labelling process is much more frenetic in the area with live conveyor channels. To facilitate the tasks of the operators in this zone, each channel is fitted with a pick-to-light device that shows them the number of boxes to retrieve.
It should be noted that certain live conveyor channels are used exclusively for orders that customers have placed online and are subject to drop shipping. This is because these products have to be packed in customer-specific boxes and with packaging adapted to direct shipment to the end customer. Moreover, these constitute priority orders that must be distributed with very detailed traceability.
Once the packaging and labelling process is finished, these orders are sent to the loading docks, where they are grouped with items to be delivered on the same run.
Aghasa Turis works with three carriers charged with delivering the orders: GLS, DHL and Correos Express. Multi Carrier Shipping Software knows in advance which agency will distribute each order. Accordingly, it automatically generates and prints a label for each package. This label includes the tracking number so that customers can know the status of their orders in real time.
Logistics for continued growth
Aghasa Turis has benefited from a complete logistics solution comprising various AS/RS, pallet racks, and automated management, all of which has increased the number of orders prepared by 27%. Easy WMS has helped to speed up picking and strictly monitor other operations and the 25,000 SKUs in stock.
Aghasa Turis’s eagerness and drive to improve its supply chain have resulted in an efficient, high-tech logistics centre capable of preparing and dispatching 95% of orders in less than 24 hours and without error, thus satisfying all its customers.
According to Darío Alonso, “New technologies bring about more and more changes and cause everything to be faster, so our logistics operations need to be prepared for this. It’s in our DNA. We can’t afford to stay in our comfort zone; we need to think about what tomorrow will bring and be ready to take on any challenge.”
There’s a story behind why we chose to entrust Mecalux with this project. The first warehouse my father ever set up had Mecalux racking. Obviously, it’s a logistics partner with considerable experience equipping all kinds of logistics facilities, from small warehouses to large-scale clad-rack buildings.
Advantages for Aghasa Turis
- Tripled storage capacity: the storage solutions already installed in this first phase have tripled the storage capacity compared to the former warehouse.
- Comprehensive solution: in a single logistics centre, Aghasa Turis has an AS/RS for boxes and another for pallets, pallet racks, and a WMS capable of managing the 25,000 SKUs in addition to all the operations carried out.
- 15% faster picking: automation has expedited picking by 15%, making it possible to deliver 95% of orders in less than 24 hours.
- 100% stock visibility: the WMS lets Aghasa Turis know its inventory and order status in real time (number of orders prepared, pending completion, to be dispatched, etc.).
AS/RS for pallets | |
---|---|
Storage capacity: | 1,708 pallets |
Unit load dimensions: | 800 x 1,200 mm |
Max. unit load weight: | 1,000 kg |
System height: | 22 m |
System length: | 52 m |
Gallery
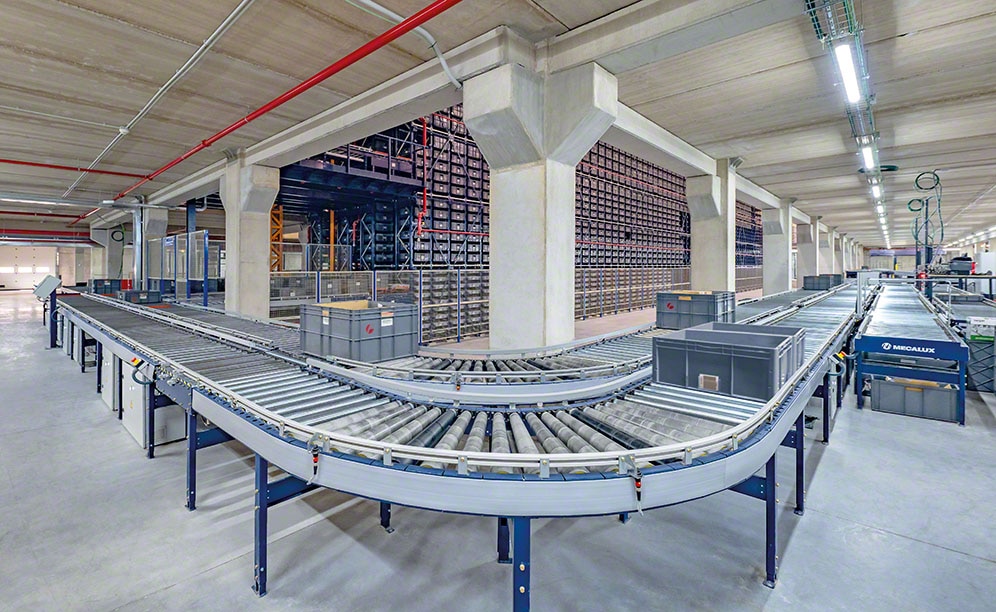
New Aghasa Turis logistics centre with two automated storage solutions
Ask an expert