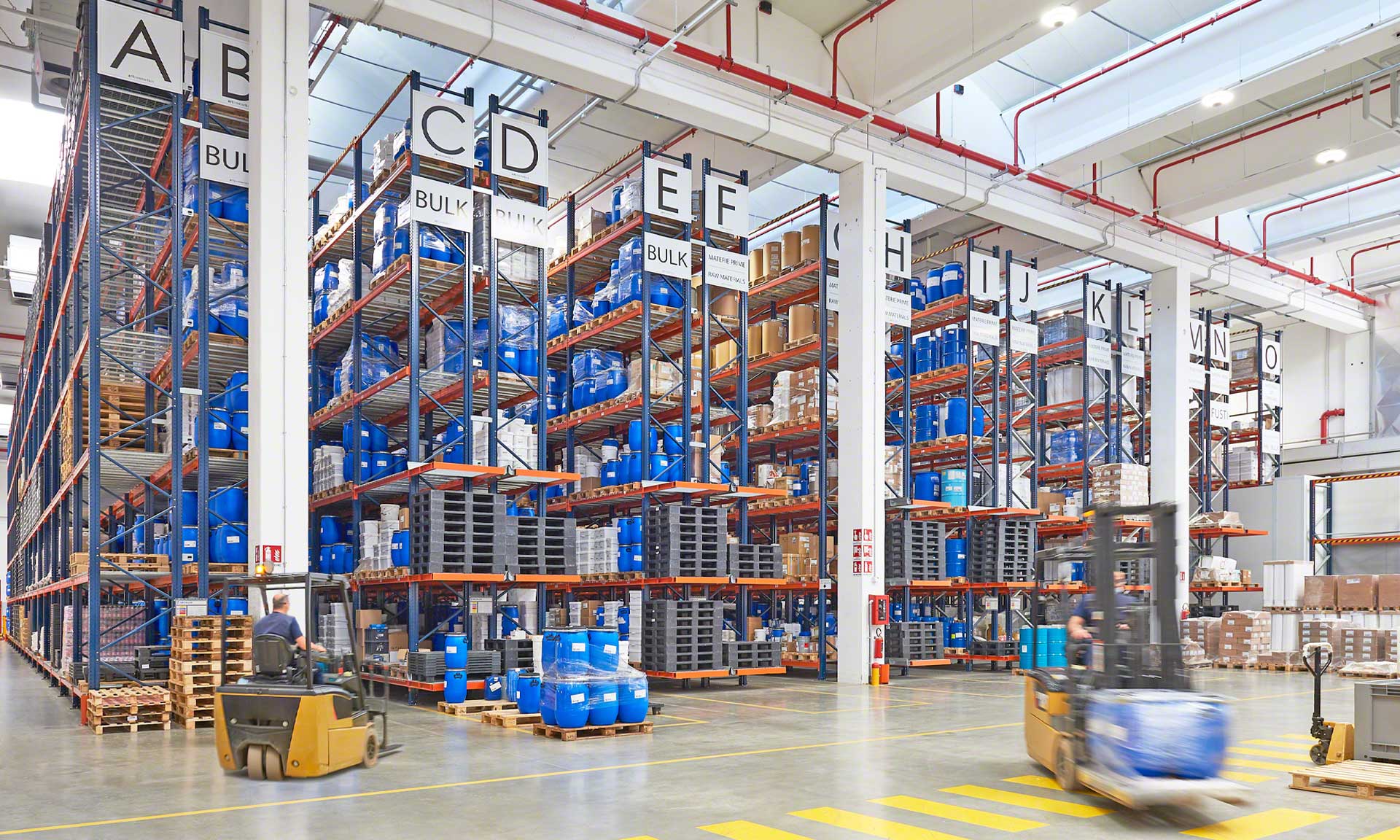
Art Cosmetics: makeover for logistics in expansion mode
The warehouse's main operation consists of supplying the production lines just in time.
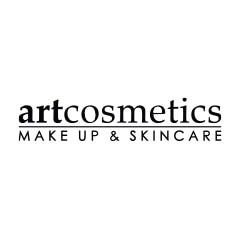
Art Cosmetics, a leading Italian makeup and skincare manufacturer, has opened its new headquarters in Fornovo San Giovanni to absorb increased production. The facility, equipped with Mecalux pallet racking and live pallet channels with rollers, houses approximately 4,800 pallets containing raw materials.
Art Cosmetics, a leading makeup and skincare manufacturer, strives to offer its customers around the world the best possible service. Recently, the company opened its new headquarters in Fornovo San Giovanni, Italy. There, to absorb the increase in production, it implemented a warehouse for receiving, storing and picking raw materials and bulk cosmetic products. Mecalux pallet racking and live pallet channels with rollers hold approximately 4,800 pallets. The facility’s main operation consists of supplying the production lines just in time.
World-renowned Italian cosmetics
Art Cosmetics, a leading makeup and skincare manufacturer, is headquartered in Italy’s iconic Cosmetic Valley, the golden triangle of cosmetics and makeup, featuring the cities of Milan, Bergamo and Crema. This major beauty industry hub plays a fundamental role in the global market thanks to its innovative character, fostering creativity supported by technical and scientific expertise.
For the business, founded in 1990, cosmetics are much more than skincare creams and beauty lotions: like poetry or painting, they are a form of artistic expression.
Carlo Fanzaga, Logistics Manager at Art Cosmetics, says: “Continuous innovation and the pursuit of perfection are our company’s two main strengths. We care deeply about the environment, people’s well-being, and health and safety in the workplace. As a result, more and more customers are rewarding us with their loyalty, helping us to advance towards the top of the world rankings among businesses in our industry."
Art Cosmetics has several production plants between the cities of Fornovo San Giovanni and Mozzanica in Italy’s Bergamo province. These centres are equipped with warehouses containing the components needed to manufacture semi-finished goods and to put the finishing touches on end products. Additionally, in the Fornovo San Giovanni facility, Art Cosmetics has a logistics centre that houses around 5,000 pallets. They contain the components used in production as well as finished products ready to be sent to customers and marketing offices in the US and Korea.
Logistics gets a makeover
Art Cosmetics recently opened its new headquarters in Fornovo San Giovanni, occupying a surface area of about eight acres. The centre manufactures cosmetics and skincare products and researches environmentally sustainable solutions.
Just next to the production lines is a space reserved for the storage of raw materials used to make cosmetics. Fanzaga says that the company’s main logistics need was to “make the absolute most of the space to accommodate more goods. At the same time, we wanted to manage our raw material and bulk products more efficiently.”
The day-to-day operations of this warehouse are as follows: it receives about 50 pallets sent by the company's suppliers. Operators identify them, label them, check their quality and store them. Meanwhile, orders are picked and sent to the production lines (another 50 pallets on average per day). Art Cosmetics’s logistics processes are highly complex: the business manages approximately 6,000 SKUs of different characteristics, volumes and turnovers.
Over two work shifts, this facility’s 10 operators are tasked with coding incoming materials. Once they pass quality control, the employees store them or perform the relevant picking operations as indicated by the warehouse management system (WMS). The main goal is to supply the production lines with raw or bulk material as required. When doing so, speed and timeliness are critical.
Any delay in the transfer of goods to production could have serious consequences for the company. Therefore, Art Cosmetics' priority is to expedite order processing taking into account the delivery times specified by customers.
With all these requirements in mind, Mecalux outfitted the warehouse with two different storage solutions that bring the speed the that company needed: pallet racking and live pallet channels with rollers.
Pallet racking: stock control
“The Mecalux pallet racking is working out really well for us. For starters, it’s helped us create an optimal space for performing many operations efficiently,” says Fanzaga.
The racks, which stand 10 m tall by 50 wide, adjust perfectly to the available space in the facility. They have been strategically distributed to safely store the largest possible number of pallets: 4,800, with a maximum unit weight of 1,000 kg.
This storage system stands out for its strength “and its robustness,” says Fanzaga. Mecalux placed electro-welded mesh on the racking units located near other work zones (e.g., the quality inspection area). The mesh covers the entire structure of the racks to ensure the stability of the loads and prevent materials from accidentally falling.
The racking is designed to store products of various sizes, weights and shapes. This was essential for Art Cosmetics, as it manages multiple unit loads — e.g., pallets, boxes, liquid containers and plastic drums — weighing between 25 kg and 200 kg. “In our warehouse, you can find pallets and boxes to plastic and metal drums containing liquid emulsions and waterless substances,” says Fanzaga. One of the particular characteristics of this storage system is the direct access to the goods using only forklifts. This is crucial for facilitating storage and order picking tasks. Moreover, all the material is labelled with barcodes, and all locations are tracked in the WMS.
Live pallet channels with rollers: smooth connections
Mecalux set up nine live pallet channels with rollers for three, four or eight pallets deep. These channels are slightly inclined so that pallets move from the highest point to the lowest by gravity. According to Fanzaga, “this solution has streamlined movements of goods in two of our key logistics processes.”
Part of the live pallet channels have been installed in the receiving area to temporarily house goods arriving at the facility. The products remain there before undergoing the physical/quality control and labelling processes. The other live pallet channels are positioned next to the production lines.
There, the operators store the raw materials that they have picked in the warehouse and that will later be used in the different production stages.
Art Cosmetics exploits its potential
Art Cosmetics has transformed its warehouse in Fornovo San Giovanni and, with it, its entire supply chain. Its objective was to maintain the innovation, production and quality standards so characteristic of the company and demanded by its customers worldwide.
“Although we weren’t hit as hard as other sectors, the pandemic led to a decline in sales in the cosmetics industry as well. However, thanks to the organisation we’ve built up over the years, Art Cosmetics has maintained high-quality service, always meeting the needs of our customers and complying with all safety measures,” says Fanzaga.
With this warehouse connected to the production lines, the company has increased its manufacturing capacity and can “continue climbing to the top of the world ranking of businesses in the industry, which is our main motivation,” says Fanzaga.
We’re extremely satisfied with our Mecalux storage systems. They’ve helped us to cut times in all our operations: product identification and monitoring, storage, order picking and transfer to the production lines.
Benefits for Art Cosmetics
- Safe, fluid movement: the live pallet channels act as a temporary storage zone for products arriving at the facility. At the same time, they ensure that raw and bulk materials are delivered to the production lines in a controlled way.
- Agile picking: the direct access offered by the pallet racking is a must for fast order picking, with operators managing different kinds of packaging for a single order.
- Leveraged space: the warehouse plays a pivotal role in supplying the production lines with the necessary materials. Everything was optimally designed and organised to accommodate the largest number of items.
Pallet racking | |
---|---|
Storage capacity: | 4,800 pallets |
Pallet sizes: | 800 x 1,200 mm and 1,000 x 1,200 mm |
Max. pallet weight: | 1,000 kg |
Racking height: | 10 m |
Racking length: | 45 m |
Gallery

Storage of Art Cosmetics' raw materials and bulk cosmetic products
Ask an expert