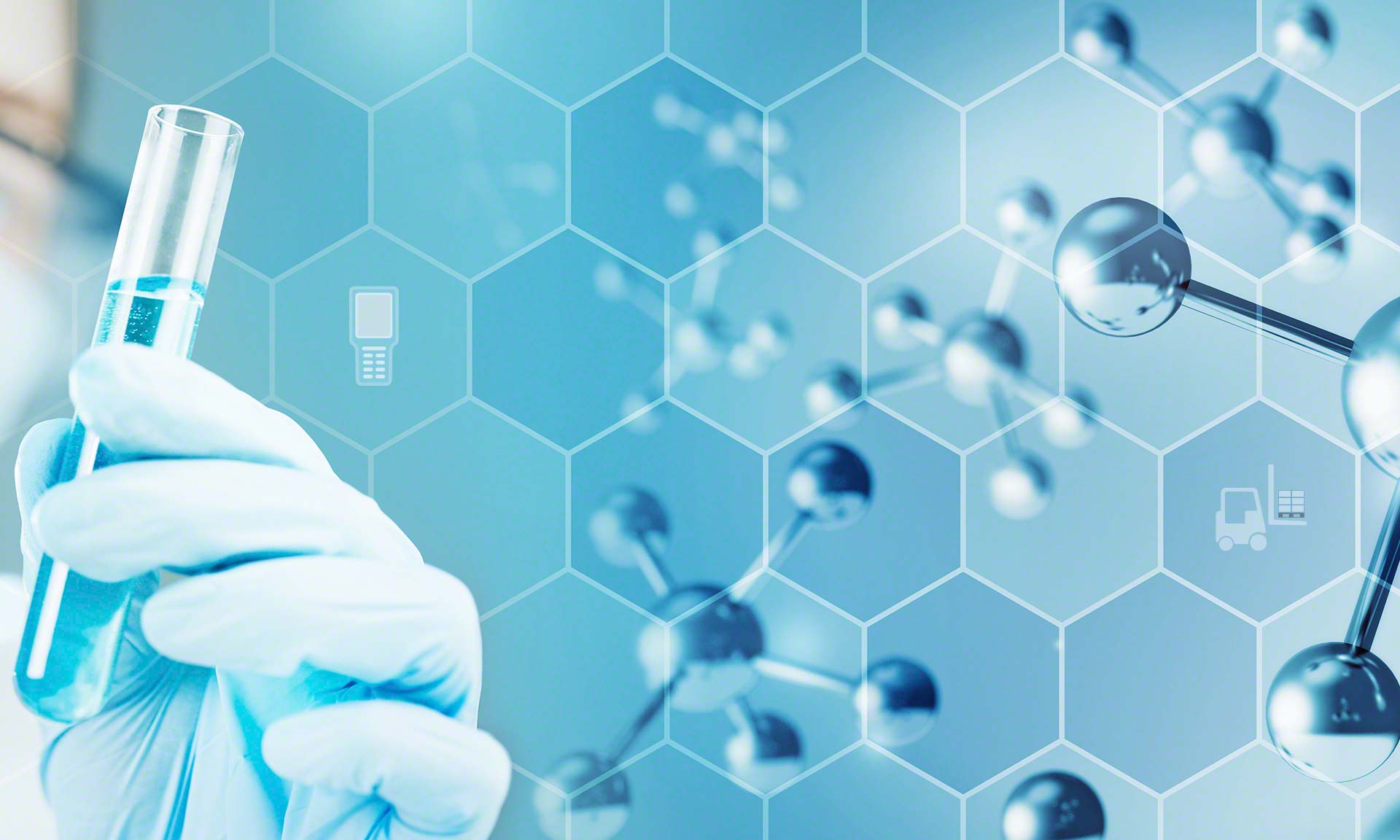
BASF: digitisation for just-in-time production
Easy WMS has been integrated with the production software to know what items are required
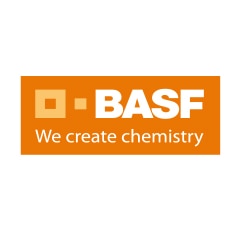
The production plant of German multinational BASF in Brazil has digitised its logistics processes. The chemical company has outfitted one of its warehouses with the Easy WMS warehouse management system from Mecalux with the aim of controlling all movements of its 1,800 SKUs in real time.
BASF, founded in Germany in 1865, has over 240 production plants in 90 countries. The firm supplies products to 90,000 customers in all sectors. In 2020, it generated global sales of €59 billion.
Since it was opened in 2000, the BASF plant in Indaiatuba, Brazil, has been renovated frequently, with improvements made to increase efficiency in its processes. Recently, the company has equipped one of its facilities with the Easy WMS warehouse management system from Mecalux.
The decision to modernise this warehouse with Easy WMS is part of BASF’s plans to digitise the majority of its facilities worldwide by 2022. Its aim is to have technologically advanced production plants to provide its customers with enhanced service.
Transformation towards digital logistics
Before turning to digitisation, all warehouse management was carried out manually. “We managed our products with the help of the SAP ERP system. The operators would enter into the system manually the products that were received and dispatched as well as the movements made in the facility,” explains Márcio de Almeida Soares, Logistics Coordinator at BASF.
To prepare an order, the operators would go up and down the aisles with a printed list specifying the number of items they had to bring to each production line. Manual management of the warehouse entailed a high risk of error. “We were looking for a software program that would allow us to organise our warehouse operations and prevent any chance of making mistakes,” says Soares. “We wanted to accurately control the SKUs, optimise operations and make the most of the available space to boost our storage capacity.”
After analysing several options, BASF opted to instal Mecalux’s Easy WMS warehouse management system. The multinational was already familiar with the applications and advantages of this software. In Guaratinguetá (also in Brazil), Mecalux had built BASF a 1,400 m² automated clad-rack facility supervised by Easy WMS. “Mecalux demonstrated advanced knowledge of warehouse management systems and proposed Easy WMS to meet our needs. The choice was clear to us from the start because we saw that the tool could be easily adapted to our processes and enhance them,” says Soares.
Digital integration in the warehouse
The facility fulfils a basic function at the BASF plant: to supply the production line with the necessary goods. The warehouse stores 1,800 SKUs, including the raw materials used on the production lines, semi-finished goods and finished products.
To optimise its production processes, the facility operates according to the just-in-time method. In other words, it supplies production with the raw materials when the time is right. To do this, the system requires seamless coordination between the warehouse and the production lines.
One of the reasons why BASF chose Easy WMS from Mecalux is because of its ability to integrate with the production plant’s IT systems. Before implementing the warehouse management software, the production supply process was much slower. Operators would lose a lot of time searching for the product they needed and moving it to the production lines.
With Easy WMS, BASF not only controls inventory in real time, but also knows which products are required in production and monitors all pallet movements.
Logistics digitisation offers the company another advantage: it can identify critical points along the supply chain to solve incidents and gain in productivity. “The software from Mecalux interacts with all our operating systems to leverage processes and oversee the SKUs,” says Soares.
Efficient warehouse organisation
Easy WMS manages and optimises all operations in the facility, from the receipt of the raw material sent by suppliers to their dispatch to the production lines.
“Our workers carry out goods receipt, storage, inventory, internal movements and dispatch tasks. Easy WMS takes into account the priorities of the production lines and sends detailed instructions to operators on what to do,” says Soares.
To communicate with the WMS, the operators work with scanners integrated with the Android operating system and that incorporate a barcode, RFID tag and QR code reader. As a result, the company can operate with any coding system. Soares says: “By integrating Easy WMS with RFID technology, we’ve sped up operator movements in the warehouse.”
The Easy WMS software intervenes in the following processes:
- Goods receipts. Every day, the facility receives 280 pallets, which operators identify aided by their scanners.
- Product storage. Once the pallets are identified, Easy WMS decides where to store them. The software comprises rules and algorithms to assign the merchandise the ideal location based on whether it is a raw material, a semi-finished product that needs to go through a process, or an item ready to be distributed to customers.
- Order preparation. Operators put together about 120 pallets on a daily basis, which are then sent to the production lines or to customers. Easy WMS generates a pick path to ensure that these workers travel the minimum possible distances through the warehouse and prepare more orders in less time.
- Dispatches. Orders are grouped by route (if sent to customers) or product type (if destined for the production lines). In the latter case, Easy WMS must notify production so that processes can be organised there.
Connection and traceability
BASF has set out to improve its entire supply chain and boost operations at its plant in Indaiatuba to continue to lead the market in its sector. To do this, it has resorted to digitisation. This has enabled it to trace its goods and make sure that the production lines have all the items they need to manufacture without interruption.
“We’re committed to managing 100% of product movements and controlling the status of the goods to enhance the quality of our supply chain and improve customer satisfaction,” says Soares.
With Easy WMS, BASF can now monitor the entire trajectory of its products, supervising the available stock and the quantities sent to production and to customers. Digitisation has streamlined operations in the facility, resulting in greater efficiency and speed.
With Easy WMS, we’ve digitised and perfected all processes in our facility. We’re sure that, with the help of Mecalux software, we’ll continue to make the most of all our operations.
Advantages for BASF
- Total traceability: the 1,800 SKUs stored by BASF are identified from the minute they arrive at the facility. The WMS controls all the data: weight, characteristics, turnover, size, etc.
- Integration with production: the warehouse is connected to production, supplying the raw materials required at just the right time. Easy WMS has been integrated with the production software to know what items are needed.
- Organised stock: Easy WMS slots the products in the warehouse in a way that optimises operator movements. Consequently, the other operations are much smoother.
Ask an expert