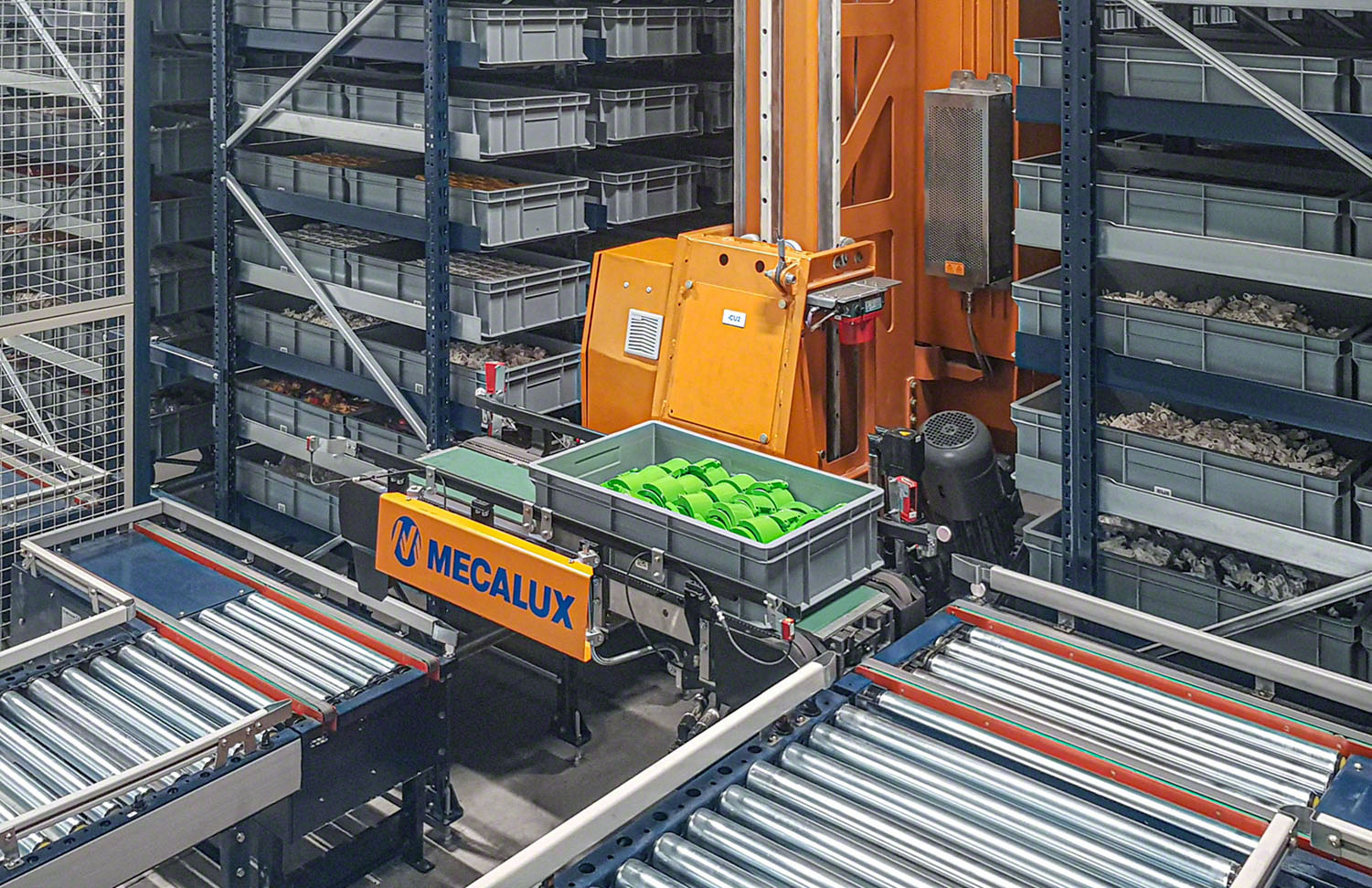
Clics Toys: automated management of 150 parts products annually
Clics Toys has automated its warehouse after tripling its production volume over the past year
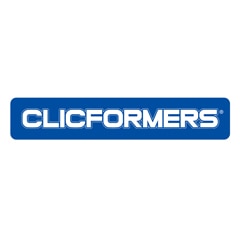
Clics Toys, the manufacturer of Clicformers construction sets, is a staunch defender of innovation and automation as tools for improving its supply chain and distributing its toys throughout 40 countries. As the company has tripled its production over the past year, it was compelled to modernise the warehouse of its plant in Wuustwezel (Belgium) in order to store the more than 150 million components it manufactures annually. The solution was to open an automated warehouse with capacity for 7,800 boxes managed by the Easy WMS warehouse management system.
Dexterity and motor skills
Construction games fulfil two important functions: to entertain children and help them to coordinate their hands using precise movements. Well aware of this responsibility since it was founded in 2001, Clics Toys strives to revamp its construction games to make them more attractive, manageable and playable.
In the beginning, this Belgian company marketed the Clics brand. Recently, however, in collaboration with its Korean partner, it has focused on developing Clicformers. This is an improved version of its product, with larger parts that are used to construct buildings and castles as well as cars, planes, robots, dinosaurs and animals. As a result, Clics Toys has expanded its market. Approximately 50 million children in over 40 countries play with these toys nowadays.
Clics Toys’ history is imbued with transformation and evolution. This family business has gone from putting toys in boxes in a small garage to building a 14,000 m2 production centre in Wuustwezel (Belgium) that has been continuously updated since it opened in 2004.
Technology: productivity and cost savings
The company knows that technology adds value to not only products but also processes. For this reason, it has turned to automation and digitalisation to create new forms of production and to benefit from the advantages brought by Industry 4.0.
“We used to store plastic boxes on the warehouse floor,” laments Hedwig Van Roy, CEO of Clics Toys. The firm was adamant that both its supply chain and its logistics systems had to be more effective. Automation is an optimal solution for this: it replaces the manual work of operators (thus, eliminating repetitive or more difficult tasks), improves service quality and cuts costs. The founder and CEO of Clics Toys states, “We’ve tripled our production volume in the last year, which is why we had to install an automated storage system.”
Clics Toys’ warehouse can operate in a completely controlled and safe way 24 hours a day. Thanks to the robots and automated handling equipment, operator presence is minimal. Moreover, part of the processes can be performed with the lights out, leading to cost savings.
Clics Toys planned on overhauling its installation to contend with the increased sales and expansion of its business. The warehouse stores finished products, that is, recently manufactured parts. Every day, this facility receives around 800 boxes, each containing close to 250 components.
The boxes are then sent to the kitting area, where the parts are sorted and grouped by shape and colour. Finally, they are inserted into the boxes marketed to customers.
By renovating the installation, the company had a clear twofold objective. On the one hand, it wanted to better leverage the available space to increase its storage capacity. On the other hand, it aimed to speed up its flow rate by automatically connecting the warehouse with the production lines and kitting area.
Automated throughput
Mecalux has built an automated warehouse for boxes consisting of two 40-metre-long aisles with 5-metre-high double-deep racks on both sides. In total, they can hold 7,800 boxes, each weighing 25 kg, equivalent to 500 SKUs.
Hedwig Van Roy acknowledges, “Even though the building is only five metres tall, we’ve been able to optimise and make the most of it, which has been really useful for us.”
A stacker crane moves with full autonomy through each aisle, inserting and removing boxes into/from their corresponding locations as per instructions from Mecalux’s Easy WMS.
The installation is right next to the production lines. This way, the boxes can be stored on the racks as soon as they leave production, which is essential for efficiently managing the 150 million parts the Clics Toys plant manufactures every year.
The connection between the warehouse and the other working areas is fully automatic, enabled by conveyors for boxes and AGVs (automated guided vehicles). A conveyor circuit moves the parts from the installation to the kitting area. There, operators receive the components and, with the help of mechanical arms to streamline the work, place them in the boxes that children will subsequently receive.
One of the greatest advantages of the conveyors — and one that has benefited Clics Toys the most — is their versatility in terms of building a wide variety of circuits. This transport system supplies the kitting area quickly and safely.
Hedwig Van Roy - CEO of Clics Toys
“We’re more than satisfied with Mecalux’s installation of the automated warehouse for boxes. During the past year, we’ve tripled our production volume and dealt with it successfully through automation. Plus, we’ve saved considerable costs by ramping up activity while continuing to work with the same number of operators.”
Easy WMS: digital transformation
Clics Toys has used the commissioning of this new automated warehouse for boxes as an opportunity to completely digitise its supply chain. To do so, it has implemented the Easy WMS warehouse management system, which carries out extremely rigorous control of the goods and movements.
The WMS organises the products. Based on rules and algorithms, it decides on a location for each of them according to their particular traits and demand level. The goods are distributed in such a way that they ensure the maximum throughput of the two stacker cranes.
This system accurately monitors the goods in real time; that is, Easy WMS knows the exact location of an item from the moment it arrives at the installation and goes through the checkpoint.
Easy WMS has been integrated with Clics Toys’ Logistics ERP to strictly monitor the processes and coordinate the movements of the automatic conveyors with the company’s needs.
Automation for flexible logistics operations
Clics Toys’ goal is to grow and perfect its processes and toys in order to provide excellent service with the capacity to excel.
A flexible logistics system is vital for the firm to adapt to new market demands and face any proposed changes. Automation is the best solution for achieving this, since it ensures high productivity using the same resources and the same team of operators. Hedwig Van Roy notes, “Thanks to automation, we’ve been able to cope with the rise in production while maintaining the same number of employees.”
With the new automated warehouse for boxes, the business has greatly improved the efficiency of its supply chain. It has not only made the best use of the available space to increase its capacity, but also relied on conveyors for boxes to automatically connect the various work areas.
Advantages for Clics Toys
- High throughput: automation enables the company to work 24/7, considerably increasing the productivity of all operations. Additionally, this solution prevents operators from having to move around the warehouse to pick products.
- Real-time inventory control: Easy WMS closely monitors the goods at all times. It knows not only their location, but also their characteristics, such as SKU and turnover type.
- Maximised space: the warehouse occupies only the area necessary for obtaining a storage capacity of up to 7,800 boxes.
Automated warehouse for boxes | |
---|---|
Storage capacity: | 7,800 boxes |
Box size: | 400 x 600 mm |
Max. box weight: | 25 kg |
Racking height: | 5 m |
Racking length: | 32.4 m |
Gallery
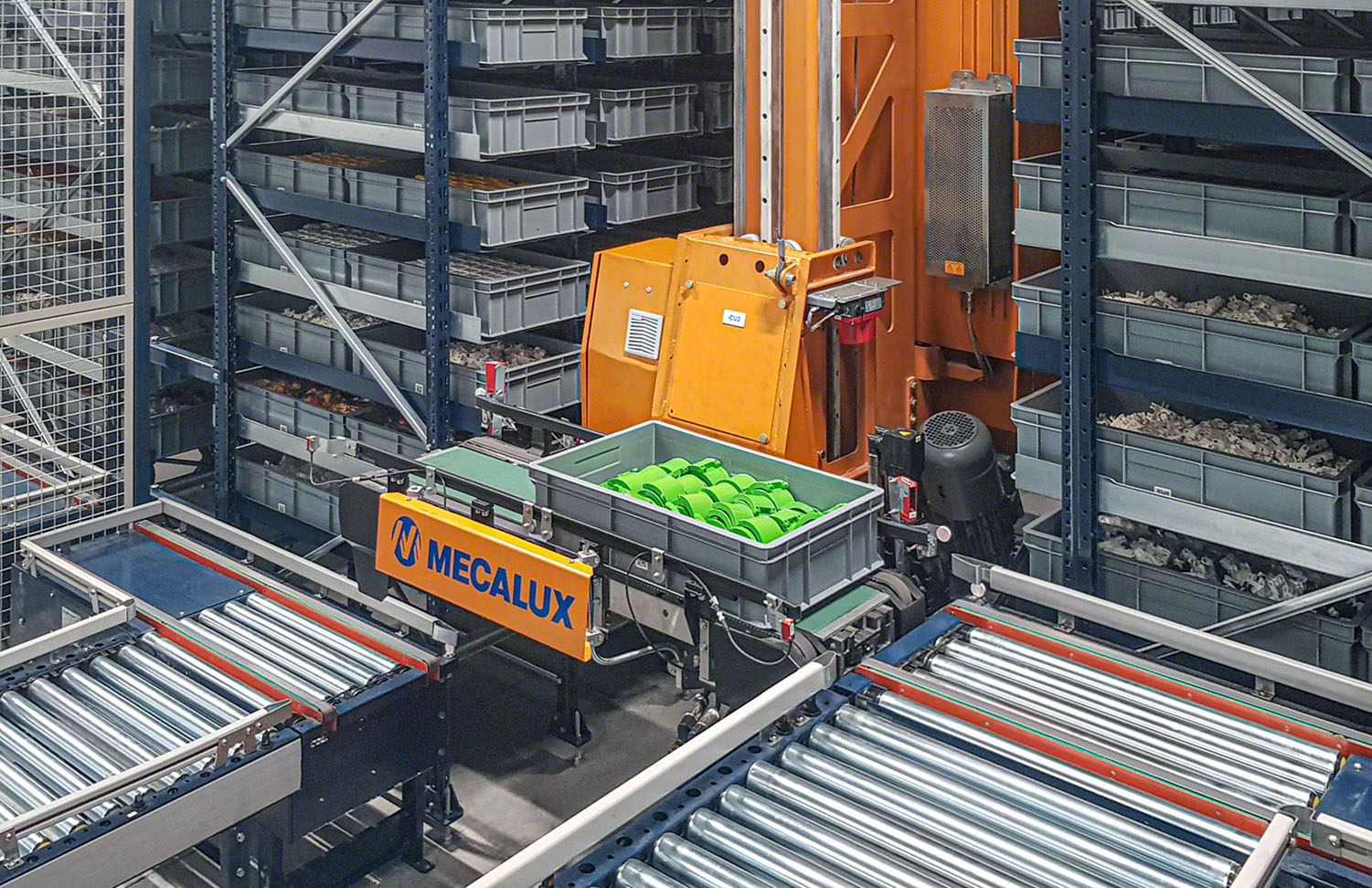
Clics Toys' new automated warehouse for boxes in Belgium
Ask an expert