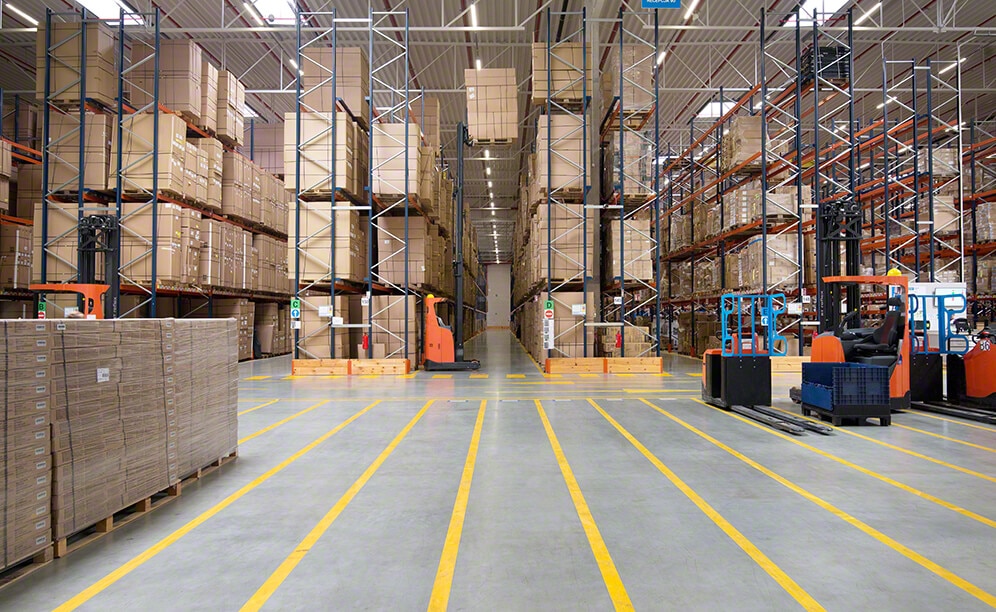
Efficient order picking system in the Decathlon warehouse in Poland
Decathlon has opened a new warehouse in Poland whose primary operation is picking orders
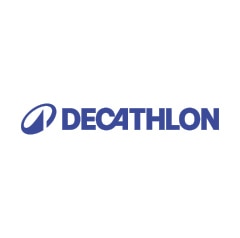
Decathlon, the established sports equipment chain, has constructed a new 30,000 m2 logistics centre in Łódź (Poland) and Mecalux has fitted it out with picking shelves and pallet racks. Both solutions help classify the goods according to their dimensions and demand, while also providing direct access to speed up order picking, this centre’s primary operation.
About Decathlon
Decathlon is a hypermarket chain that focuses on selling and distributing sporting goods. Established in France in 1976 and, since then, it has opened more than 1,100 shops around the world.
The company makes and markets its private label brands, specifically designed to meet the needs of sportspeople. Each brand represents a specific sport or activity, such as dancing, swimming, cycling, mountain sports, fishing, fitness or tennis.
The needs of Decathlon
Decathlon is a very innovative company, which rethinks its business strategy constantly in order to increase customer satisfaction. To that effect, in the last few years, it has focused on opening new urban-based shops in downtown capital city areas.
Meanwhile, it has also boosted the online sale of products bought off its website and improved order delivery times.
Solidifying these aims would require a system that could bring speed to order picking and consolidation.
The company Decathlon asked for Mecalux’s collaboration to get the maximum storage capacity in its new logistics centre in Łódź (Poland). Likewise, this required that SKUs be classified based on their sizes and taking ABC rotation criteria into account.
The logistics centre
The facility is sectored into three different zones:
- Mezzanine with picking shelves
- Reception and dispatch area
- Pallet racking
Both the mezzanine floor and ground level were installed with hand-pick shelving for small-sized products.
A conveyor circuit connects the two floors and automatically moves finished boxed orders up to the completion and consolidation area.
On the other hand, the pallet racks are set aside for bulky products and palletised reserves with goods for the picking shelves.
Pallet racks
The 9.5 m high by 89 m long pallet racks offer storage capacity for 11,518 pallets. Picking is also done directly from the pallets on lower levels, where boxes are picked right off pallets.
An underpass was enabled that cuts across the racks and improves personnel workflows, while also acting as an emergency exit. The levels above are fitted out with electro-welded mesh to prevent the accidental fall of materials.
This warehouse is operated by reach trucks to insert and extract pallets from their locations and by ground level order pickers for picking.
Order preparation
Picking shelves feature direct access to boxes, which facilitates the handling of the small-sized goods contained inside the boxes.
Picking is based on the «person-to-product» criteria: operators push handcarts up to the shelves to manually pick the SKUs listed by the warehouse management software (WMS) on a radiofrequency device.
Replenishment takes places when fewer numbers of orders are being prepped. Operators deposit pallets with reserve product on the mezzanine level using reach trucks. Two up and over pallet gates were arranged on the mezzanine to keep operators completely safe during the loading of goods.
Conveyor circuit
This circuit flows centrally through each mezzanine level. The main conveyor has ten built-in picking tables on both sides (one in front of the other). Each table corresponds to a certain number of shelves and operators, which vary according to the quantity of orders that must be put together.
Once he or she has finished putting together their part of the order, the operators set the boxes on the central conveyor belt that takes them up to the next table that holds the products it needs. In the event the orders have been completed, the conveyor routes them directly to the verification and packaging area.
Sorted, consolidated and shipped out
The conveyor circuit ends at the consolidation area where the finished orders are sorted automatically into eight different channels. Next, workers verify orders are error-free, they seal the boxes and distribute them on pallets, sorted by customer or shipping route.
Pallets from the same order or route are grouped together on the floor in front of the docks, streamlining the subsequent loading of lorries and avoiding timeouts.
Advantages for Decathlon
- Efficient order preparation system: the distribution of the goods, taking into account their characteristics and demand, allows for the optimisation of operator movement and maximum picking throughput.
- Every mm counts: the centre has an 11,518-pallet capacity, as well as more than 6,000 shelves where a variety of boxes are housed, all filled with small items.
- Operational flexibility: each warehouse area has a set number of operators that differs according to the pick demand.
Decathlon logistics centre: Pallet racks | |
---|---|
Storage capacity: | 11,518 pallets |
Pallet sizes: | 800 x 1,200 mm |
Max. pallet weight: | 700 kg |
Racking height: | 9.5 m |
Racking length: | 89 m |
Gallery
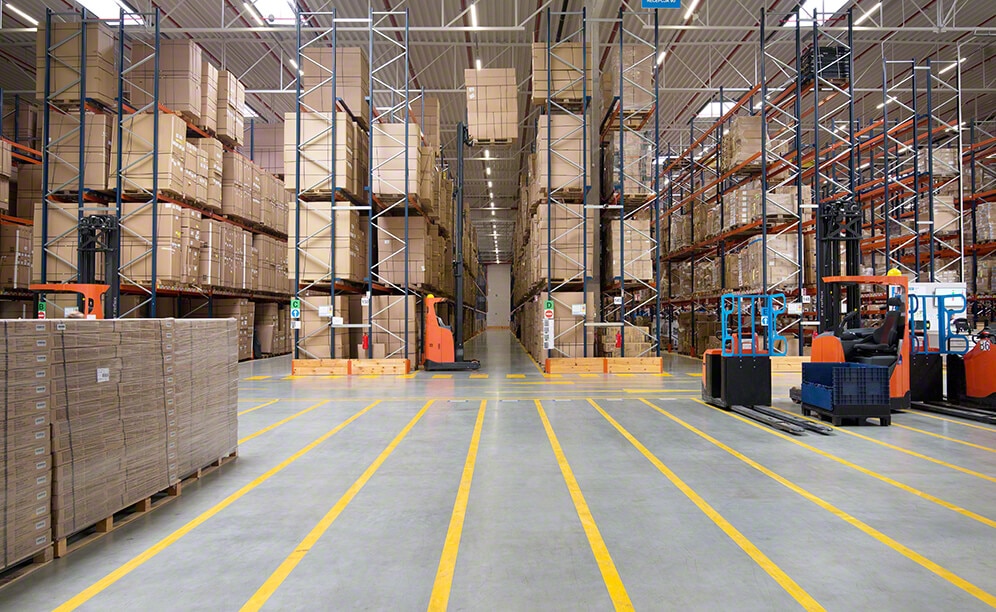
Decathlon warehouse in Poland with pallet racks and picking shelves
Ask an expert