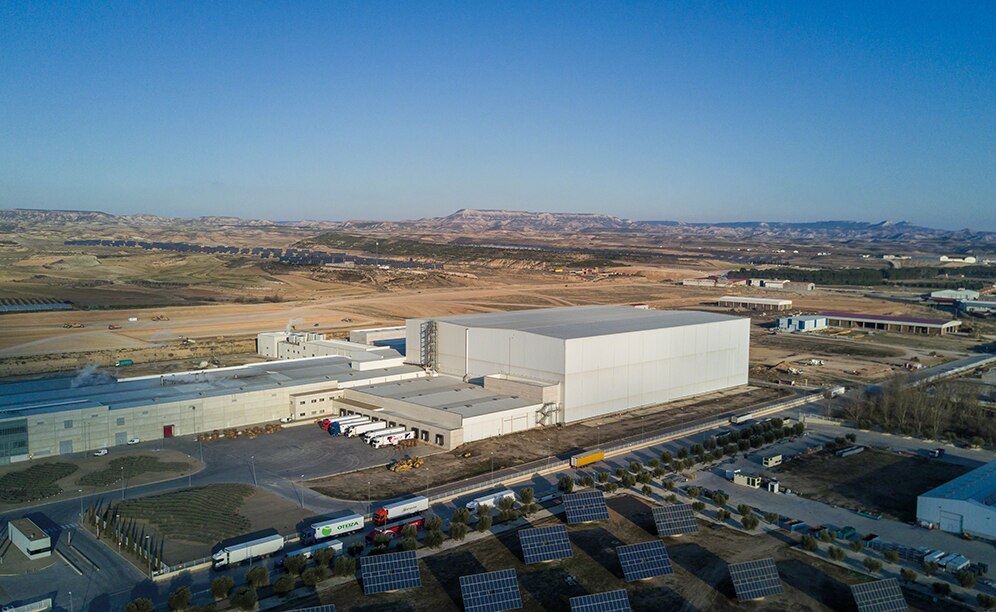
Mecalux stands alongside Congelados de Navarra in its steady growth
Congelados de Navarra has a capacity for 146,000 pallets in three automated frozen storage chambers
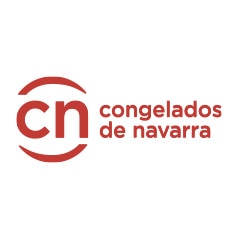
Established in 1998, Congelados de Navarra is one of the Europe's youngest frozen food companies and one on a solid footing. Its strong commitment to technology and innovation in all production processes has made it one of the top 10 frozen vegetable specialists on the continent. From the beginning, Mecalux has collaborated with the company in its expansion projects, designing and implementing more efficient logistics solutions to meet its needs.
A success story
Congelados de Navarra is a clear example of persistence and success, infused with a keen entrepreneurial spirit. The story begins in 1998, when Benito Jimenez founded the company and started the construction of its production centre in the town of Arguedas (Navarra).
Initially, the centre consisted of a frozen storage chamber with high-density drive-in racking, but its capacity was insufficient to meet the increase in sales. The company was forced to make a strategic investment to expand the installation. From the outset, the firm was aware of the importance and need to automate in order to capitalise and maximise the productivity of all its processes.
Currently, the Arguedas centre has two fully-automated frozen storage chambers, which offer a storage capacity for 12,700 pallets.
The company has always benefited from the advantages of automation when optimising its centre's throughput. Hence, it has experienced continuous growth and has achieved high acclaim, such as being Europe's largest producer of deep-frozen broccoli in 2004.
Given its forecasted growth, in 2008 Congelados de Navarra opened its second production centre, located in Fustiñana (just 24 km from its first factory).
This centre has been expanded and adapted according to the requirements of the company.
At present, it has two automated clad-rack constructed chambers with a total storage capacity for 63,000 pallets and is in the process of building a third chamber, which will have a capacity to store 83,000 pallets.
In 2012, the company opened its first office in France, which signalled the beginning of business expansion at an international level.
Today, the company also has subsidiaries in the UK and the United States. It exports 70% of its production and has established an extensive network of distributors and importers that help sell its products worldwide.
Mecalux and Congelados de Navarra
Collaboration between the two organisations dates back to 1998, with the establishment of Congelados de Navarra.
Following the advice from Mecalux, the company has thought out and developed new goals and projects, improving its logistics operations. These are some of the installations built during this time:
Arguedas
In 2000, Congelados de Navarra hired Mecalux to construct the first automated frozen storage installation (within a traditionally built chamber) in its production centre in Arguedas. The high-density Pallet Shuttle system with stacker crane was installed with a 3,800 pallet storage capacity.
In 2004, the second automated chamber, also clad-rack, was put into operation right next to the first. It measures 33 m high and consists of three aisles with double-depth racks on both sides, providing a storage capacity of 8,900 pallets.
Fustiñana
Congelados de Navarra celebrated the grand opening of a new production centre located in Fustiñana in 2008, to keep pace with projected growth and to respond quickly to its customers.
This ambitious project has continued to enlarge and flourish in different stages:
- Phase 1
Mecalux built a 36 m high automated clad-rack chamber, which operates at a constant temperature of -21 °C. It consists of six aisles, with double-depth racks that have a 27,000 pallet storage capacity.
In this centre, all internal transport between the different production areas and the frozen storage chamber is automated, using a circuit of roller conveyors, transfer cars, lifts and electric monorails.
- Phase 2
Between 2010 and 2011, a new chamber similar to the previous one was erected, attached and integrated to the first, with a capacity for more than 36,000 pallets, distributed in eight aisles.
- Phase 3
In 2015, Congelados de Navarra extended its packaging and mixing zone.Again, the firm asked Mecalux to install all internal handling equipment connecting these areas to other production areas, including the warehouses.
- Phase 4
A year later, Congelados de Navarra requested Mecalux’s collaboration in finding a solution to cope with foreseen increases in production comfortably and thus solidify its growth, both in terms of production and storage capacity.
The company has decided to build another frozen storage chamber, in addition to the previous two and entirely for partially-finished products. When completed, it will be connected to existing internal transfer circuits to move goods in both directions.
The warehouse will measure 43 m high with an 83,000 pallet capacity –a colossal sized building, very unusual in this type of chamber. It will be equipped with the automatic high-density Pallet Shuttle system with transfer cars, allowing a very high number of movements.
Streamlined installation at Fustiñana
The vast majority of Congelados de Navarra's production is processed in the Fustiñana centre. Food goes through a set of processes (most of them automated) to ensure the highest quality while maintaining a good texture, nutritional value and taste.
Production output
The beginning of the Mecalux installation is where the goods have crossed through the freezing tunnel. Channels of roller conveyors are mounted just below the sorting lines. Empty "octa bins" (large octagonal corrugated or plastic bulk boxes) move to the hoppers and are filled with products.
Then, a transfer car moves the pallet to the lifts, which raises them to the top floor. There, automatic stretch wrappers seal off the octa bins, protecting the product.
Once their condition is verified, they enter the electric monorail circuit, which runs towards the storage chambers (or the other production areas).
The electric monorail circuit design allows the required trolleys to be at each point via dynamic allocation. In addition, there are shortcuts to prevent the trolleys from having to go through the entire route.
Chamber entry points
Before being placed in the warehouse, pallets cross a SAS (Security Airlock System).It is an ante-chamber that has two fast action doors –one of them opens into the chamber and the other out–, which are never open at the same time. This system is used to prevent sudden changes in temperature, cold loss and condensation.
There is also a SAS installed at the pallet exit point that faces the processing areas.
The installations feature two connected levels, and both have two conveyor circuits –one for input and one for output.
On the top floor, goods arrive from the plant and outgoing pallets that are routed to the processing areas (packaging and mixing). Downstairs is the product entry point from outside the warehouse and also the dispatch area is set up here.
Features of the frozen storage chambers
The two connected chambers are 140 m long, 103 m wide and 35 m high and comprise 14 aisles with double-depth racks on each side, which provide a total storage capacity of 63,000 pallets.
This is a clad-rack construction, i.e., the racking must withstand their own weight, that of the goods, as well as the wall and roof cladding. At the top of the racks, there are trusses where cooling equipment is located. This achieves continuous air flow and a uniform distribution of the temperature throughout the installation.
In each aisle, the twin-mast stacker cranes move pallets between input and output conveyors and rack locations assigned by the Mecalux Easy WMS warehouse management software, according to previously parameterised rules.
Walkways and platforms are enabled on top of the chambers, designed for performing maintenance of the refrigeration equipment and the stacker cranes. These are accessed from outside the warehouse.
Bottom floors of the frozen storage
The output of products to dispatch takes place on the lower floor of the frozen storage installations. A conveyor circuit connects the storage aisles with the exit doors that open into the ante-chambers, where pallets are deposited and await distribution in transport vehicles.
In the ante-chamber (short in height and temperature controlled) goods of the same order or route are grouped to expedite subsequent loading onto delivery lorries. This space can hold 500 pallets ready for shipment.
Three SAS door systems connect the docking area to the ante-chamber. Once crossed, the pallets are made available to operators for placement into the transport vehicle's box.
In this same area, there are entry points for products coming from outside the processing plant. Pallets that are not of adequate quality are placed on a slave pallet, which can be of two different sizes:800 x 1,200 mm or 1,000 x 1,200 mm.
Packaging and mixing area
The products that head to the processing area leave the frozen storage chambers through the top floor and are picked up by the electric monorails.
The processing area is higher compared to the monorail transport circuit. For this reason, lifts have been installed that take the goods up to the top level. Here, there are packaging and mixing hoppers, and a conveyor circuit that delivers pallets to the appropriate position.
Pallets that finish these processes descend via lifts and are taken by the monorail to their new destination.
Sending octa bins to production
Sending empty octa bins to production is vital for the proper operation of this centre and is performed automatically.
The octa bins are packaged in a specific area: they are placed on pallets, lined with a large bag that prevents contact between the frozen product and the cardboard and, finally, labelled with a RFID code.
Two lifts send the octa bins to the transport level, and the electric monorails automatically move them to the most appropriate points.
Electric monorails
The electric monorails are the main artery that flows through this installation and are responsible for the internal movements between all production areas.
The rails are suspended from the ceiling, the trolleys receive power from them, and their position is also detected in the circuit. Detours are fundamental: there are shortcuts, maintenance areas and trolleys on-hold.
The electric monorails are very agile and ensure a steady flow of goods. They are ideal for food companies like Congelados de Navarra, as they do not create large obstructed surfaces on the floor area, facilitating clean-up.
Easy WMS, the brain of the whole system
Optimal logistics management
The software developed by Mecalux manages and is involved in all processes carried out in a facility, including the entry of goods from processing and outside sources, allocation of locations, stock control, storing, extraction, sending pallets to processing areas, warehouse returns, etc.
The Easy WMS by Mecalux supplies octa bins nonstop for the continuous replenishment of production outputs.
When storing goods in their locations, rules and algorithms take into account the characteristics, consumption criteria and turnover of the products. The rules are configured in Easy WMS Mecalux to classify stock between the 14 frozen storage aisles. Thus, the bulk product is deposited in the octa bins closest to the packaging and mixing area; on the other hand, finished product is located next to the dispatch zone.
The company ERP, Oracle’s JD Edwards, requests bulk products for the packaging area. The Mecalux WMS calculates the number of octa bins needed and sends them to their destination along a pre-set sequence. Orders that are routed to the mixing area receive the same care from the WMS as those in packaging.
Dispatches are made by lorries. The WMS generates tasks to extract the orders from their locations and deposit them in the ante-chambers, awaiting transfer to the docks. When a lorry backs into the dock to be loaded, pallets are automatically released to the exit point and Easy WMS, from a display screen, tells the operator which load must go to which dock.
Triangular communications
For this warehouse to operate correctly, the Easy WMS Mecalux is in permanent connection with the other two management systems involved in this project: the enterprise resource planning system (ERP) of Congelados de Navarra, and the production control system (MES).
The MES control programme tells the Easy WMS what product entries are taking place in real-time on each production line. It also requests the bulk goods that must be sent to this area. It also requests the bulk goods that must be sent to this area.
The ERP reports the entry of pallets from other logistics centres in Congelados de Navarra, headed to the storage area, and also places orders for bulk products for its packaging or mixing.
Galileo, the heart of the installation
A warehouse as complex as Congelados de Navarra's requires solutions that simplify and optimise its management. In this sense, the Mecalux Galileo control software works as the general coordinator of the installation, launching the movements of the electromechanical equipment that perform transport tasks and the storage of goods.
Galileo is responsible for handling the machines (conveyors, stacker cranes, electric monorails, lifts, etc.), controlling the hardware components (scanners, RFID readers, drives, etc.) and recording any problems or incidents, as well as all communication with the warehouse management software (WMS).
To sum up: it receives orders from the WMS, sends the signals corresponding to the machines and facilitates automatic movements of the octa bins.
Also, the use of the SCADA system provides all relevant warehouse information in real-time about each machine, breakdowns, transport in motion, etc., without the need for specific visual hardware.
Ready for the future
The production centre at Fustiñana is ready to grow and has provided for the possibility of building more frozen storage chambers in the future, depending on market needs and company’s business goals.
Mecalux software will serve the company at all times, adjusting to changes and increases experienced in production. It is a scalable system, i.e. able to increase or reduce the resources and output according to the centre’s requirements.
Accordingly, to ensure the smooth operation of the new frozen storage chamber, Easy WMS will incorporate a module for using the automatic Pallet Shuttle system with transfer cars.
Thinking ahead
Benito Jimenez, entrepreneur and founder of Congelados de Navarra, decided to incorporate automated systems into all processes, from production to storage, including internal transport.
The ultimate goal is to maximise the throughput of the centres and solidify company expansion.
Automation of all the storage areas in Arguedas and Fustiñana centres has meant a massive step forward for Congelados de Navarra, by streamlining storage capacity with minimal human intervention.
Mecalux has always advised Congelados de Navarra when turning its expansion projects into reality. It has furnished all its knowledge and experience in order to find customised solutions that can efficiently solve the voiced logistical needs.
The Fustiñana automated centre is the outcome of this close partnership and is one of the most modern and technologically advanced in the European market, as well as a benchmark installation worldwide.
Gallery
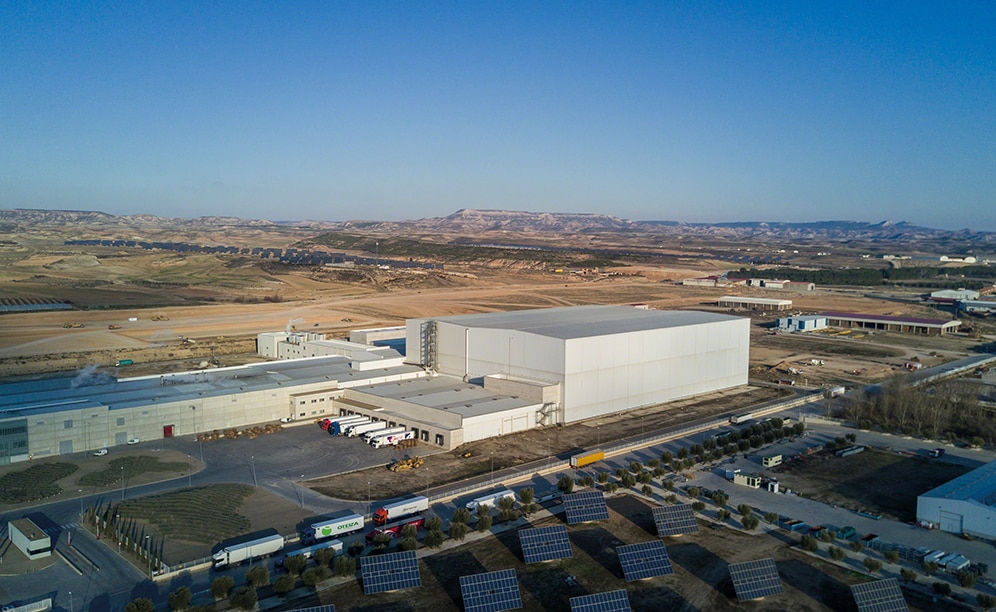
The total storage capacity of the two chambers in phases 1 and 2 is 63,000 pallets
Ask an expert