
A comprehensive conveyor circuit streamlines the order prep of an e-commerce pioneer
The successful Swedish e-business builds a large warehouse in Poland
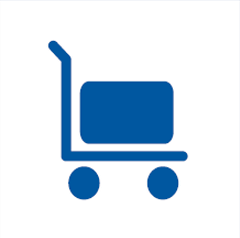
One of the leading companies in the on-line sale of apparel and accessories for the motorcycling and snowmobiling industry built a warehouse in Szczecin (Poland). It is composed of pallet racking, picking shelves for boxes and a conveyor circuit that includes a sorting zone. The variety of solutions provided by Mecalux has allowed the company to increase storage capacity and speed up the preparation of orders.
Customer needs and the solution
After years of continuous growth, the company decided to make a qualitative leap logistically and move its central warehouse to Poland with the aim of improving the distribution of its products to its customers, mostly concentrated in central Europe.
The Polish city of Szczecin was chosen, on the border with Germany, for its proximity to the Scandinavian market and the rest of Western Europe. Moreover, in Szczecin there is the Panattoni Park, a modern distribution centre where the warehouse is located, which occupies an area of more than 10,000 m2.
Furthermore, and in anticipation of the future needs of the company, it has enabled an area of over 4,300 m2 next to the current warehouse for a possible extension.
Under the premise of optimising storage capacity and streamlining processes for preparing orders, Mecalux supplied pallet racking, picking shelves for boxes, a goods reception area, an output area for bulky products, a conveyor circuit to consolidate orders, preloads area, etc.
Main warehouse areas:
- Pallet racking
- Shelving for picking
- Input conveyors
- Output conveyors for pallets
- Consolidation zone
- Preloads/sorting by routes area
Pallet racking area
It consists of one single and nine double racks that are 8 m high and 48.5 m long to store pallets from the loading docks.
Operators, who have direct access to all SKUs housed on racks, use reach trucks for handling goods.
The lower level of the racks is set aside for direct picking from pallets, because it is required for a high percentage of orders. Reserve product is stored on upper levels.
To streamline storage operations and, at the same time, as an additional security measure, an underpass that cuts across the racks was opened up. The first level of each rack above the safety passageway has mesh to prevent materials from falling.
For greater safety, the uprights of all the racks and the frames which coincide with the emergency aisle have been protected in order to absorb the impact caused by handling equipment during maneuvering of unit loads.
Picking shelves for boxes
On an area of more than 3,700 m2, a large variety of racking bays with six load levels were installed that comprise 39 storage aisles each 1.2 m wide.
The aisles are wide enough so that operators can move with specific trolleys and perform picking and the replenishment of products. In addition, there are two 2.5 m wide intermediate cross-aisles that cut across to the end of the block of racks. Thus, two trolleys can move simultaneously, which facilitates the movement of operators and the connection between all the racks comprising this zone.
Operators follow a method of grouping orders, allowing them to optimise the number of trips in preparing all items of multiple orders in a single trajectory.
For storage of smaller products, eleven storage levels were enabled at the ends of 40 shelves. Each level accommodates five boxes.
The space between the front of the racks and the conveyor circuit has been reserved for large-scale picking from pallets deposited on the ground.
Shelving levels are formed by slotted shelves that enhance the passage of water in case the fire safety system is activated. Vertical side mesh has also been placed that acts as a separator between the various bays and sides of the shelves.
Main conveyor circuit: consolidation zone
The boxes where items for orders have been placed are introduced onto a 38.2 m conveyor circuit capable of accumulating 51 boxes and transporting up to 1,000 boxes per hour.
Once they have traveled this distance, they continue to the top level so that the circuit transports them to the consolidation stations.
This area has twelve stations where operators separate the items and introduce them into the box used to ship the order. When the order is completed and before being transferred to the sorting area, it is packed and both the packing list and shipping labels are created. To perform all these tasks, each station has packing boxes of different sizes, prep tables, computers and printers.
When the order is consolidated and the shipping box packed, it is introduced onto the intermediate level of the conveyor circuit and transferred to the sorting area, where it will be grouped by routes and agencies.
This zone consists of thirteen conveyor ramps each 5 metres long and on a 4% incline. The last of all the conveyors was allocated to rejects or defective boxes that cannot be dispatched. The warehouse has eleven loading docks.
Empty boxes, used during picking and the eventual consolidation of the order, return via the lower level of the conveyor circuit. Finally, they arrive to a full pallet stacker which is tasked with stacking them and leaving them ready to be used again.
Reception and sorting of palletised goods
Just in front of the pallet racking, conveyors have been installed whose mission is to carry out inputs from loading docks and outputs of larger products.
For inputs, eight conveyors each 9 m long and on a 4% incline are arranged. Each station has a table where the operator receives the boxes extracted from the pallet. The operator verifies that the content is correct and sorts them to be stored according to the criteria configured by the warehouse management system.
Beside inputs and outputs, and especially reserved for bulky products, there are four conveyors each 12.6 long that move goods via gravity flow. In the centre of each line a semi-automatic strapping machine is set up. This area is also equipped with the computer equipment necessary to carry out the preliminary dispatch consolidation.
Picking trolleys
The warehouse has specific trolleys adapted to perform picking and replenishment of smaller sized products stored on the shelves.
Replenishment trolleys have four wire shelves, wire mesh that protects the ends and four wheels. Meanwhile, prep trolleys can carry up to 12 boxes of 336 x 518 x 302.5 mm, and are composed of three mesh shelves, six wheels and ladder set up on one end that facilitates the operator in picking at heights.
Communication: WMS and Galileo
The warehouse management software is responsible, among other functions, for managing all input processes, choosing the location where the goods are received, controlling stock, designating picking tasks to be performed by each operator, executing the movement of boxes, etc.
Also, the Galileo control program handles all automatic movements of the conveyor circuit. To this end, it is connected with the WMS itself in order to ensure efficient transport and placement of the boxes within the system.
Advantages for this warehouse
- High storage capacity: the warehouse has a total storage capacity of over 5,500 pallets and a large variety of boxes with smaller items.
- Logistics simplicity: a conveyor circuit eliminates a portion of the internal movements, increases agility and minimises errors in preparing orders.
- Variety of solutions: the facility has various storage solutions that fit all types of products.
Pallet racking area | |
---|---|
Storage capacity: | +5,500 pallet |
Pallet dimensions: | 800 x 1,200 x 1,400 mm |
Racking height: | 8 m |
Racking length: | 48.5 m |
No. of racks: | 11 |
Load levels: | 6 |
Gallery
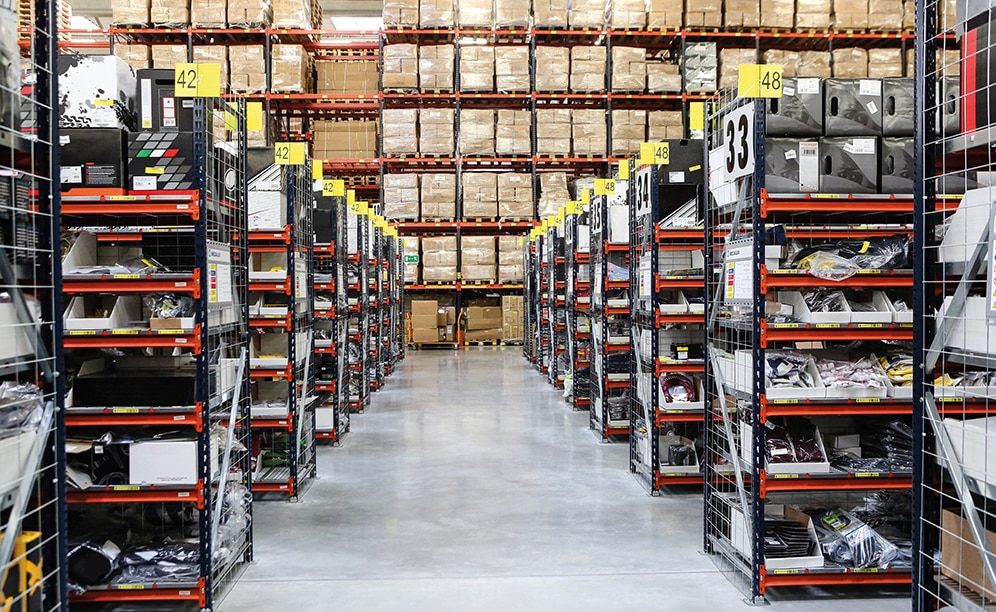
This warehouse is composed of pallet racking, picking shelves for boxes and a conveyor circuit that includes a sorting zone
Ask an expert