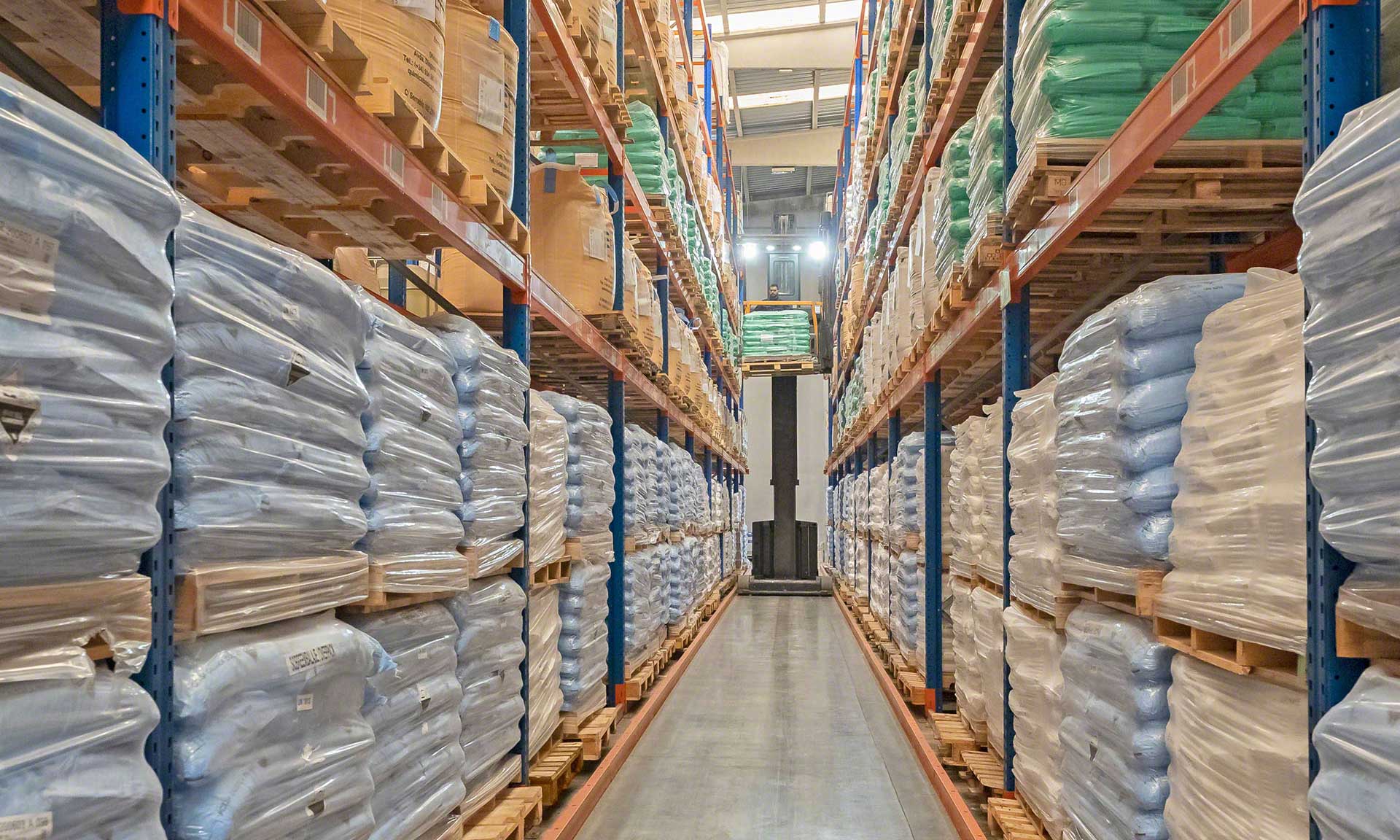
Global-TALKE: zoned warehouse with 1,000+ chemical SKUs
The storage systems facilitate the work of the operators and ensure safe storage of chemicals
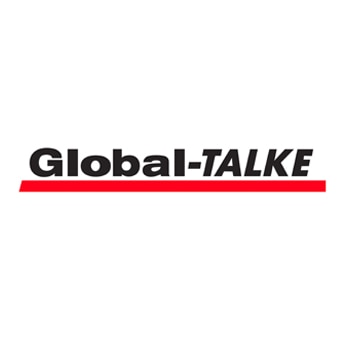
Global-TALKE, a logistics provider specialising in chemicals, boasts a logistics centre in Tarragona, Spain, with capacity for 30,0000 pallets divided into different warehouses for safety reasons. To equip each of these facilities, the company has installed two versatile and resistant storage systems: pallet and drive-in pallet racking that facilitate the safe entry and exit of around 1,000 pallets a day.
Logistics services for the chemical sector
In 2005, logistics service providers Global Spedition and TALKE Logistic Services pooled their experience and knowledge to create Global-TALKE. This 3PL (third-party logistics) provider offers all kinds of services to the chemical, industrial, and food industries: storage, packaging, bagging, mixing and transport in tankers.
Its headquarters are located in Tarragona, Spain, a strategic position due to its easy access to the AP-7 motorway — which connects the entire Mediterranean coast — and to the port. There, Global-TALKE has a large 38,820 m² logistics centre where it carries out all its logistics processes and distributes goods to customers, mainly in Europe, North America and North Africa. “Our strength lies in that, in the same space, we carry out basic logistics processes, such as goods storage, along with other innovative services such as micronising and blending of powdery solid products,” says César Garraza, Project Manager at Global-TALKE.
Because it manages 1,000 SKUs of chemical goods, and to comply with fire safety regulations for industrial establishments, the logistics centre is divided into different zones, with each section assigned to the products of a specific customer. The centre has been expanded various times to increase the storage area and incorporate new processes that will help the company to be more competitive. Global-TALKE’s complex logistics operations stand out for their bustling activity: every day, the centre receives about 500 pallets and distributes another 480. To avoid mistakes and boost agility, the company wanted to outfit the different warehouses with new storage systems that would facilitate safe product handling.
How are chemicals stored?
Facilities dedicated to the storage of chemicals must fulfil strict safety requirements, since, in many cases, they handle hazardous goods:
- Divide the warehouse into differentiated sections, assigning each of them to specific types of items. The access points should be kept clear and signposted.
- Store strictly necessary quantities of chemicals.
- Keep the chemicals in closed containers.
- Classify the products by hazard type (fire, corrosive, toxic, etc.).
- Use containers adapted to the corrosive effect of the substance they contain.
- Store the containers away from sunlight and low temperatures to prevent deformation.
- Ventilate the warehouse, especially zones with flammable products.
- Avoid work that could produce heat or sparks (e.g., welding) near the storage areas.
- Comply with applicable regulations: occupational risk prevention laws, chemical storage regulations, fire safety regulations for industrial buildings, and electrotechnical regulations for low voltage, primarily.
Two storage solutions
The warehousing systems that Global-TALKE needed had to comply with all security measures relating to the storage of chemicals. This means that the goods had to be easily accessible and that the distribution of the racks in the facility should keep handling to a minimum to avoid spillage and leakage. Taking this into account, Mecalux implemented two highly versatile storage systems to house the more than 1,000 different SKUs:
Pallet racking
This storage solution offers direct access to the products, making it easy to deposit and remove them from their locations. Moreover, each slot is intended for a single SKU, thus enabling perfect visual control of the stock.
One particular feature of this racking is its ability to adapt to any type of load, weight or volume. Garraza says, “With this solution, we haven’t just expanded our storage capacity — we’ve also considerably improved stock management. Now, we can organise the centre in line with our customers’ needs.”
The racks stand 9 m tall and provide storage capacity for 20,000 pallets in total. As the aisles are narrow — just 2.1 m wide — the operators use wire-guided trilateral forklifts to move inside them.
This handling equipment works with a wire embedded into the warehouse floor; the wire produces a magnetic field, which the machine detects and uses as a guide. With this solution, the machines move down the centre of the aisles, avoiding possible impacts against the structure of the racks and, above all, against the pallets.
Four levels of consoles have been set up on the ends of the aisles. There, operators deposit the pallets using counterbalanced forklifts. Due to its rotating head, the trilateral forklift can pick up and leave pallets in three positions: one on the front and two on either side. This way, it can pick pallets resting on the consoles and bring them to the correct location without having the leave the aisle.
Drive-in racks
Certain areas of the logistics centre are outfitted with drive-in racking. This compact storage solution is made up of lanes with up to five levels. Operators enter the lanes with the goods raised above the level on which they will be deposited.
"The advantage of this system is that it makes the most of all the available surface area to increase the storage capacity. We’ve boosted our warehousing capacity by over 50%,” says Garraza. The racks provide an overall storage capacity for 10,000 pallets.
Goods are managed according to the LIFO (last in, first out) method, where the last pallets to arrive are the first to leave. By having a single working aisle, goods are deposited and removed from this aisle.
Capacity and safety
Global-TALKE has equipped its logistics centre with two Mecalux storage solutions that accommodate over 1,000 SKUs of its customers’ products.
The pallet and drive-in racks facilitate the management of chemicals as well as the loading and unloading on and from the racks of approximately 1,000 pallets every day.
The two storage systems have helped us tremendously when it comes to optimally managing the products we store. In terms of the pallet racking, I’d stress the direct access, which enormously facilitates storage of all the products. As for the drive-in racks, we really like how they’ve leveraged the space to accommodate more products.
Advantages for Global-TALKE
- Storage of more than 1,000 SKUs: the pallets and drive-in racks provide sufficient versatility to efficiently manage a thousand SKUs of varying sizes.
- Direct access: the pallet racking allows direct access to the products, streamlining storage and order prep tasks.
- Safe goods management: the warehousing solutions installed are designed to facilitate the work of the operators and ensure the safe storage of the chemicals.
Pallet racking | |
---|---|
Storage capacity: | 20,000 pallets |
Pallet sizes: | 800/1,000 x 1,200 mm |
Max. pallet weight: | 1,333 kg |
Max. racking height: | 9 m |
Gallery
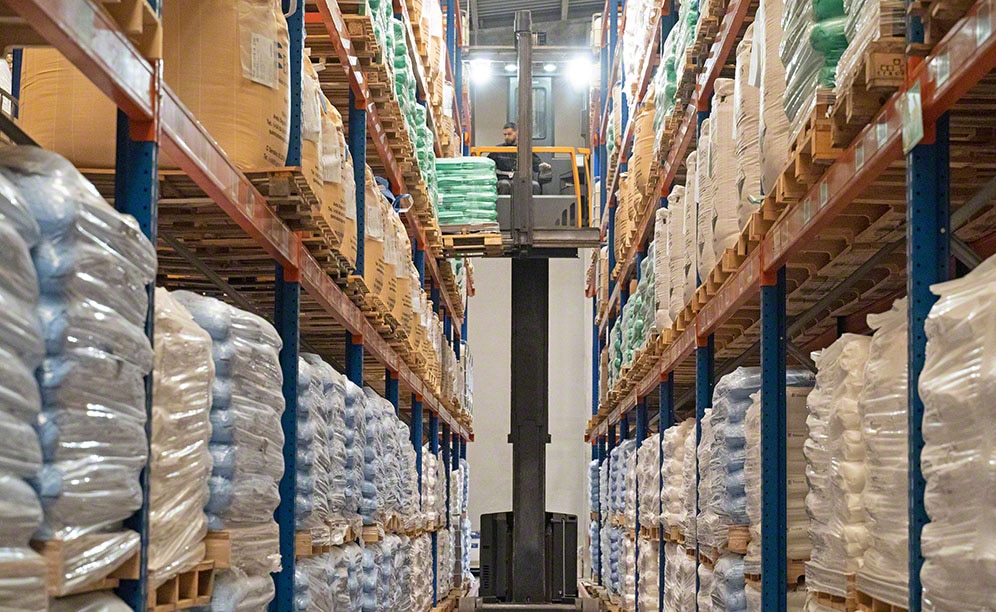
Global-TALKE warehouse for chemicals in Tarragona, Spain
Ask an expert