
Traceability in two digital warehouses
Easy WMS controls the traceability of IMP PUMPS' 1,000 SKUs distributed among its two warehouses
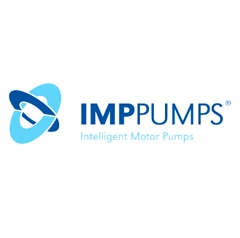
Slovenian pumping system manufacturer IMP PUMPS has its sights clearly set on driving its international expansion forward and providing its customers all around the world with optimal service. To do this, it has implemented the Easy WMS warehouse management system in its two warehouses in Komenda and Metlika (Slovenia). This software provides extremely accurate control and traceability of the more than 1,000 SKUs in stock. The result is greater flexibility in storage and order prep tasks, in addition to the elimination of errors.
Strong commitment to technology
Founded in 1947, IMP PUMPS is a manufacturer of pumps and pumping systems based in Komenda (Slovenia). In the 2000s, with the entry of Slovenia into the European Union, the company strengthened its international expansion, with very successful results. Currently, 96% of production is sold in 80 countries around the world (mostly in Europe, North America, Asia, Africa, North Africa and Australia).
Innovation is this firm’s main motivation. As such, it allocated 15% of its turnover to its R&D department. IMP PUMPS’ technical team works to come up with new energy-efficient and environmentally-friendly solutions.
The company has two production plants with its respective warehouses in Komenda and Metlika (120 km apart). At these warehouses, IMP PUMPS not only stores finished products, but also the components essential for the manufacture of the pumping systems.
When IMP PUMPS’ sales began to skyrocket, the firm realised it needed to improve the management of both installations. Peter Babič, Production Manager at IMP PUMPS, acknowledges, “Before, we didn't have enough control over our logistics processes, and we were using too much time and human resources to perform operations.”
At the time, all management was carried out manually (with pencil and paper); thus, there was a high risk of error. Between the two warehouses, the company oversees an average of 1,000 SKUs of different characteristics, sizes and turnovers. Keeping track of stock in real time — knowing the exact number of SKUs at every turn — is crucial for responding quickly to changes in demand and streamlining order prep.
To achieve this, it was imperative for IMP PUMPS to incorporate technology in its supply chain. Through a warehouse management system (WMS), the company would be able to offer its customers better service. Peter Babič understood this very clearly, stating, “Our priority was to obtain much more rigorous traceability of our products, tracking their path from the time they leave the production lines until they reach the customers.”
Digital logistics
IMP PUMPS sought support from Špica, a Slovenian technology company specialising in supply chain management solutions, to find software for its two warehouses. In turn, the software would be adapted to the particular characteristics of IMP PUMPS’ supply chain.
After analysing the company’s requirements, Špica’s technical team suggested installing Easy WMS, the WMS by Mecalux — because of its flexibility, adaptability and scalability.
Peter Babič affirms, “We chose Easy WMS because it could easily integrate with Pantheon, our ERP.” This is essential for ensuring that the two warehouses are running efficiently and for monitoring goods more strictly.
The ERP and the WMS continuously transfer information to achieve greater productivity and satisfy IMP PUMPS’s business needs. For example, when a customer receives an order, the ERP notifies the WMS so that it can arrange for the package to be prepared immediately.
Peter Babič - Production Manager at IMP PUMPS
“We chose Easy WMS because of its easy integration with our ERP, Pantheon, and its ability to adapt to the particular characteristics of both of our warehouses. This WMS gives us information in real time on the products, and it streamlines and speeds up all operations.”
Efficient organisation of both warehouses
Easy WMS manages the operations of IMP PUMPS’two installations. In the words of the Production Manager, “It intervenes in all processes, from the receipt of goods from production or suppliers to transfers between warehouses and order prep and dispatch.”
Goods receipt and storage
Every day, IMP PUMPS’ warehouses receive pallets from two sources: on the one hand, finished products directly from production, and, on the other, components sent by suppliers. It is then that operators, with the help of radiofrequency terminals, identify each item so that the WMS can assign them a location.
Easy WMS incorporates rules and algorithms to decide the best location for each product. These are based on parameters such as whether the item is a component or a finished product and its SKU, size and turnover. This way, the most popular products are placed in easily accessible locations to speed up their entry and exit.
“The improvement we’ve noticed the most in our day-to-day activities is, indeed, stock management. Now, the products are well organised; we can locate them really quickly and right when we need them,” says Peter Babič.
Optimal goods distribution results in safer, more streamlined warehouse operations. Workers merely need to follow instructions from the WMS to store the merchandise and prepare orders.
Another operation to take into account is the transfer of products between one installation and the other. Easy WMS supervises this process in detail to prevent mistakes and stockouts during goods movements. It does so by means of advance shipping notice (ASN). That is, Easy WMS is is notified in advance of the arrival of goods from another warehouse. When they are received, operators only have to check that the items that were expected match those that have actually arrived.
Thanks to this working method, IMP PUMPS has benefited, above all, from increased traceability. Peter Babič states, “Easy WMS provides us with real-time information on products and enables us to manage stock much more efficiently.” All items are properly identified and tracked from the time they arrive at the installation. Thus, they can be rigorously monitored up to their delivery to customers.
Order preparation and dispatch
To prepare orders, operators move around the warehouse, locating the required SKUs and placing them on pallets. The instructions from Easy WMS are so precise that the margin of error is minimal. The WMS tells the operators which aisle to go to, the exact location, the item and quantity they need to pick, etc. Once the pallet is full and the order has been completed, it is sent to the consolidation and packaging area.
There, Easy WMS generates a packing list, detailing the items that make up each order, packaging material used, weight and dimensions of the goods. This list is printed and attached to the pallet in question. Simultaneously, the list is sent to the Pantheon ERP to keep the sales team informed of orders that have been prepared and are ready for dispatch.
Next, the pallets are sent to the preload area, where they remain until the delivery lorry arrives. There, they are organised based on transport route and customer. Once the goods have been loaded onto the lorry, Easy WMS once again notifies the ERP to, thus, inform customers that their orders are on the way.
“Easy WMS also orchestrates the preparation of orders that have to be delivered to the production lines,” explains the Production Manager. Technically, the operation itself is the same: the workers travel up and down the aisles locating the SKUs requested. The difference is that, in this case, the components are brought directly to the production line.
Change that drives growth
Digitalisation has been the best solution in terms of satisfying IMP PUMPS’ logistics needs. Through technology, the company has full control over its goods movements and the various operations in its two warehouses.
Easy WMS is an intuitive software program that simplifies the work of the staff. Peter Babič explains, “New employees learn to use it very quickly. This was vital for us, now that we’re growing and hiring new personnel at both installations continuously.”
Optimal organisation of the two warehouses will help this company to grow even more. The Production Manager explains, “Although we’ve maintained our work pace, the coronavirus pandemic has certainly limited our future growth perspectives. Nevertheless, our expectations for the coming year are still very optimistic. We’re convinced that the WMS will help us to work in a way that’s organised, fast and error-free.”
Advantages for IMP PUMPS
- Total traceability: the WMS monitors the goods stored from the moment they arrive at either of IMP PUMPS’ warehouses until they are sent to the production lines or end customers.
- Agile, optimised operations: Easy WMS manages all goods movements (whether within a single installation or to transfer products from one warehouse to another). This prevents any possibility of error and facilitates order preparation and dispatch.
- Successful cooperation: Špica and Mecalux have worked as a team once again to find the right advanced technological solution for IMP PUMPS. Easy WMS is aligned with the particular features of this business and has boosted the efficiency of the company’s supply chain.
Gallery
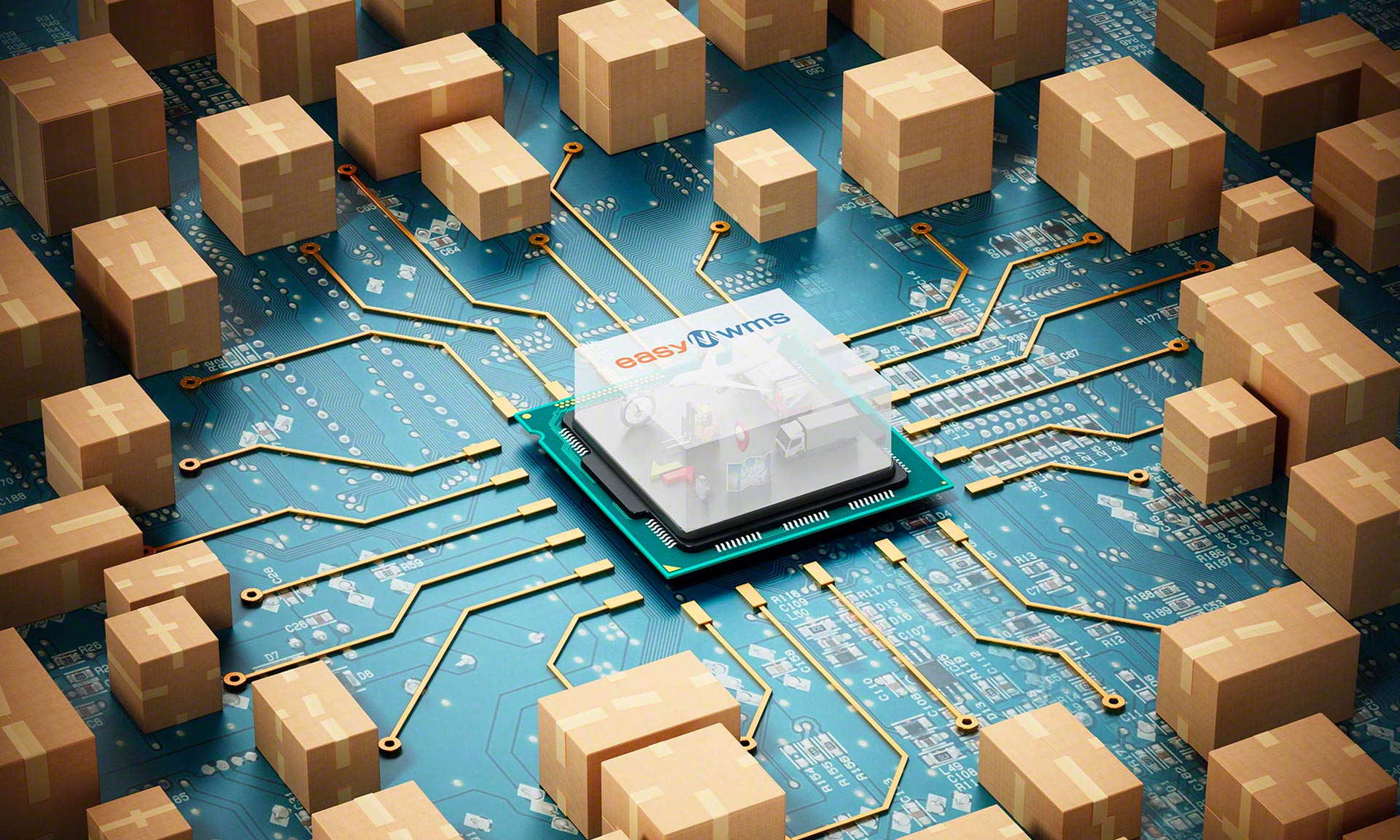
Easy WMS manages IMP PUMPS' two warehouses in Slovenia
Ask an expert