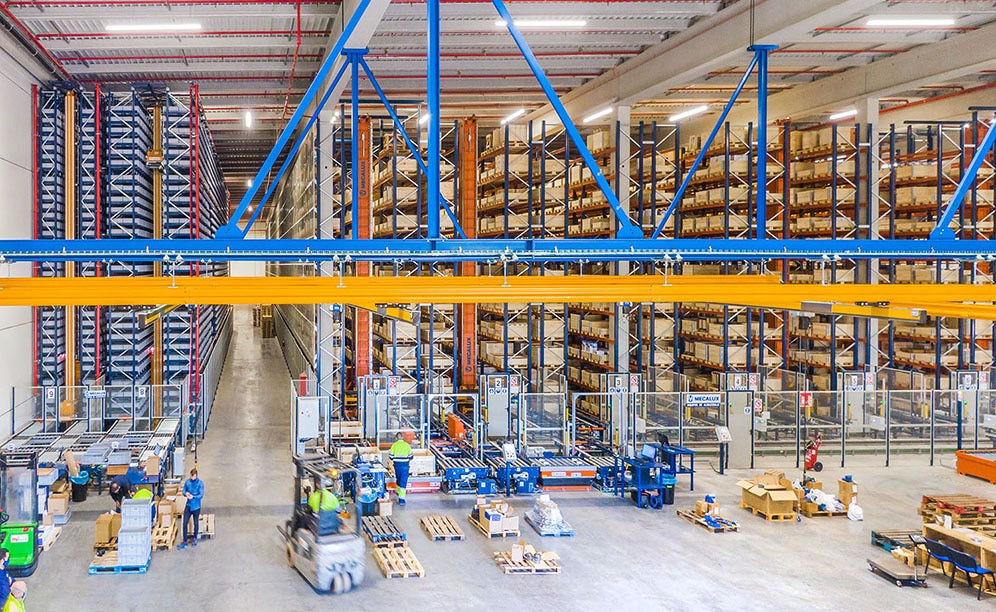
Industrias Yuk: centralised logistics, five installations in one with thousands of SKUs
The warehouse management system provides full traceability of the more than 13,000 SKUs
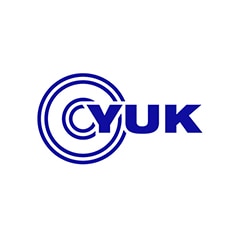
Industrias Yuk, a manufacturer of chains and industrial transmission components, has built a 10,200 m2 modern technological centre at the Valencia Logistics Park in Ribarroja, Spain, where it will centralise its logistics operations. It is made up of two automated warehouses: one for boxes, with 12,920 locations, and another with capacity for 15,246 pallets. Easy WMS, the warehouse management system from Mecalux, provides total traceability of the more than 13,000 SKUs and supervises all operations to maximise throughput and meet the needs of the company’s customers throughout the world.
Over 50 years of experience
Founded in 1964 in Ribarroja (Valencia, Spain), Industrias Yuk designs and manufactures metal chains for transport as well as transmission components for all kinds of industries.
With approximately 20,000 SKUs in its catalogue, the firm exports its products to more than 1,500 customers from 15 different sectors in over 40 countries around the globe.
In recent years, Industrias Yuk has been engaged in a technological modernisation process with a view to raising its activity throughput and diversifying its product portfolio. By incorporating new technologies, it has improved its production capacity. At the same time, it has begun to manufacture products that, up to now, it could not make and had to outsource. As a result, it was forced to modernise its supply chain.
To do so, it built a centre designed to be the business’s main logistics installation. The objective was to consolidate in a single space all the goods that were previously spread across five different warehouses.
Thus, in 2018, Industrias Yuk purchased a 14,700 m² parcel of land in the Valencia Logistics Park, a strategic location well-established as the ideal hub for all types of businesses, particularly transport and logistics companies. There, Industrias Yuk has built a 10,200 m² logistics centre comprising a storage area and offices, thereby positioning itself at the forefront if its sector.
The new warehouse, located just three 3 km from the firm’s production plant, is designed to store more than 13,000 SKUs of finished products, including chains, sprockets, transmission components, engines, gearboxes and accessories. For its activity, the business needed an automated storage system for both boxes and pallets. In the words of Santiago Agost, Systems Manager at Industrias Yuk, “We were convinced that it would help us reduce picking times and potential human errors and, at the same time, absorb the peaks in demand that we face from time to time.”
In addition to supporting Industrias YUK’s centralisation strategy, automation is the best solution for improving workplace ergonomics and minimising mistakes caused by manual picking. Thanks to the product-to-person order prep method, the movements of picking operators have decreased, while productivity has risen.
Rodrigo Andrés, Chief Commercial Officer at Industrias Yuk, says, “Out of all the storage system suppliers we contacted, Mecalux convinced us because it understood our needs and made us a proposal that met them. In short, we wanted more speed and flexibility.”
Industrias Yuk also required a warehouse management system (WMS) that connected directly and bidirectionally with its Geinfor ERP to monitor stock in real time and supervise goods receipt, storage, picking and dispatch operations.
Two automated warehouses in one
Industrias Yuk’s logistics centre consists of two perfectly complementary automated storage systems that work independently yet are both run and overseen by Easy WMS. These two solutions have enabled the company not only to sort products according to their characteristics and sizes but also to increase its efficiency in order prep. “We’ve gained in flexibility,” enthuse Rodrigo Andrés and Santiago Agost.
Additionally, an 11-metre-tall automated warehouse for pallets has been installed. It has seven 94-metre-long aisles, and a trilateral stacker crane travels along each of them. Thanks to its rotating head, this type of stacker crane has the advantage of picking and inserting pallets from/in the racks in three positions: the front and the two sides.
With a capacity of 15,246 pallets, this warehouse manages pallets with finished products that are mostly later used for picking. For this task, two pick stations have been set up in the front of the installation. The goods arrive there by means of a conveyor circuit and a transfer car.
Just alongside the warehouse for pallets is a new automated installation with capacity for 12,920 boxes measuring 400 x 600 mm. Standing 11.8 m tall with two 40-metre-long aisles, the warehouse has one aisle with double-deep racking on both sides and another with single-deep racking.
This installation stores small products in boxes weighing up to 100 kg, mainly accessories and components such as gears, nuts and small-sized material. In the front are pick stations equipped with all the elements necessary for carrying out this task efficiently.
The automated warehouse for boxes was devised taking into account Industrias Yuk’s growth prospects and, therefore, can be expanded at any time if the company requires it.
Ramped-up efficiency in operations
With these two automated warehouses, Industrias Yuk has centralised its logistics systems and, in turn, cut logistics costs by maximising resources, facilitating goods handling and streamlining picking.
The Easy WMS warehouse management system also plays a decisive role in this logistics centre, as it optimises the flows of both installations. “The fact that we could integrate it with Geinfor, our ERP, was a plus point. This process was rather quick, thanks to the work of the Mecalux software team,” highlights the Systems Manager.
Operations at this logistics centre are organised as follows:
Controlled goods receipt
The products are sent to the facility via lorries from the manufacturing plant or other warehouses or are shipped by suppliers in South East Asia. When a lorry leaves production or any of Industrias Yuk’s other installations, the ERP informs the WMS of the impending arrival of merchandise ready to be stored by means of advance shipping notice (ASN).
Once the lorry parks in the docking area, Easy WMS springs into action to manage the receipt of the goods. First, the workers identify each pallet using radiofrequency terminals. This ensures that the goods previously designated by the ERP match those actually delivered by the lorry.
After scanning each item, the system decides where to place each pallet based on the type of product it contains. Easy WMS applies several criteria when making this decision: item volume, unit load weight and turnover.
“With this way of working, we can ensure complete traceability of the goods,” affirms the company’s CCO. The WMS identifies and tracks the products from the moment they arrive at the warehouse until they are dispatched.
Before entering the automated installation for pallets, the goods have to go through a checkpoint, where their sizes are verified. If the measurements fall within the corresponding ranges, Easy WMS directs the stacker cranes to store the pallets in their assigned locations.
Error-free picking
Easy WMS is the foremost authority when it comes to organising order prep. The high degree of automation enables orders to be prepared according to the product-to-person principle, cutting down on operator movements and streamlining the entire operation.
Orders can include products from the automated installation for pallets, the automated warehouse for boxes or both. Those orders that include products from both installations are consolidated in a specific area just in front of the loading docks.
The operation begins in the automated warehouse for pallets, where products are sent to one of the picking posts via a transfer car and conveyors. The workers then remove the items they need in order to put together each order. If the original pallet is left with few (small-sized) goods, they are stored in the automated installation for boxes. This frees up space in the automated warehouse for pallets.
Picking in the automated warehouse for boxes is carried out in practically the same way, minus the presence of a transfer car. The boxes are brought to the pick stations automatically by means of conveyors. Once there, operators follow instructions from Easy WMS via radiofrequency terminals. When the order is completed, it is sent to the dispatch area.
For every picking task carried out, Easy WMS sends a message to the ERP, reporting on the particular characteristics of each order: products included, quantity, origin, etc. Upon closing an order, Easy WMS prints a label that provides access to all these data when scanned with a barcode reader.
Goods dispatch
All orders are sent to the consolidation area, where they are grouped on the floor, waiting to be moved to the loading docks. Using radiofrequency terminals, the operators verify that no mistakes have been made during order prep. Once this process has finished, the parcels are sent to the assigned dock following the sequence defined by Easy WMS.
Finally, Easy WMS creates an order for the lorries to be loaded. These indications assure operators that they are loading the right goods onto each lorry.
A technological and innovative logistics centre
Industrias Yuk has opened a high-tech logistics facility that enables it to grow by leaps and bounds and achieve maximum efficiency in its supply chain.
The two automated warehouses provide storage, picking and dispatch flows with agility and safety. In a project of such magnitude, it is essential to carry strict control of the goods and of orders containing products from both automated installations. Following instructions from Easy WMS, order delivery is much speedier in addition to error-free.
Automation has brought numerous advantages to Industrias Yuk’s logistics centralisation strategy. These mainly comprise lower logistics costs due to staff optimisation, increased productivity and total availability, as the facility can run 24 hours a day at maximum throughput.
Santiago Agost - Systems Manager at Industrias Yuk
“We’re pleased with our logistics centre: it’s allowed us to speed up all our operations, and we’ve gained full traceability of all our products. We’re in the process of merging our five installations into this one, so we expect this to become Industrias Yuk’s only facility within a year.”
Advantages for Industrias Yuk
- Unified logistics: this manufacturer of chains and industrial transmission components has a modern, technologically-driven logistics centre. There, it concentrates all its goods, which were previously distributed among five different installations.
- Goods traceability: Industrias Yuk knows — at all times — which stock is available, where it came from, where it is located and where it is headed. The more than 13,000 SKUs are optimally organised based on the company’s requirements.
- Picking productivity: automation considerably improves the concept of workplace safety and ergonomics, which is especially beneficial in order prep operations. Easy WMS can manage orders made up of pallets, boxes or both, without error.
Automated warehouse for pallets | |
---|---|
Storage capacity: | 15,246 pallets |
Pallet size: | 800 x 1,200 mm |
Max. pallet weight: | 1,000 kg |
Racking height: | 11 m |
Racking length: | 94.1 m |
Gallery
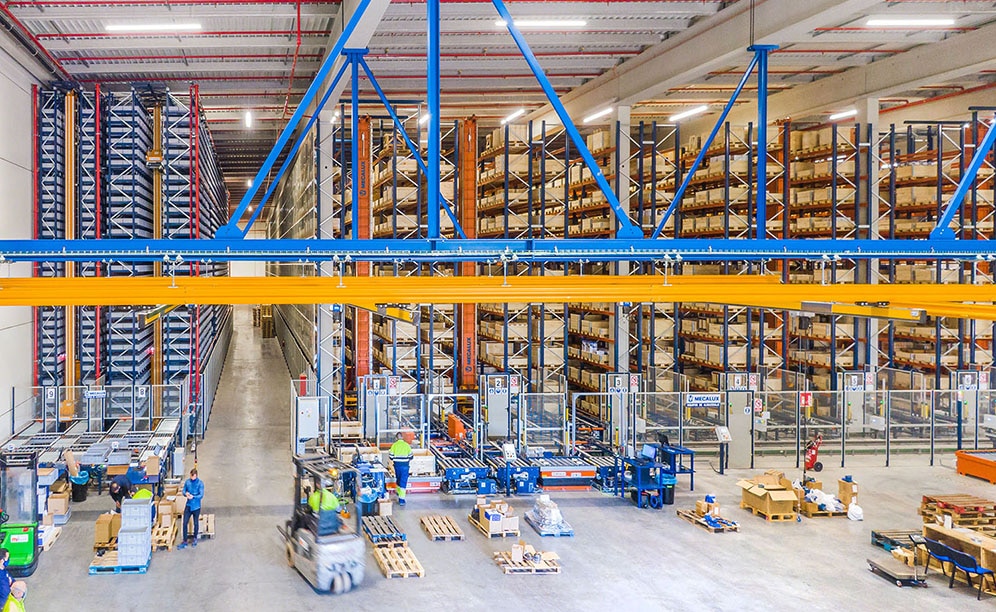
Industrias Yuk's highly automated logistics centre in Ribarroja
Ask an expert