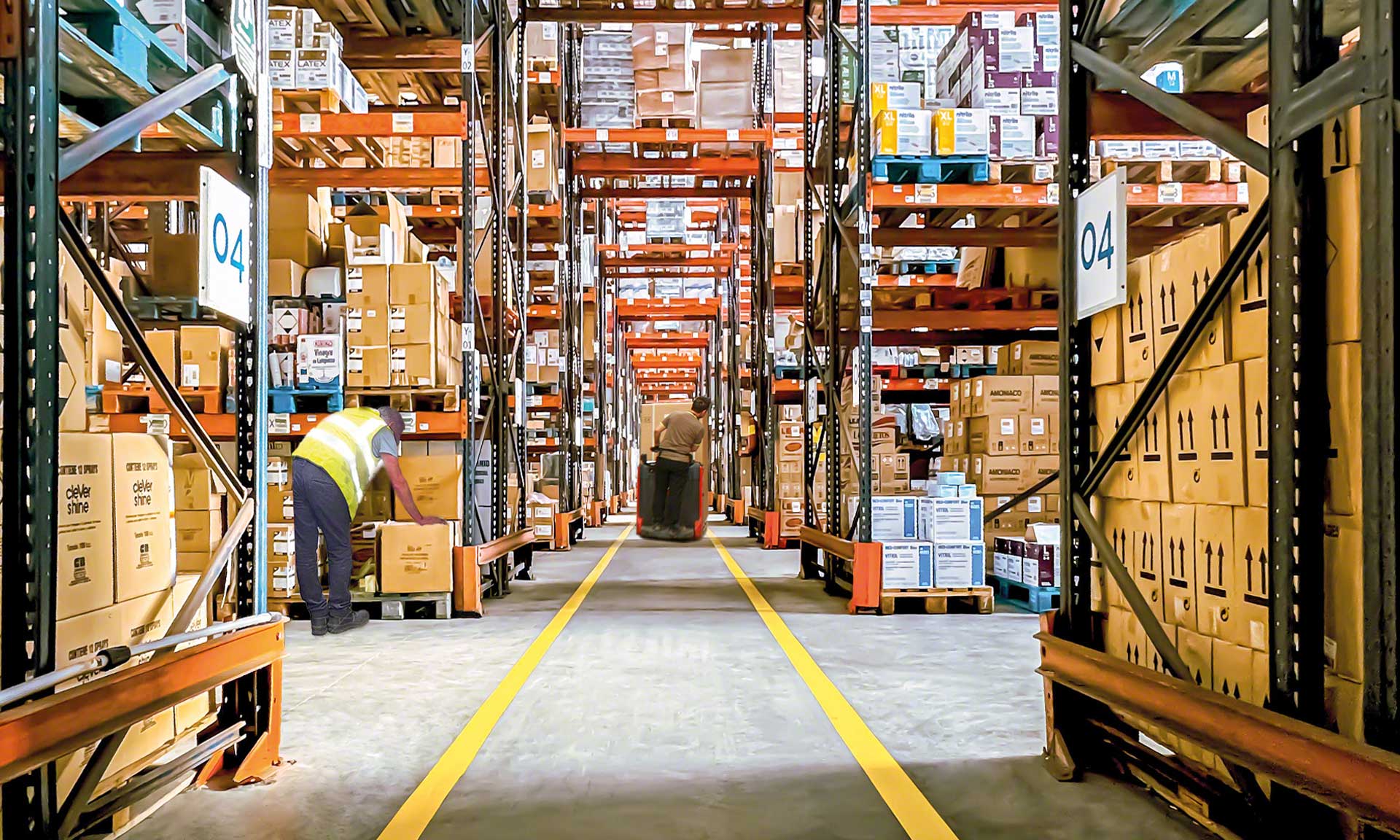
Pedrosa monitors its industrial hygiene products with Easy WMS
Pedrosa has installed Easy WMS to control its 2,800 SKUs in real time and fill 600 orders a day.
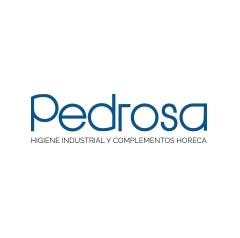
Industrial hygiene products company Pedrosa has installed Easy WMS in its facility in Palma de Mallorca, Spain. With this program, the company controls a wide variety of SKUs and optimises its operations, from goods receipt to dispatch.
Pedrosa: industrial hygiene products
Pedrosa is a distributor of industrial hygiene products and supplies such as professional cleaning materials and chemicals for swimming pool maintenance. From its logistics centres in Mallorca, Ibiza and Menorca, the company distributes products to its customers. These include hotel chains, restaurants, pubs, catering businesses, gyms, schools, universities and government agencies, among others.
- Founded in: 1972
- Total storage space: 6,000 m²
- No. of employees: 70+
CHALLENGES
|
SOLUTION
|
BENEFITS
|
---|
Pedrosa has modernised its supply chain to boost its rate of expansion. “Our company has grown exponentially over the past few years, and this compelled us to gain greater control of our logistics operations,” says Tony Cursach, CEO of Pedrosa.
In recent years, the hygiene and cleaning products sector has undergone a remarkable transformation. “Before, there wasn’t such a variety of products compared to now, and with few SKUs, we were able to cover all our customers’ needs. Today, the sector is highly professionalised: there’s a product for every specific demand,” says Cursach.
With a larger number of solutions, the business can accurately fulfil all customer requirements and provide better service. The logistics challenge this presents, however, is quite complex: how do you efficiently manage growing numbers of SKUs and orders? The key lies in digitisation. By employing technology solutions such as a warehouse management system (WMS), companies can rigorously control their inventory and fine-tune their processes.
“At our facility in Palma de Mallorca, we prepare and dispatch about 80,000 orders a year. With such a large number of goods in constant movement, we needed tighter control over our stock to avoid errors and mismatches. We decided to install warehouse management software that would help us provide our customers with better service. After weighing several options, we chose Easy WMS, the program from Mecalux, because we knew it would optimise our logistics operations,” says Cursach.
Commitment to digitisation
For years, Pedrosa used its own computer system to organise its logistics processes. “But we had a lot of information gaps,” says Cursach. As the number of SKUs rose (reaching up to 2,800 with distinct characteristics, storage requirements and demand levels), the company realised that change was inevitable.
For Pedrosa to go a step further — i.e., to increase its efficiency in storage tasks, ramp up its warehouse productivity and control its inventory — it had to implement a more sophisticated logistics software program.
“We came to the conclusion that we needed to digitise our supply chain to improve our operators’ performance. Installing WMS software in our facility was the pinnacle of our transformation,” says Cursach.
Digitising its processes with a flexible, scalable software program such as Easy WMS has allowed Pedrosa to adapt to business changes, e.g., increases in demand and in the number of SKUs.
“We’re happy with Easy WMS because we can supervise all movements of goods in the warehouse. Plus, we know the status of our inventory in real time. Since the software orchestrates all operations, we now have a meticulous record of all tasks carried out. Ultimately, we have much more effective control over our logistics processes,” says Cursach.
Easy WMS is integrated with Pedrosa’s ERP system, so the two programs communicate with each other continuously and bidirectionally. They transfer data and information that are essential for getting the most out of all the logistics operations performed in the facility. For example, Easy WMS notifies the ERP system of replenishments so that it can organise purchases from suppliers.
Advanced warehouse management
Easy WMS intervenes in all processes in the facility, from location management to order picking and dispatch. The program distributes the work among the operators, showing them which items to collect for each order and the exact location of these products on the racking.
Pedrosa’s business is seasonal. During peak season (April to October), the workload increases considerably due to higher demand from customers, particularly hotel chains. To ship all orders without errors or delays, proper organisation of warehouse operations with Easy WMS is vital.
These are the main operations carried out through Easy WMS:
- Goods receipt. During the high season, the number of pallets received rises tenfold, up to 150 a day. Pallets arrive at the facility from suppliers in Spain and other European countries. The operators read the barcodes on the pallets with their RF scanners. The WMS identifies them, enters them in the database and assigns them a location.
- Storage. Easy WMS incorporates rules and algorithms to distribute Pedrosa’s 2,800 SKUs strategically, taking into account the available warehouse slots and orders to be processed. The software then assigns operators storage tasks, showing them which items to pick and which position to deposit them in.
- Inventory management. In addition to controlling stock continuously (the stored goods are updated in the system in real time), Easy WMS organises the physical inventory. To do this, operators count the stock in the facility item by item to know which products are available. The program sends operators instructions on which goods to locate and count. With this process, the company verifies and guarantees that the products are in ideal condition.
- Order picking. Every day, Pedrosa fills 500 to 600 orders. As directed by Easy WMS, operators walk up and down the aisles, removing from the racking the items required to put together the orders. The software calculates the optimal travel distances, making operators more efficient.
- Dispatch. Pedrosa can distribute up to 150 pallets a day during its busy season. These are sent mainly to customers in the Balearic Islands. In the preload area, pallets are grouped by order or route, streamlining the distribution of loads onto the trucks.
Besides organising warehouse operations, Easy WMS facilitates and optimises operator tasks. “The program is very intuitive and user-friendly. New workers joining the company don’t necessarily have to be familiar with the products — all they need to do is follow the commands from Easy WMS,” says Cursach.
The road to innovation
Digitisation and automation are in Pedrosa’s DNA. With the help of technology, Pedrosa can take on market changes, e.g., rising demand during peak season.
“We’re still exploring the infinite possibilities of Easy WMS. We hope to apply all its functionalities to work more efficiently every day. In the first year since we installed it, we’ve minimised stock imbalances in the facility,” says Cursach.
For an organisation with a high business volume like Pedrosa’s, warehouse management software is an invaluable tool: it is instrumental in streamlining supply chain operations. Thanks to Pedrosa’s advanced, innovative logistics processes, the company aims to continue meeting its customers’ needs effectively and to expand its market.
We’re happy with Easy WMS because we can supervise all warehouse movements. Plus, we know the status of our inventory in real time. Since the software orchestrates all operations, we now have a meticulous record of all tasks carried out. Ultimately, we have much more effective control over all our logistics processes.
Gallery
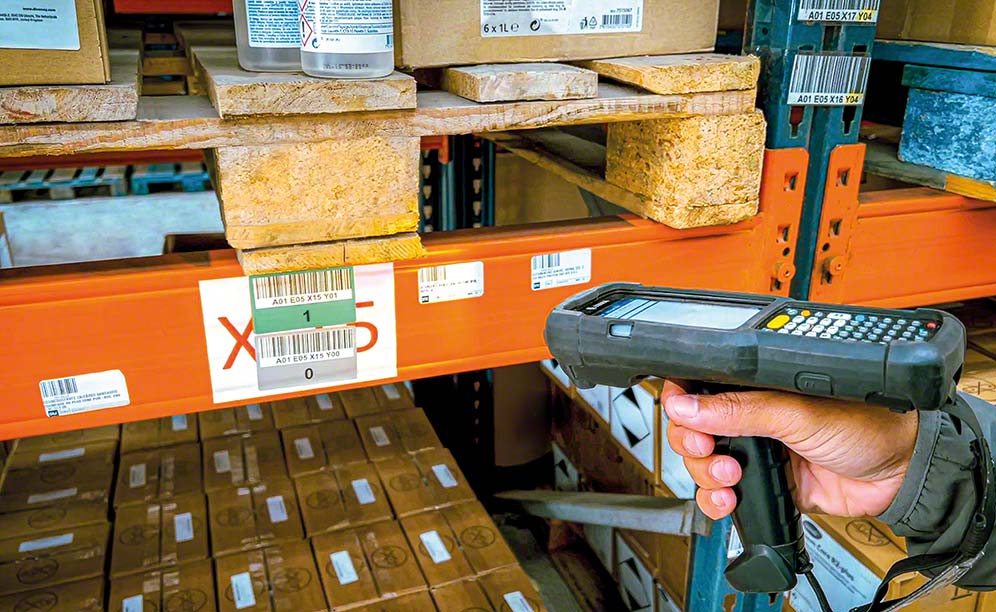
RF scanners for following instructions from Easy WMS
Ask an expert