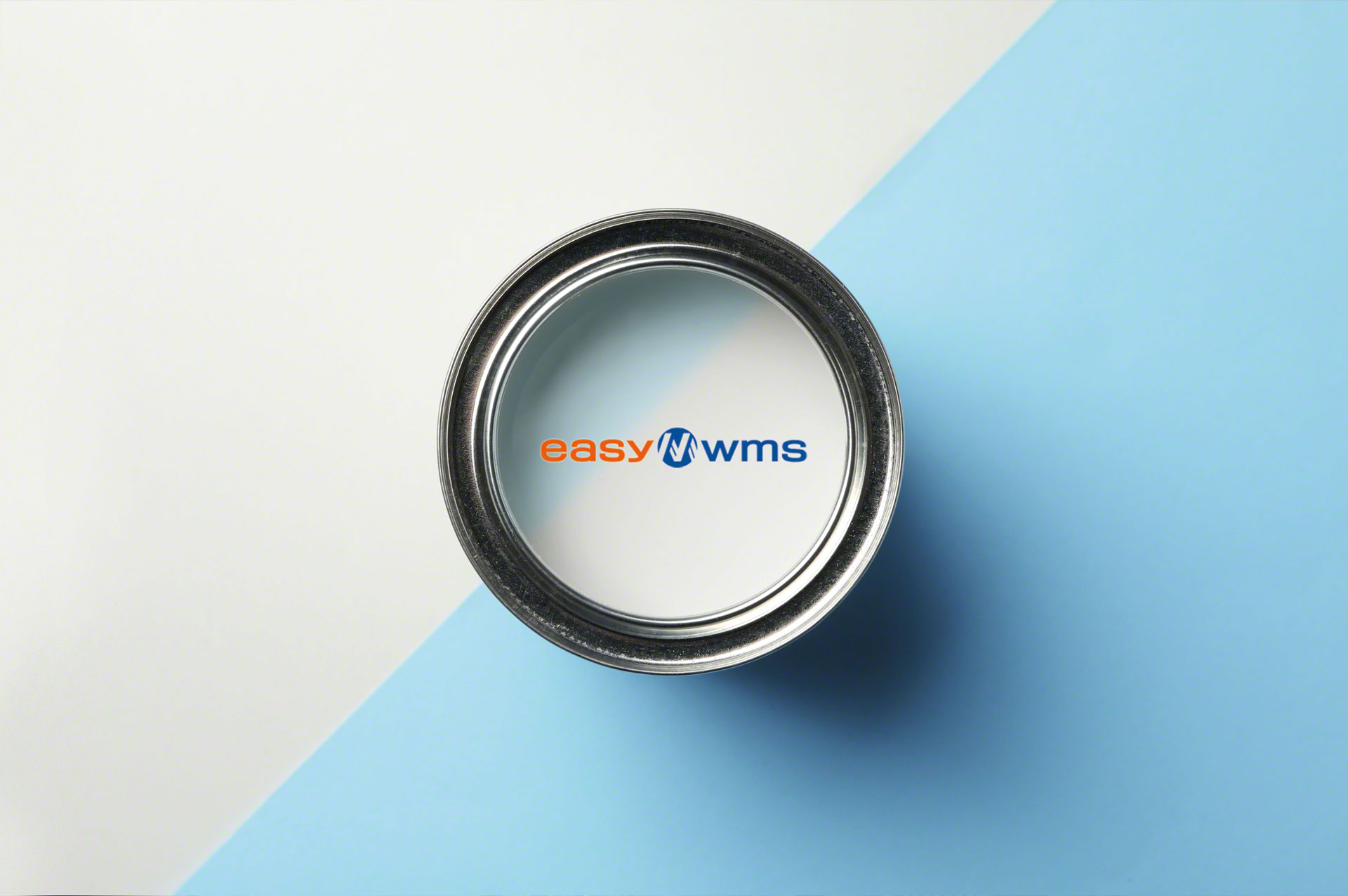
Pinturas Lepanto digitalises its logistics operations to manage over 2,500 SKUs
Pinturas Lepanto, a manufacturer of decorative paint, has digitalised its warehouse to boost picking.
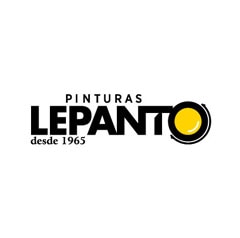
The decorative paint manufacturer Pinturas Lepanto has overhauled its warehouse in Spain with the installation of Mecalux’s Easy WMS. The program accurately monitors products as they come off the production lines until their delivery to end customers.
Pinturas Lepanto: passion for painting
Founded in 1965, Pinturas Lepanto is a family-run business devoted to the manufacture and sale of decorative paint with satin, gloss and matte finishes for all kinds of surfaces. The company is built on three values: quality, trust and good service. Innovation and research are intrinsic to Pinturas Lepanto, along with its commitment to developing effective, environmentally friendly solutions.
- Founded in: 1965
- No. of employees: 40
- International presence: Andorra, France, Spain and Romania
- Total surface area: 9,000 m² for offices, a laboratory and production, and 4,500 m² for storage space
CHALLENGES
|
SOLUTIONS
|
BENEFITS
|
---|
“Our business is currently going through a period of growth with very favourable future prospects. To drive forward the rate of expansion, we needed to optimise our logistics processes and be more competitive,” says José Ignacio Ruiz, Warehouse Manager at Pinturas Lepanto in Binéfar, Spain.
Effective supply chain management is a priority for this decorative paint manufacturer. “We have more than 2,500 SKUs in stock, which calls for tight control to avoid mistakes,” says Ruiz. To guarantee the traceability of its products in real time, Pinturas Lepanto has modernised its facility with Mecalux’s Easy WMS. This warehouse management software greatly enhances operational efficiency and performance.
Pinturas Lepanto’s logistics facility was overhauled in stages. The company first contacted Mecalux to equip its warehouse with two storage systems to house goods coming off the production lines: adjustable pallet racking and drive-in pallet racking. But the business wanted to take its operations to the next level.
“We realised that in addition to expanding our storage capacity, we had to improve our logistics processes,” says Ruiz. The company required a logistics solution that would control all its operations and streamline product picking and distribution.
Easy WMS is involved in all warehouse processes, from goods receipt to the storage and dispatch of orders shipped to customers in Spain, Andorra, France and Romania.
“Our logistics operations have been fully optimised. We’ve gone from managing processes manually to rigorously monitoring our goods with the Mecalux software,” says Ruiz. Before, Pinturas Lepanto organised its supply chain with an internal management program. However, it was unable to take care of logistics operations. The company knew it needed a more advanced system centred on warehouse management.
Easy WMS has boosted Pinturas Lepanto’s logistics processes. The software was integrated with the business’s ERP system, transferring data and essential information to control the facility more efficiently and make processes more cost-effective. For example, by connecting both systems, Easy WMS knows in advance which products will arrive at the warehouse and ensures that the necessary items are available to fill orders.
Operators communicate with the Mecalux software via RF scanners, where they receive instructions on preparing orders quickly and without making mistakes. “The Easy WMS interface is extremely intuitive. Our operators have learnt how to work with it really quickly.”
Optimised processes
Easy WMS has enhanced the entire facility, from the way products are organised and distributed in the storage systems to the methods for performing the different operations. The software helps Pinturas Lepanto offer its customers a higher level of service, with on-time, error-free deliveries.
Goods receipt and storage
Next to the production lines, Mecalux has installed a block of adjustable pallet racking units that acts as a buffer. These racks temporarily house products waiting to be moved to the storage area.
Operators merely identify the pallets by reading the barcodes with their RF scanners and Easy WMS records them in its database and assigns them a location. The system uses advanced algorithms to decide where to slot each item, considering factors such as SKU type, size and demand level.
When assigning the goods a location, it is vital to bear in mind their characteristics to guarantee smooth operations. For instance, pallets containing bulky and heavy products can only be placed in lower positions to prevent them from accidentally falling. Likewise, some paints containing flammable or corrosive components are deposited in a restricted area away from other products.
Organising the goods has a direct impact on other logistics operations. “By distributing the products correctly, we’ve reduced the distances operators have to travel around the facility. And that goes for storing items and picking orders,” says Ruiz.
Tintometry
One of Pinturas Lepanto’s main operations is tintometry. This consists of replicating the specific colour requested by a customer from an unlimited range of tones. The company uses the pallet racking serving as a buffer to store white paints that go back to the production lines to be transformed into customers’ colours of choice.
To carry out the tintometry process, the ERP system informs Easy WMS of the white paints it needs. The WMS then sends operators instructions to locate the items and move them to production. This software ensures that operators travel the shortest distances to deliver the goods on time and avoid manufacturing delays.
Order picking and dispatch
Every day, the Pinturas Lepanto warehouse picks and distributes 100 orders, each made up of 10 to 15 lines. “With an ever-increasing number of orders, we wanted to minimise any possibility of error,” says Ruiz.
Easy WMS tells operators which location to go to and which items to pick from the racking. When preparing orders, the software takes into account the products’ weight and size. Operators first retrieve the heaviest barrels of paint and then place the smaller tins on top.
Orders are picked individually, one after the other. An operator travels around the facility, gathering the products that make up a single order. After, the person brings the goods to the consolidation and preload area.
The Pinturas Lepanto warehouse also merges orders, grouping those belonging to the same customer (e.g., a client might order some paints in the morning and others that afternoon). Before loading the delivery lorry, the operators verify that each order contains the products requested. “Thanks to the control and instructions from Easy WMS, we never ship incomplete or wrong orders,” says Ruiz.
Some customers place large orders well in advance. In these cases, Easy WMS directs the goods to be grouped in a specific area in the facility as they leave production. When all the items are available, they are then distributed.
Logistics operations designed for growth
During its 50 years in business, Pinturas Lepanto has continuously improved its manufacturing and logistics processes to broaden its market. Digitalising its supply chain with Easy WMS is part of the company’s plans to better serve its customers.
“For us, the key was to fine-tune our warehouse operations, especially order picking. With Mecalux’s Easy WMS, all our items are properly organised, making processes much faster,” says Ruiz.
As the Mecalux software is scalable, it can adapt to changes in Pinturas Lepanto’s business, such as the rising number of orders. This system will accompany the organisation in its future plans, ensuring advanced logistics operations capable of satisfying customers’ most demanding needs.
The Easy WMS warehouse management system gives us very tight control over all our products. With this software, we can find out the exact location of any item in real time. We’ve also optimised picking, speeding up order distribution and eliminating any chance of error.
Ask an expert