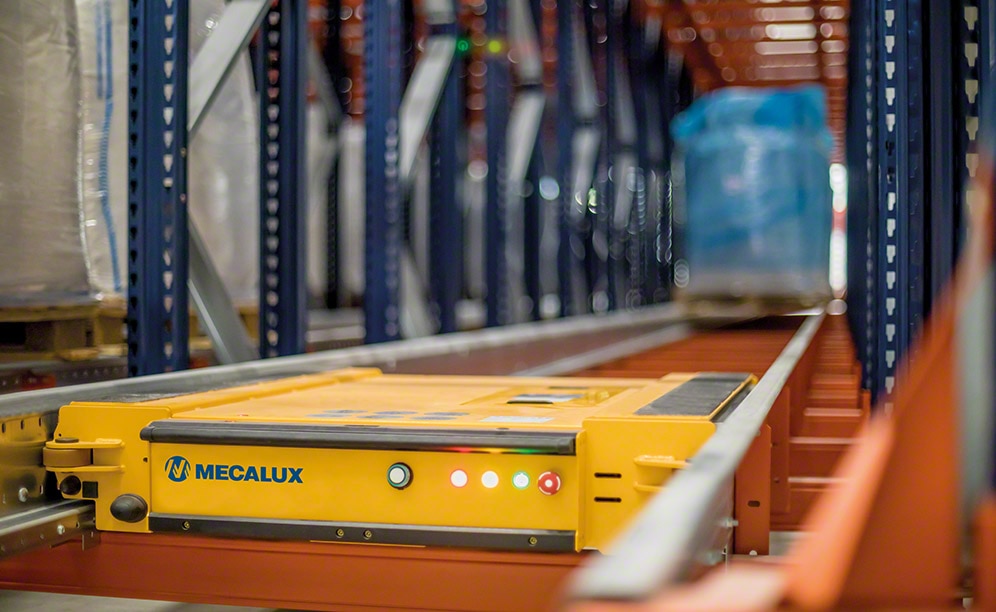
A powered ingredients warehouse for the agribusiness industry
Easy WMS and the WMS & Pallet Shuttle Integration are Huijbregts Groep's two new software
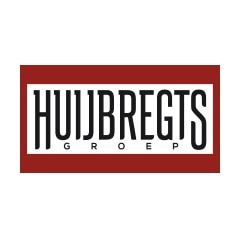
Huijbregts Groep, a powder ingredients maker for the food industry, has a new block of racks run by the Pallet Shuttle system with a capacity for 2,295 pallets in its production warehouse in Helmond in the Southern Netherlands. It has deployed the Easy WMS warehouse management system to manage product loading and unloading, as well as a specific software to control how the automatic shuttles function. The productivity and potential that the Easy WMS yields convinced the company to use this WMS in all its installations to better organise the warehouse operations that it carries out there.
Innovation and vision
Huijbregts Groep is in the business of managing and processing powdered ingredients for the food industry. Its history is marked by continuous evolution, innovation and harmonisation with market changes.
In 1936, Wim Huijbregts founded this company that, at first, sold food substitutes. After World War II, this entrepreneur started mixing herbs and spices for butchers in the Eindhoven region.
From 1973 onwards, when his son Frans Huijbregts joined the business, the firm experienced huge growth that continues until today. At present, 80% of goods sold in the Netherlands includes something made with the ingredient mixes of Huijbregts Groep. On top of that, they are expected to keep growing, even internationally.
More capacity for an ever-expanding company
In 2010, Huijbregts Groep opened a massive centre (filling a 5,000 m2 surface) in Helmond. It is a highly modernised installation with the latest in cutting-edge technology for achieving top productivity of all operations, including mixing ingredients, packing these mixes based on each order, and storing. According to Erik van den Nieuwelaar, manager of the innovation department of Huijbregts Groep, “our company manages around 2,500 SKUs of raw materials and another 14,000 finished products.”
“Our company is growing in leaps and bounds,” points out Erik van den Nieuwelaar. Little by little, the company’s centre became too small. So, it needed to expand its storage capacity with a solution explicitly meant to house raw materials and finished products.
“There was no more space to build a new warehouse. So, that is why we made full use of every millimetre at our disposal,” added Erik van den Nieuwelaar. “Moreover, the assembly of the racks had to be done on the double because we urgently needed this storage space.”
Each day, the warehouse receives an average of 200 pallets of raw material that it forwards to manufacturing. According to the innovation manager, “These pallets arrive from around the world, chiefly from inside a 1,000 km radius in Europe —although 30% do not.” On the other hand, it also ships out between 250 and 300 pallets of finished product to its customers spread throughout the world. Although Huijbregts Groep considers these finished products, their customers do not. In reality, these are semi-finished products that are used to produce margarine, bread, yogurt, soups, sauces or snacks, among other foods.
Considering this work volume, Mecalux has equipped the warehouse with a block of racks run by the Pallet Shuttle system. The assembly and installation were done over a period of approximately four months, to let Huijbregts Groep continue its operations uninterrupted.
The Easy WMS was also installed, the robust warehouse management system designed to run all the centre’s operations, as well as the Pallet Shuttle control software (specifically for directing the automatic shuttle of this storage system).
“This is our first time working alongside Mecalux. Before making any sort of decision, we compared its proposal with ones from two other storage solution providers. Finally, we handpicked Mecalux because they could offer us a better solution for our requirements and, of course, we also appreciated the price,” stressed Erik van den Nieuwelaar.
Pallet Shuttle features
The block of racks stands 13 m tall and, featuring a total of 85 channels that are 26.5 m deep, houses pallets with a 1,100 kg maximum unit weight. According to Erik van den Nieuwelaar, “we use this solution to organise 2,500 SKUs of raw materials and another 14,000 of finished products.”
Goods management fulfils the FIFO criterion (first in, first out). Pallets are inserted into one side of the racking units (e.g. on the side facing the loading docks when dealing with raw materials). Then, they are extracted out the other side, which, in this case, faces manufacturing.
The entrance and exit can also work in the opposite direction (i.e. from manufacturing to the docks), if finished products are ready to be shipped out.
The warehouse has five Pallet Shuttles to manage the volume of movements throughout each day. Along one side of the warehouse, some 14 m high pallet racks were installed that are six levels high. These act as a buffer, i.e., up to 303 pallets are kept on hold, waiting to be deposited in the racks by the Pallet Shuttles.
A potent software to control the Pallet Shuttle
Mecalux has installed a software specifically to control the Pallet Shuttle. The main advantage is that it gives better charge over products and facilitates the optimum organisation of storage tasks that must be carried out. In the words of Erik van den Nieuwelaar, “this software is both comprehensive and easy to use.”
Operators have Wi-Fi connected tablets to send commands to the motorised shuttles (i.e. insert or extract pallets). As the interface is user-friendly, no specific training is required for its usage. Numerous functions are carried out through these devices, such as selecting how many pallets to extract, counting inventory, checking Pallet Shuttle statuses and managing authorised users. Furthermore, while they are carrying out pallet loading and unloading, operators can view the orders that they must do up next.
This is a versatile, flexible software, which was moulded to the particular needs and features of the Huijbregts Groep warehouse: basically, a single block manages both inputs of raw materials and outputs of finished products. The software that runs the Mecalux Pallet Shuttle provides better control and safety during pallet inputs and outputs.
Easy WMS: an instrument for growth
According to Erik van den Nieuwelaar, “Normally, we develop our own software in our Innovation Department. However, due to business expansion and the arrival of some new projects, we requested Mecalux’s assistance.”
As a first step, Huijbregts Groep contracted the basic “Pro” version of Easy WMS. This system manages and coordinates the warehousing processes and movements: receipts, storage and dispatch of exit orders.
However, as Erik van den Nieuwelaar states, “What we really needed was a flexible system and one that talks to our ERP.” Realising the huge potential the Easy WMS offered, the company decided to deploy the most advanced and powerful “Enterprise” version —for the specific purpose of managing all operations in its Helmond centre.
Erik van den Nieuwelaar - Innovation Manager at Huijbregts Groep
“We are thrilled with the Pallet Shuttle system, with the software that runs the automatic shuttles and the Easy WMS of Mecalux. From its installation, the warehouse has turned out excellent results. Giving exact figures is hard, but, between February and August of 2018, we stepped-up our sales volume by around 8%.”
Advantages for Huijbregts Groep
- Efficient management of all operations: Easy WMS from Mecalux is set up to optimise operations in the entire Huijbregts Groep centre, both automatic or manual ones, as well as keep pace with future changes.
- Speedy high-density system: among compact systems, the Pallet Shuttle is the most agile when facilitating the insertion and extraction of pallets from their channels.
- Space purposing: the racking unit hones the available surface area to yield a 2,295-pallet capacity.
Warehouse of Huijbregts Groep | |
---|---|
Storage capacity: | 2,598 pallets |
Pallet size: | 800 x 1,200 mm |
Max. pallet weight: | 1,100 kg |
Racking height: | 13 m |
Racking depth: | 26.5 m |
No. of shuttles: | 5 |
Gallery
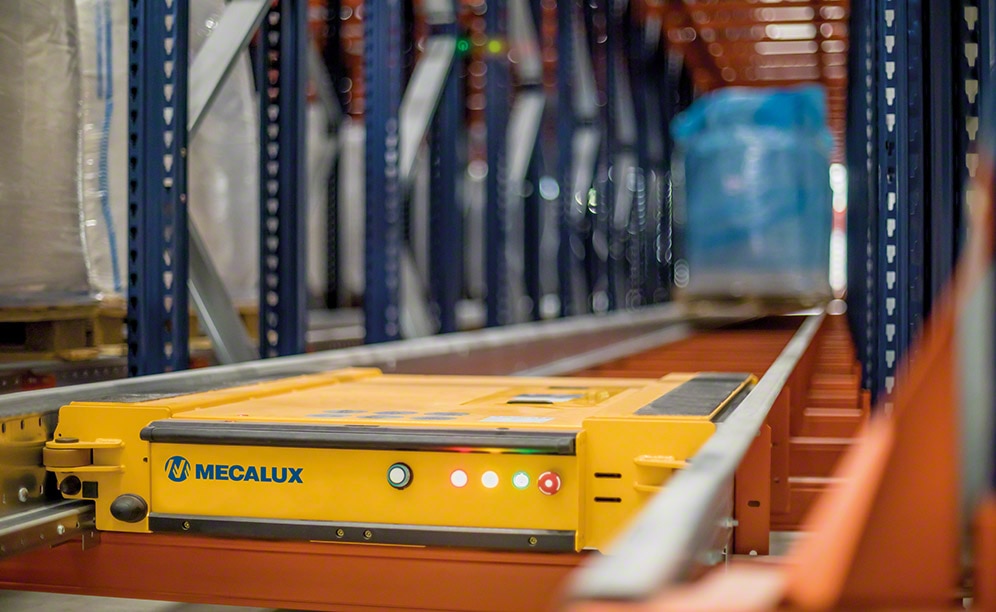
The semi-automatic Pallet Shuttle services a 2,295-pallet capacity
Ask an expert