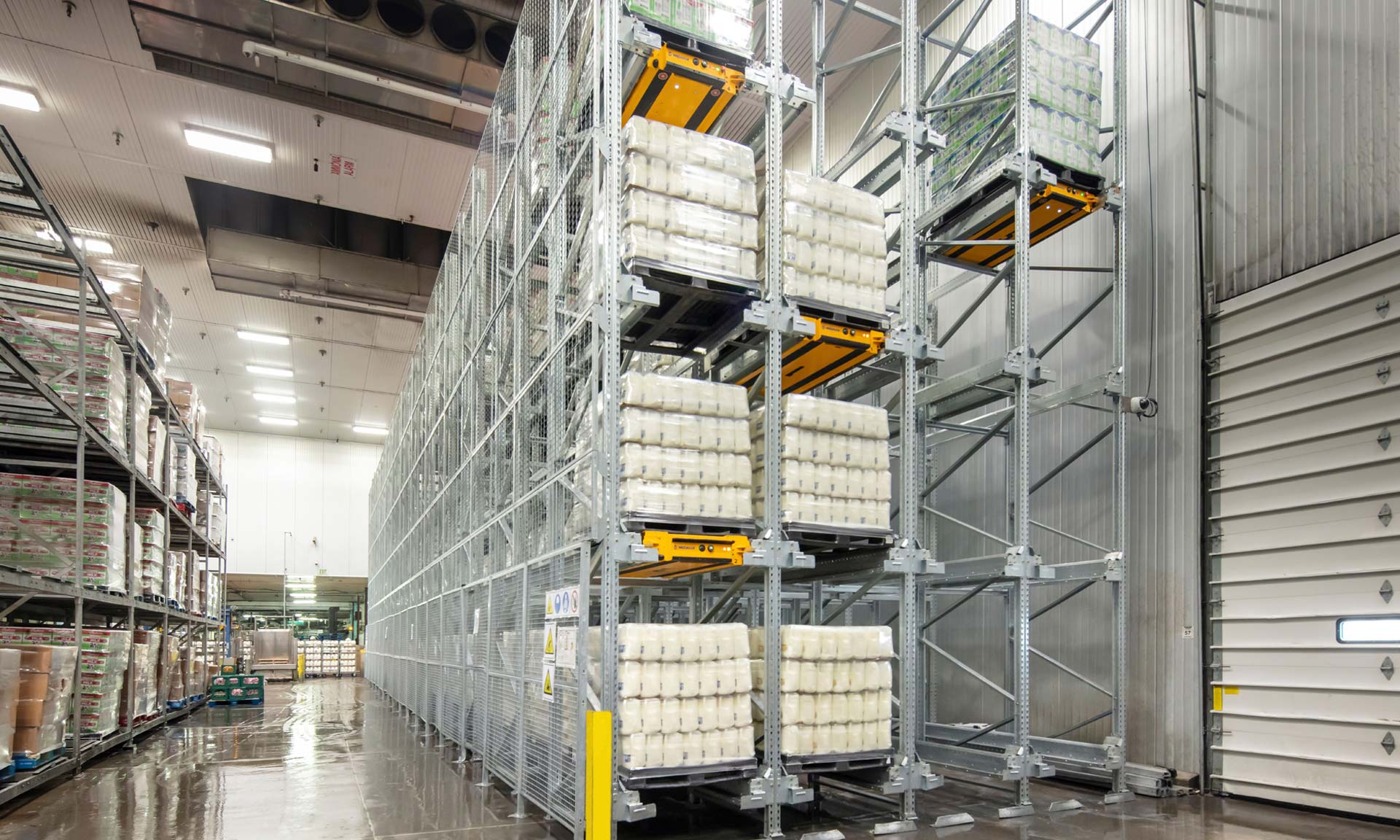
The Pallet Shuttle doubles capacity
Producers Dairy has doubled its storage capacity with the Pallet Shuttle from Interlake Mecalux
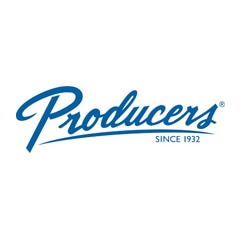
Dairy products supplier and distributor Producers Dairy recently installed a semi-automated Pallet Shuttle for its 4,645 m² cooler at its plant in Fresno, California. The Pallet Shuttle replaced the company’s outdated and inoperable pallet racking system. By installing the Pallet Shuttle system, the firm was able to double its capacity and prepare 300 orders per day.
Nourishing lives one at a time
During the 1930s, the Great Depression caused people to travel to California for jobs and opportunities. Four ambitious businessmen saw an opportunity and founded Producers Dairy Inc. on 22 December 1932. In the spring of 1949, Larry Shehadey purchased a majority interest in the company that continues to operate as a family-owned business to this day.
Today, the company has two plants in California, one in Nevada and one in Oregon, the largest of which is a 12,542 m² facility in Fresno, California, that bottles all sorts of dairy products including milk, creams and ice cream mix, half-and-half, and drinks such as orange juice and apple juice.
Recapturing pallet storage
Faced with an ageing four-level pneumatic pallet racking system, the company knew it had to find a new system for its 4,645 m² cooler at its Fresno facility. “It had been failing for some time, and we were looking for a solution to replace the existing racking system,” said Mike Ramirez, Producers Dairy Plant Manager.
The situation was so bad that the installation was losing pallet capacity because of it. “We finally got to a point where we basically decommissioned the top two levels of our previous racking system because it was not working any longer. So we were down to about 180 pallet positions,” Ramirez explained.
That’s when Interlake Mecalux and partner PacVS stepped in. “They came and proposed the Interlake Mecalux Pallet Shuttle system, and we agreed that it would work for our operations,” Ramirez says.
The high-density, semi-automated system uses a shuttle powered by an electric motor that runs along rails inside a storage channel. This solution considerably lowers operating times and allows operators to group the facility’s 150 active SKUs by channels rather than by entire lanes. This allows for greater diversification because each channel houses a different item.
The Pallet Shuttle also solved Producers Dairy’s capacity issues by enabling the plant to house 370 pallets in its cooler, more than double the 180 pallets it was previously storing. The system is 7.6 m high with four levels and operates with five shuttles that transport 1,016 x 1,219 mm black plastic iGPS pallets.
The shuttles follow orders sent by an operator through a Wi-Fi-connected tablet specially designed to operate in low temperatures, like that of the Producers Dairy cooler, which is 4.4 ⁰C inside. The Pallet Shuttle system is perfect for cold storage systems; it is highly suited to warehouses where products need low temperatures since it takes advantage of storage volumes and reduces handling times.
Not having forklift traffic inside the lanes also increases storage capacity in terms of depth and decreases the risk of accidents. The forklift operator simply places the motorised shuttle in the channel where the pallet is going to be stored. Then, the operator places the pallet in the entrance to the level, resting on the rails. Only the forklift’s forks enter the rack structure. The shuttle lifts the pallet slightly and moves it horizontally until it reaches the deepest available location, where it deposits the pallet. After that, the shuttle returns to the channel entrance to repeat the movement with the next pallet.
The operator repeats the sequence as many times as necessary until the corresponding channel is full. Before the operator fills the last position, he/she removes the shuttle and repeats the sequence in the next channel where work is necessary.
The Pallet Shuttle system is an ideal solution for companies with a high volume of pallets per SKU, a high turnover of goods and large-scale entries and exits of the same product. Producers Dairy uses the Pallet Shuttle system in its cooler for storing inventory for only a short period of time.
“We’re a bottling facility, so we actually have product that’s processed, filled into 3.79-litre containers and palletised,” Ramirez says. “These pallets go into the Pallet Shuttle racking system for typically 24 hours. We have what we have in inventory for about 24 hours, and that goes right into a lorry and is delivered to the customer.”
The company can load 50 to 70 trailers per day with about three or four orders on each for a total of about 300 orders per day.
Additional problems solved
In addition to fixing Producers Dairy’s cooler capacity issues, the Pallet Shuttle system also offered more benefits. For one, it reduced the company’s utility costs by eliminating the air compressors used in the firm’s old pneumatic racking system.
The Pallet Shuttle system, on the other hand, uses easy-access lithium batteries that have fast connections.
The Pallet Shuttle system also allows the facility to build up inventory and preload trailers ahead of time in the event that the plant has to take a line down for maintenance or other reasons.
“If we have unforeseen problems that shut the line down, we're able to build inventory in this racking system in an organised manner to be able to support a shutdown in production,” Ramirez says. “Before, we weren’t able to do that, and that’s probably the biggest positive step forward.”
Plans for expansion
In fact, the project was so successful that Producers Dairy plans to add on to its new system in the future. “We have very limited space, so we really had to design it based on the existing footprint of the old racking system,” Ramirez notes. “We have plans to expand the cooler, and we’re going to tear down the wall that’s adjacent to the racking system to then build onto and extend the system and add more shuttles and racking capacity.”
If we have unforeseen problems that shut the line down, this racking system enables us to build inventory in an organised way so that we can support a shutdown in production. Before, we weren't able to do that, and that's probably the biggest positive step forward.
Advantages for Producers Dairy
- Doubling capacity: by replacing its former racking system with the semi-automated Pallet Shuttle, Producers Dairy was able to go from storing 180 pallets to 360 pallets.
- Energy savings: after doing away with its pneumatic racks, which used air compressors, the firm saved significantly on utility costs.
- Greater flexibility: Producers Dairy can now build up inventory and load trailers in advance, which allows the plant to take down a line for maintenance.
Gallery
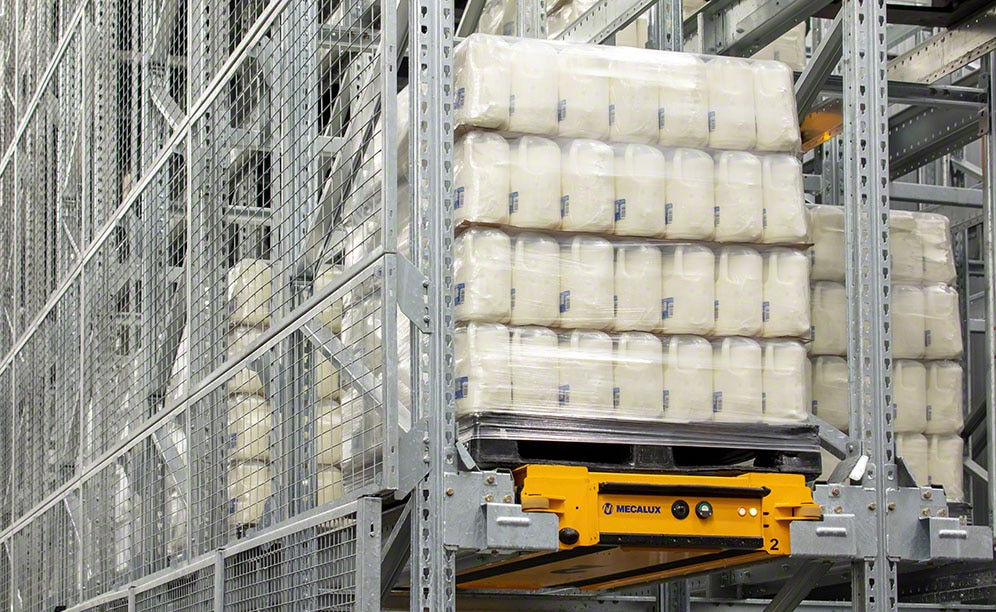
Producers Dairy has revamped its warehouse with the Pallet Shuttle system
Ask an expert