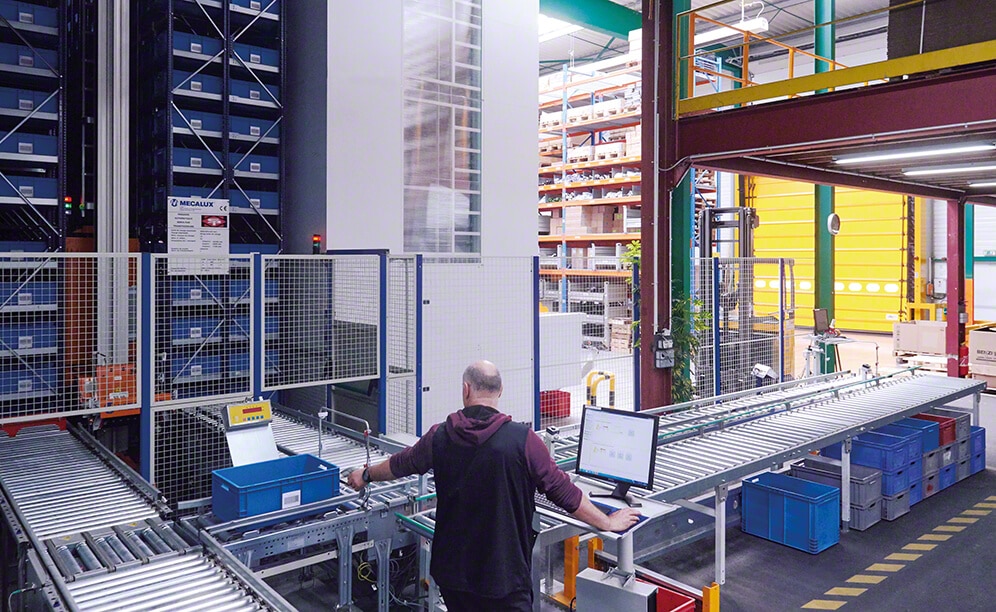
Symta-Pièces automated warehouse for boxes for agricultural machine spare parts
New automated warehouse for boxes holds up to 3,000 boxes for Symta-Pièces in France
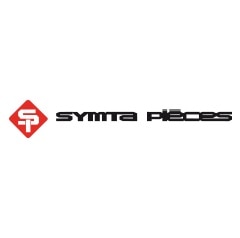
An automated warehouse for boxes is much more than a solution to hold small products. For French agro-machinery and tractor spare parts distributor Symta-Pièces, it has also marked a breakthrough in its supply chain. The company has benefited from automated product entries and exits, which has helped speed up the preparation and dispatch of the orders. The Mecalux Easy WMS, the warehouse management system in charge of managing all the operations, has been deployed to enhance productivity.
Tractors and harvesters
It all began at the start of the 20th century in Saint-Florent-des-Bois (France). This family business sells spare parts for tractors, harvesters and all kinds of agricultural machinery.
Currently, it works with the most prestigious brands on the market and has an extensive catalogue with over 57,000 SKUs. The company know that its logistics is essential to meet customer needs and must be foolproof.
New miniload warehouse
Symta-Pièces is constantly modernising its business to strengthen its growth rate. Along this line, it has recently renovated its distribution centre in the French city of La Roche-sur-Yon.
When it came to reworking the installation, the company wanted a solution that would help it manage smaller sized SKUs. Dominique Praud, manager of the Symta-Pièces warehouse, explains: “Before, we stored small products right on pallets which, apart from being really impractical for operators, took up a lot of space.”
On that account, Mecalux laid out a plan to install a miniload warehouse. A storage system designed specifically with small products in mind, it facilitates the automatic management of goods and order preparation. In this way, Symta-Pièces’s two main requirements would be met: “for our new warehouse, we wanted to optimise storage space and speed up operations,” says Praud.
Picking is this distribution centre’s main operation. Every day, around 1,000 orders are prepared with spare parts requested by the company’s customers. The automated warehouse for boxes actually acts as a buffer, supplying the picking area with smaller products at the right time.
Dominique Praud - Warehouse Manager at Symta-Pièces
“Our company revenues are on the rise, which is why we needed to increase our distribution centre’s productivity. Mecalux was on hand when we started this project and, given its competitive pricing, the solution it proposed has met our needs.”
Three-in-one
The miniload is an automated storage system comprising three elements: racks, automatic handling equipment (stacker cranes and conveyors) and a warehouse management software (WMS).
The Symta-Pièces warehouse consists of a single 32 m long aisle with double-deep racks on both sides (i.e. boxes are placed one behind the other). The racks are 7 m high, feature 15 storage levels and offer a combined 3,000 box capacity (50 kg per box).
The structure has been adapted to work with two box models of different heights: 240- and 420-mm. Smaller boxes are set on the lower rack levels, while largest ones are deposited on the top ones.
A miniload stacker crane runs through each aisle that inserts and extracts the goods from their locations automatically. The stacker crane’s cradle consists of a blade and two independently moving belts that collect the boxes from either side of the aisle.
The stacker crane only works inside the aisle and deposits the boxes on the conveyors running along the front of the racks, fulfilling the “product-to-person” principle. According to Praud, “thanks to the automated inflow and outflows of goods, we have increased how fast we supply the picking area.”
Merchandise is organised in the warehouse based on its rotation. For this reason, the highest demand products are placed at the aisle ends to optimise stacker crane movements. Additionally, the goods are managed with the FIFO principle (first in, first out). In other words, the first pallet in will be the first to leave.
The warehouse is equipped with efficient management software to avoid any sort of product errors. “We need the WMS system to know where each box is stored at any given time,” says Praud. Mecalux has implemented the Easy WMS, a warehouse management system that organises in-house operations and carries out very precise product control. Easy WMS offers total traceability: the system identifies the boxes once they arrive at the warehouse and, in this way, is able to track the stocks’ status in real time.
Product oversight
Mecalux’s Easy WMS has optimised all the miniload system’s processes. Since each box is monitored, any potential errors arising from manual management have been entirely eliminated and inventory can be updated whenever necessary.
“Easy WMS manages the locations and the inputs and outputs of the miniload system,” states the manager. Stock control is a must to achieve better warehouse performance. The system organises the boxes to optimise the stacker crane’s movements and, above all, to supply the distribution centre’s picking area as quickly as possible.
The WMS communicates with Symta-Pièces’ Navision ERP to coordinate the distribution centre’s needs with the operations of the automated warehouse for boxes. “Easy WMS seamlessly interacts with our ERP, providing it with stock status information,” points out Praud.
More efficient management
The automated warehouse for boxes has been completely integrated into the Symta-Pièces distribution centre. Not only does it make use of the entire available surface area to hold 3,000 boxes, it also acts as a depot for small products and supplies the order preparation zone with these types of goods.
The miniload is a “product-to-person” system. Thus, the operators will not have to move around the warehouse. Instead, the stacker crane and conveyors will bring them the boxes they need. Since this solution is fully automated, it has helped to improve the performance of Symta-Pièces’ supply chain.
Advantages for Symta-Pièces
- Space savings: the automated warehouse for boxes consists of a single 32-metre long aisle with 7-metre high racks housing 3,000 boxes of 50 kg.
- Increased productivity: the inputs and outputs automation guarantee that the distribution centre’s picking zone can be supplied promptly.
- Ongoing inventory updates: Mecalux’s Easy WMS warehouse management system carries out very strict real-time stock monitoring.
Automated warehouse of Symta-Pièces | |
---|---|
Storage capacity: | 3,000 boxes |
Box dimensions: | 356 x 556 x 240 / 420 mm |
Max. weight of boxes: | 50 kg |
Racking height: | 7 m |
Racking length: | 32 m |
Gallery
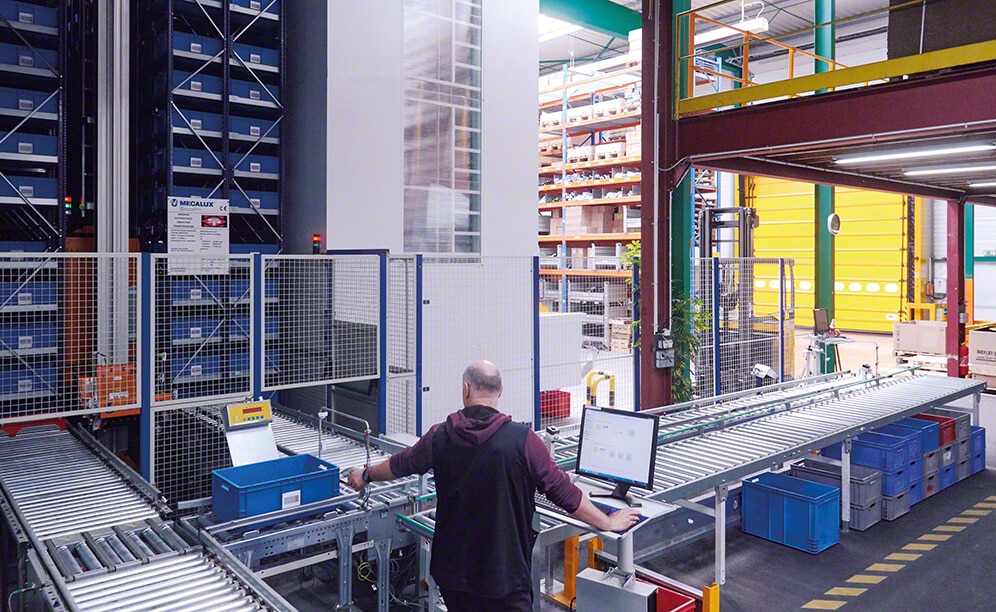
Symta-Pièces’s automated warehouse for boxes in France
Ask an expert