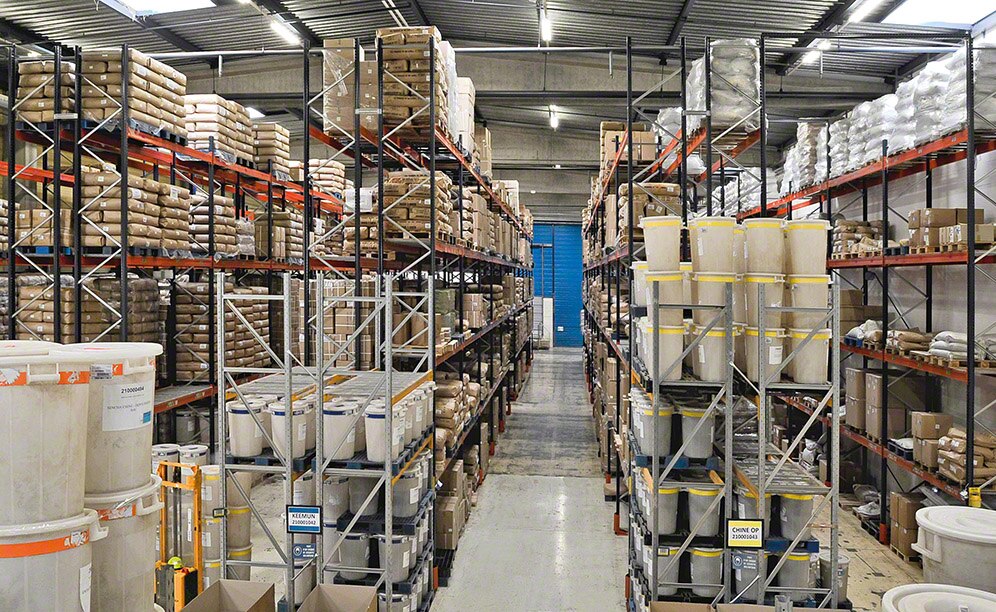
Pallet racks and conveyors for the tea of Dammann Frères
The new warehouse is connected to the production centre through an automatic conveyor
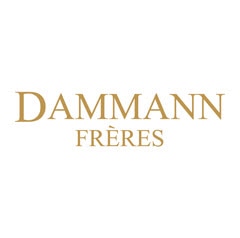
The French tea brand Dammann Frères has a new warehouse installation equipped with pallet racks and an automatic conveyor circuit that stretches to the manufacturing centre. This conveyor system is highly-effective, ensuring a constant flow of goods and minimising any interference with other operations.
About Dammann Frères
Founded in 1925 by two brothers, Pierre and Robert Dammann, this company has turned into the biggest brand of tea in France. The company has deployed technology in all its productive processes to develop and expand its repertoire of flavoured teas. After being in business for three generations, Dammann Frères has managed to increase exports and is present in more than 60 countries.
Needs and the solution
Dammann Frères owns a 9,000 m2 warehouse in the town of Orgeval (close to Paris), but did not have enough storage capacity to face growing sales from recent years.
Determined to resolve this situation and reinforce its growth rate, the company moved to a new 30,000 m2 production centre located in Dreux. The warehouse is composed of three different areas: packaging and cardboard boxes, finished products and raw materials.
The different warehousing zones are equipped with pallet racks, given their adaptability to any load type, weight or volume variable.
Additionally, the warehouse is linked to the manufacturing centre through a conveyor circuit by Mecalux.
Automatic pallet conveyors
The conveyor circuit’s job is to send the goods needed during each workday from the warehouse to the production centre automatically. It includes pallet recirculation to redistribute these bases in case of any type of incident.
This is a reversible system, i.e., unnecessary merchandise can be returned to the warehouse. A protocol has been established to prevent interference, depending on what is being moved and only with preauthorisation after four in the afternoon.
At the beginning of the circuit, workers operate forklifts to insert pallets on a hydraulic table, which lifts the load to the level of the conveyor. Once the pallet arrives at its destination, another hydraulic table lowers the pallet to the ground level where operators extract it from the circuit.
The conveyors are steered by the Galileo control software of Mecalux, which makes sure the system runs properly and carries out movements when goods are shifted to the production centre.
Pallet racking
The three zones of the warehouse are fitted out with this type of racking. Adept at storing a huge quantity of pallet with many different SKUs, the racks are arranged differently in each one of the sectors to adapt to the massive variety of available products.
This storage system has the benefit of supplying direct access to all in-warehouse pallets, which streamlines storage and order prep tasks. On lower levels, picking is carried out directly off the pallets and reserve products are deposited on upper levels, making the required items available at all times.
Operators crisscross the warehouse locating the SKUs for each order, as instructed by the warehouse management software (WMS) via a radiofrequency device.
Electric forklifts are run by operators in the finished products warehouse down narrow aisleways to handle the pallets. These machines require mechanical guide rails along both sides of the aisle to run safely along it, and also to avoid potential damage to the racking structures.
Advantages for Dammann Frères
- Optimal logistics management: goods are sorted and stored in the corresponding area of the logistics centre, taking into account their size, rotation and features.
- Dynamic transportation of the goods: the conveyor moves the goods at high speeds from the warehouse to the production centre, averting interference between the other operations in motion.
- High productivity: direct access to the merchandise guarantees a speedier management of the goods.
Warehouse of Dammann Frères: Conveyor | |
---|---|
Transport speed: | 20 m/min |
Length: | 48.3 m |
Gallery
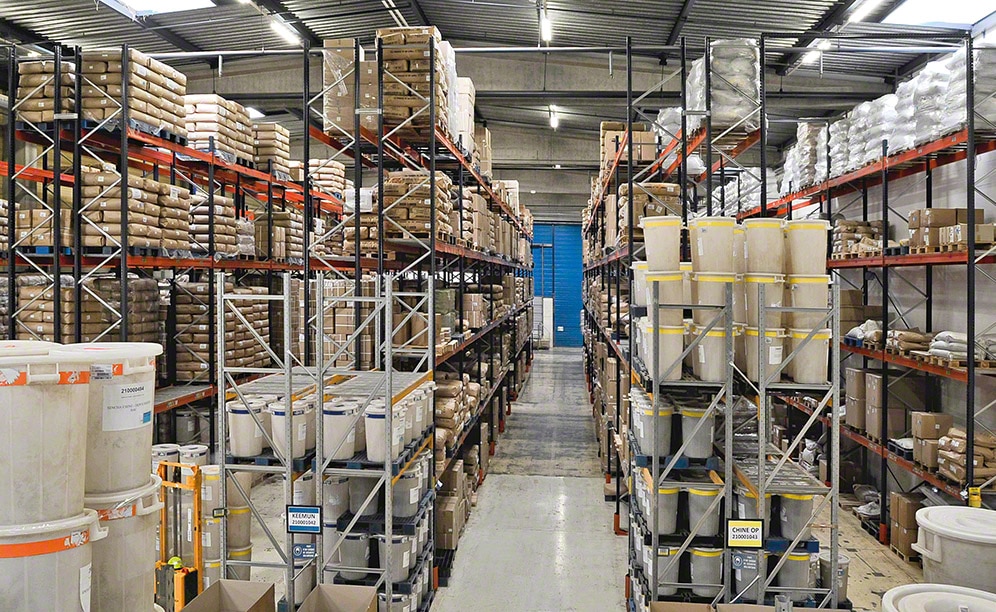
The warehouse that houses the tea of Dammann Frères
Ask an expert