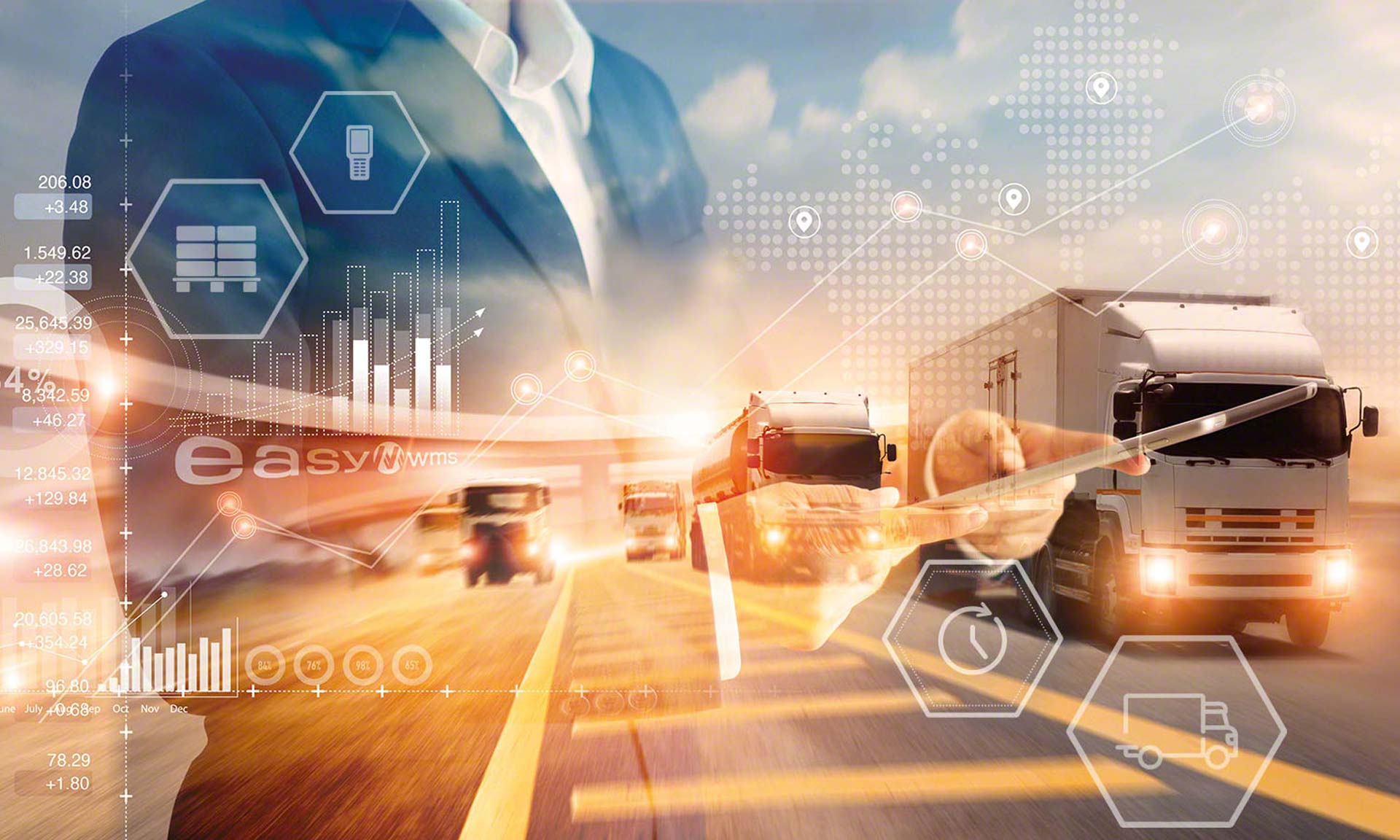
Express service with latest-generation software
Easy WMS in its cloud mode helps this express transport company to optimise its logistics processes
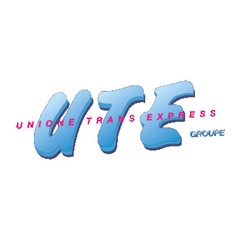
French express transport company UTE has optimised flows in its facility in Le Mesnil-Amelot (France) with Easy WMS, the warehouse management system by Mecalux. With this solution, the business has set itself several objectives: to modernise its image, carry out accurate and real-time control of its customers’ stock, and streamline goods entries and exits. Easy WMS, in its cloud mode, helps this logistics provider to offer its customers high-level service, with on-time, error-free deliveries.
Flexibility and agility
UTE celebrated its 30th anniversary by overhauling its business and its supply chain yet again. Since it opened its doors in 1991, this French road transport firm has continuously transformed its operations and services with a single goal: “to attract new customers,” emphasises UTE Technical Director Stéphane De Oliveira.
Its capacity to adapt to the needs of its customers is ingrained in the company’s DNA. UTE transports all kinds of products, from equipment used in European concert tours for a multitude of music groups through to hazardous materials. In recent years, however, it has specialised in express transport. “To do so, we’ve expanded our vehicle fleet with over 100 lorries and vans that have enabled us to deliver goods anywhere in Europe, thanks to our agile, flexible and error-free logistics systems,” says Stéphane De Oliveira.
In this vein, UTE recently improved the organisation of its facility in Le Mesnil-implementing Mecalux’s Easy WMS warehouse management system. “We turned to Mecalux because of its long track record of offering logistics solutions for all types of companies, including those of us who are transport specialists and logistics providers; we knew they’d satisfy our needs,” explains UTE’s Technical Director.
Moving to digital logistics
The warehouse operations of 3PL providers are remarkably complex. They manage many SKUs belonging to different customers (processing each one of them in a specific way), and they also prepare multiple orders in the shortest possible time.
In the case of UTE, its 4,000 m2 facility accommodates around 450 SKUs stored on pallets and in boxes and containers. Most items belong to an air-conditioning systems company and to a refrigeration machine manufacturer for the hospitality sector.
In the past, UTE controlled all its stock (and even took inventory) by means of Microsoft Excel. The operators manually noted which products arrived at the warehouse and which were dispatched. Nevertheless, as the number of products and of orders rose, this way of working became increasingly less practical.
Stéphane De Oliveira explains, “The risk of the operators making mistakes was too high, and we couldn’t have that if we wanted to keep increase our customer portfolio.” At that point, the company made the decision to implement a warehouse management system.
The reason is that a WMS would allow the company to have information in real time on the stock in its facility and to control the traceability of its products during the various processes.
After consulting with Mecalux, UTE knew that Easy WMS was the software it needed to modernise its logistics systems. “We realised that, with Easy WMS, we’d be able to organise the goods strategically, placing items with a higher demand in a more accessible way to facilitate their entry and exit. This would have a direct effect on all operations, as it minimises travel when employees go to locate the items they require,” affirms the Technical Director.
Easy WMS in the cloud
UTE has implemented Easy WMS in its SaaS (software as a service) mode, that is, in the cloud. This solution has simplified the installation of the warehouse management system and made it much more accessible for the company. Data storage has been moved to external servers, doing away with the need for the firm to purchase and maintain its own servers.
These are some of the advantages of Easy WMS in SaaS mode:
- Lower initial investment: not relying on company servers substantially reduces the initial outlay.
- Flexibility: it is possible to have a variable number of licenses, which is very useful with highly seasonal operations. Furthermore, businesses with multiple warehouses can sync their stock across the various facilities and control all processes.
- Maintenance and security: no IT staff is required for maintenance. The data is securely stored on the external servers.
- Automatic upgrades: with the software in the cloud, the company always has the latest version of Easy WMS.
- Accessibility: the business can access Easy WMS from any computer or device with an internet connection to verify the status of the different warehouse operations.
WMS: the brain of the warehouse
“Easy WMS manages all operations taking place in our facility: goods receipt, storage, picking and dispatch,” indicates Stéphane De Oliveira. The WMS monitors the products from the moment they arrive at the warehouse until they are distributed to customers.
To do this, it sends precise instructions to the operators on what to do with each product via their radiofrequency scanners. With the supervision of the WMS, they perform all tasks much faster “and, most importantly: we’ve eliminated any possibility of error,” enthuses the firm’s Technical Director.
Every day, the facility receives a wide variety of products, which operators identify by scanning the label with their radiofrequency devices. This way, Easy WMS verifies that the products received match the items communicated by the customer (in quantity, model and characteristics).
Goods receipt is a crucial operation in UTE’s warehouse, as it triggers the product flow. “We’re well aware of the fact that, without the help of the WMS, we’d run the risk of making many mistakes that would affect our inventory and limit our productivity,” points out Stéphane De Oliveira. Easy WMS registers all the information and keeps a record of all products that arrive to control their traceability.
Once the goods are identified, the WMS automatically assigns them a location in the warehouse, taking into account the particular attributes of each product, for example, its customer, SKU and turnover.
To prepare orders, Easy WMS guides the operators, telling them which slot to go to, which products to pick and in what quantity. “The software is so intuitive and the messages so detailed that our employees have learned really quickly how to work with Easy WMS,” says Stéphane De Oliveira. The WMS generates a route that ensures that operators travel the shortest distance possible and are more
efficient.
Lastly, Easy WMS organises all orders prepared in the dispatch area (right in front of the loading docks) based on their transport route. For example, parcels to be delivered first are the last to be placed on the lorry.
Ever-expanding logistics
“Easy WMS is hands down an effective tool for us. It provides us with real-time stock control and optimises all warehouse operations,” asserts the Technical Director.
For a logistics provider such as UTE, carrying out strict monitoring of all its customers’ SKUs is essential, as is streamlining goods inflows and outflows in order to distribute the products as soon as possible. With Easy WMS, the company’s supply chain runs much more smoothly.
Moreover, Easy WMS is a flexible and scalable software program capable of adapting to business changes. “In the next few years, we hope to increase our storage capacity with a new facility,” declares Stéphane De Oliveira. This system will accompany UTE in any of its projects and help it to provide its customers with the quality service for which it is known.
We’re extremely satisfied with Easy WMS from Mecalux because of the benefits it’s brought us: fewer errors, agility in all operations and stock information in real time. Likewise, with this WMS, we can project a more modern image to our customers.
Advantages for UTE
- Error elimination: UTE has gone from managing its stock manually with Excel to doing so digitally with a cloud-based WMS, thereby eliminating possible errors.
- More efficient operations: Easy WMS supervises the operators, giving them directions at each turn to make them faster and more efficient.
- Inventory control: the WMS monitors the 450 SKUs in stock from the moment they arrive at the facility until their dispatch.
Ask an expert