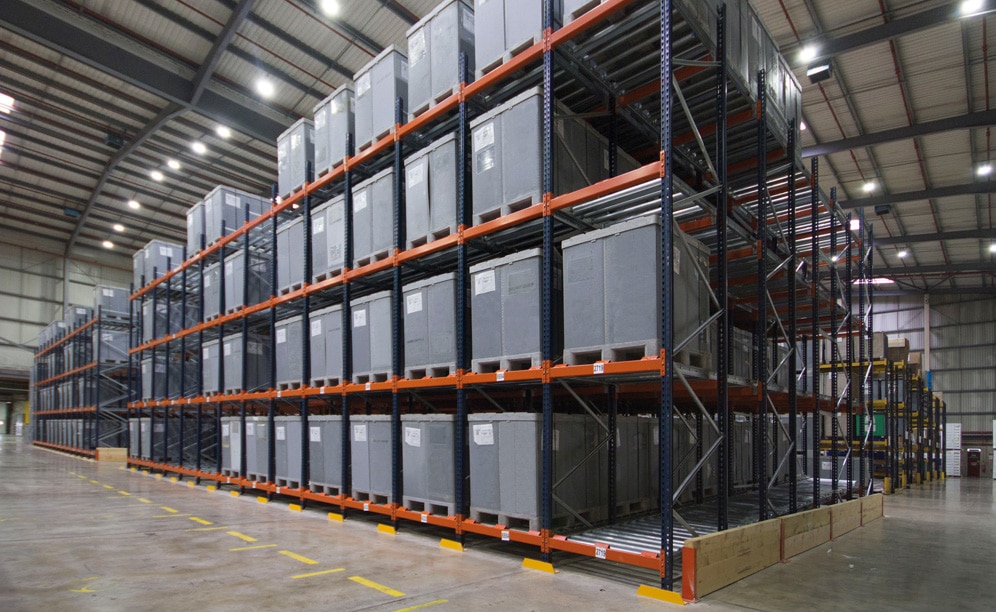
Vaillant reorganises its warehouse operations to meet growing product demand
Live pallet racking connects Vaillant’s storage and production areas
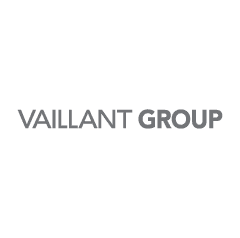
Mecalux has supplied Vaillant, one of the leading air conditioning companies in the sector, with live pallet racking for its warehouse in the United Kingdom. This system allows the quick supply of necessary components to the production centre. In this way, the company can maintain constant growth in Northern Europe and strengthen its leadership worldwide.
Needs of Vaillant
Vaillant is a company specialised in the manufacture of heating and ventilation equipment, such as furnaces, water heaters, radiant flooring and air conditioning systems. It was founded in 1874 in Remscheid (Germany) and currently has 13 production centres in six countries within Europe and in China. They have a far-reaching sales network that also extends into Africa and Asia.
The company decided to reorganise its manufacturing centre in the town of Belper (UK) to adapt to the constant growth of sales achieved in Northern Europe. Up to this point, the company used a very inefficient system in their warehouse, since all the goods from the Hungarian, Czech and Slovakian factories were deposited on the floor. To resolve this situation, Vaillant sought the advice of Mecalux.
The manufacturing warehouse
It is set aside for the storage of engines, water pumps and various furnace components used in the manufacturing centre, located in the same plant. Mecalux provided two blocks of live racking where they deposit the plastic containers with the goods.
The racks were distributed four tiers high. They comprise 112 live channels that receive eight pallets in depth, boosting capacity to more than 890 pallets.
Live racking
This is a compact storage system that maximises the available surface area and, in turn, facilitates the access to the load units.
The warehouse provisions the production centre of Vaillant with the goods that come from their other manufacturing plants. Therefore, live gravity flow pallet racking is the most suitable to expedite the loading and unloading of pallets. It ensures a continuous flow of products, with minimal handling on the part of the operators.
In addition, this system ensures the perfect turnover of goods when applying the FIFO method, i.e. the first pallet in is the first out. The pallets are placed into the loading aisle, glide by gravity to the opposite end and are ready for their removal. The interference between the two operations is thus eliminated.
Advantages for Vaillant
- Maximum performance: it leverages the surface available for more storage capacity and enlivens operations with the aim of supplying the production centre more swiftly.
- Perfect turnover: the live racks ensure optimum turnover of products. The loading and unloading of pallets are carried out in two different aisles to avoid errors.
Storage system with live racking in the United Kingdom | |
---|---|
Storage capacity:: | 896 pallets |
No. of pallets in depth:: | 8 |
Levels high:: | 4 |
No. of channels:: | 112 |
Max. frame height:: | 6 m |
Warehouse height:: | 39.3 m |
Gallery
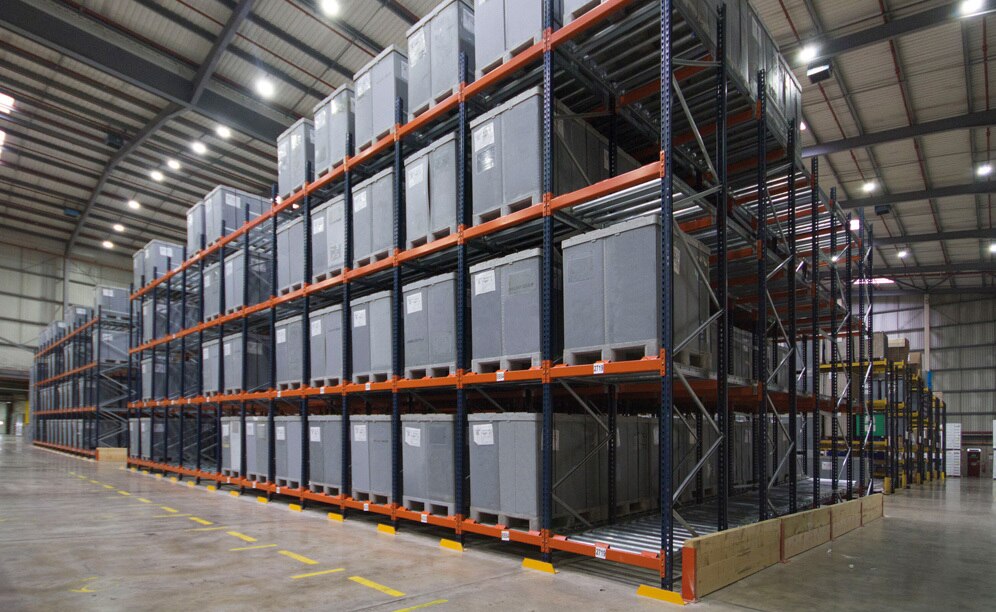
Ask an expert