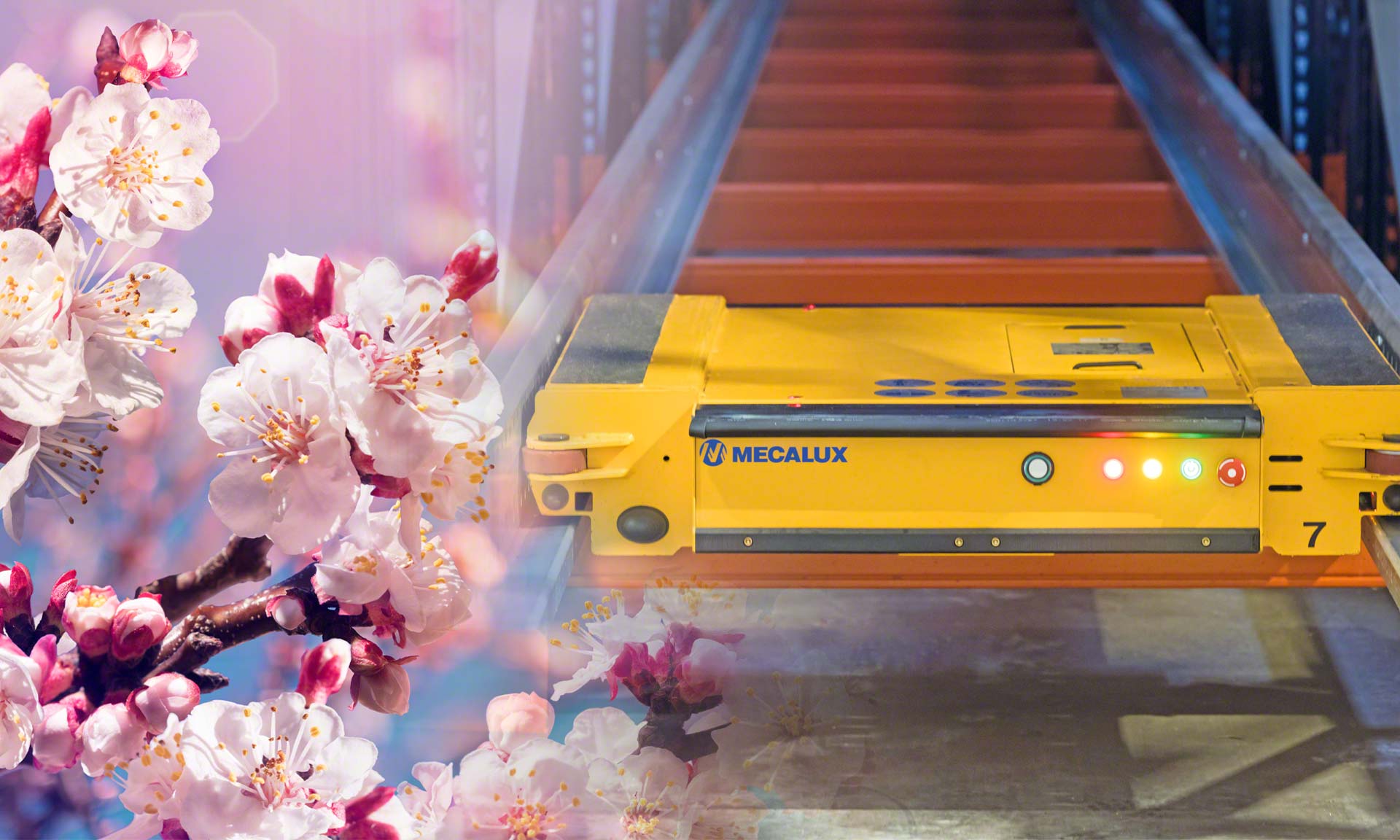
De Prado boosts production with the Pallet Shuttle system managed by Easy WMS
Agricultural company De Prado digitises logistics processes with a temp-controlled warehouse for almond production
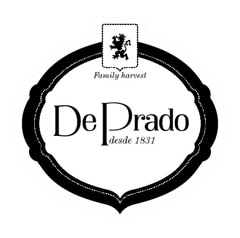
Agricultural company De Prado has launched a new business line dedicated to almond production and, to that end, has overhauled its logistics processes. The business has opened a warehouse in Portugal equipped with Mecalux's Pallet Shuttle system and Easy WMS warehouse management software.
De Prado: family agricultural company
In 1831, the De Prado family began growing olive trees and other crops such as cereal and grapevine. Today, De Prado is a producer of olive oil, olives for consumption and almonds. The company has a qualified, specialised team devoted to the production of 21,000 tonnes of olive oil and 25 million kilos of olives for consumption. In 2014, De Prado set out to diversify its products, planting more than 5,000 hectares of the main varieties of almond trees in Spain and Portugal. Today, it has 10,100 hectares of this crop. In a change of strategy, the company began selling its raw material in bulk to businesses in the food and fast-moving consumer goods industries.
- Founded in: 1831
- Production plants: Spain, Portugal, the US and Chile
- International presence: Spain, Italy, France and other countries
- Hectares of olive trees: 17,900
- Hectares of almond trees: 10,100
- No. of employees: 600+
CHALLENGES
|
SOLUTIONS
|
BENEFITS
|
---|
De Prado, one of Spain’s largest producers of olives for consumption and olive oil, has overhauled its infrastructure to boost its growth. In recent years, it has run one of its most ambitious projects to date, diversifying its portfolio with the launch of a new business line dedicated to almond production. “We’re very excited: over the next few years, we want to become a key player in the international market,” says Javier García, Industrial Manager at De Prado.
To start the new line of business, the company planted 5,000 hectares of almonds in Spain and Portugal. “Nut farming is already underway: in 2021, we produced 15 million kilos of almonds, and we’re planning to double that figure in 2022. We expect growth to be exponential for the next four or five years — even tripling our current production. Right now, we have over 10,000 hectares of almonds to be processed in our production centres, so we have to be prepared to adapt our logistics facilities,” says García.
When production was lower, De Prado would place big bags containing almonds in an area specially set up to accommodate them. “It was a temporary solution because we needed a warehouse that would enable us to properly store the almonds and accurately control temperature and humidity to prevent pests,” says García.
De Prado has opened a new, 1,040 m² , 14-metre-tall facility in Beja (Portugal) to house all its almonds. “They’re kept at a constant temperature of 10-15 °C, and we make sure the humidity never goes above 60-65%,” says García. To equip the warehouse, the company turned to solutions from Mecalux. “They had extremely good references and offered us the best technical and cost-effective proposal,” says García. Mecalux suggested installing the semi-automated Pallet Shuttle system, Easy WMS warehouse management software, and the WMS & Pallet Shuttle Integration module.
“In a facility as busy as ours, where we work 24/7 in three shifts, the Pallet Shuttle has enabled fast operations adjusted to the particular characteristics of the goods. And the warehouse management software allows us to monitor product traceability in real time,” says García.
Features of the semi-automated Pallet Shuttle
“We chose the Pallet Shuttle system because it’s ideal for managing many pallets of the same SKU,” says García. De Prado’s SKUs include finished and semi-finished products as well as almonds of different sizes and qualities.
The company has installed two racking units with storage capacity for 2,772 pallets. In each of the 180 available locations, De Prado can deposit up to 17 pallets of the same SKU in depth.
This storage solution consists of a motorised shuttle that moves inside the storage channels, inserting and removing the pallets from their locations with full autonomy.
“We’re thrilled with the Pallet Shuttle because, besides being really easy to use, it organises our stock to a T,” says García. The operators merely have to place the motor-driven shuttle and the pallets in the first position in the channel, and the shuttle moves the pallets to the first free location, where they are stored.
Almond traceability
De Prado’s production processes are automated and fully controlled by a MES (manufacturing execution system), a software program that organises, manages, and oversees operations. “Our production operations were supervised, and we wanted the same for our logistics processes. Our intention was to monitor the products more accurately,” says García.
In the past, the company tracked all its stock manually. The operators would make a note of the items that arrived at the warehouse on spreadsheets; later, they would enter that information in the company’s Primavera ERP system. “Now, the process is much faster and easier, and operators are less likely to make mistakes. They simply scan the barcode on each item, and Easy WMS assigns it a location automatically,” says García.
To digitise its facility, De Prado equipped it with RF scanners. Using this technology, the operators receive instructions from the Easy WMS warehouse management software from Mecalux, which tells them where to slot each product.
“Easy WMS records the information on each of the big bags, e.g., almond type, batch, quality characteristics and humidity level. Based on these data, the program decides on the ideal location for each item,” says García.
How does Easy WMS supervise the traceability of De Prado’s almonds so accurately? By assigning each item a slot, the software knows its exact location. Likewise, by sending operators instructions on where to take each item or which pallets to remove from the warehouse, Easy WMS records and tracks all movements.
Warehouse synced with production
“We crack the almonds, but, as a rule, they’re not ready for sale. Before selling them, they have to go through other processes such as calibration, which consists of sorting the almonds according to their size and by means of an optical sorting system,” says García.
As these processes are not consecutive, the goods are stored between one operation and the other. To seamlessly sync the warehouse with production, Easy WMS has been integrated with De Prado’s Primavera ERP system. Thus, the ERP system notifies Easy WMS of the items needed, and the WMS organises their retrieval from the racks and delivery to the production lines.
Finished products arrive at the warehouse in 1,000-kilo big bags that are stored and then distributed to customers. “These are mainly food companies that manufacture chocolate, nougat or ice cream and that generally process, fry or toast our almonds,” says García.
Software to control the Pallet Shuttle
De Prado has also implemented the WMS & Pallet Shuttle Integration module, a software program specifically designed to streamline the tasks of operators that work with this storage system from Mecalux.
Using a tablet connected to Easy WMS, operators control the movement of the motor-driven shuttle. With this tablet, they can enter the items that need to be stored or retrieved, count the number of pallets stored in each channel and direct the goods to be compacted.
“The operators have adapted really well to the Pallet Shuttle system. It comes with intuitive software that allows them to easily send instructions to the motorised shuttle,” says García.
Scalable, future-ready logistics
De Prado is currently diversifying its portfolio with its eye set on expanding its business. To that end, the company has purchased more hectares in Spain and Portugal to boost olive and almond production. “We’re going to triple production at our plant, which will mean a threefold increase in warehouse entries and exits.”
De Prado benefits from scalable logistics operations prepared to cope comfortably with a more frenetic pace of work. With the Pallet Shuttle system, it can house a large number of items to be stored in a specific area. The company can also ensure that the almonds are stored in proper conditions and control their temperature and humidity.
Moreover, the Easy WMS warehouse management system provides total traceability of the products and organises them taking into account their particular features. Digitisation is key for De Prado: it has enabled the business to optimise its supply chain operations and maintain strict control over the movements each item makes.
Digitised goods management has improved the safety and speed of De Prado’s storage tasks. The Mecalux software will support the agricultural company in its plans for future expansion.
In building this new business line for almond production, we’ve had to modernise our entire logistics infrastructure. The semi-automated Pallet Shuttle system has enabled us to better organise and handle the products, while Mecalux’s Easy WMS gives us much more accurate and safer stock control.
Ask an expert