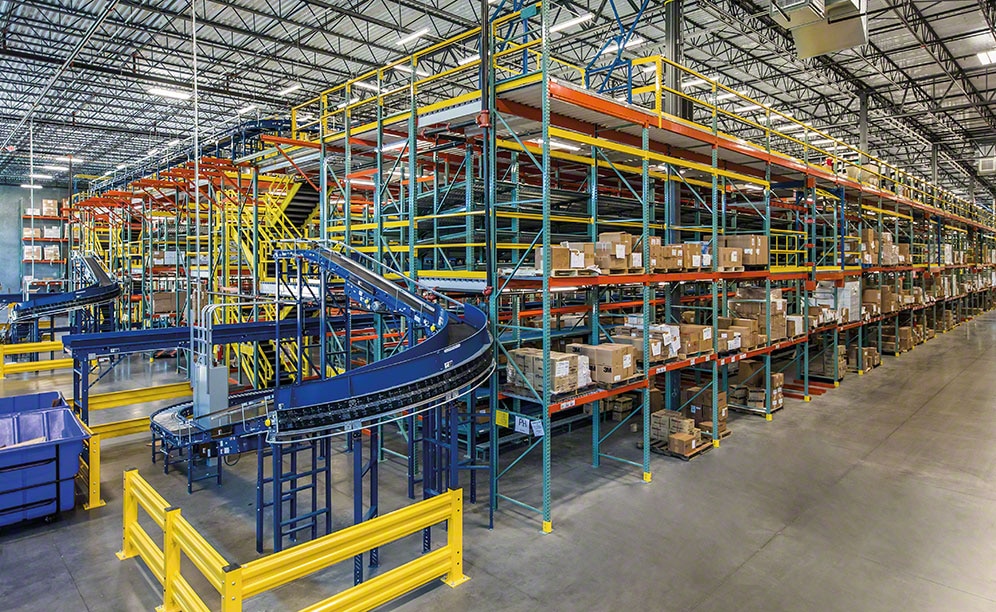
Benco Dental's picking warehouse for dental products
Picking solutions to store dentistry materials for the customers of Benco Dental
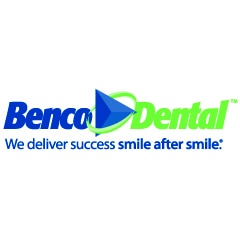
Since equipping six of Benco Dental’s distribution centres spread throughout the United States, Interlake Mecalux has modernised the warehouse this well-known dentistry material and instrument distributor has in Florida. The storage solution includes two picking blocks, live storage for picking and pallet racks.
Benco Dental: growing outwards
Benco Dental is the biggest distributor of dental material, equipment and technological innovations in the United States. With more than 85 years of experience, the company sells everything from toothbrushes to toothpaste, from dentist chairs to X-ray machines.
The business started out in the 1930s when Ben Cohen opened a small dental-care products office in Wilkes-Barre, a city located in the State of Pennsylvania Over time, the company kept growing and diversifying itself progressively. In 2002, Benco Dental inaugurated one of its main distribution centres in Jacksonville (Florida) and, since then, it has opened logistics centres in Fort Wayne, Indiana, Dallas, the State of Texas and Nevada. All the pick solutions in these logistics centres have been supplied and installed by Interlake Mecalux.
The company’s winning business strategy has allowed Benco Dental to experience strong growth over recent years, topping out 650 million euros in sales in 2018. With this sales volume it is logical that, despite renovating its Jacksonville distribution centre several times, the 6,500 m2 it occupied fell short when it came to managing the 22,000 SKUs the company presently works with efficiently.
The company recently acquired a new 12,000 m2 distribution centre to resolve the lack of space. Only 20 km from the old centre, the customer has once again chosen picking solutions from Interlake Mecalux.
Over-sized picking platform to optimise space
Once it analysed Benco Dental’s needs, Interlake Mecalux opted to use vertical warehouse space and optimise this space by enabling two picking blocks with three shelf levels. Both blocks, fitted out with live storage for picking, picking shelves and conveyors, are linked by a raised passageway located on both ends of the upper level.
“The picking solution from Interlake Mecalux has let us triple the useful storage area. By making use of the centre’s height, now we have much more space with regards to square metres,” said Doug Jones, operations manager of the Benco Dental distribution centre.
Additionally, an extra space was reserved in case, down the road, Benco Dental keeps up this sales pace and needs to expand its storage system. “As a company, we are always progressing and our yearly growth has been quite good,” assured Michael Mangan, project coordinator of Benco Dental.
Michael Mangan - Project Coordinator at Benco Dental
“We knew it was crucial to have an area set aside for future expansion. We arrived to the point that we didn’t want to be rethinking the centres’ storage capacity every couple of years. To really use the space in the most efficient way and give us room to grow.”
Getting orders ready
The 6.4 m tall, 61 m long by 38 m wide picking structure hosts different zones that are joined by means of a large conveyor circuit. Said circuit crosses each one of the floors centrally (with racks running down both sides) and moves the orders up to the consolidation and packaging zone.
Both floors have live storage for boxes comprised of lightly inclined roller shelves. Boxes that are set into the highest end slide through gravity down to the end that faces the pick aisle, making FIFO based (first-in, first-out) goods management possible. The upper level is rounded out with picking shelves for small-sized products.
Order prep starts on the second floor according to the pick zone method, based on the “person-to-product” criteria. The operators carry out picking on order picking table with rollers. After completing the order, the operator deposits the box on the main conveyor circuit to send it to the next picking station or, in the case of an already finished order, the sorting area.
In the words of Doug Jones, operations manager of the Benco Dental distribution centre, the installed solution must not only help optimise the space, but also improve the entire storage and picking process: “Certainly, the main need was to get more space. But, at the same time, we managed to increase the efficiency of the whole flow of goods in our warehouse.”
Pallet racking
Pallet racks were installed to store 2,880 pallets of reserve stock used during picking operations. Each block of racks is 8 m tall and comprises five shelf levels for storage.
This direct access system stands out for its adaptability and versatility when accommodating goods of different sizes.
Advantages of Benco Dental
- Space optimisation: the company has space-purposed the building’s height to triple the useful storage area with the installation of a three-story pick block.
- Increased productivity: the new order picking system helps this operation get done in the most efficient way.
- Product diversity: the installed solutions permit the storage of a wide variety of products of various sizes and weights.
Benco Dental's distribution center - Picking block | |
---|---|
No. of live box shelves: | 173 |
Height: | 6.4 m |
Length: | 61 m |
Width: | 38 m |
No. of levels: | 3 |
Total surface: | 2,340 m² |
Gallery
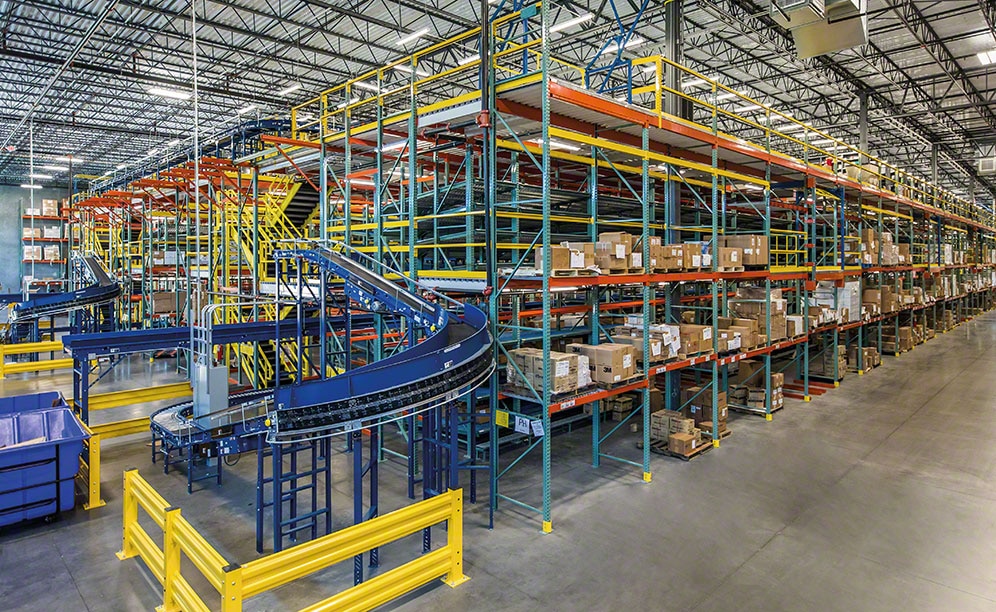
The dental products warehouse of Benco Dental
Ask an expert