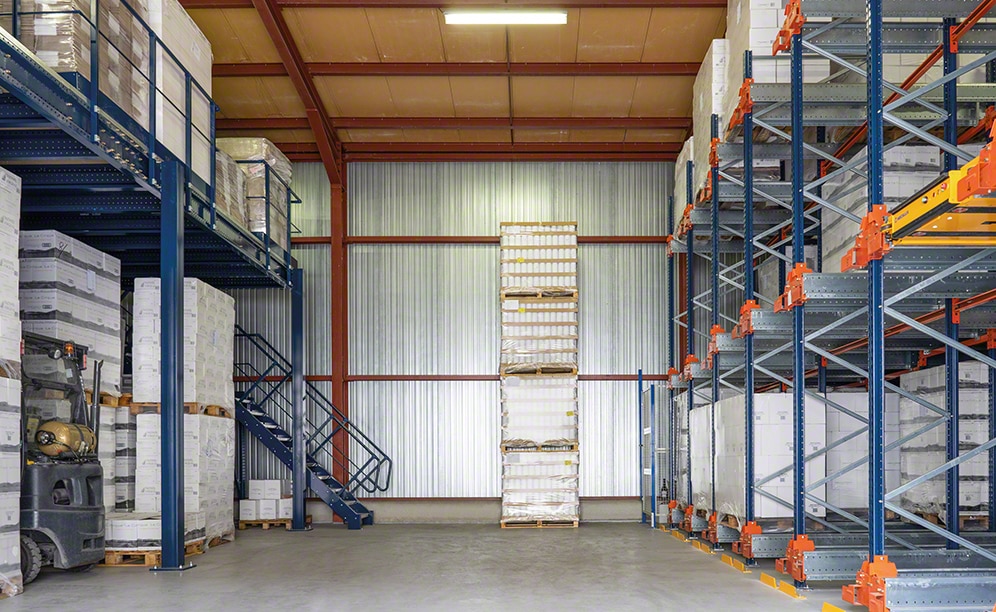
Mecalux equips the warehouse of French wine maker Vignerons de Tautavel
Pallet Shuttle system in a wine warehouse: storage capacity and streamlined inputs and outputs
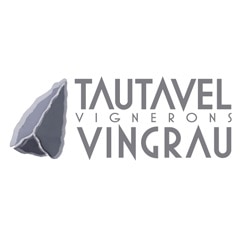
The Vignerons de Tautavel Vingrau warehouse, in the South of France, is neatly linked to the manufacturing centre. On one side, empty bottles are sent to be filled with wine and on the other, ready to be shipped finished product is received. Mecalux has set up the semi-automatic Pallet Shuttle system to house the company’s wines, keep them stored for the required duration and, finally, to distribute them in a timely fashion. A mezzanine was also explicitly constructed to house cardboard boxes and packaging.
A long tradition of winemaking
The company opened in 2010 with the merging of the Tautavel and Vingrau cooperative wineries, in Southern France. This union constitutes a fusing of wine-making knowledge with the most modern technologies to guarantee quality, flavourful wines.Coordinated storage and manufacturing
Vignerons de Tautavel Vingrau has a 375 m2 warehouse right next to the production centre. The two installations run in perfect synch, meaning the warehouse supplies empty bottles essential to the production process and, contrarily, finished products are received in the other (bottled wine grouped on pallets) ready to be distributed.
In the beginning, pallets were set on the floor and stacked one on top of the other, “but this system proved inadequate if we wanted to expand production and, as a result, our storage capacity,” mentions Tatiana Rey-Landriq, a sales team member at Vignerons de Tautavel Vingrau. Faced with this situation, the company needed to make better use of its available space and automate the entry and exit of the merchandise, where possible.
Warehouse operations are very simple. Around two or three times a month empty bottles are sent directly to the production centre so they can be filled with wine (without storing them). During those three days that month, 30 pallets with full bottles are moved to the warehouse and slotted in the racks for around 60 days to be later sent to customers. Shipments depend on the number of orders that have been received, although, broadly speaking, between 20 and 30 pallets are distributed each month, even though there can be occasional peaks in demand.“Our clientele are located, above all, in France, the United States and Asia,” adds Rey-Landriq.
Often, each order contains between 10 and 12 lines, and each one of these lines is prepared in the same production centre. Bottles are filled according to the orders that have been received. With this system, production is demand-based and, thus, avoids the storage of excess product.
Active space purposing
Vignerons de Tautavel Vingrau works with very few SKUs (27 to be exact) and many pallets per SKU. The most ideal solution, taking this into account, consists of a high-density storage system that offers optimal storage capacity.
The warehouse is equipped with a block of high-density racking. It stands 5 m high, with three shelves and a width of 13 m, including a capacity for up to 15 pallets in depth. This depth is not usual, but in this case, space was fully-purposed to accommodate as many pallets as possible.
As such, the products can remain stored during the required period waiting to be sent to customers. Each channel is assigned the same SKU.
Mecalux took it a step beyond by proposing the installation of a semi-automatic system like the Pallet Shuttle that streamlines the input and output of the goods.
The motorised shuttle runs inside the channels automatically for the purposes of inserting pallets into their corresponding locations and extracting them as required.
According to Tatiana Rey-Landriq, “This system guarantees very swift pallet management and top safety.”
A 4 m tall mezzanine was constructed right in front of the block of racks. This solution multiples available space by enabling a +75 m2 floor level. Cardboard boxes and packaging are deposited on the two levels to package the bottles of wine directly on the ground floor.
The Pallet Shuttle in action
The semi-automatic Pallet Shuttle system minimises operating times because operators do not enter the aisles to handle goods, it is the shuttle which carries out the movements automatically. “We have made things easier for our workers,” points our Rey-Landriq.
Operator involvement is needed to transport the pallets and to activate the electric shuttle, even though the Pallet Shuttle’s movements inside the racks are automatic.
Wi-Fi connected tablets are used by operators to send commands to the Pallet Shuttles. Through these devices, they can select how many pallets to extract, count inventory and organise users and authorised personnel.
Tatiana Rey-Landriq - Sales team member at Vignerons de Tautavel Vingrau
“Thanks to the Pallet Shuttle system, the entry and output of the goods are much quicker compared to other high-density solutions. Plus, we can efficiently view and control all our stock.”
Advantages for Vignerons de Tautavel Vingrau
- Space optimisation: both the compact Pallet Shuttle system and the mezzanine make maximum use of available space to provide greater storage capacity.
- Agile high-density system: the Pallet Shuttle facilitates the insertion and removal of pallets that stay stored around 60 days.
- Maximum productivity: the Pallet Shuttle system minimises handling by operators, which translates into higher warehousing productivity.
Wine warehouse Vignerons de Tautavel Vingrau | |
---|---|
Storage capacity: | 405 pallets |
Pallet size: | 800 x 1,200 mm |
Max. pallet weight: | 915 kg |
Racking height: | 5 m |
Channel depth: | 13 m |
Mezzanine height: | 4 m |
Gallery
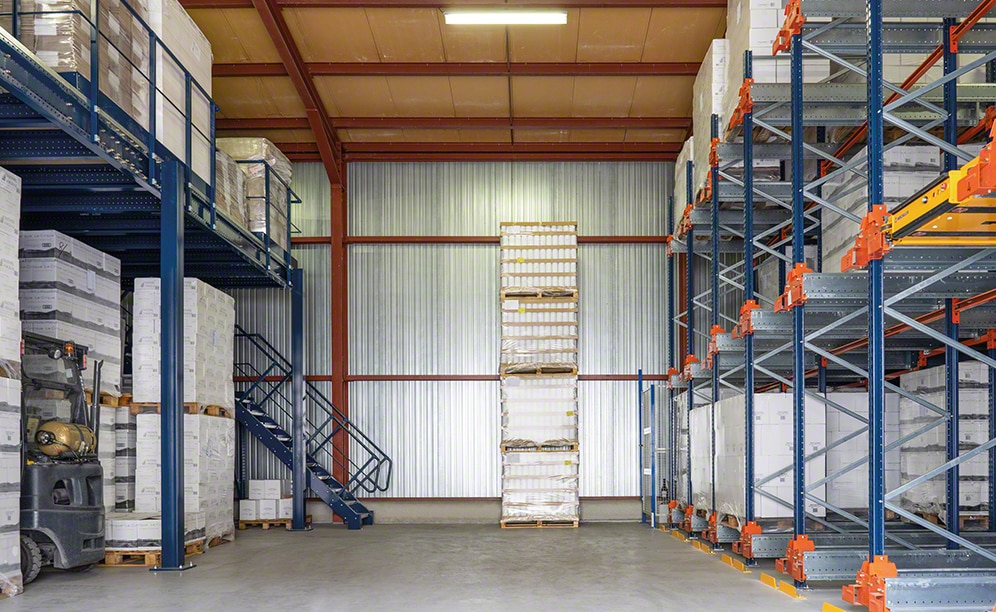
The wine warehouse of Vignerons de Tautavel Vingrau in France
Ask an expert