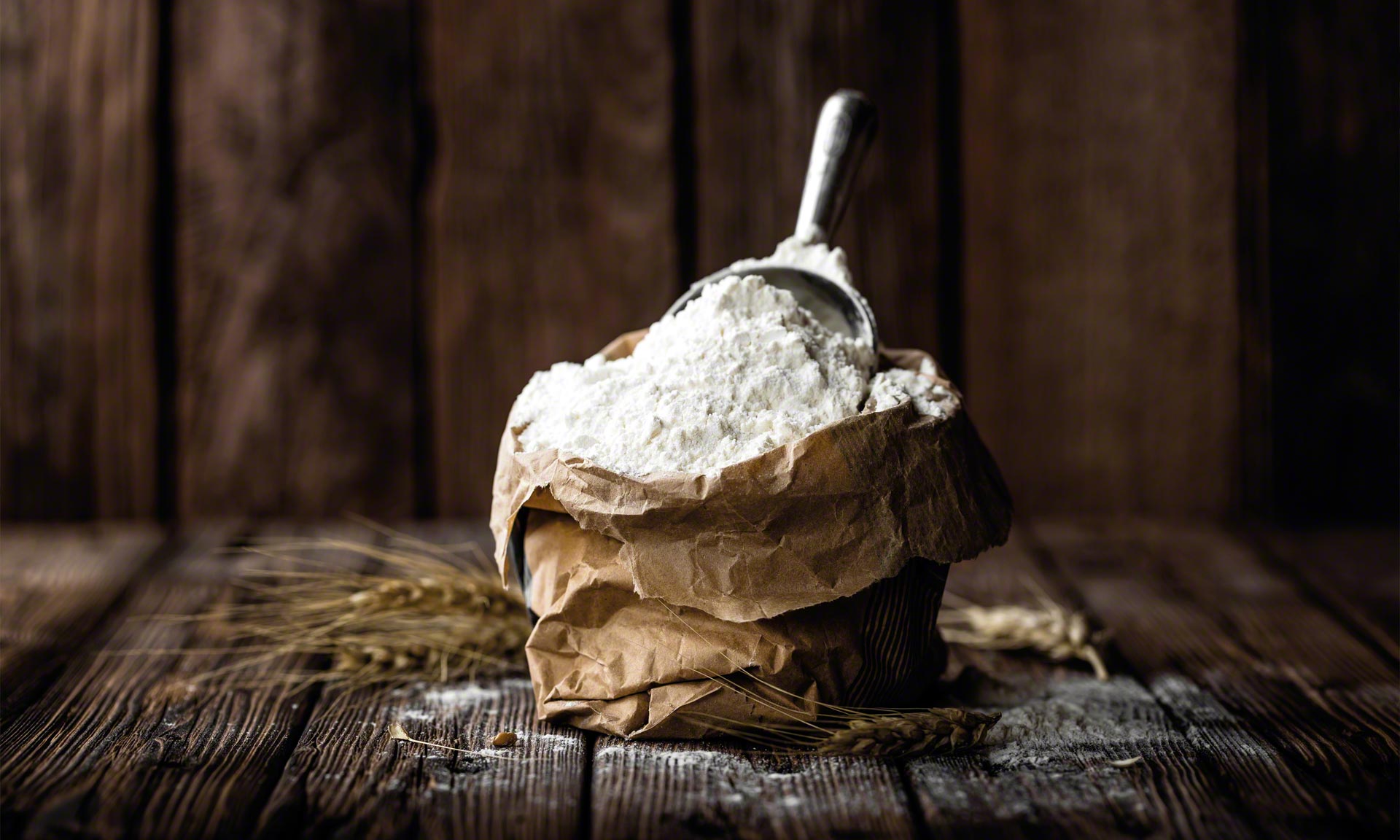
Haricaman modernises flour storage at its plant in Toledo, Spain
Haricaman implements Easy WMS and the semi-automated Pallet Shuttle system to manage the production of 60 million bags of flour a year.
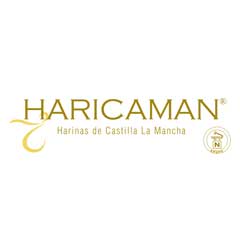
The flour and breakfast cereal producer Haricaman has modernised its logistics processes with Easy WMS software and the semi-automated Pallet Shuttle system. The comprehensive solution from Mecalux enables the company to store finished goods from its flour plant, where it manufactures 60 million bags a year.
Haricaman: natural, additive-free products
Haricaman is a family-run business that started out manufacturing and marketing flour for bakeries. Today, it boasts an extensive product range, specialising in a wide variety of cereals, semolina and breadcrumbs. Additionally, since 2017, it has produced and packaged gluten-free products using the most advanced technology. It follows strict food safety standards to keep its customers healthy.
CHALLENGES
|
SOLUTIONS
|
BENEFITS
|
---|
Haricaman, a renowned flour producer, has undergone a renewal process to address the increase in production in recent years and boost its growth. The company, which initially served local bakers, has become a leading manufacturer, supplying supermarket chains such as Carrefour, Auchan, Alimerka and El Corte Inglés. Nowadays, its central business activity and the chief driver of its growth is the production of a broad range of breakfast cereals.
Haricaman strives constantly to modernise its manufacturing and logistics processes, seeking to make its operations more efficient and expand its market share. The organisation recently opened two manufacturing plants in Spain equipped with a total of four production lines. In particular, its plant in Toledo (Spain) is a pioneer in processing gluten-free flours and other related products. It features three specialised lines, for extrusion and coextrusion, muesli and granola and cereal puffing. One year after its opening, the plant manufactures 60 million bags of flour, breadcrumbs and breakfast cereals, 20% of which are exported to countries such as Portugal, Cuba, France and the UAE.
To manage its finished products, Haricaman opened a new, 1,500 m² warehouse. This facility has enabled the company to cope with rising production levels and manage the goods it sends to large distributors. The business contacted Mecalux to outfit its new warehouse with the storage solution that would best meet its logistics requirements. “We needed a system that would facilitate the putaway and shipment of all pallets leaving production. At the same time, it had to control the traceability of our SKUs in real time,” says Nicolás Rodríguez, CEO of Haricaman.
After analysing the exact movements, the number of SKUs (around 350) and the type of finished products stored, Mecalux installed a comprehensive solution comprising the semi-automated Pallet Shuttle and the Easy WMS warehouse management system.
Haricaman chose the Pallet Shuttle because it is an ideal high-density storage solution for housing a large quantity of pallets per SKU. Moreover, equipped with a motorised shuttle car, the organisation can load and unload merchandise more rapidly. Haricaman also decided to digitalise the management of its facility with Easy WMS because of the software’s ability to monitor goods at all times. Traceability is an indispensable requirement in food logistics.
Easy WMS was integrated with Haricaman’s SAP ERP system to transfer data and information on pallets leaving production and ensure that orders are shipped at the right time. This has resulted in greater productivity and the complete assurance that warehouse operations meet the set objective: to effectively satisfy customers’ requirements.
Semi-automated storage of finished goods
“By automating operations with the Pallet Shuttle, we’ve achieved the throughput necessary to store pallets from production and subsequently send them to our customers,” says Rodríguez.
In addition to leveraging all available surface area to accommodate the highest number of finished products (primarily breakfast cereals), the semi-automated Pallet Shuttle speeds up the storage and retrieval of goods from their locations.
Mecalux set up a total of three 13-metre-tall blocks of racking with a capacity of over 2,000 pallets. It personalised the locations to fit both European and North American (GMA) pallets. “The advantage of this solution is that we can house a large quantity of products in a small space,” says Rodríguez. Operators place each pallet at the entrance to the channel and the motor-driven shuttle car automatically moves them to the first free location.
In the central block of racking, goods are managed according to the first in, first out (FIFO) method to guarantee the perfect turnover of perishable goods. The racks have two working aisles: one for inserting pallets and another for removing them. The biggest advantage of this solution is that goods can be loaded and unloaded without interference.
Real-time traceability of flour
Traceability consists of monitoring the manufacture, processing and distribution of products, from the supply of raw materials for production through to the distribution of finished goods to end consumers. “Traceability is essential for our business because we have to comply with the most stringent food safety standards,” says Rodríguez.
By installing Easy WMS, Haricaman has modernised its entire supply chain. Before, the company managed its products manually with the help of its SAP ERP system. However, the risk of error was high. “We needed a WMS that would enhance efficiency and avoid the mistakes that come with manual management,” says Rodríguez.
In today’s logistics landscape, it is practically mandatory for businesses to be equipped with tools that record information quickly and accurately. Easy WMS is a software program that provides exhaustive, real-time tracking of goods that enter, remain in and exit the warehouse. This system knows all product details: size, batch, weight, characteristics, manufacture and expiry dates and inspection checks undergone.
To ensure traceability, goods that leave production arrive stretch-wrapped and labelled. Easy WMS identifies them as operators read them with RF scanners. Once the pallets are recorded in the system, the Mecalux software assigns each one the ideal location. It does this by making a series of calculations considering each item’s SKU and demand level and the number of empty slots.
To ship goods, Easy WMS assigns an outbound order to a dock. As directed by the software, operators locate the products included in each order and deposit them on the corresponding loading dock, where they await distribution. By monitoring each process the materials go through, the Haricaman warehouse has minimised errors and fulfils orders in a timely manner.
Pallet Shuttle integrated with Easy WMS
The company has also implemented a software program to control the Pallet Shuttle system. This advanced Easy WMS functionality enables operators to manage the status of goods as well as the movements made within this storage system from a single device. Using a Wi-Fi-connected tablet with an intuitive interface, operators orchestrate the maneuvers of the motorised shuttle cars. They can execute numerous functions, such as:
- Specify the quantity of pallets to insert in or remove from a channel.
- Control inventory by counting the number of pallets stored in the channels.
- Choose the goods location strategy for managing loads: FIFO or LIFO (last in, first out).
- Compact the pallets in the channels.
- Locate a shuttle by means of an audible, light-up signal.
- Manage users and authorise personnel to operate the shuttle cars.
With this software, Haricaman has simplified and expedited the work of shuttle operators. The company can manage Easy WMS tasks and control the electric shuttles via the same screen.
Future-ready digital logistics
With Easy WMS, Haricaman can chart its products in real time. The software has also been instrumental in making its logistics processes more efficient. The organisation can now satisfy the needs of its production plant and supply its customers as quickly as possible.
Since it was founded in 1991, Haricaman has embraced innovation and progress to achieve the quality, productivity and sustainability goals it pursues in all its production processes. Its facility in Toledo — capable of producing 60 million bags of flour a year — has become a benchmark in the sector thanks to process digitalisation and automation.
Mecalux’s end-to-end solution — with the semi-automated Pallet Shuttle system and Easy WMS software — has allowed us to optimise and streamline the storage of our finished products. At the same time, it’s given us complete traceability of every item we send to our customers.
Gallery
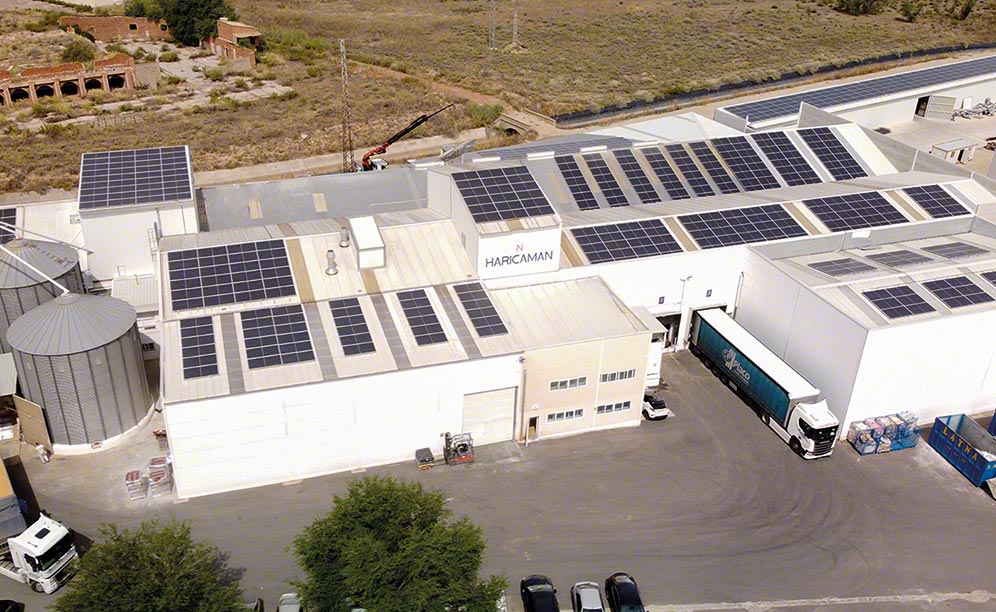
The Haricaman facility in Toledo, Spain, with Mecalux’s Pallet Shuttle system
Ask an expert