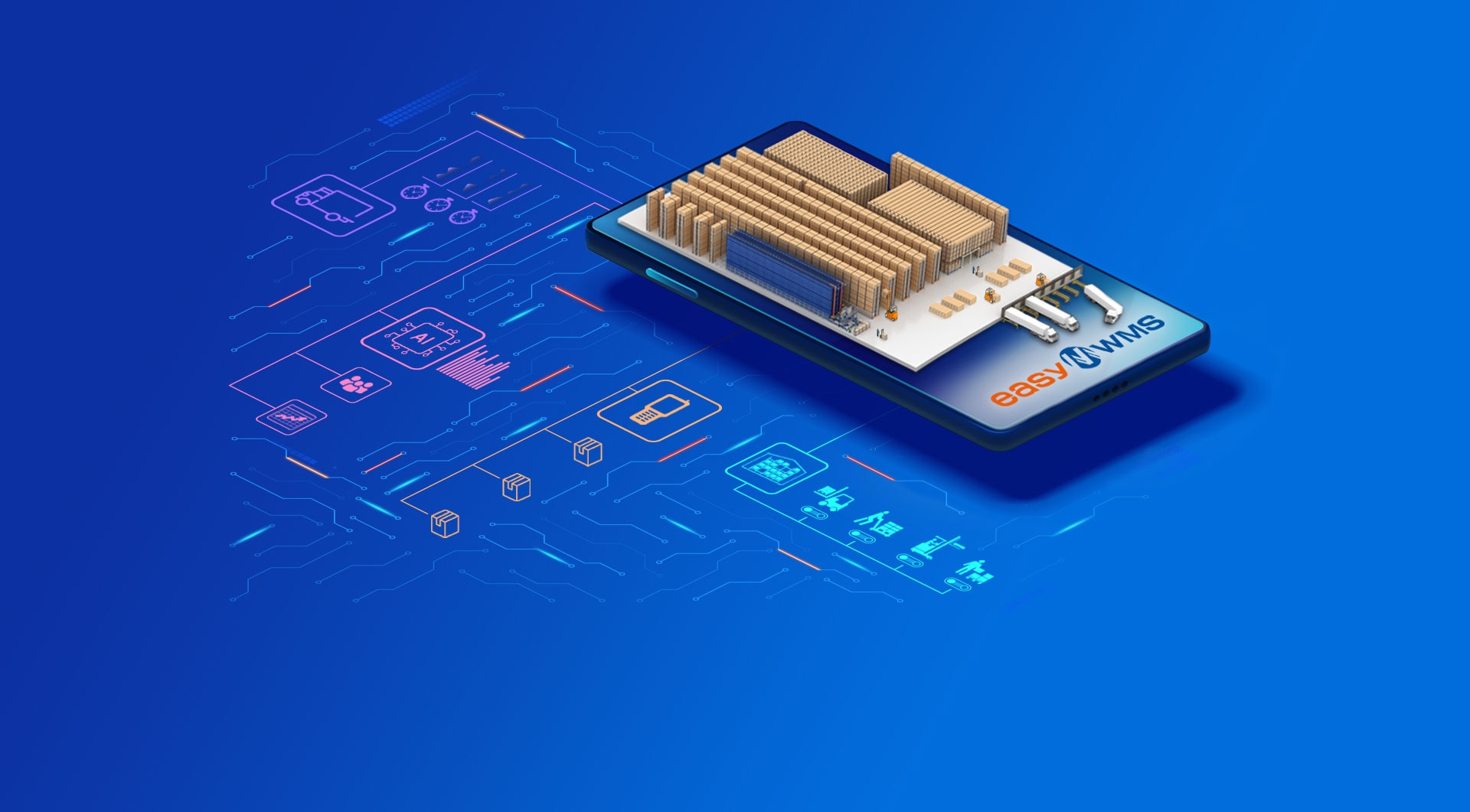
How do you ensure error-free management of 6,000 different references from the automotive industry?
Centres AutoEquip are now able to manage a multitude of different car parts, and provide any single one within minutes, thanks to Mecalux’s Warehouse Management Software EasyWMS.