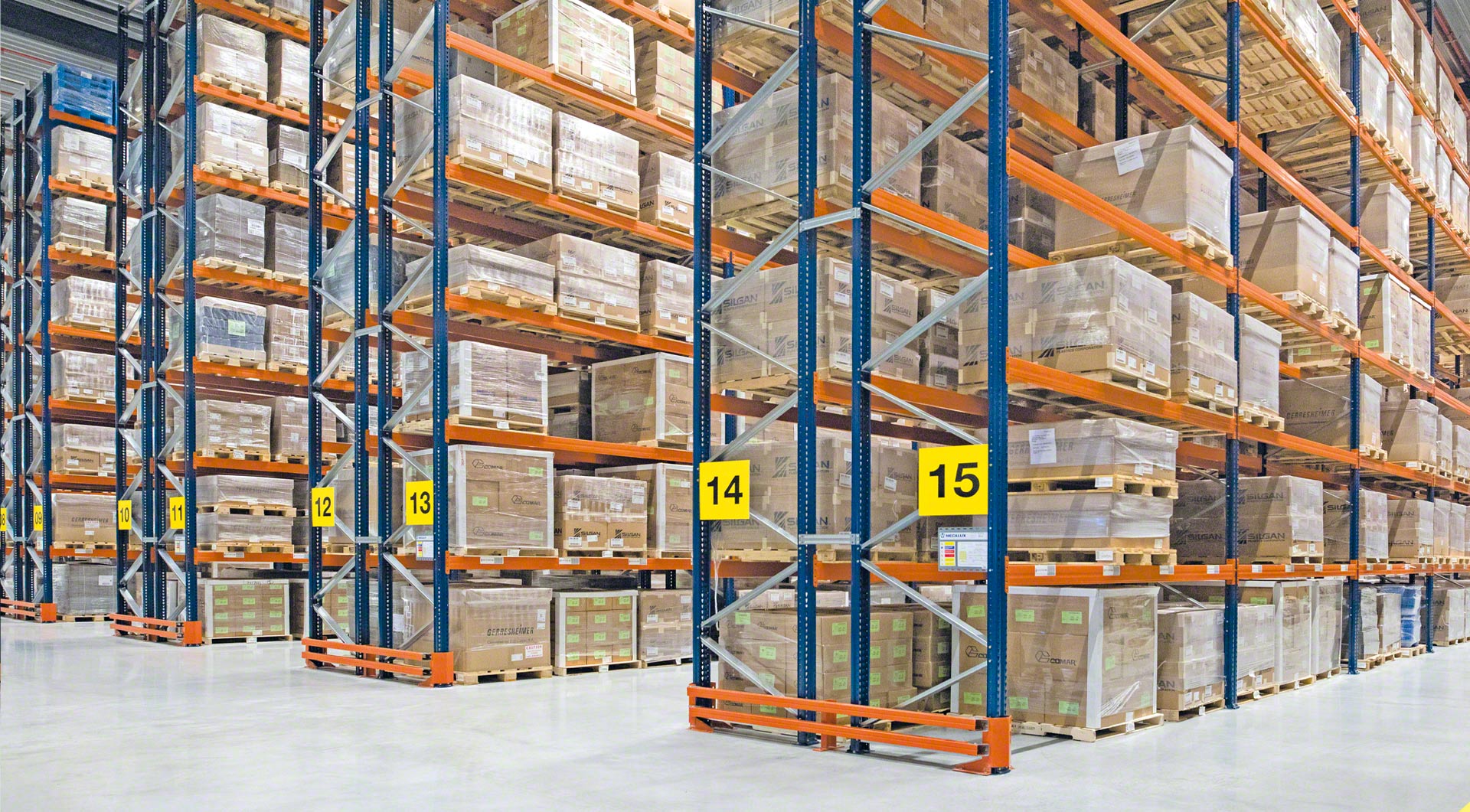
Mecalux keeps the logistics operator Disalfarm in action
Trilateral stacker cranes; an excellent option for automating your warehouse. Replace forklists with automated systems, without having to modify the existing rack structures.
Trilateral stacker cranes; an excellent option for automating your warehouse. Replace forklists with automated systems, without having to modify the existing rack structures.