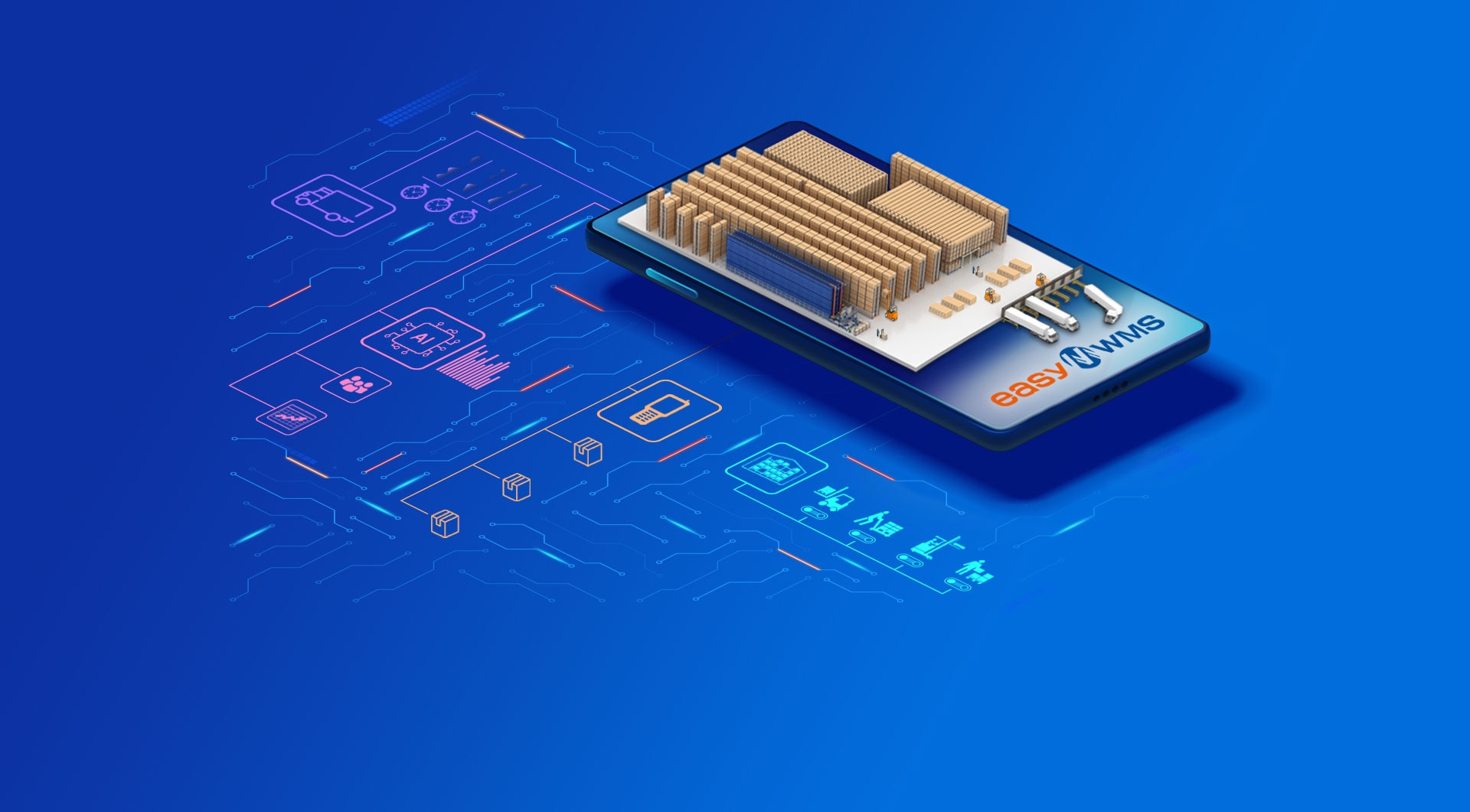
Omnichannel solution for Danone's logistics operations
The implementation of Easy WMS — and its Multi Carrier Shipping and Supply Chain Analytics modules ─ has helped Danone to benefit from an agile, flexible supply chain capable of adapting to changes