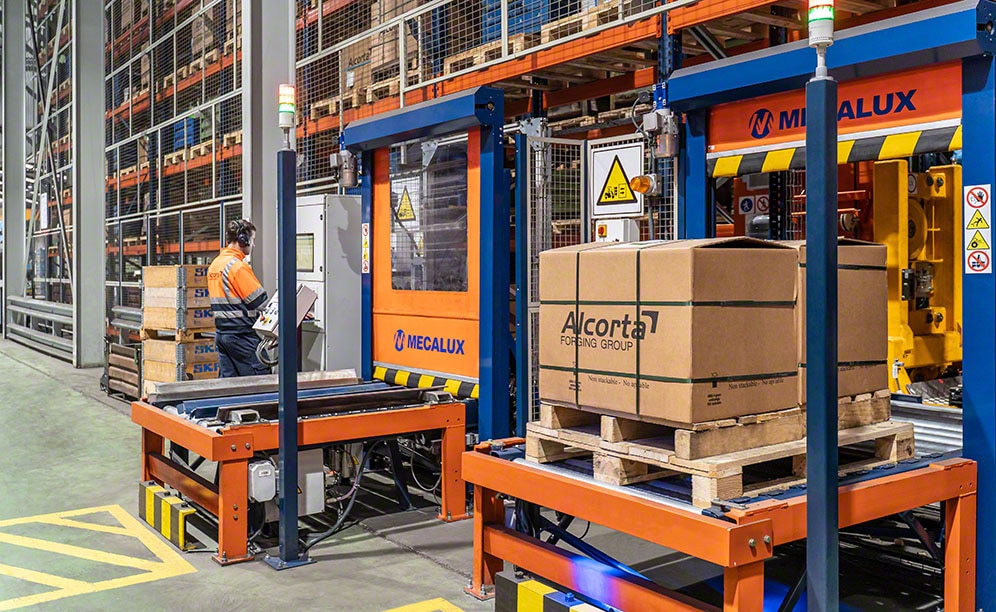
Alcorta Forging Group: technology connecting the warehouse with production
Alcorta Forging Group has installed an automated warehouse for car parts, managed by Easy WMS
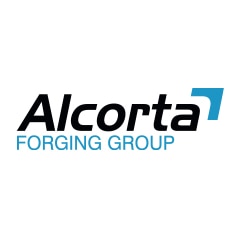
Transformation and improvement are part of the DNA of metalworking company Alcorta Forging Group. In this vein, it has put into operation a 14-metre-high automated installation with the capacity to store 1,115 pallets in its production plant in Elgoibar (Basque Country, Spain). Supervised by the Easy WMS warehouse management system by Mecalux, the installation moves around 300 pallets per day (including both entries and exits of raw materials and finished products) safely and accurately.
Forging solutions
Alcorta Forging Group has been doing business in the metallurgical sector for over a century. The firm, headquartered in the Spanish town of Elgoibar, is present in Germany, France, the Czech Republic, South Africa, China and the US.
Its origins date back to 1911, when it began manufacturing weapons. Since the 1980s, it has been designing and developing components and spare parts for companies in the automotive industry. The firm is noted for the quality of its products, its relentless pursuit of innovation and its commitment to respecting the environment.
With a turnover of EUR 70 million per year, 85% of which is comprised of exports (mainly to France, Germany and South Africa), Alcorta Forging Group has established itself as one of the most prominent Spanish businesses.
The engine of the production centre
The company has a production plant in Elgoibar (Basque Country, Spain), where every year it manufactures and distributes close to 20 million parts and components for leading automotive companies.
For Alcorta Forging Group, customer satisfaction is a major priority. Hence, its dayto-day activities consist of designing and developing new solutions to meet the needs of an increasingly demanding market. José Antonio Fernández, manager of the warehouse in Elgoibar, stresses that the firm transforms and improves all its operations assiduously to make them more efficient: “we are undergoing a process of unprecedented growth. To serve more customers, we strive to improve and automate all our processes, including logistics.”
In line with this objective, Alcorta Forging Group has opened an automated installation bidirectionally connected to the production lines. It is designed to house the raw materials that must later be sent to the factory and, at the same time, to store and dispatch the finished products.
José Antonio Fernández asserts, “With this project, we aimed to track our stock reliably from the arrival of the raw materials through to the shipment of orders to customers.” With this in mind, the company has also implemented Easy WMS, the warehouse management system (WMS) by Mecalux. This software has centralised all information about the products and monitors their movements throughout the installation, thus ensuring total traceability.
In terms of design, Fernández adds, “We wanted to take advantage of the height of the building to achieve greater storage capacity.” The warehouse is 13 m high and 54 m long. With two aisles of single-depth racking, it holds 1,115 pallets with more than 300 different SKUs.
Automated solution
The installation is comprised of two clearly differentiated work areas:
- Front of the racking (connected to production): in this area, finished products are received, and raw materials are sent to the plant.
- Side of the warehouse (connected to the loading and unloading docks): here, raw materials sent by suppliers or other plants belonging to the company arrive, and finished products are shipped to end customers.
Each day, a total of 150 pallets are received (from both the docks and production). They must all go through a checkpoint where it is validated that their weight, measurements and characteristics comply with the parameters established and required in the installation.
At this checkpoint, Easy WMS identifies each item and introduces it into the system. Subsequently, it assigns it a slot according to its demand level and whether it is a finished product or a raw material. “With this working method, we have optimised the resources used to control stock,” says José Antonio Fernández.
The proper distribution of the goods throughout the warehouse has a positive effect on all operations. In the words of the installation manager, “It has provided us with increased flexibility and speed in storage and picking tasks.”
In addition, Easy WMS knows the exact location of each item automatically at all times. Achieving total traceability of the goods significantly reduces the possibility of making mistakes in any of the operations.
Easy WMS is integrated with Alcorta Forging Group’s ERP. Both systems communicate continuously and bidirectionally with the aim of managing the warehouse more efficiently and leveraging all the logistics processes carried out.
In each aisle, a twin-mast stacker crane is charged with moving the pallets from the entry points to the location assigned by the WMS at a travel speed of 120 m/min.
This automatic equipment speeds up goods storage, preparation and dispatch processes. Just as in the case of pallet receipts, a total of 150 pallets leave the installation every day, with two possible destinations: on the one hand, raw materials are sent to production, while, on the other, finished orders are distributed to customers. The pallets leave the warehouse in sequence, taking into account the order or transport route, and remain grouped together until they can be loaded onto the lorry.
Advantages of an automated warehouse
- Productivity and availability. The installation can run 24 hours a day at maximum throughput.
- Reduced operating costs. As operations are fully automated, a limited number of people and resources are required.
- Real-time inventory. The WMS identifies and monitors the status of goods at all times.
- Maximum use of space. The racks optimise space to achieve the greatest possible storage capacity.
Integration and automation
Logistics automation provides a constant flow of goods, increasing productivity, minimising errors and reducing costs for Alcorta Forging Group. Its new installation is fully integrated with production to supply the raw materials necessary to manufacture close to 20 million parts and components annually.
Technology is the link that connects production and storage with the utmost precision. Stacker cranes and conveyors streamline the goods entry and dispatch processes. Moreover, the WMS ensures total product traceability.
José Antonio Fernández - Manager of Alcorta Forging Group’s warehouse in Elgoibar
“The installation serves the purpose it was designed for: to be perfectly integrated with production plant operations. With this automated solution, we have optimised stock control and order preparation.”
Advantages for Alcorta Forging Group
- Total traceability: thanks to Easy WMS, the company identifies the origin and different phases that each product goes through across the manufacturing process.
- Integrated warehouse: the installation serves the important purpose of supplying production with raw materials and receiving and dispatching 150 pallets with finished products on a daily basis.
- Optimisation of space: the racking, measuring 13 m high by 54 m long, makes full use of the physical space of the warehouse, thus achieving greater storage capacity.
Warehouse of Alcorta Forging Group | |
---|---|
Storage capacity: | 1,115 pallets |
Pallet sizes: | 800 / 1,000 x 1,200 mm |
Max. pallet weight: | 1,300 kg |
Racking height: | 13 m |
Racking length: | 54 m |
Gallery
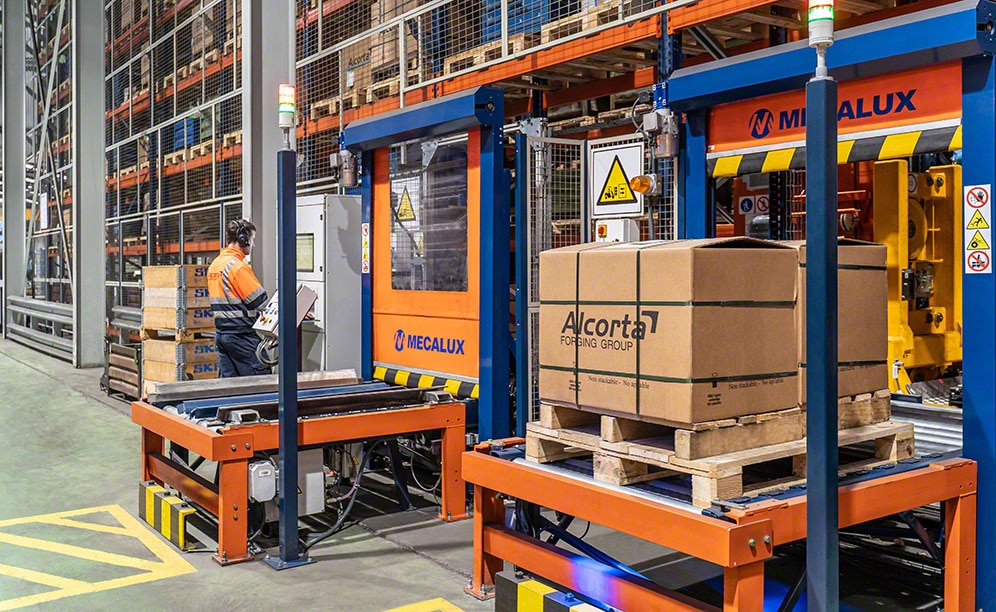
Alcorta Forging Group's automated warehouse for car parts
Ask an expert