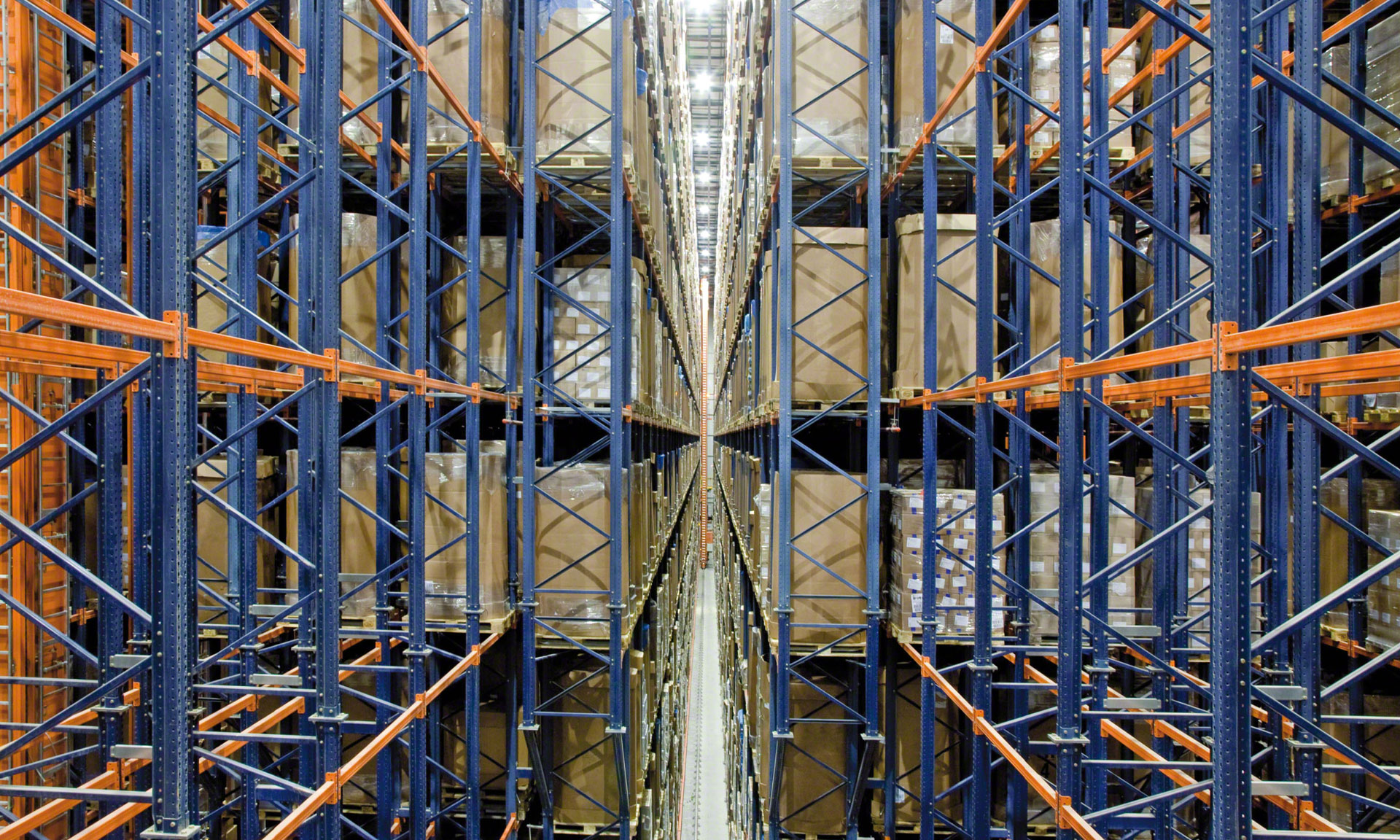
Large-scale cold-chain logistics automation
Congelados de Navarra’s logistics centre, managed entirely by Mecalux’s Easy WMS software, has one of Europe’s largest frozen food warehouses.
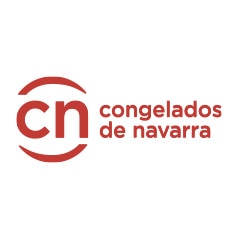
Congelados de Navarra automates its entire logistics centre in Fustiñana, Spain, with one of Europe’s largest frozen food warehouses. Mecalux’s Easy WMS is the nerve centre of the logistics complex, performing simultaneous and combined management of the different warehouses.
Steady and sustainable growth
Congelados de Navarra is a European leader in the manufacture and sale of deep-frozen vegetables. With a sustained annual growth of 20%, in little more than two decades, it has achieved a presence in more than 70 countries. The company employs 1,000 workers and 1,500 local farmers who grow the highest quality food on 24,000 hectares. A total of 65% of the 250,000 tonnes produced per year is exported to countries such as Germany, France, the UK and the US.
- Founded in: 1998
- No. of production centres: 6
- Annual production: 250,000 tonnes
- No. of employees: 1,000+
CHALLENGES
|
SOLUTIONS
|
ADVANTAGES
|
---|
The production and distribution centre of Congelados de Navarra in Fustiñana has become a clear benchmark in technology, innovation and productivity.
In recent years and as a result of sustained business growth, Congelados de Navarra’s logistics strategy has had a common denominator: to increase storage capacity to be able to dispatch its entire production output.
Julián Arnedo, Head of Shipping at Congelados de Navarra, explains that, to achieve this, they have always relied on Mecalux storage solutions: “Since 1998, when Congelados de Navarra began its journey, we chose Mecalux to install the first storage systems in our Arguedas centre. And we’ve maintained this relationship over the years.”
After building two automated frozen food warehouses between 2008 and 2011 with a capacity for 63,000 pallets, Congelados de Navarra needed a new facility to double its capacity and cope with the increase in sales. “The reason we built a new frozen foods warehouse was because our storage needs have increased dramatically in recent years. We wanted to double our storage space,” says Arnedo.
The company was looking for a system that would expand its warehousing capacity and, at the same time, streamline the flow of goods. “For this new project, we’ve continued to rely on Mecalux because their solutions have always worked very well for us,” says Arnedo.
The solution? To build one of Europe’s largest automated frozen food facilities: 44 m tall, 68 m wide and 170 m long. The clad-rack warehouse stores 83,300 pallets with products at -25 °C using the automated Pallet Shuttle system with transfer cars. This solution maximises storage capacity and streamlines the flow of movements. “In this case, and unlike our other warehouses, we opted for a high-density storage system because its design allows us to optimise space occupancy and energy costs,” explains Arnedo.
The facility with the Pallet Shuttle system has also been equipped with Mecalux’s Easy WMS warehouse management system. The logistics centre’s four automated facilities operate as one as a result of the combined and simultaneous management offered by the WMS software. This program manages the palletised goods from the time they leave production and arrive at the corresponding warehouse until they are prepared for distribution.
“The Easy WMS software enables us to manage this facility dynamically to maximise the occupancy rate of the storage locations. We now have occupancy rates of over 92%,” says Arnedo.
High flow of movements
In addition to doubling storage capacity, the automated Pallet Shuttle system with transfer cars installed in Congelados de Navarra’s warehouse is one of the most efficient high-density storage solutions on the market, guaranteeing a very high flow of incoming and outgoing goods.
Instead of one stacker crane distributing the pallets on all levels, three transfer cars have been placed on each level to move the goods to the storage channels, thus multiplying the number of cycles per hour. In total, the system’s 42 transfer cars move thousands of pallets daily following instructions from Easy WMS.
At the ends of the storage aisles, 10 pallet lifts have been installed — 6 at the front and 4 at the rear — connecting the 14 levels that make up the automated warehouse. The facility has two conveyor systems, one at each end of the aisles, to carry out different operations and prevent interference between them. At the front end, goods from production are received, and products are dispatched to two possible destinations: other frozen food warehouses or directly to the dispatch area. At the rear, the outgoing goods are sent to the packing and mixing area.
The automated facility with the Pallet Shuttle system is completely connected to the rest of the areas in the Fustiñana centre. Through the use of robotic handling equipment, this warehouse is linked to the production lines, the other three facilities, the packing and mixing area and the dispatch zone.
The goods from production are transported to the automated warehouse via a 130-metre-long electrified monorail. This system reaches a speed of 100 m/min and ensures a constant and safe flow of goods. Before entering the frozen food facility, the pallets pass through an anteroom equipped with a security airlock system. This technology consists of two interlocking doors that are never open at the same time. It avoids sudden changes in temperature, loss of cold and condensation to keep the goods in perfect condition.
The dispatch area has 11 automated conveyor channels that are used as preloads. Following the sequencing previously established by Easy WMS, the pallets are classified by customer order or route.
Easy WMS, the nerve centre delivering traceability and control
Mecalux’s Easy WMS software is involved in all processes carried out in the Congelados de Navarra logistics centre. It does this by coordinating the four warehouses that make up the complex. Easy WMS manages palletised goods coming from production, assigns their location on the racks, controls the stock and streamlines the dispatch and movement of pallets to the mixing areas, among many other functions. All of this is based on an essential premise for any company working in the food sector: traceability. Easy WMS provides real-time information on the status, location, batch and expiry date of each product.
The goods arrive in bundles from the production lines. The WMS identifies the pallets when they cross the checkpoint, validating whether they comply with the requirements established for their storage. Easy WMS then assigns them a location in one of the four warehouses based on rules and algorithms that take into account the characteristics of the products, consumption criteria, their turnover and the number of empty locations.
In the case of the frozen food facility with the automated Pallet Shuttle system, the rules configured in Easy WMS classify the stock between the three aisles according to their production batch. Due to Congelados de Navarra’s high consumer demand, Easy WMS has been configured to achieve a warehouse occupancy rate of over 92%.
This is made possible by a shared channel operation. That is, each channel can store two different SKUs in order to occupy all locations. In addition, the WMS follows the FEFO (first expired, first out) criterion when dispatching goods, so the first products to leave the facility are those with the closest expiry date.
For dispatch, the WMS designates the items to be distributed based on the orders placed by customers. Easy WMS organises the pallets with finished products that can be dispatched, ordering them to be sent to the loading docks in sequence. Throughout the process, the goods are always kept frozen so as not to break the cold chain.
In order for management at the Fustiñana centre to function correctly overall, Easy WMS is in permanent communication with the other software used at the company’s centre: Congelados de Navarra’s ERP program and manufacturing execution system (MES).
A landmark centre within the sector
With a capacity for more than 160,000 pallets, the Congelados de Navarra logistics centre has 18 stacker cranes, 53 transfer cars, 42 shuttles, 20 lifts, four 600-metre-long electrified monorail systems with 72 trolleys and hundreds of metres of conveyor lines. Easy WMS allows all these elements to move thousands of pallets efficiently every day, with up to 100 truckloads dispatched daily.Congelados de Navarra manufactures most of its products at its Fustiñana plant, one of the most modern and technologically advanced production centres in the European market, as well as a global benchmark in the food sector. Thanks to Mecalux’s collaboration and automated storage solutions, the leading company in the production and distribution of deep-frozen vegetables has efficient and centralised logistics operations to support its high production volume and distribute its products around the world.
Fustiñana: a centre with the Mecalux stamp
Opened in 2008, the Fustiñana production plant has been expanded over the years in different stages. In total, more than 160,000 pallets of frozen products are stored in four automated facilities connected by conveyors and electrified monorail systems.
Phase 1. In 2008, the first automated clad-rack warehouse, which operates at a constant temperature of -25 °C was built. With a height of 36 m and a capacity for 27,000 pallets, it is made up of six aisles with double-deep racking.
Phase 2. In 2011, the assembly of the second automated frozen food warehouse was completed. With similar characteristics to the previous one, it is attached to and integrated with it but larger in size: it has eight aisles and a capacity for 36,000 pallets.
Phase 3. In 2017, Congelados de Navarra built a new packing and mixing line. Once again, it relied on Mecalux to install stainless steel conveyors, ideal for humid areas, to connect this zone with the rest of the production areas and the logistics facilities.
Phase 4. In 2019, the third automated clad-rack warehouse was commissioned. With a capacity for 83,300 pallets, it houses frozen products in a space of more than 500,000 m³. Unlike the other two facilities, it is equipped with the Pallet Shuttle system with transfer cars.
Phase 5. In 2022, the fourth automated warehouse of the logistics centre was built and outfitted with double-deep stacker cranes. Also rack-supported, this facility has a capacity for around 16,000 pallets of frozen products.
In 1998, when Congelados de Navarra began its journey, we chose Mecalux to install the first storage systems in our Arguedas centre. And we’ve maintained this relationship over the years. For this new project, we’ve once again relied on Mecalux’s experience and the quality of its solutions.
Gallery
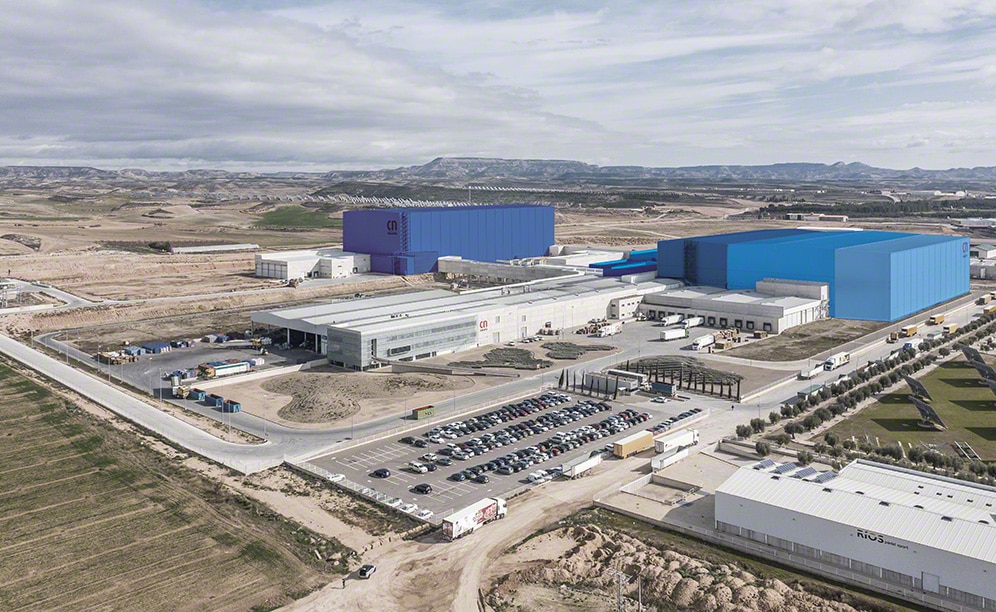
Congelados de Navarra’s logistics centre in Fustiñana
Ask an expert