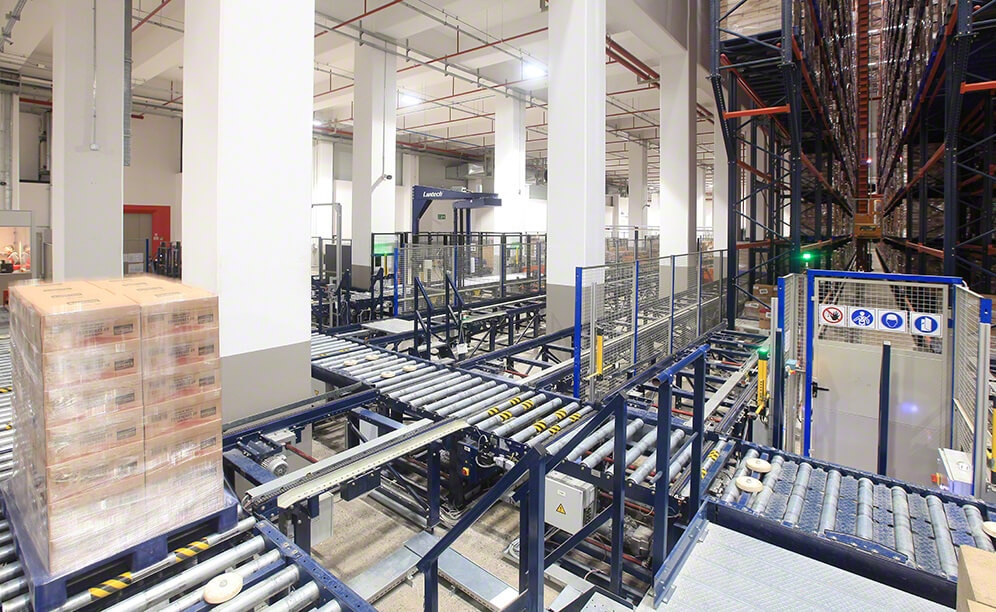
Tadim’s automated warehouse with dried fruits and nuts in Turkey
Tadim’s automated warehouse in Turkey manages 5,300 pallet of finished product
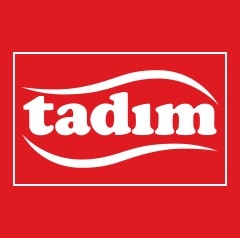
Tadım, a merchandiser of nuts and dried fruits, has opened an automated warehouse in the city of Gebze (Turkey). More than 5,300 pallets filled with finished product are warehoused in this storage installation, ready to be shipped to company clientele. The rollout of cutting-edge technology in all its logistics processes, including Easy WMS by Mecalux, falls within its strategy to move towards Industry 4.0 based business practices progressively. As a result, Tadım has expanded storage capacity by 143%, increased productivity and reinforced its international expansion process.
Leaders in Turkey
Founded in the Turkish city of Gaziantep, Tadım is a front-runner in the preparation and packaging of nuts and dried fruit products. Since it started doing business in 1971, this company has shown that it operates at very high work standards to make sure its products are of the highest quality and the freshest.
According to Kemal Güler, logistics manager of Tadım, “Our company enjoys very solid brand recognition, an enthusiastic team and visionary management. All these synergies have materialised in Tadım’s expanding market share in Turkey year after year, as well as us managing to expand into new countries.”
Currently, it operates four production centres spread throughout Turkey and Germany, besides a sales network that stretches Europe-wide, and into the US.
Tadım’s installations
Tadım operates one of its biggest production centres out of Gebze in Turkey. It fills a full 25,000 m2 and consolidates its entire range of products and materials under one roof (even products from other plants) required for processes like salting, toasting, packaging and packing.
Previously, it had a warehouse in which it could house 2,000 pallets, but it was a tight fit. “We needed more space,” emphasizes Kemal Güler. “Both Tadım’s product range and distribution territory were expanding in leaps and bounds, which would require more warehousing space and meant we had to run inputs and outputs at full speed.”
The company set out to build a new warehouse and to allocate space occupied by the old storage installation to enabling more production lines and, as such, got in touch with Mecalux. “We turned to Mecalux as a supplier because, without a doubt, it is one of the leading companies in the storage solutions sector worldwide. The close partnership we maintain with the technical team from its Turkish delegation was our main reason for choosing Mecalux,” points out the logistics manager.
The Mecalux technical team in Turkey travelled to the Gebze district to visit Tadım’s installations and analyse its needs in-detail and gear a solution towards the company’s specificities. “We created a planning team to discover the best solutions that would adapt to our needs. On the other hand, Mecalux presented us with two solutions: an automated warehouse and a warehouse management system. We saw that the two worked hand in hand in a viable way that worked for us,” explains Kemal Güler.
Setting up an automated warehouse was a critical decision for Tadım because it would have direct repercussions on its company’s productivity. For this reason, the company’s management wanted to be completely sure of all possible options before making any sort of definitive decision.
According to Kemal Güler, “the Mecalux team organised a trip to Spain for us and invited us to visit another warehouse with fairly similar operations to our own. A visit to this multination cracked the project wide open since we saw first-hand the role these solutions played, and had only seen on paper up till then.”
Features of the automated warehouse
It fills a 7,700 m2 area and comprises three, 70 m long aisles with single-depth racks on each side. “Right now, we have three aisles, although we have set aside space to enable three more aisles in the future, when we really need them,” points out Tadım’s logistics manager.
The racks are 23 m high, divided into three storage levels, and offer a total storage capacity of 5,364 pallets with around 120 different SKUs. “This warehouse has meant a 143% increase in capacity compared to our previous installation,” compliments Kemal Güler.
A stacker crane circulates in each aisle in charge of collecting pallets from the inbound conveyors and depositing them in the locations assigned by the Easy WMS warehouse management software of Mecalux. Automatic handling of loads has had a direct impact on the warehouse’s productivity and the customers’ overall satisfaction and experience: “we have reduced the number of damaged pallets by 85%,” assures the logistics manager.
The stacker cranes move at a travel speed of 220 m/min and 66 m/min when raised, which makes it possible to carry out 100 combined cycles/hour (100 incoming and 100 outgoing pallets).
The warehouse is located close to the production centre. “The two installations are connected through a conveyor circuit,” explains Kemal Güler. The conveyor system’s job is to move pallets flowing from production to the warehouse’s entrance and, also, send empty pallets and returned goods from the warehouse to production.
Automated inputs represent a major achievement for Tadım. In the words of Kemal Güler, “we raised our daily receptions by 73%.” It receives 1,000 pallets/day on average because this conveyor system ensures a continuous flow of goods and minimises handling equipment activity (which is also a risk prevention measure).
Kemal Güler - Logistics Manager at Tadım
“The new warehouse has sorted out all the business needs we presented to Mecalux’s technical team. We expanded storage capacity (in fact, we doubled it) and, at the same time, increased the number of daily inputs and outputs as a result of improved productivity. In addition, the warehouse management system has reached 99.1% effectiveness over the last few months. Without a doubt, we have a system on our hands which we can really rely on.”
The advantages of going automated
“Now, Industry 4.0 is bigger than ever and digital business is one of the central pillars in our vision for the future,” asserts Tadım’s logistics manager. Industry 4.0 means the implementation of digital technology in all production and logistics processes to make them more efficient.
Digitalization offers huge advantages to companies, because it means they can adapt to fluid demand levels and new consumer habits easily, providing personalised customer care or designing, making and selling products in less time. Tadım wanted its new warehousing facility to be more productive.
That is why, “automating was the best solution for us, compared to traditional storage systems,” adds Kemal Güler.
An automated warehouse is the evolution of a traditional warehouse, because the electromechanical equipment (conveyors, stacker cranes, transfer cars, etc.) carry out operations that, in a non-automated warehouse, would otherwise be done by workers operating traditional forklifts (mainly, in-house transporting and slotting of the goods in the racks).
Building an automated warehouse yields the company advantages like:
- Optimum use of space and constructed volume.
- Perfect control over stored goods and maximum storage capacity optimisation.
- Real-time inventory.
- Higher productivity and availability.
- Lower structural maintenance costs.
- Reduced operating costs.
- Safely kept goods and lower risk of accidents.
- Non-stop 24-hour operations.
- Lower personnel costs.
Order fulfilment and dispatch area
Each day the installation puts together around 40 orders, each of which comprises around 24 product lines. It set up a specific zone to carry out this operation, just next to the automated warehouse.
A total of 57 live channels were enabled (each one of these corresponds to a distinct SKU), while there is also space for the addition of more channels sometime in the future.
These channels, which rest on the floor, are slightly inclined so that pallets flow via gravity from the highest to the lowest point. Down below, operators have direct access to pallets and collect the boxes that comprise each order.
The channels run in parallel, with a central aisle where a transfer car circulates distributing pallets to the corresponding channels. Each channel holds up to a maximum of two pallets of the same SKU, making sure reserve goods are always available.
Once all the orders are prepared, these are warehoused (on standby) waiting to be sent to the dispatch zone, located just in front of the storage aisles. A total of 21 live preload channels were placed here, each deep storing up to 16 pallets. A transfer car sorts the goods in the preload channels. The pallets are grouped into each channel taking into account if the pallets are part of the same order or route and are subsequently readied to load into the distribution vehicles.
“With how the dispatch zone is designed and organised, we have increased the number of pallets leaving the warehouse by 56%,” mentions Kemal Güler. The warehouse distributes 1,000 pallets each day and, out of this figure, 95% are sent to supermarkets and small retail shops in Turkey. Meanwhile, the remaining 5% is primarily shipped to Tadım’s customers in the Balkan Peninsula (countries like Romania, Kosovo, Albania, etc.).
Computerised system for large-scale project
It was a crucial step to deploy an efficient warehouse management system (WMS) for such a massive, fully-automated installation like Tadım’s, a system ready to monitor all the installation’s processes: input of the goods, storage, order prep and dispatches.
Likewise, Easy WMS is in permanent, bidirectional communication with Tadım’s SAP ERP to achieve global warehouse management. The two systems share information like, e.g., what products are about to arrive at the warehouse or the orders that the customers have requested and, as such, must be fulfilled and distributed on the double.
Before flowing into the warehouse, the pallets coming from production pass through a pallet inspection checkpoint where each pallet’s weight, load size (via the loading gauge) and pallet condition (spaces, studs and skids) are revised, and the product’s barcode is scanned for its identification. Here is when they also check that the received pallets correspond to those Tadım’s SAP ERP indicated in its advanced delivery notification.
Pallets that are stored in the racks on a daily basis might include finished products from the production lines, prepped orders in the picking zone or customer returns. Strict control over products avoids any sort of error and also increments the productivity of all the operations.
Easy WMS must identify the products’ characteristics before they are slotted in the warehouse. The rotation of the goods is one of the main determinants for assigning a location in the racks. So, the A rotation products are deposited close to the conveyors in one of the end racks, because these products enter and exit more often. Type C products, by contrast, are placed at the end of the aisle. It also considers the production or expiration date of each item.
Order fulfilment is a vital operation at Tadım. That is why it has a well-designed picking zone, which in addition to Easy WMS’s tailored instructions mean the company can prepare a huge volume of orders per day.
It is the WMS’s job to supply the live picking channels as the need presents itself. Thus, the exact items are always available and operators never have to wait to make up each order. Replenishment is automatic, since the system uses conveyors and transfer cars to shift pallets from the automated warehouse to specific locations in the live channels.
When it comes to picking, workers must also consider the products’ characteristics which comprise each order and if these items can be stacked. The system has designed a general sequence the operators must follow while preparing any order: first collect the heaviest products and after that, the lighter ones.
Operators carry handheld radiofrequency devices to communicate with Easy WMS. The system tells them which SKU they must collect directly off the pallets located in the live channels. Once they have done so, they confirm the action as completed.
When they finish making up the orders, these orders are stored waiting to be sent to the dispatch zone. Easy WMS organises pallets as per what is exiting the warehouse (following a sequence). In each channel, pallets are classified according to the order or shipping route. Likewise, channels are organised based on when they are delivered. So, for example, pallets which are delivered first, exit the warehouse last. These are placed in the end position of the preloads channel and, as such, are the last to be loaded in the lorry.
Advantages for Tadım
- Automated operations: Tadım has been the direct beneficiary of fully-automated operations and management, because it has rubbed out any potential mistake making and has incremented productivity.
- Picked, packed, ready: the company has allocated an area just for picking in order to prepare as many orders as possible (up to 40, 24-line orders each day).
- Bigger better capacity: the warehouse provides room to house 5,634 pallets, i.e., a boost of 143% compared to Tadım’s previous warehouse.
Automated warehouse of Tadım | |
---|---|
Storage capacity: | 5,364 pallets |
Pallet size: | 800 x 1,200 mm |
Max. pallet weight: | 200 kg |
Warehouse height: | 23 m |
Warehouse length: | 70 m |
Gallery
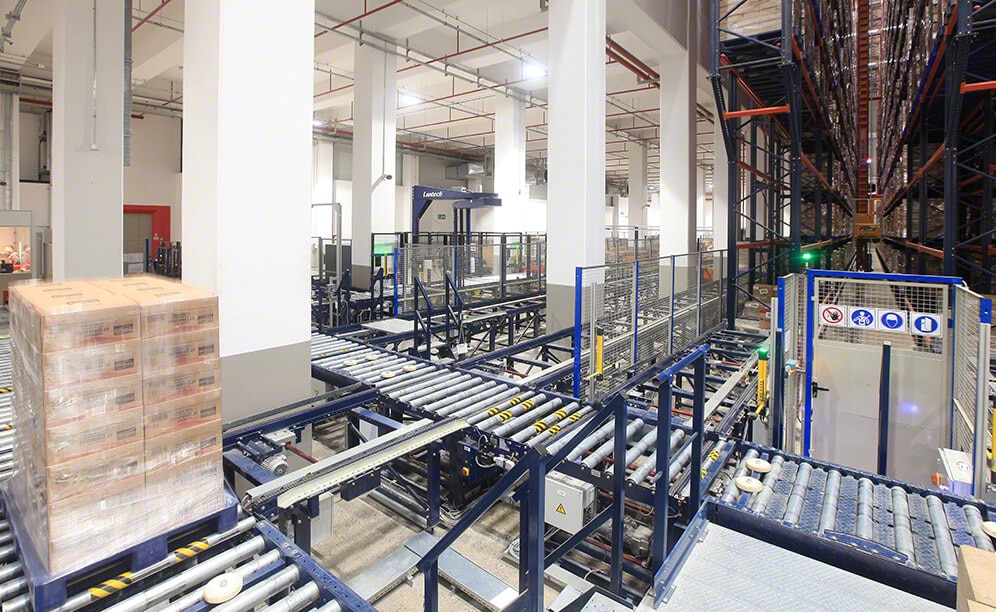
Automated warehouse for Tadim’s dried fruits and nuts in Turkey
Ask an expert