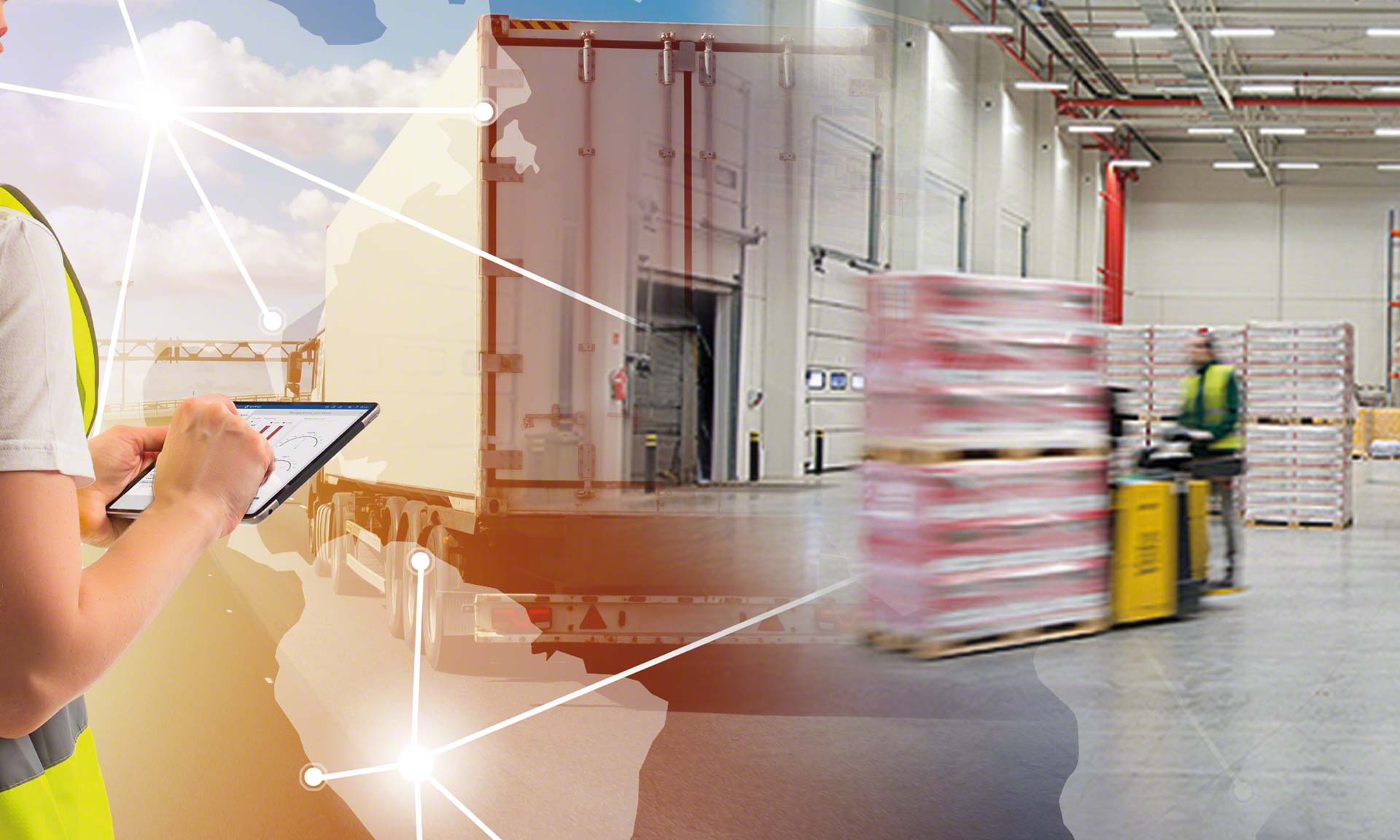
Electrolux manages household appliances with Mecalux’s Easy WMS software
Electrolux, the world leader in home appliances, digitises its logistics operations to boost online sales.
Electrolux, a world leader in household appliances, has digitised its facility in Cali (Colombia) with Easy WMS warehouse management software by Mecalux. The company’s priority is to monitor products and processes in order to make strategic improvements based on reliable data.
Electrolux: a world leader in household appliances
Founded in Sweden, Electrolux is a leading company in household and professional appliances. Electrolux products include refrigerators, dishwashers, washing machines, vacuum cleaners and cookers sold under the Electrolux, AEG-Electrolux and Zanussi brand names. The company strives to constantly innovate in order to offer products that meet the most demanding needs of its customers.
- Founded in: 1919
- International presence: 150+ countries
- Sales: 40+ million products annually
- No. of employees: 51,000
CHALLENGES
|
SOLUTIONS
|
BENEFITS
|
---|
In recent years, the multinational household appliance company Electrolux has been pursuing a strategy of expansion on the Latin American continent, especially in Colombia, Ecuador and Peru. To absorb this growth, the company has decided to optimise its logistics processes to speed up the dispatch of orders.
In Colombia, Electrolux has modernised its supply chain with the help of the latest technology. Specifically, it has digitised its facility in Cali with Mecalux’s Easy WMS warehouse management software. This computer program organises the different operations and controls the traceability of 250,000 products in real time.
“Traceability is indispensable in a facility with as many products as ours. In an area of 6,000 m², we store 72,000 finished products and 178,000 spare parts. We need to continually track all the movements our goods make, from the moment they arrive in the warehouse until they’re dispatched, in order to reduce the number of errors and ensure top-quality deliveries to end customers,” says Jeison Saavedra, Inventory Analyst at Electrolux.
Prior to the implementation of Easy WMS, the multinational had been using warehouse management software that was becoming outdated. “With a supply chain as dynamic as that of Electrolux, we needed a more advanced program with more functionality. When the number of products started to increase, we realised that we had to keep tighter control of the goods. We wanted to minimise any possibility of errors arising from manual handling,” says Saavedra.
When it came to choosing the software, Saavedra points out one of the basic requirements it had to have: “We wanted it to be able to integrate with our ERP system.”
After comparing different options, Electrolux opted for Easy WMS, the digital solution from Mecalux. “We felt that it would be able to solve our needs because it had all the functionalities we required: it could control the goods, organise an effective slotting strategy and integrate easily with our ERP,” says Saavedra.
At its Cali facility, Electrolux uses iScala ERP software to organise all the information flows within the company, including data related to logistics. By integrating iScala with Easy WMS, both programs communicate permanently and bi-directionally, transferring information to streamline operations and boost warehouse productivity. For example, the ERP communicates customer orders to Easy WMS so that the logistics system can organise their immediate picking and dispatch.
Facility prepared for online sales
“Our company is growing very fast in Colombia. Online sales are on the rise and are set to continue increasing in the coming years. We have to improve our logistics operations to ensure our deliveries to customers buying online,” says Saavedra.
Easy WMS is a flexible software program that adapts operations to the company’s new requirements. The system can modify its functionalities to cope with changes in processes, such as a rise in the number of online orders. How is this done? “The software is involved in all our warehouse processes, especially with incoming goods, order picking and shipping,” says Saavedra.
The Electrolux logistics centre in Cali receives around 10,000 items per month, between spare parts and finished products. Operators simply read the barcode on the items with their RF scanners so that Easy WMS can enter them into its database and assign them a location.
“During the goods receiving process, it’s essential that Easy WMS register all the information to record the arrival of new material and control its traceability,” says Saavedra. The software decides on the location for each item taking into account the characteristics of each product, its SKU and its level of demand. Thanks to effective stock organisation, Electrolux has been able to make better use of the space in its logistics facility and expand its storage capacity.
Once the receiving process is completed, the operators move these goods to the corresponding location following instructions from Easy WMS. One of the special features of this software is that it designs optimal routes to ensure that operators travel the shortest possible distances.
The Electrolux warehouse prepares around 200 orders per day, which are shipped to customers in Colombia and other Latin American countries. The Mecalux software distributes the work among the operators and sends them personalised instructions to perform picking.
On a single run, operators process several orders at the same time, following the Easy WMS instructions step by step. The products are moved to the consolidation area, where they are grouped by destination or transport route to maximise the loading space on the lorries and reduce the costs of distributing the goods.
“What we like most about Easy WMS is that we have precise control over our warehouse operations, the status of the locations and the traceability of the goods,” says Saavedra.
Optimised and controlled logistics processes
When modernising its logistics operations in Colombia, Electrolux had one priority: to have greater control over all processes performed in its facility. “Our desire is to have a competitive and flexible supply chain that can react to changing scenarios,” says Saavedra.
To adapt to new market needs and operate in a constantly changing supply chain, Electrolux has implemented two modules: Supply Chain Analytics Software and Labor Management System. These two extensions to Mecalux’s Easy WMS incorporate new functionalities so the company can monitor its warehouse operations.
► Supply Chain Analytics Software
The program comprehensively tracks all activity in the facility. Based on data analysis, the company can monitor the performance of all its processes and obtain a detailed map of operations. With this information, Electrolux can implement strategic measures to anticipate any changes. “To have an agile and flexible supply chain, we need to constantly make improvements in all our processes. The information that Supply Chain Analytics Software provides us with allows us to address the future changes we’ve foreseen in our business,” Saavedra says.
The module consists of control panels with precise information on warehouse operations. At a glance, the company’s logistics managers can view KPIs such as incoming goods, outgoing goods and the status of order picking.
► Labor Management System
The module measures the performance of the different warehouse activities with a view to facilitating decision-making by the company’s logistics managers.
“The work of our operators is fundamental to the development of the operations. Labor Management System enables us to plan the necessary personnel. One of the things we value most is that now we know the status of the operations without having to be physically present in the warehouse,” Saavedra says.
Labor Management System keeps track of workflows at the facility. The information allows the company to identify opportunities for improvement aimed at increasing operator productivity.
Digitisation to tackle the future
Electrolux is a company that is constantly evolving to adapt to market changes. The digitisation of its Cali warehouse is part of its expansion strategy in Latin America and its efforts to promote more online sales. With more effective control of its logistics operations, the company is able to maintain full availability of goods and serve a larger number of customers.
“At Electrolux, our mission is to enhance the customer experience and to ensure this is an added value. To this end, we aim for excellence in our logistics operations. Digitising our supply chain has led to more efficient and agile processes, as well as greater flexibility to adapt to market demands,” says Saavedra.
The Easy WMS software tracks Electrolux’s operations, thus ensuring a faster and more efficient warehouse. The system provides full and comprehensive control of each product and process, helping managers make decisions that contribute to optimising the supply chain. The Mecalux program will accompany Electrolux in any project it takes on in the future.
Mecalux’s Easy WMS meets our requirements: it can control the goods, organise an efficient slotting strategy and easily integrate with our ERP. Through the additional modules Supply Chain Analytics Software and Labor Management System, we have objective information that helps us to deal with the future changes we’ve foreseen in our supply chain.
Ask an expert