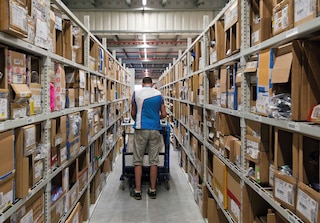
Warehouse slotting: amp up your productivity
Warehouse slotting is the process of determining the optimal location for goods in an installation. A good slotting strategy is essential for ensuring an installation’s efficiency. In fact, decreased delivery times and more expensive logistics floor space have forced companies to maximise the capacity of their storage space to remain competitive.
In this post, we’ll delve into the definition of slotting, exploring the main location management strategies and the ways in which certain software solutions can help in this regard.
What’s warehouse slotting?
The term slotting describes the strategy for distributing inventory throughout the various locations in the warehouse. The goal is to increase productivity in processes such as goods receipt, stock replenishment and picking.
This logistics procedure has become essential in light of the difficulty of expanding storage space. With new consumer trends, it’s no longer merely enough to prioritise space maximisation, but also the location of each SKU; the aim here is to reduce movements and fulfil orders more quickly.
Normally, the logistics manager is charged with devising the warehouse slotting strategy. To implement any location management technique successfully, you first need to have an identification method shared among all warehouse staff. Thus, the logistics manager must number the locations according to a system communicated to the operators, while ensuring that no mistakes are made when placing and removing the various SKUs.
Of course, the ideal inventory slotting strategy must fit the requirements of the warehouse and should be based on criteria such as:
- The stock turnover rate of each product (A, B, or C).
- The expiry date of each item.
- Goods flows throughout the installation.
- Optimal picking routes.
Bear in mind that warehouses have increasingly varied item masters — with a broader range of SKUs — calling even more for the adoption of slotting strategies.
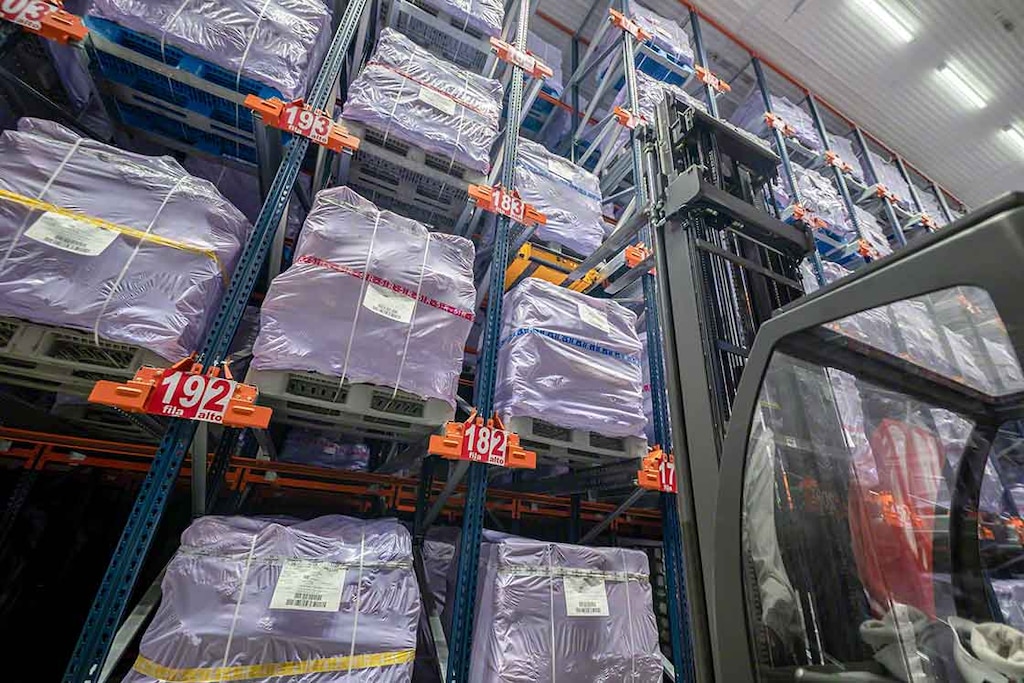
Advantages of optimising warehouse slots
Inventory slotting enables the following:
1. Maximisation of storage space: slotting takes into account all the available locations in the installation, not just specific areas with a certain type of product. This makes better use of the centre’s space.
2. Increased warehouse productivity: a good slotting strategy analyses the time spent picking each product and determines the positions of the goods. It does this in order to reduce the total time taken to carry out these movements, that is, to ramp up productivity in the installation.
3. Goods traceability: the slotting strategy prevents mistakes in product traceability, guaranteeing that workers know — at all times and in real time — the exact location of an item on its journey through the warehouse.
In addition, it should be noted that, to make the most of space and significantly boost productivity, inventory slotting should be designed with careful consideration to the installation’s characteristics and current flows. To do this, it is necessary to first extract these data. In this vein, the use of specialised software can be of great help.
Warehouse slotting software: The digital strategy
Digitisation has become the best method for eliminating inefficiency in any logistics process, including product slotting. Only a warehouse management system (WMS) is capable of designing an optimal, error-free location strategy, based on the criteria established by the manager of the installation.
A WMS such as Easy WMS by Mecalux not only ensures real-time stock control, but also allows you to know each SKU’s location at all times. More specifically, it coordinates product entries and exits to and from the warehouse based on designated variables, making the work of employees much easier.
The application works like this: the software is configured according to work and product flows — real or desired — taking place in the installation. Based on several goods entry criteria, the WMS classifies the product and applies certain location rules specified by the warehouse manager.
Let’s look at an example of how this software works: the WMS receives an entry order from the ERP on SKU01, set to expire in a week. The program is configured in such a way that all SKUs with an expiry date of less than a month are sent directly to the order preparation area (as opposed to being stored). In this scenario, the application will create an inventory replenishment task to stock the picking shelves and the operator in charge of receiving the goods will see it directly on his/her terminal. This prevents unnecessary movements and possible loss of stock.
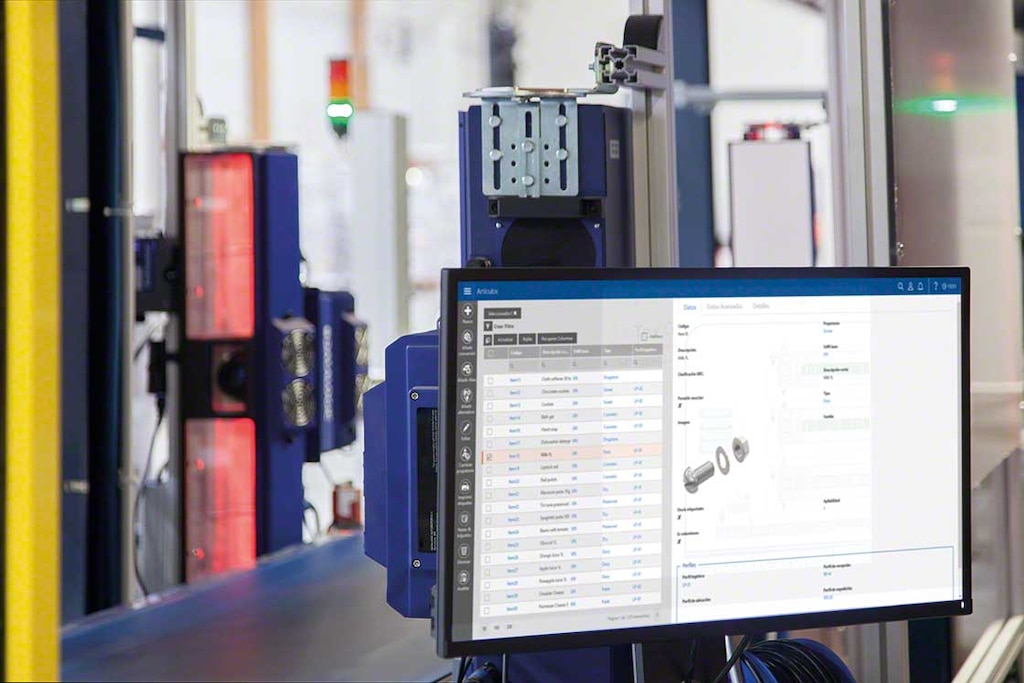
Automation of slotting management
New logistics trends are compelling warehouses to implement technology to increase their productivity. Slashed delivery times and the standardisation of boxes as the main e-commerce unit load have led logistics centres to search for procedures to maximise their installations’ throughput.
Several strategies have come to their aid, including slotting, which multiplies warehouse capacity and considerably reduces time spent on movements. All of this leads to a significant rise in productivity at these centres.
In the end, efficient warehouse slotting management reduces pickers’ workloads and optimises goods flows in the installation. Nevertheless, to ensure error-free implementation of warehouse slotting criteria, it’s necessary to use software that automates location assignments. This is because manual management of locations could result in serious errors and extra costs.
Easy WMS, our warehouse management system, has been implemented by more than 500 customers in 36 countries. If you’re looking to optimise inventory slotting at your warehouse, don’t hesitate to contact us. One of our expert consultants will help you to raise your installation’s efficiency to the next level and beyond.