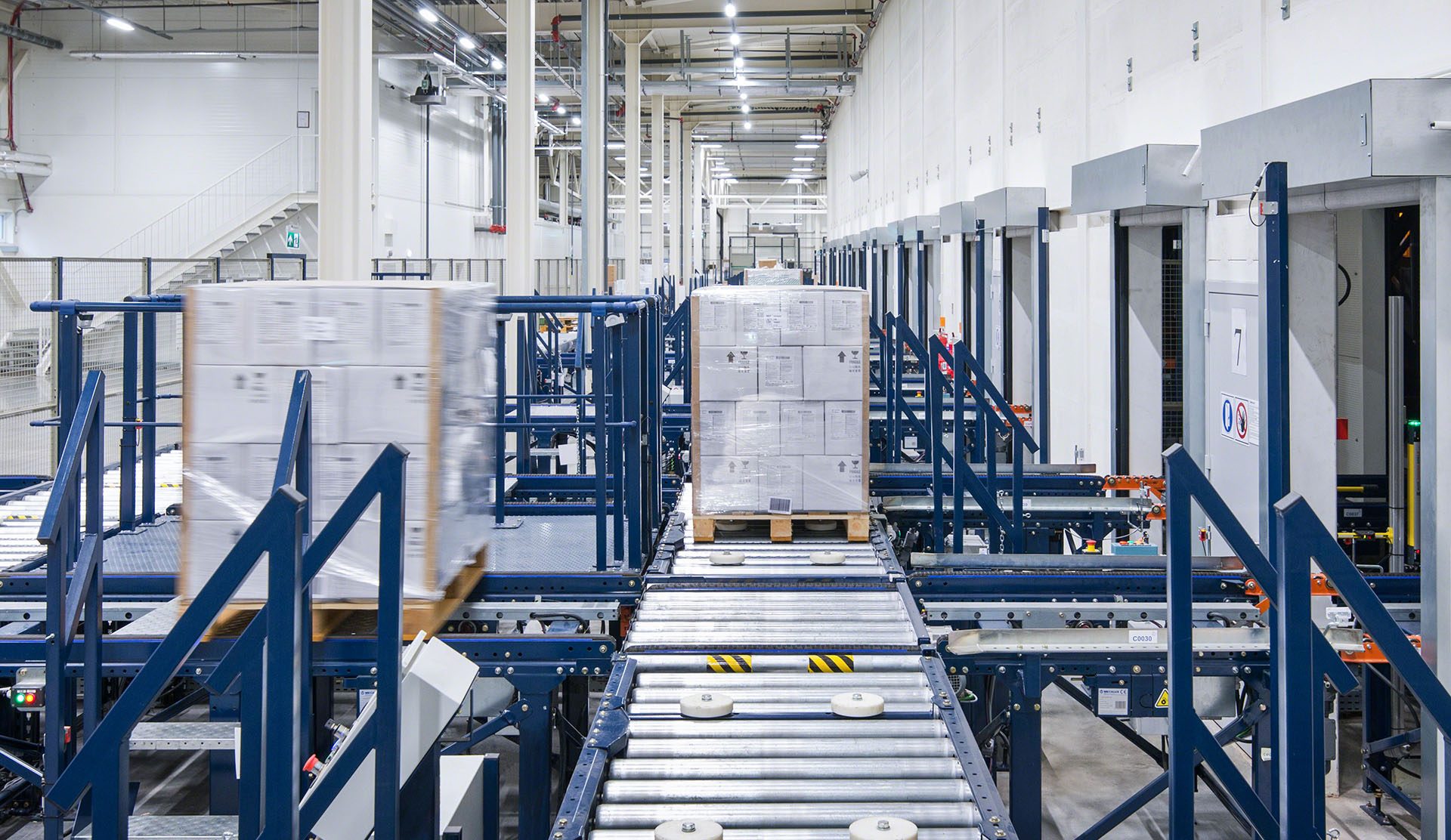
Intersurgical: oxygen for a medical product manufacturer’s logistics systems
With capacity for 50,400 pallets, it is one of the largest installations in the Baltic States
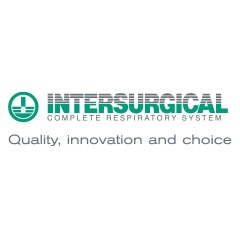
Innovation, technology and effort are the words that best describe Intersurgical, a multinational that provides flexible patient solutions for airway management, anaesthesia, critical care and oxygen and aerosol therapy for use within emergency care, hospitals and homes. To centralise its logistics operations, it has commissioned a 30-metre-tall clad-rack warehouse with capacity for 50,400 pallets in Pabradė, Lithuania. It is now one of the largest installations in the Baltic States. Automation was crucial for Intersurgical to be able to handle the 50% rise in warehouse inflows and outflows as a result of the COVID-19 pandemic.
Respiratory care specialists
Founded in the UK in 1982, Intersurgical is a global designer, manufacturer and supplier of a wide range of high-quality medical devices for respiratory support. These products are used in numerous hospitals, operating theatres, intensive care units, ambulances and homes in over 100 countries throughout the world.
This multinational, present in countries such as Germany, the USA, the UK, France, Canada, Spain and Sweden, arrived in Lithuania in 1994. It has a plant in the city of Pabradė where it manufactures solutions for anaesthetics and oxygen and aerosol therapy. In total, 99% of these items are exported to other countries around the world.
The arrival of the coronavirus pandemic, which causes serious respiratory infections, has led to an increase in Intersurgical’s workload. For example, movement flows in its warehouse have increased by 50% in a matter of weeks. In fact, the company has manufactured and distributed one million respirators for healthcare workers in Lithuania in record time. The key to Intersurgical’s continued efficiency? Being equipped with a flexible logistics system that operates 24 hours a day, thanks to automation.
Automation for centralised logistics
Intersurgical had been determined to build a large distribution centre for some time. Its intention was to turn the facility into its main logistics hub. In the words of Martynas Tamosiunas, Group Supply Chain Manager at Intersurgical, “We had been leasing external warehouses, operated by our staff and handling equipment, to store our finished products. We were also using the services of other external 3PLs to manage goods flows from the Far East.”
Determined to cut logistics costs, Tamosiunas adds, "What really drove this project forward was the need to consolidate all our external storage centres in one warehouse. This way, Intersurgical would be the sole owner and responsible for managing its own merchandise.”
One of Intersurgical’s priorities for this installation was for it to have fully automated operations. Martynas Tamosiunas acknowledges, “We chose to automate our processes because we believe this logistics trend will become increasingly important in our business. This is especially true if we want to have uninterrupted logistics flows and, likewise, minimise operating costs.”
In this vein, Mecalux has built and started up a spectacular, automated, 30-metre-tall clad-rack warehouse in Pabradė that provides storage for up to 50,400 pallets and 2,000 SKUs. The installation consists of eight 121-metre-long storage aisles with double-deep racks.
Its construction is self-supporting, that is, the racks themselves support the binding and vertical cladding. When designing and building these types of structures, Mecalux’s technical team took into account the force exerted by the stacker cranes and the wind as well as the weight of the snow. As a result, Intersurgical boasts a completely safe warehouse that leverages all available height and surface area to accommodate the greatest number of pallets.
Every day, the installation receives up to 500 pallets from different origins: the manufacturing plant located just beside it; other factories in the UK, China, and Italy; and suppliers. Meanwhile, nearly 400 pallets leave the warehouse throughout the day via the pick stations or the dispatch area (when full pallets are distributed).
All these operations are optimized by Easy WMS, the warehouse management system by Mecalux. This software rigorously monitors each product from the moment it arrives at the warehouse until its delivery to the end customer. This is vital, taking into account that the goods are medical materials. Easy WMS is also charged with organising and managing dispatches in order to streamline lorry loading and the subsequent distribution.
Intersurgical’s Group Supply Chain Manager enthuses, “We’re happy to say that, in a matter of very little time, we now have better control over all our logistics processes. This will be essential in the future as our business grows and we seek to maintain this centre as our main global distribution hub."
Martynas Tamosiunas - Group Supply Chain Manager at Intersurgical
“We chose Mecalux because its proposal was the most balanced in terms of cost–benefit. One decisive factor in our decision was Mecalux’s ability to provide us with a complete solution that included hardware and software and, at the same time, to manage the entire project from start to finish. For all these criteria, we thought Mecalux was the best qualified company. And we were absolutely right — the start-up went off without a hitch.”
Why install an automated warehouse?
Intersurgical has decided to build an automated installation to gain the following advantages:
- Productivity and availability. Automated warehouses do away with manual goods movements, eliminating any possibility of error. They can operate 24/7 without interruption.
- Real-time inventory control. The system identifies each product the moment it arrives at the warehouse and continuously monitors movements.
- Maximum use of space. The clad-rack warehouse stands 30 m tall and 121 m long to provide the maximum possible storage capacity.
- Optimum safety. The automated handling equipment transfers the goods in a safe and sterile manner.
- Cost reductions. Although the initial investment is more substantial than that of a traditional warehouse, the structural and operational maintenance costs are lower.
Order preparation and dispatch
Picking is one of the main operations of Intersurgical’s warehouse. Therefore, a specific area has been set up to facilitate and streamline this work. Orders are prepared according to the product-to-person principle, which reduces operator travel and increases speed.
On one side of the installation, there are three pick stations. There, goods are sent automatically from the warehouse, and up to 12 orders are prepared at the same time. At each station, four orders can be put together simultaneously.
Operators remove boxes from the pallets and distribute them among the other pallets located behind them (which will then be dispatched and delivered to customers). To maintain sequencing and prevent errors, the operators follow the orders issued by Easy WMS via a monitor.
When an order is closed, a transfer car picks it up and sends it to the stretch wrapper and labelling machine. Following that, the conveyors send the order to the dispatch zone.
This area consists of 30 live channels, each of which can house six pallets deep. These roller channels are slightly inclined so that pallets flow via gravity from the highest to the lowest point (which faces the docks).
Two transfer cars pick up the prepared orders pending dispatch and place them sequentially in the corresponding live channel. Thus, the pallets are grouped in each channel according to whether they correspond to the same order or delivery route. In addition, they are prepared to be subsequently loaded onto the distribution lorries, minimising wait times.
Stringent goods control
Traceability and good practices are fundamental in the healthcare sector and in the management of Intersurgical’s 2,000 SKUs of medical products. For this reason, Easy WMS must keep the goods under extremely strict control, from the time they arrive at the warehouse until they are sent to the customers.
“We’re really pleased with Easy WMS because it offers the capabilities we need from a warehouse management system and integrates perfectly with our ERP, EFACS", says Martynas Tamosiunas.
Easy WMS optimises goods movements to achieve higher productivity. When a pallet goes through the checkpoint, the WMS assigns it a location, taking into account its SKU and turnover. For example, “A” items (those in greater demand and which represent 12% of the total pallets stored) are distributed at the front of the aisles to streamline their entry and exit.
Besides traceability, Easy WMS executes such precise control of the stock that it dispatches the goods sequentially. Sequencing the orders and grouping them in advance in the preload channels helps to save time and minimise errors during distribution.
Constant transformation
“Demand for our products has increased dramatically during the COVID-19 pandemic,” affirms Martynas Tamosiunas. Thanks to the new automated installation and the controlled, enhanced operations, Intersurgical was able to absorb a 50% increase in warehouse inflows and outflows.
As the company manages healthcare products, lack of contamination is a priority. In this vein, automation is especially advantageous because it prevents operators from having to handle the products manually. Likewise, traceability is a must for this warehouse. The WMS monitors the goods from the time they arrive from production to their subsequent dispatch. As a result, Intersurgical knows all the movements that each pallet has made.
Lastly, Intersurgical’s Group Supply Chain Manager declares, “We’re more than satisfied with all the processes implemented in our new warehouse. Of course, we’ll look to further improve certain aspects in the future because that’s our work philosophy. But so far, all processes are working as planned and expected.”
Advantages for Intersurgical
- Sustained increase in productivity: Inflows and outflows at Intersurgical’s automated warehouse have increased twofold following the start of the pandemic. The company was able to provide high-quality, error-free service, thanks to its high-tech logistics systems.
- Centralised logistics: the firm has brought together in one logistics centre all the goods that, previously, had been distributed among various installations. This has enabled the firm to cut costs and organise its entire distribution network from a single warehouse.
- Goods control: the automated installation and supervision from Easy WMS enable real-time goods sequencing and traceability, which is essential when managing products for operating theatres and hospitals.
Automated warehouse | |
---|---|
Storage capacity: | 50,400 pallets |
Pallet sizes: | 800 x 1,200 mm |
Max. pallet weight: | 500 kg |
Warehouse height: | 30 m |
Warehouse length: | 121 m |
Gallery
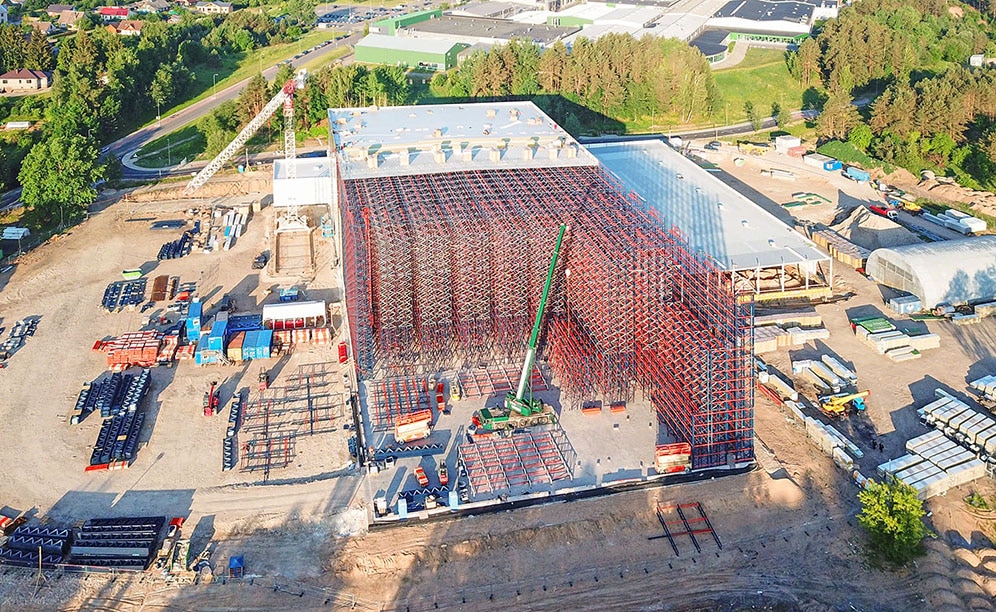
Intersurgical's automated clad-rack warehouse in Lithuania
Ask an expert