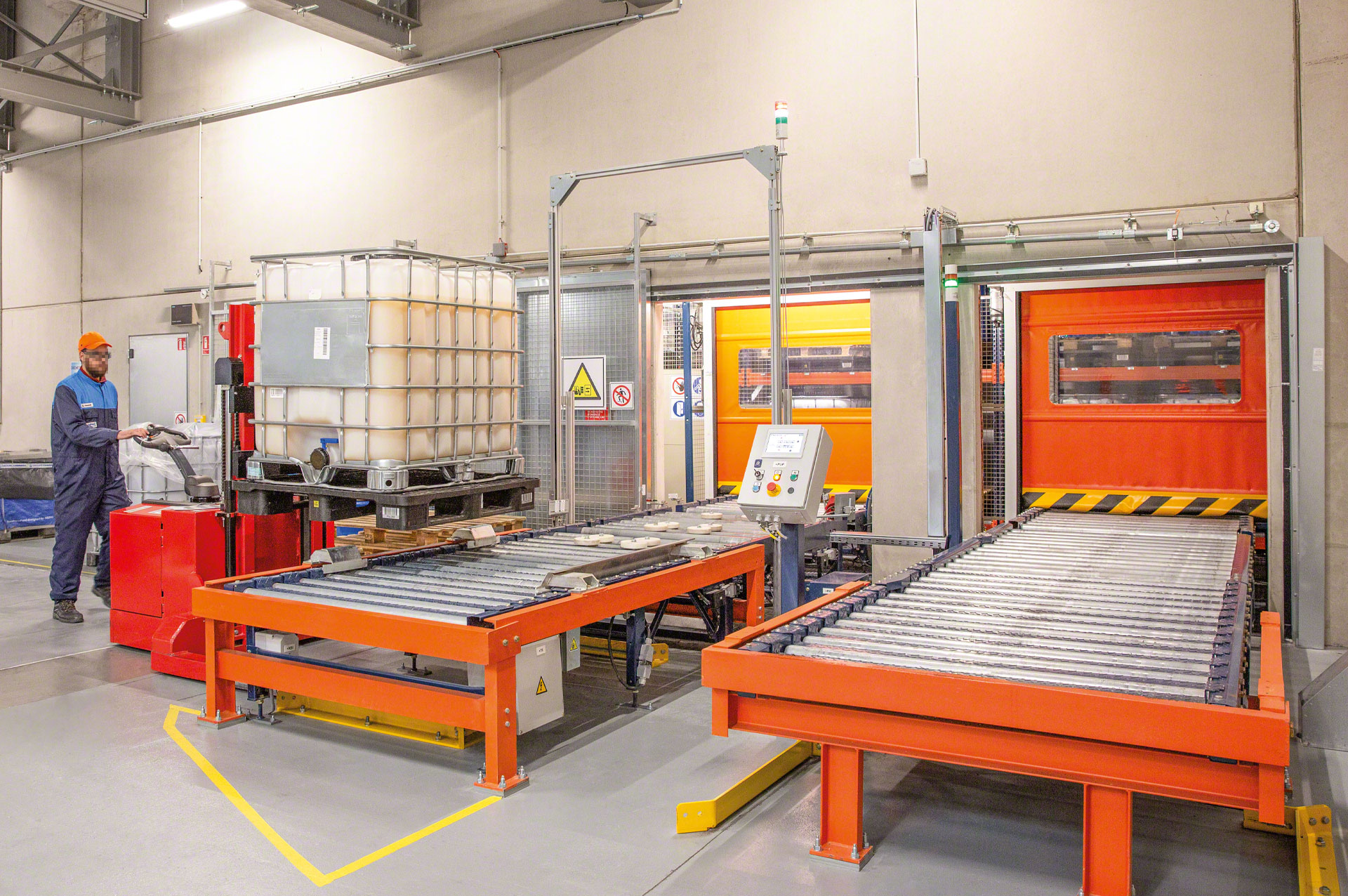
Automated warehouse with Nippon Paint’s automotive paint
Nippon Paint automates its facility to support the annual production of 3,000 tonnes of automotive paint.
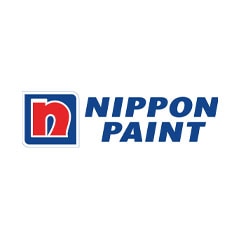
Nippon Paint, a manufacturer of automotive paint, automates its warehouse to support the production of 3,000 tonnes of paint a year. Easy WMS provides strict control of all SKUs in stock and of entries and exits of raw materials in the AS/RS.
Nippon Paint: over 100 years of experience
Nippon Paint is a global leader in the paint and coatings industry, providing innovative solutions for over 140 years. Specializing in the production and sale of paint for the automotive sector, the company has subsidiaries in Asia, Europe and North America. Nippon Paint’s products are used by 75% of vehicle manufacturers.
- Founded in: 1881
- No. of employees: 30,000 worldwide
CHALLENGES
|
SOLUTIONS
|
BENEFITS
|
---|
The automotive paint manufacturer and distributor Nippon Paint has bolstered its presence in Europe. It has opened a modern facility in Plessis-Pâté (France), where it has centralised its production and storage operations. Located just 25 km from Paris, Nippon Paint’s manufacturing plant is equipped with the latest technologies and robotic equipment to produce 3,000 tonnes of paint a year.
“Our main logistics need was to consolidate our business and bring all our goods located in several buildings all under one roof,” says Francis Lepême, Production and Project Manager at Nippon Paint. Logistics is critical to sustaining a high production rate like Nippon Paint’s. The company knew that to centralise its supply chain, it would have to invest in an automated storage and retrieval system (AS/RS) to ensure continuous product flows and maximise the available space to accommodate all raw materials.
“Automating our logistics processes was a strategic initiative to guarantee the smooth operation of the production lines. In the past, we stored our raw materials with manual equipment and managed the warehouse with pen and paper,” says Lepême.
Determined to incorporate the most recent technological advances in its processes, Nippon Paint installed an AS/RS from Mecalux to streamline the storage and supply of raw materials to the production lines. “The experience, the price, and the maintenance contract all contributed to our decision to choose Mecalux as our storage system supplier. Moreover, we had the chance to visit other facilities in operation, which helped us make our decision,” says Lepême.
Nippon Paint has also deployed Mecalux’s Easy WMS warehouse management software to strictly control all its stock. The program monitors the raw materials entering and exiting the storage system and keeps a real-time record of the status of the goods.
“Of all the advantages of Mecalux’s Easy WMS software, one of the most important is its integration with our ERP system: this has optimised communication between the warehouse and the production area,” says Lepême. For instance, the minute one of the production lines needs raw material, the ERP notifies Easy WMS, which arranges for the product to be picked as soon as possible.
Lastly, the business also installed adjustable pallet racking — a robust yet versatile storage system — to house finished products and the raw materials used in the manufacturing process.
Automatic raw material storage
“The AS/RS has more than met our expectations. It’s given us numerous benefits, including error-free FIFO stock management. We were also surprised by the automated solution’s fast response time between the receipt of a manufacturing request and the arrival of the raw material on the production lines,” says Lepême.
Nippon Paint’s AS/RS is made up of a single 40-metre-long aisle with a storage capacity for 384 pallets. Raw materials are stored in drums and intermediate bulk containers. These are deposited on pallets and have a capacity of up to 1,300 kg.
A stacker crane operates in the aisle of the AS/RS, moving goods from the entry points to the locations assigned by Easy WMS. The storage aisle was adapted to the dimensions of the warehouse. It spans almost the entire length of the building, leveraging all available surface area.
One particular characteristic of Nippon Paint’s facility is the integration between the storage zone and the different manufacturing processes. The AS/RS features goods infeed/outfeed stations at two different heights: floor level in the front and at 5.2 m on the side of the racking. The infeed station’s automatic conveyors provide a continuous, safe flow of raw material in supplying the paint production areas.
Warehouse under control
Concentrating all activity in a single aisle calls for goods distribution criteria designed to avoid mistakes. Easy WMS plays a key role when it comes to organising stock, determining the optimal location for each pallet based on rules and advanced algorithms.
“Easy WMS communicates with our ERP system to know in advance which pallets the AS/RS will receive from Europe, the US, and Asia,” says Lepême. This way, using RF scanners, operators merely have to place the pallets on the corresponding inbound conveyor. During the goods receipt process, all pallets must cross a checkpoint, where their dimensions are verified. If the measurements fall within the margins established, the WMS software assigns them a location in the AS/RS.
Traceability is vital in Nippon Paint’s facility. All items are identified by a barcode, so Easy WMS can rigorously monitor the 150 available SKUs. Knowing the status of the goods in real time helps the company minimise errors and handle any situation effectively.
The supply process begins when the ERP system notifies Easy WMS of the raw materials required on the different paint production lines. Regardless of their destination, the Mecalux software dispatches the goods following the FIFO (first in, first out) method.
Pallet racking with direct access
“We’re really happy with the pallet racks, especially because they’re so easy to use. Plus, we can store plastic pallets on them, which are much more hygienic than wooden ones,” says Lepême.
The racking stands 6.5 m tall and has a capacity for 448 pallets in two storage aisles. Nippon Paint opted for this storage system because it offers direct access to products, making goods management and order picking extremely agile. The pallet racks also facilitate inventory control, as each location is allocated to a single SKU.
Integration of logistics and manufacturing
With its new AS/RS, Nippon Paint can manage in a single aisle the raw materials required by the production lines, which manufacture 3,000 tonnes of paint a year. Together with automated operations, Easy WMS has provided control and traceability through digitalised management. And these are essential for ensuring the safety and quality of the company’s stock stored.
Thanks to automation and technology, Nippon Paint has an efficient, optimised supply chain. Its new centre in Plessis-Pâté has been equipped with a personalised solution that meets the business’s requirements. This has given Nippon Paint a competitive edge, boosted its productivity, and enhanced the quality of its customer service.
We chose Mecalux because of its experience and professionalism. We also had the chance to visit other facilities in operation. All of this played a part, in addition to the solution being efficient on a technical and economic level. The stacker crane brings many benefits, including reductions in operating costs, manufacturing time, and human errors. Another plus point was the synergy between both companies during the design phase.
Gallery
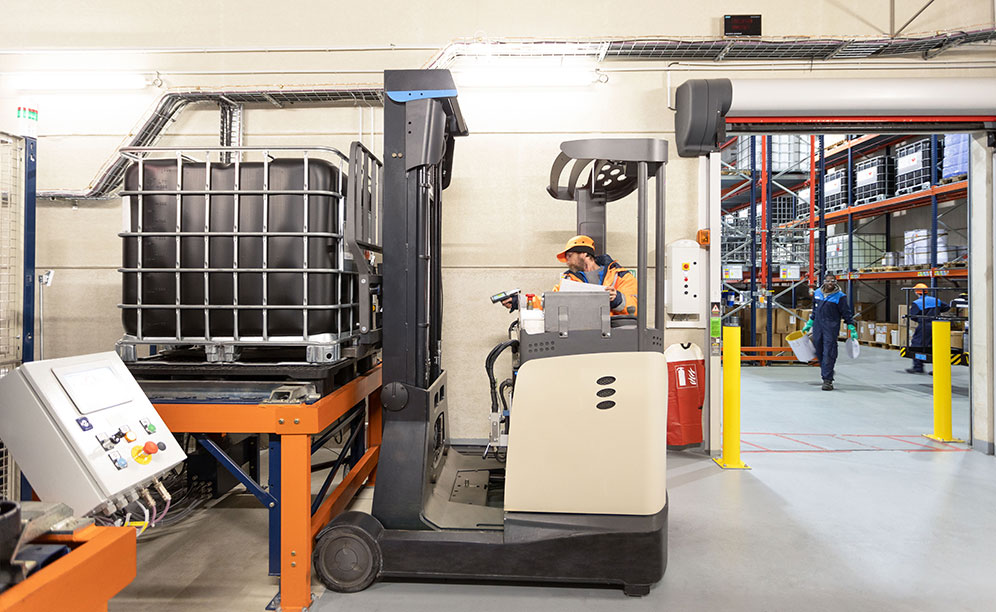
Nippon Paint installed an AS/RS in its logistics centre in France
Ask an expert