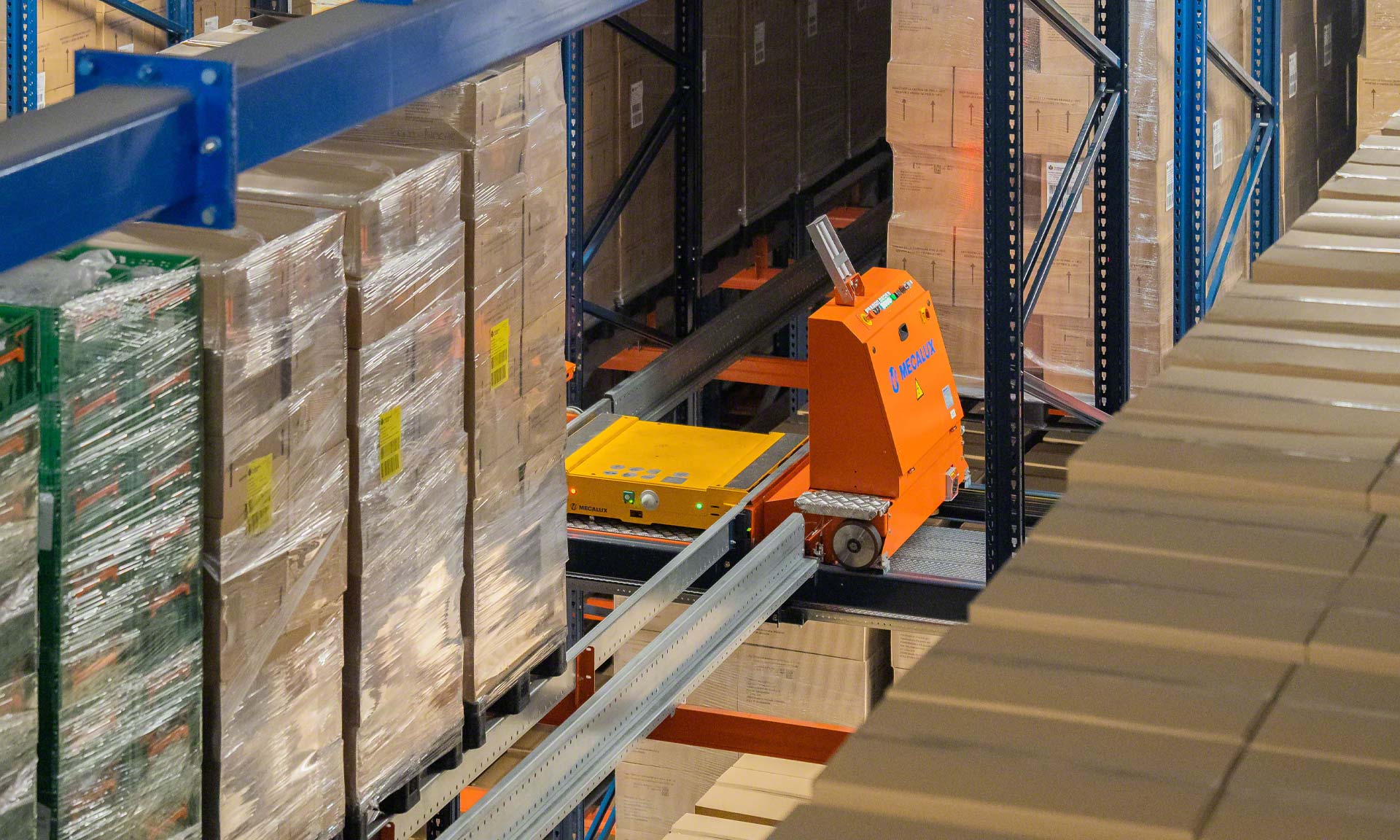
Panificadora de Alcalá automates logistics processes to make over 1 M product units a day
Panificadora de Alcalá’s logistics centre produces more than 1 million product units daily.
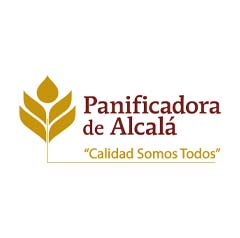
Bread manufacturer Panificadora de Alcalá has a modern logistics centre outfitted with the latest storage and traceability control technology. The logistics centre consists of Mecalux’s semi-automated and automated Pallet Shuttle systems with transfer cars, as well as its Easy WMS software.
Panificadora de Alcalá: commitment to quality
Panificadora de Alcalá is a company devoted to the manufacture of bread and bread-derived products. The company integrates cutting-edge technologies in its manufacturing and logistics processes to ensure high-quality, low-cost products and maximum food safety. Since 2006, it has been a supplier of Spanish supermarket chain Mercadona.
- Founded in: 1955
- Production: 1 million-plus product units/day
CHALLENGES
|
SOLUTIONS
|
BENEFITS
|
---|
In the food industry, the application of strict quality and safety standards makes the logistics operations of companies like Panificadora de Alcalá more demanding. This renowned bread manufacturer — and supplier of Spain’s Mercadona supermarket chain — has a modern logistics centre in Alcalá de Henares. Every day, the facility produces over 1 million units of product.
“Our logistics centre’s most important goal is to make sure that the flow of goods doesn’t halt the manufacturing process. We also devote a lot of resources to traceability for quality and food safety. We need to keep tight control of the movements of the raw materials arriving at the warehouse and of the finished products that make their way to our customers’ tables. Cleanliness is another essential requirement for the logistics processes performed in our facilities: the protocol for cleaning and access to the production lines is the same as in the warehouse,” says Joaquín Frutos, Head of Logistics and Procurement at Panificadora de Alcalá.
Equipped with the latest technology, Panificadora de Alcalá’s logistics centre has been modernised over the years as a result of the steady increase in manufacturing activity. “Before, we didn’t have all this technology. We used to store the goods on pallet racking and at floor level in the facility. All processes were manual,” says Frutos.
The business knew automation was a must for taking on the major challenges of food logistics: traceability of perishable products, uninterrupted flow of goods and optimisation of costs linked to temperature control in the warehouse. “We decided to automate our logistics operations to ramp up the number of entry and exit movements, optimise the surface area allocated to storage to gain more manufacturing space, and eliminate errors. Our reason for automating was to ensure that our logistics operations could support the activity of our production lines,” says Frutos.
After weighing several options, the company decided to equip its new freezer warehouse with the Pallet Shuttle system with transfer cars from Mecalux. This solution is one of the most efficient high-density storage systems on the market. The business has swapped the forklifts used with the semi-automated version of the Pallet Shuttle for fully autonomous handling equipment — a transfer car on each level — to move the pallets to the storage channels.
The automated solution, which guarantees a high flow of incoming and outgoing goods, is the backbone of a logistics chain that also includes two facilities with the semi-automated Pallet Shuttle storage system as well as one with drive-in racking. “The automated and semi-automated Pallet Shuttle systems store our finished products, while the drive-in racking houses our raw materials and supplies. The Pallet Shuttle system operates in two freezer warehouses with finished products and in another facility at ambient temperature, where we keep items such as breadcrumbs and croutons,” says Frutos.
Panificadora de Alcalá has implemented the Easy WMS warehouse management system from Mecalux in all its facilities to gain full traceability of stock, from goods receipt to customer deliveries. “Even though we have different warehouses with separate stock, Mecalux’s Easy WMS makes it possible for them to share the item master, customers, characteristics, configurations and users. Each facility has its own stock, inbound materials and operations, but they’re managed jointly.”
Automated logistics: capacity and throughput
“The automated Pallet Shuttle from Mecalux has enhanced our speed and safety in goods handling, leveraged space and brought down our error rate,” says Frutos.
With a capacity for more than 4,100 pallets, the system consists of two 45-metre-long racking units with five storage levels. On each level, a transfer car positions the motorised shuttle at the entrance to the storage channel assigned by Easy WMS. With a maximum of 19 pallets deep, the shuttle moves inside the channels, inserting or removing the goods. The warehouse operates at a constant temperature of -20 °C to guarantee that the food is stored properly and preserve its properties for a long time.
The cycles per hour performed by the Pallet Shuttle system with transfer cars are multiplied by the number of levels in the facility, five in this case. Mecalux also installed a lift to connect the levels and move the goods to the corresponding one. Besides throughput, another advantage of the automated Pallet Shuttle is that it makes the most of the available space to increase storage capacity. Likewise, this high-density system notably reduces the energy used to generate cold air since the air is distributed among a larger number of pallets stored.
The automated warehouse is connected to the production lines by conveyor. It is also linked to Panificadora de Alcalá’s freezer store that was already up and running with the semi-automated Pallet Shuttle system. This storage solution comprises a motorised shuttle that moves inside the storage channels, inserting and removing pallets from their locations with full autonomy.
Benefits of the automated Pallet Shuttle
- Increase in the number of cycles per hour compared to other storage systems.
- Elimination of errors resulting from manual management.
- Rapid movement of the electric shuttle car, reducing goods-in/goods-out times.
- Maximum space savings by compacting materials on the racks. The racking can measure over 40 m tall and have storage channels up to 45 m in depth.
- Energy savings: the electric shuttle’s supercapacitors charge automatically onboard the transfer car.
- System that allows for different configurations depending on the number of SKUs, pallets and movements required in each case.
- Optimal stock control and perpetual inventory via Easy WMS warehouse management software.
Easy WMS: traceability as a priority
“With digitalisation, everything’s an advantage. Digitalising our logistics operations allows us to be more exhaustive in our work. Knowing the exact minute each production batch is manufactured, a pallet is moved, and the goods are loaded and unloaded from the trucks gives us great reassurance. The implementation of Easy WMS has given us total control over stock through traceability. Plus, it’s minimised errors and enabled us to make better use of space,” says Frutos.
To ensure this traceability, goods leaving production arrive stretch-wrapped and labelled at the pallet checkpoint. There, Easy WMS identifies them before they enter the warehouse. This checkpoint also verifies whether the pallets meet the requirements for storage on the racks.
Once the pallets from production are identified, Easy WMS makes a series of calculations taking into account the number of empty locations, the SKU and the demand level to assign each item the ideal slot. For example, top-selling products are placed near the lift to streamline their entry and exit. “Every day, we move 1,200 pallets: we receive around 600 containing finished products from the production lines and ship another 600 to customers in Spain and internationally,” says Frutos.
“Easy WMS software is extremely flexible and user-friendly. Very few programs on the market offer operators such flexibility. I’ve been working in the logistics industry for many years, and I’d never worked with such a flexible system when it comes to making split decisions. Easy WMS is a powerful tool that can come to the rescue in difficult situations,” says Frutos.
Software to control the Pallet Shuttle
Panificadora de Alcalá has also installed the WMS & Pallet Shuttle Integration module. This software program is designed to simplify the tasks of the operators who work in the area home to the semi-automated Pallet Shuttle system.
Using a tablet connected to Easy WMS, operators control the movement of the motor-driven shuttle. With this device, they can enter the items that need to be stored or retrieved, count the number of pallets in each channel and direct the goods to be compacted.
“We’re thrilled with the WMS & Pallet Shuttle Integration module. From a single screen, users can monitor the stock and all the movements of the motorised shuttle car. The interface used to control the system is really intuitive and reliable. This module saves us a lot of time in handling pallets and lets us make better use of our resources,” says Frutos.
Quality and customer satisfaction
““In terms of the future, we plan on continuing to grow to offer a quality product through excellent service. Logistics is key for reaching that goal because any mistake could jeopardise our performance,” says Frutos.
The success enjoyed by Panificadora de Alcalá over the past few years lies in its commitment to customer satisfaction. Its top priorities are to guarantee the quality of the food it sells and to make on-time deliveries. Thanks to the automation and digitalisation enabled by Mecalux, the company’s logistics operations meet the safety and efficiency its customers demand.
Our logistics centre’s most important goal is to make sure that the flow of goods doesn’t halt the manufacturing process. The automated warehouse operates 24/7 at sub-zero temps, stopping only twice a year. The automated Pallet Shuttle from Mecalux has enhanced our speed and safety in goods handling, leveraged space and minimised our error rate.
Gallery
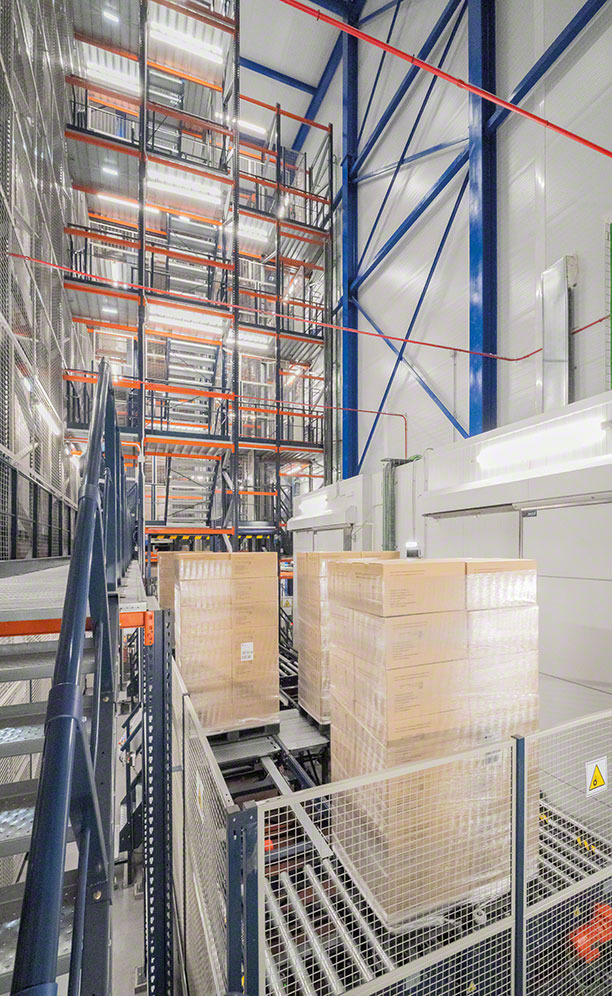
Panificadora de Alcalá’s logistics centre in Alcalá de Henares, Spain
Ask an expert