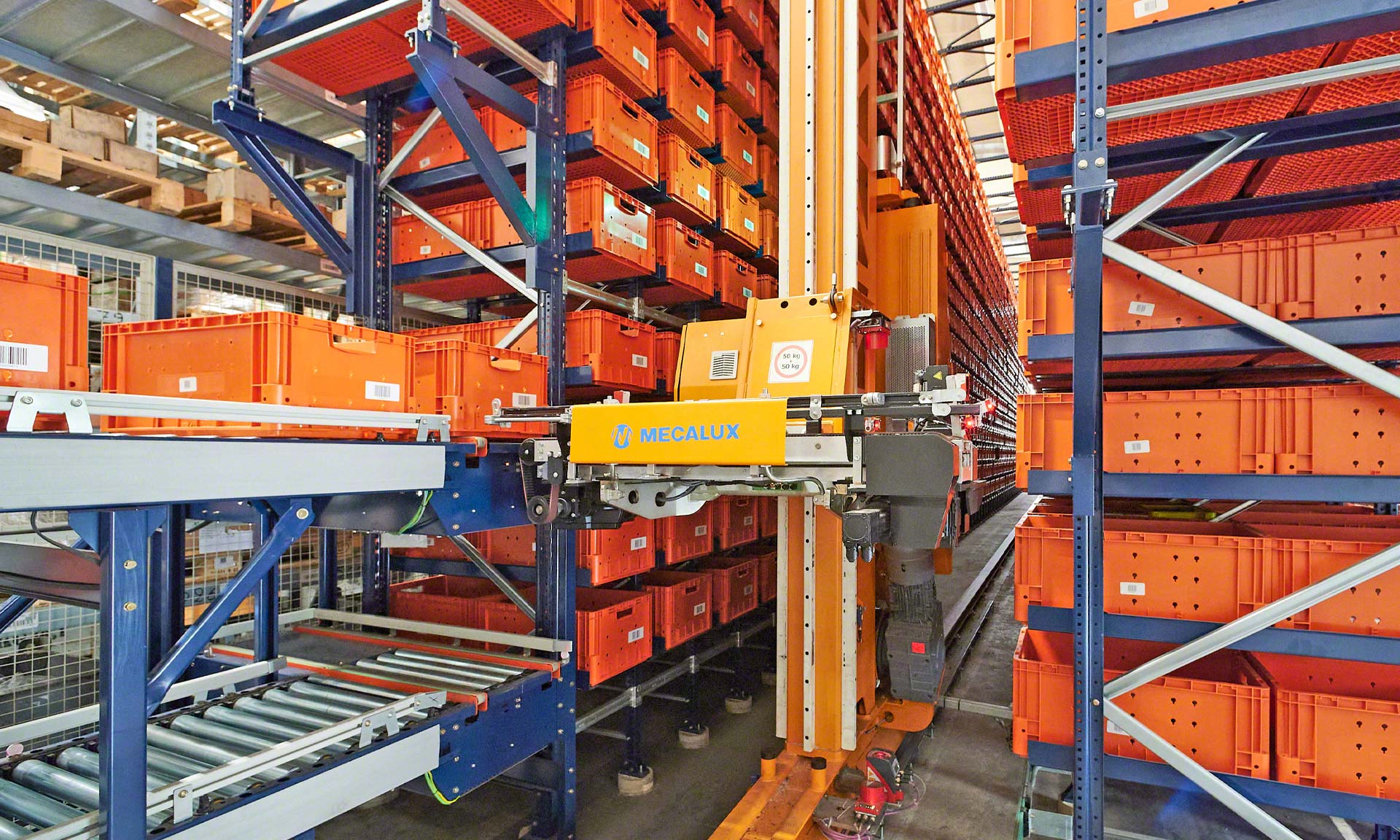
Screw and fastener distributor ICF revamps its logistics operations
ICF, a screw and fastener distributor, has modernised its logistics operations with a mini-load system, conveyors and Easy WMS warehouse management software.
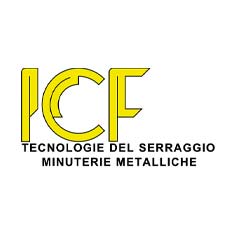
Screw and fastener distributor ICF has modernised its distribution centre in Varese, Italy, with an all-in-one logistics solution. Mecalux has installed a mini-load system, conveyors and Easy WMS warehouse management software.
Founded in 1990, ICF specialises in the manufacture and sale of screws and fasteners produced by three different methods: cold forging, hot forging and mechanical processing.
- Founded in: 1990
- No. of employees: 25
CHALLENGES
|
SOLUTIONS
|
BENEFITS
|
---|
Managing over 1,500 stock-keeping units (SKUs) of different sizes and turnovers calls for logistics operations that are organised as well as efficient. Screw and fastener distributor ICF has transformed its logistics centre in Varese, Italy, with a mini-load AS/RS, conveyors and Easy WMS warehouse management software from Mecalux.
“When we decided to install the automated storage system, our main logistics needs were to speed up order picking and shipping and to expand our warehousing space,” says Andrea Boeri, IT Manager at ICF.
Before making this technological leap, the company stored its finished products on pallet racking. As the business expanded and the production rate became more intense, this storage system was no longer effective: it was impossible to continue managing all the goods manually.
ICF’s investment in automation marked a before and after for the company’s logistics processes. “We chose a mini-load system because it’s the perfect solution for maximizing productivity in a limited space and dispatching orders more quickly and without errors,” says Boeri.
“We use the mini-load AS/RS to store finished and semi-finished products, standard and special screws, and small parts packed in boxes or bags,” says Boeri. Thanks to this comprehensive solution, Boeri adds that ICF “has ramped up its operational throughput. We’re now dispatching up to 300 boxes a day flawlessly.”
In addition to optimising ICF’s warehousing capacity, this new storage system enables the business to group in the same zone all the operations necessary for managing small goods (receiving, order picking and shipping).
Besides the AS/RS and conveyors for boxes, ICF implemented Mecalux’s EasyWMS warehouse management software. Through direct, two-way communication with ICF’s enterprise resource planning (ERP) system, the program monitors stock and provides total traceability of all products in the mini-load system. “Easy WMS optimises our box storage and retrieval operations while streamlining order picking,” says Boeri.
Automated logistics operations
One particular feature of this mini-load system that really impressed ICF was its ability to leverage the available surface area to accommodate a larger number of goods: nearly 4,000 boxes are stored in just over 130 m².
With a height of 7.5 m, the AS/RS consists of a single 36.5-metre-long aisle with double-deep racking served by a stacker crane for boxes. Equipped with telescopic forks, the stacker crane can simultaneously transport up to two 50-kilo boxes, dispatching a total of 300 boxes a day.
Mecalux’s Easy WMS warehouse management software orchestrates operations and the movement of boxes in the mini-load AS/RS: it organises product inflows/outflows and controls order picking.
Picking is performed in line with the goods-to-person method. For this purpose, the front of the warehouse was outfitted with a pick station. Operators remain there as products are brought to them automatically. Easy WMS sends orders to the stacker cranes and conveyors, which execute the relevant movements to transfer the materials to the pick stations.
Behind the mini-load system, Mecalux installed a 25-metre-long two-way box conveyor to connect the manual storage zone with the AS/RS. This area also includes a pick station with computers and RF scanners to help operators sort products and fulfill orders.
Easy WMS directs this operation to enable workers to process a larger number of orders in the shortest possible time. The WMS tells them which and how many items they require to put together each order. By following these instructions, the risk of error is practically nil.
The Easy WMS warehouse management software strictly controls all goods, thanks to its permanent two-way connection with ICF’s ERP system. For every product that arrives at the mini-load AS/RS, the Mecalux software receives an advance shipping notice (ASN) from the ERP system. Based on this message, Easy WMS uses a set of rules and algorithms to assign the items a location according to their characteristics and turnover. The 1,500 SKUs stored in the mini-load system are fully traceable. ICF knows the location of all its products in real time and can precisely track all goods movements through Easy WMS.
Advantages of the mini-load system
- High productivity and availability. Automation minimises errors and reduces the number of goods movements made in the warehouse.
- Accessibility to stored products. The stacker cranes and conveyors store and move the materials in an agile, accurate and safe way.
- Speed in order picking and dispatch tasks. The goods-to-person method cuts picking times considerably.
- Space cost-effectiveness. The racking makes the most of all the surface area to provide the highest storage capacity and the greatest throughput.
Modern, high-tech logistics
Thanks to an all-in-one warehousing solution, ICF has revamped its logistics centre with two main goals: to optimise the storage of 1,500 SKUs and boost the throughput of its operations, especially order picking.
All product movements are coordinated by Mecalux’s Easy WMS warehouse management software, and inventory is always up-to-date. Expediting order picking, ramping up productivity and leveraging space were decisive for achieving the logistics efficiency required by ICF’s customers.
We incorporated a mini-load system in our centre to maximise the use of the available space, applying the goods-to-person concept. We also wanted to eliminate mistakes due to manual management to enhance the quality of our customer service.
Gallery
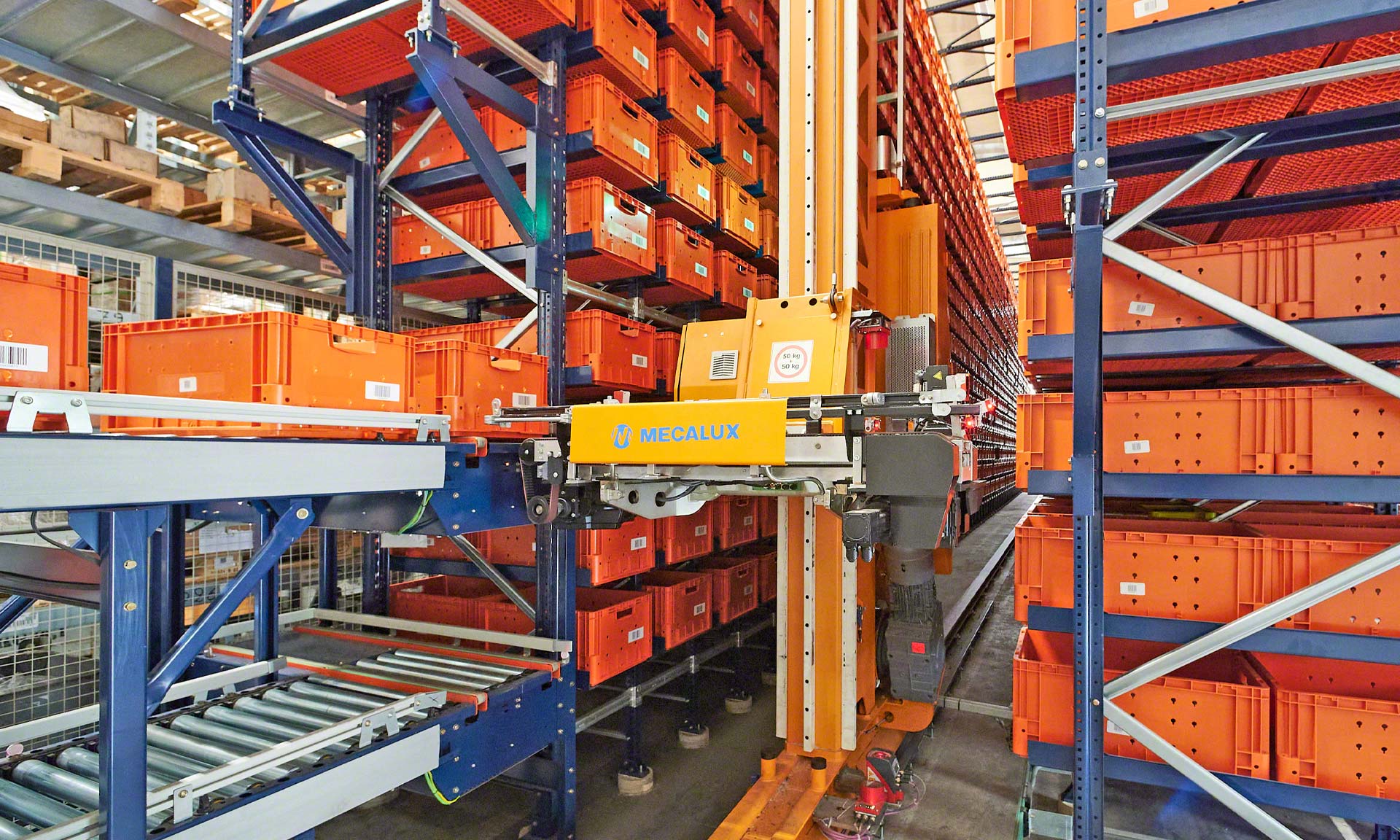
Automated warehouse of screw distributor ICF in Varese, Italy
Ask an expert