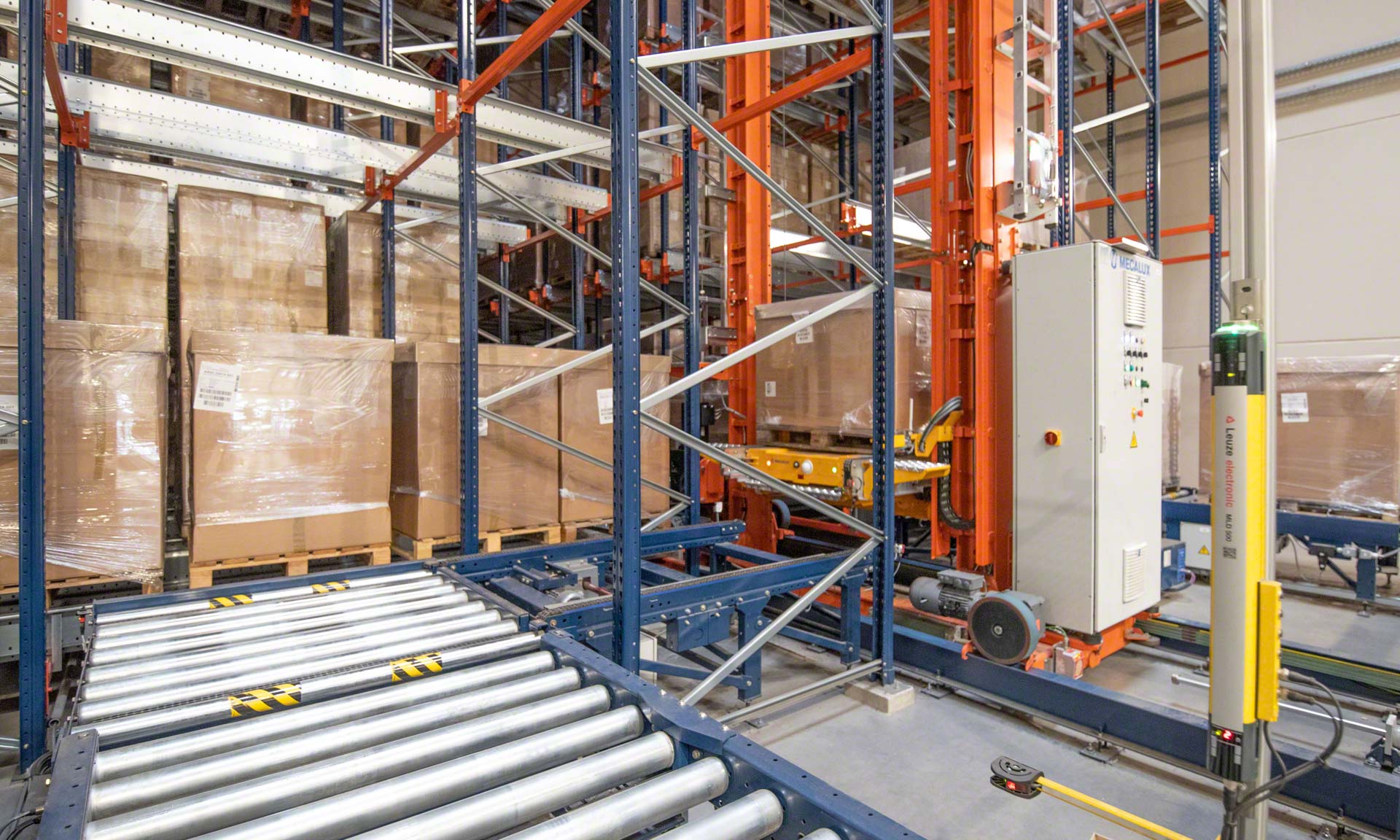
Thermoforming ideas in step with automation
Automated logistics: the solution for producing 2 million pieces of packaging a day
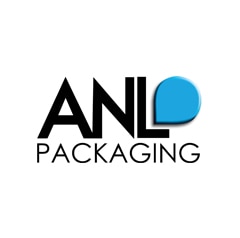
To produce two million thermoformed plastic containers a day, automation is a must. With the aim of expediting production, plastic packaging company ANL Packaging has opened an automated warehouse in the South of France equipped with the Pallet Shuttle system, capable of moving around 600 pallets a day. Precision, safety, and speed characterise this facility, supervised by the Easy WMS warehouse management system from Mecalux.
Founded in Wellen, Belgium, in 1938, ANL Packaging designs and manufactures thermoformed plastic containers for companies in all sectors. Thermoforming is a process in which a plastic sheet is heated and then shaped by means of moulds.
In its three production plants in Belgium, France and Poland, respectively, ANL Packaging manufactures a billion trays per year. The sustainable and environmentally committed production process meets exacting standards of protection, design, quality and durability.
Automated solution for growing demand
In Cahors, South West France, ANL Packaging’s 9,800 m² production centre runs non-stop: it produces two million containers a day, which are distributed to hundreds of companies in Europe. Since opening in 1991, the facility has been expanded and modernised, incorporating technologies that ensure the safety and productivity of its processes.
“Our company is strongly committed to innovation, so we make sure we update our processes regularly to increase our throughput,” says Filip Mertens, Managing Director at ANL Packaging France. A large part of the operations in the production centre are automated to eliminate errors, perform tasks more quickly and reduce costs.
Recently, ANL Packaging has added on to its centre in Cahors with the construction of a new, 2,000 m² automated warehouse used to store finished products as they come off the production lines. Every day, around 360 pallets are received, and 240 are distributed in 10 lorries to hundreds of businesses in Europe.
In the past, all items were deposited in an old warehouse, where they were stacked directly on the floor. However, the increase in the production pace rendered this method unfeasible. “We needed to optimise the space to be more efficient, accommodate more products and reduce forklift traffic inside the warehouse,” says Filip Mertens.
In light of these needs, the company contacted Mecalux to come up with a solution: the installation of the automated Pallet Shuttle system served by a stacker crane. The main advantage of this automated solution is that the racks maximise the warehouse surface area to boost the storage capacity. Moreover, by having fully automated operations, the company can monitor goods inflows and outflows more accurately and do away with mistakes in order prep.
The warehouse is made up of a single 65-metre-long aisle with racking on both sides. The racks measure 10.5 m high and have 4 levels. They can store five pallets deep on one side of the aisle and 15 on the other, with a maximum storage capacity of 3,160 pallets.
The company has also implemented the Easy WMS warehouse management system, charged with distributing the goods in their locations while taking into account their SKU, characteristics and turnover. “Easy WMS allows us to know the exact location of the products and monitor traceability in real time,” says Mertens.
Automated Pallet Shuttle: How does it work?
The Pallet Shuttle is a compact storage system made up of a motorised shuttle that autonomously inserts and removes the pallets from their locations. ANL Packaging’s solution is fully automated, requiring no operators: a stacker crane transports the shuttle and the goods to the location assigned by the Easy WMS software.
ANL Packaging’s facility stands out for its simplicity: product entries and exits are carried out with minimal operator intervention. The workers pick the products up from the production lines using a forklift and place them on a conveyor leading to the warehouse.
Once there, they are automatically moved to a checkpoint where their gauge, weight and dimensions are checked. Barcodes are also read here so that Easy WMS can identify each item and assign it a location. The software applies rules and algorithms to decide on the ideal slot for each product.Advantages of the automated Pallet Shuttle system
The automated Pallet Shuttle is an automated storage system that ramps up the productivity of any logistics facility.
- Surface area optimisation: the racks take up the largest available surface area to provide the maximum storage capacity (in the case of ANL Packaging, this accounts for 3,160 pallets in just 1,235 m²).
- High availability: the electric shuttle is equipped with supercapacitors that are charged automatically while on board the stacker crane cradle. Thus, the shuttle is always ready to go.
- Increased productivity: the automatic movement of the goods greatly enhances the company’s throughput. All product management is carried out with minimal operator intervention, eliminating errors.
- Cost reductions: automation cuts costs in terms of traditional handling equipment, warehouse surface area, staff and energy.
- Perpetual inventory: the software orchestrates all goods movements and takes inventory in real time.
Success story
ANL Packaging has achieved success as a result of the transformation and modernisation of its business. “The incorporation of technology has helped to drive and optimise our processes, from the production of the thermoformed plastic packaging to its storage and distribution,” says Mertens.
Logistics is the cornerstone of this company. On the one hand, it supports the daily production of two million products. On the other, it ensures the preparation and distribution of orders to the firm’s extensive European customer network.
Integrating the automated Pallet Shuttle system into its logistics process has enabled ANL Packaging to accommodate a large number of products in its warehouse, streamlining goods entries and exits to likewise speed up distribution. The Easy WMS warehouse management system has provided the company with absolute control over its products and over all movements in the facility.
With this comprehensive logistics solution, ANL Packaging now has an efficient, optimised supply chain capable of producing two million thermoformed plastic trays a day.
We’re extremely pleased with the automated storage system from Mecalux. We’ve not only streamlined our movement flows, but also made the most of our storage space. With this modern warehouse, we can easily cope with the high production rate our business requires.
Advantages for ANL Packaging
- Resource optimisation: the automated Pallet Shuttle system saves space, time and personnel costs in the warehouse. Furthermore, goods are moved quickly and safely.
- Movement of 600 pallets/day: the Pallet Shuttle system with stacker cranes guarantees that the merchandise is deposited and removed at the right time.
- Improved product organisation: ANL Packaging has gone from storing products on the floor to housing them in this new warehouse that leverages all the available space to accommodate more goods.
Automated Pallet Shuttle system | |
---|---|
Storage capacity: | 3,160 pallets |
Pallet size: | 800 x 1,200 mm |
Max. pallet weight: | 500 kg |
Racking height: | 10.5 m |
Racking length: | 65 m |
Gallery
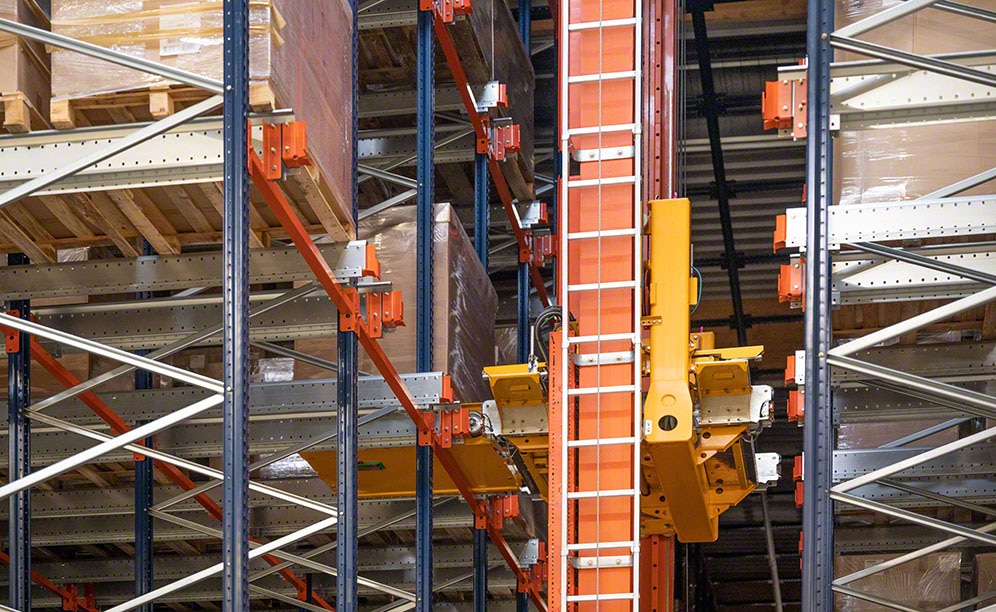
Automated Pallet Shuttle with stacker crane at ANL Packaging
Ask an expert