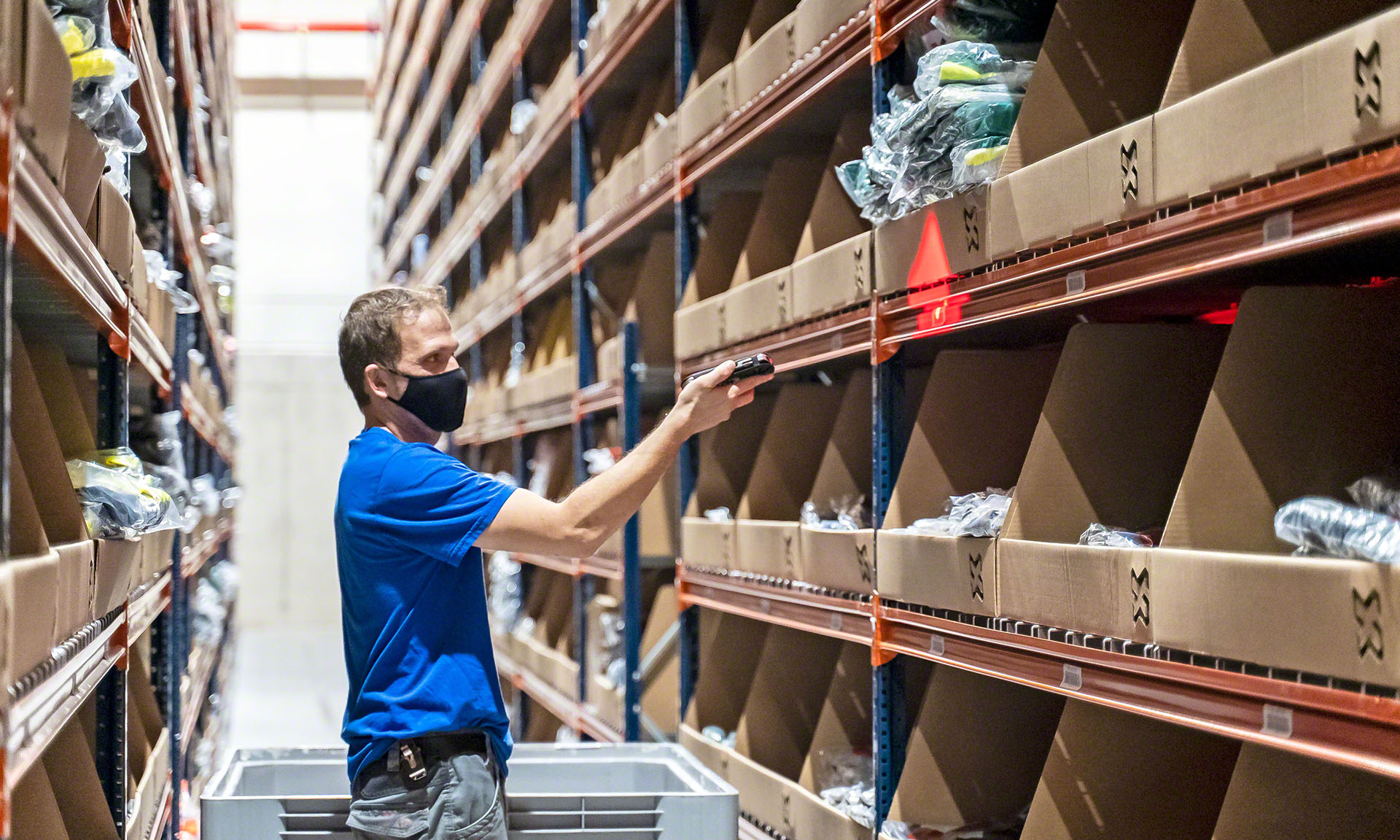
Würth Modyf: warehouse adorned with innovation
Würth Modyf adapts its logistics to omnichannel with the Easy WMS warehouse management system from Mecalux
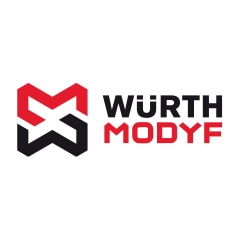
Würth Modyf, a Spanish company specialising in workwear, corporate uniforms and safety footwear, has renovated its supply chain. The business has moved to a new facility in Polinyà, Barcelona, equipped with the Easy WMS warehouse management system from Mecalux.
Würth Modyf: the workwear shop
Würth Modyf is a company specialising in workwear, corporate uniforms and safety footwear for all types of professionals. The organisation, which forms part of the Würth Group, a multinational tool and fastener manufacturer, works according to a B2B (business-to-business) business model and supplies companies in a number of European countries.
- Employees: +200
- Products in stock: +430
- Customers: +255,000
- International presence: Germany, Austria, Belgium, France, Spain, Netherlands, Italy, Norway, Portugal and Switzerland, among others
THE CHALLENGE
|
THE SOLUTIONS
|
THE BENEFITS
|
---|
Würth Modyf, a company specialising in workwear, corporate uniforms and protective footwear, has experienced unprecedented growth in recent years. “Between 2015 and 2020, we went from a turnover of €3 million to over €20 million,” says Juan Martínez, the business’s Operations Manager.
This increase in revenue of over 550% compelled Würth Modyf to transform its supply chain operations: “We needed more storage capacity and a new way of working that would give us more control over our stock,” says Martínez.
So, how was Würth Modyf able to boost its growth and prepare over 1,500 orders a day during its peak season? Firstly, by moving to a new, 8,000 m² warehouse in Polinyà (about 20 km from Barcelona). Secondly, by implementing the Mecalux Easy WMS warehouse management system to eliminate errors and ensure tight control over all logistics processes.
Würth Modyf has also installed three additional Easy WMS modules that make it possible to add new functionalities to adapt to business changes: Supply Chain Analytics Software, Labor Management System and Multi Carrier Shipping Software.
Würth Modyf’s warehouse is omnichannel: it supplies the company’s flagship store in Sant Boi de Llobregat (Spain) as well as businesses that purchase work clothes and footwear for their employees via the website.
Modern logistics operations
The pace of work in the Würth Modyf warehouse is frenetic. Every day, it receives a high volume of materials. At the height of the season, workers can prepare and dispatch over 1,500 orders a day, many of them with more than 10 lines each. “Our peak workloads are very high. April, May, June, October, November and December are the most intense months, with a greater number of orders to prepare,” says Martínez.
Before modernising its logistics operations, all orders were prepared using paper. Operators had delivery notes containing the list of items they needed to locate and the quantity required to complete each order. “With the growth our company was experiencing, this way of preparing orders was no longer efficient. So, we committed to digitising our operations with a WMS,” says Martínez.
Installing a warehouse management system is a critical decision for any company, since it has a direct impact on business performance. “We’d been comparing different warehouse management systems on the market, and, in the end, we decided to go with Mecalux’s solution. The Würth Group had spoken very highly of the software and its positive experience when starting up an automated clad-rack warehouse by Mecalux in La Rioja (Spain) managed by Easy WMS,” says Martínez.
Three storage systems
Mecalux has equipped the Würth Modyf facility with three storage systems: pallet racking, heavy duty shelving and light duty shelving. According to Martínez, these systems “make the most of the space in our warehouse.”
The pallet racks and picking shelves share a common denominator: they offer direct access to the products, which is indispensable for facilitating storage and picking tasks. Additionally, the locations can be adapted to accommodate any type of product. “The racks are ideal for our goods because we manage many different SKUs,” says Martínez.
How Easy WMS works
Würth Modyf opted for Easy WMS because it is a very intuitive, user-friendly software program. “The operators have got used to this system more quickly than we expected,” says Martínez. Easy WMS intervenes in all processes taking place in the warehouse. With the help of RF (radiofrequency) scanners, the employees follow instructions from the software to complete any logistics operation:
- Goods receipt: operators identify the items that arrive every day by reading the barcode with their RF scanners. Easy WMS assigns them a location based on their SKU, size and turnover, notifying Würth Modyf’s ERP (enterprise resource planning) system so that it can integrate this data.
- Storage: the operators bring the products to the location designated by Easy WMS, whether on the pallet racks or the picking shelves. The software organises this operation in such a way that the picking locations are replenished first. This ensures that they are stocked with the necessary goods at all times and avoids any interruption due to a stockout.
- Order preparation: orders are prepared according to a combination of batch and zone picking. This means that the operator works only in the area assigned to them and, once there, picks products belonging to various orders on a single run. Easy WMS shows the operators how to prepare each order, telling them which location to go to, which items to pick and how many to extract.
- Consolidation: once the tasks generated by Easy WMS have been finished, the operator moves the goods to the consolidation area. There, the WMS groups the items that make up a single order and that have come from the different working areas in the facility. Additionally, the operators group together products of similar sizes so that they are distributed by the ideal transport agency in terms of their volume and zone.
- Dispatches: after packaging, labelling and printing all the pertinent documentation, the orders are delivered to the various transport agencies and sent to their destination.
Scalable logistics
Würth Modyf’s supply chain is ever-changing. To adapt to new market needs, the company has expanded the functionalities of Easy WMS with the following additional modules, which foster logistics scalability:
Multi Carrier Shipping Software
- Comprehensive control of the packaging, labelling and dispatch process.
- Creation of the necessary documentation for the carrier and of the tracking number.
- Communication with the transport agencies that deliver the orders.
- Order grouping by route and carrier.
Dispatches constitute a critical phase in the Würth Modyf warehouse, taking into account the wide variety of destinations to which orders are shipped. Before delivering the goods to the various transport agencies, the company carries out a set of processes, ranging from order picking, packing and labelling to the creation of documentation for the carrier.
The Multi Carrier Shipping Software module facilitates and streamlines all these operations to avoid delivery delays and errors. To do so, it sends instructions to the operators on how to package each order and generates the labels and documentation for each carrier.
The program also communicates with the distribution agencies that deliver Würth Modyf’s orders to create the labels and tracking number automatically. “Multi Carrier Shipping Software communicates with the various agencies we work with, facilitating dispatches and allowing us to monitor our packages much more rigorously,” says Martínez.
Supply Chain Analytics Software
- Comprehensive control of all warehouse activity.
- Monitoring of information on warehouse processes.
- Continuous improvement in the warehouse through data analysis.
- Customisation of software by being able to add complementary KPIs.
Würth Modyf is aware of the fact that, to have an agile, flexible supply chain, it is necessary to constantly carry out improvements in all processes. And for this, it is crucial to understand its intricacies.
Würth Modyf uses Supply Chain Analytics Software to analyse its logistics operations in detail. This software provides useful data on the main tasks performed in the warehouse in order to implement strategic improvements that increase productivity. The module contains operator panels and provides comparative graphics with information on the operation of the warehouse. At a glance, logistics managers can check indicators such as entries, exits, available capacity, number of SKUs, prepared orders and pending orders.
Labor Management System
- Operational performance monitoring.
- Identification of improvement opportunities in the workflow.
- Warehouse workforce planning.
- Increased operator productivity.
Given the key role of operators in carrying out the various tasks, Würth Modyf wanted to objectively monitor operational performance to detect improvement opportunities.
With the Labor Management System module, the company can measure the throughput of the various warehouse activities and then make decisions geared towards improving efficiency. “With Labor Management System, we can monitor workflows in our facility to enhance productivity,” says Martínez.
Digital, omnichannel logistics
Würth Modyf, a company with its sights set firmly on growth, has expanded enormously in recent years. To cope with this increase in turnover and order volume, the company has had to overhaul and modernise all its logistics processes to adapt to omnichannel retail.
With the help of Easy WMS, Würth Modyf can monitor all its SKUs in stock much more accurately and prepare over 1,500 orders a day more quickly. Technology has helped the company manage this expansion and will enable it to keep growing in the future.
We’re thrilled with Easy WMS; this system has been completely tailored to our needs. Plus, the operators have got used to it more quickly than we expected. With Mecalux software, we can guarantee 24-hour service with practically zero errors.
Würth Modyf responds:Interview mit Juan Martínez, Operations Manager at Würth Modyf |
---|
Why did you decide to digitise your logistics operations with a warehouse management system? Between 2015 and 2020, our company’s turnover increased from €3 million to more than €20 million. The Würth Group has always placed great importance on the role of the logistics department: our priority is to deliver orders to customers in 24-48 hours at most. With such a high turnover and a growing number of orders, we had to digitise our processes to avoid any possibility of error. The only way to ensure 24-hour service with errors brought down to practically zero was with the help of a warehouse management system. It’s very clear to us that, to keep expanding, we need to properly manage our entire business, which includes the administrative and sales side as well as logistics. |
How was picking done before having a WMS? Initially, picking was done manually; we relied on paper. The operators were given a delivery note specifying the items and quantities of each needed to complete each order. When order numbers began to rise, working in that manner wasn’t effective any more. It was essential to look for a much more accurate inventory management solution. |
|
That’s when you implemented Easy WMS from Mecalux. Correct. We moved to a new, bigger warehouse in Polinyà, not far from Barcelona, where we tripled our storage capacity. We took the opportunity to change our working methods with the help of the Easy WMS warehouse management system. We wanted to modernise our logistics operations with this software to double our productivity, ramp up the number of orders and, above all, guarantee continuous 24-hour service. Thanks to the software from Mecalux, our warehouse is now much more controlled and organised.Order is basic for differentiating the different working areas, flows and products. Otherwise, we’d have difficulty delivering orders to customers. |
Why is innovation so important for your business? Year after year, our customers’ needs change, and the number of businesses that count on us grows. Our customers’ satisfaction is fundamental for us, so we need to align our logistics operations and our way of working with their requirements. |
|
The WMS enables you to keep tight control over your warehouse processes. Why was it such a priority for Würth Modyf to analyse the status of its operations? For us, it’s essential to analyse the status of operations in the facility because the data enables us to improve processes. Without analysing what’s going on in the warehouse, it’s impossible to detect which operations we can improve or which measures we can implement. It’s our intention to optimise the facility and constantly boost productivity. |
What was Würth Modyf’s experience during the coronavirus pandemic and what are its prospects for the future? Fortunately, the pandemic hasn’t affected our business negatively; we were able to adapt in the face of adversity. Although clothing and footwear sales went down because many companies had stopped doing business, we sold other products that the situation called for. Now, little by little, we’re getting back to normal. Our future plans are very optimistic: we expect to double our turnover in the next five years and to open new stores in Madrid and other cities in Spain. |
Gallery
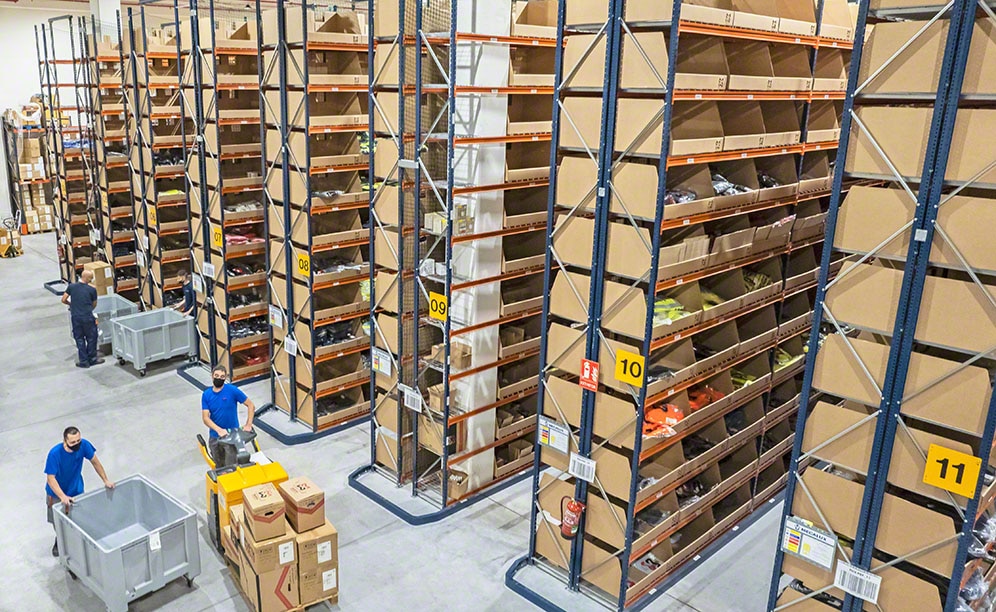
Würth Modyf's warehouse for workwear and corporate uniforms
Ask an expert