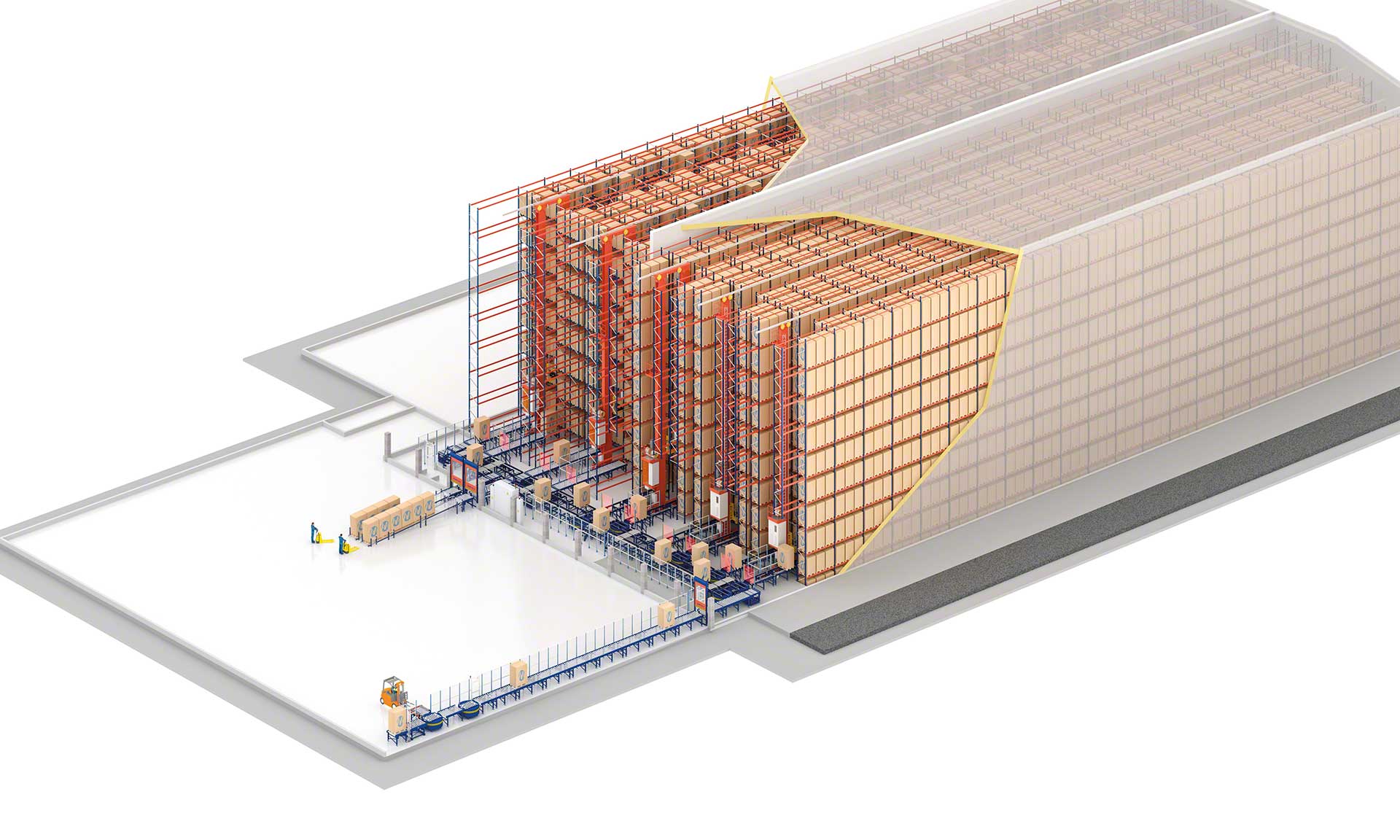
Cardboard packaging manufacturer WOK Brodnica automates storage of finished goods
WOK Brodnica, a renowned Polish manufacturer of corrugated cardboard packaging, has automated the internal transport and storage of its finished goods to accelerate its expansion in the Polish market.
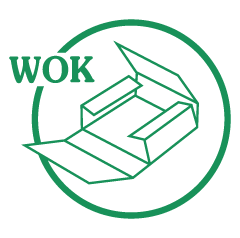
WOK Brodnica, a renowned Polish manufacturer of cardboard packaging, has automated the conveyance and storage of finished goods in its centre in Brodnica. The company has installed an AS/RS for pallets managed by Easy WMS and connected to production via conveyors.
WOK Brodnica: high quality cardboard packaging
WOK Brodnica is a family-run business specialising in the manufacture of corrugated cardboard boxes and packaging. Since it was founded in 1991, it has continuously diversified and expanded its product range. WOK routinely automates all its working processes to improve productivity and provide better customer service.
- Headquarters: Brodnica, Poland
- Founded in: 1991
- No. of employees: 400
- Customers: mainly food companies
CHALLENGES
|
SOLUTIONS
|
BENEFITS
|
---|
A sudden increase in production volume can throw logistics processes off-kilter, leading to cost overruns and inefficiencies in the supply chain. In recent years, corrugated cardboard box and packaging manufacturer WOK Brodnica has managed to cope with increased production thanks to its clear commitment to process automation.
Nowadays, WOK has an efficient supply chain with a warehouse in Brodnica, Poland, capable of effectively managing the daily conveyance and storage of 1,500 pallets from its production centre.
“Our logistics needs were covered until we realised we lacked the space to store our finished products and that we had to better meet our customers’ growing demands,” says Wiesław Lipiński, Investment Manager at WOK.
The company decided to install an automated storage and retrieval system (AS/RS) for pallets from Mecalux to house its finished goods from production. To speed up product flows, the AS/RS is automatically connected to the production line outputs by means of a conveyor system. The conveyor runs throughout the logistics centre to move the finished goods ready to be shipped to customers.
“One of our main logistics challenges is to ensure the storage and delivery of all our finished items from the production plant in the shortest time possible. Optimising logistics costs is also a priority,” says Lipiński.
WOK’s facility, which is a clad-rack structure, has been expanded to adapt to the spike in production. Originally, two aisles were installed, and a few years later, three more aisles were added. “In total, we can store around 14,000 pallets with finished goods and a small amount of raw materials,” says Lipiński. To control the automated warehouse, WOK has deployed Easy WMS warehouse management software from Mecalux. It acts as the brain of the facility, supervising and coordinating all the operations that take place in it: goods receipt, identifying products and validating their characteristics; the storage process, which includes placing the pallets in the racking locations based on rules and algorithms; and dispatch, grouping outbound orders by destination.
“Thanks to automation and competitive software, we can meet all logistics requirements while minimising losses. The expansion of the warehouse has also helped us to optimise stock,” says Lipiński.
Custom-designed AS/RS
“Every day, the AS/RS receives 1,500 pallets from our production lines that are then sent to customers in Poland,” says Lipiński.
The AS/RS, with 23-metre-tall racking, stands out for its functionality. The goods-in/goods-out processes — separated to avoid interference — are carried out automatically by means of a conveyor system. The conveyor lines move the unit loads systematically and in an agile way, without errors or human intervention.
The inside of the facility was designed to optimise space without compromising throughput. “This AS/RS provides a large storage capacity in a relatively small space. It allows us to store a wide range of products,” says Lipiński.
To speed up flows of goods, two of the five aisles are outfitted with stacker cranes adapted to the characteristics of the AS/RS and to the products housed in it: these machines have telescopic forks that can store up to four pallets deep on each side of the aisle.
Traceability of 14,000 pallets
“Thanks to the Easy WMS warehouse management software from Mecalux, the products are identified as soon as they enter the facility. The WMS also gives us immediate information on stock and locations and enables us to efficiently prepare the orders dispatched to customers,” says Lipiński.
One of WOK’s priorities was to integrate the warehouse management software with its SAP ERP system and for the two programs to maintain permanent two-way communication. The connection between the systems ensures the transfer of data and information essential to manage the facility more efficiently, boost the productivity of logistics processes and coordinate movements of goods (from the time they leave production and arrive at the AS/RS until they are prepared for distribution to customers).
The products arrive at the AS/RS stretch-wrapped and labelled from production. Easy WMS identifies the pallets the moment they cross the checkpoint, where it is verified that they meet the requirements established for their storage on the racking. Once the pallets are identified, Easy WMS makes a series of calculations taking into account the number of empty locations, the SKU and the demand level to assign each item an appropriate slot. Thus, for example, high-demand products are placed near the lift to streamline their entry and exit.
Fire safety system
WOK Brodnica works with boxes and packaging made of corrugated cardboard, a material classified as an ordinary solid fuel and that produces embers when burned. Therefore, to ensure the safety of the entire warehouse, it is equipped with an effective fire protection system: smoke detectors and control devices that, in the event of a fire, would act directly on the affected area until extinguishing it.
The fire safety system consists of a network of pipes filled with pressurised water and outfitted with discharge nozzles (sprinklers) positioned strategically inside the racks. In the case of fire, only the sprinklers near an area with fire exceeding a certain temperature would be activated, with water flowing freely through the racking.
Future-ready warehouse
“We’re optimistic about the future. At WOK, we work constantly to enhance the quality of the products we offer,” says Lipiński. Increasing the production volume without sacrificing logistics efficiency is one of the biggest challenges for any company, even more so when it is committed to ensuring excellent customer service.
Through automation, WOK now has logistics operations prepared to take on future challenges. With the automatic conveyance and storage of finished goods from production, WOK benefits from a supply chain capable of managing 1,500 pallets a day to satisfy the needs of its customers throughout Poland.
We’re thrilled with the benefits the AS/RS has brought to our logistics operations. Thanks to the Mecalux solution, we’ve ramped up productivity and, at the same time, reduced errors, risks and problems when it comes to locating the products stored.
Gallery
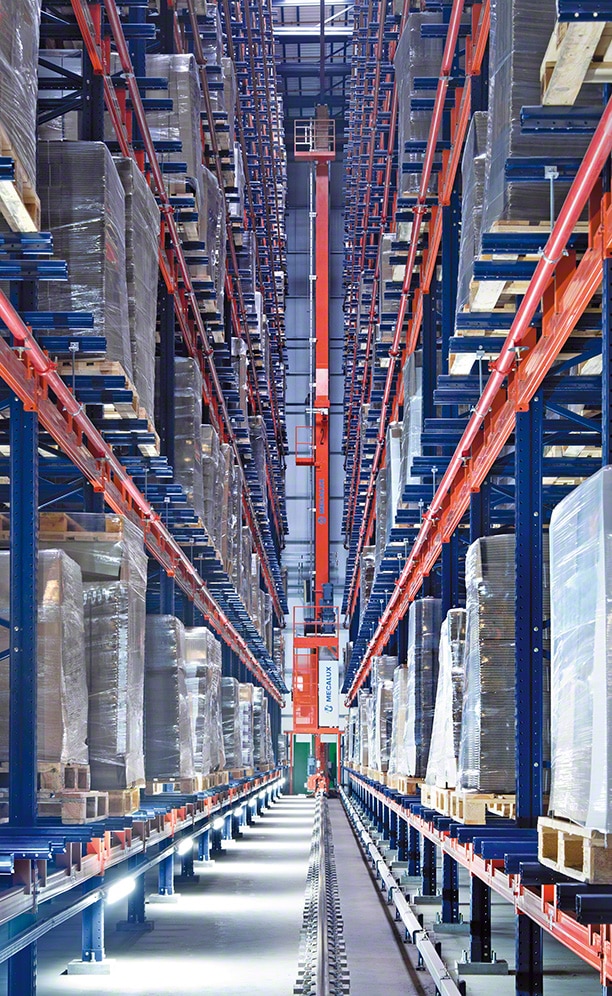
Automatic stacker crane custom-designed to WOK's requirements
Ask an expert