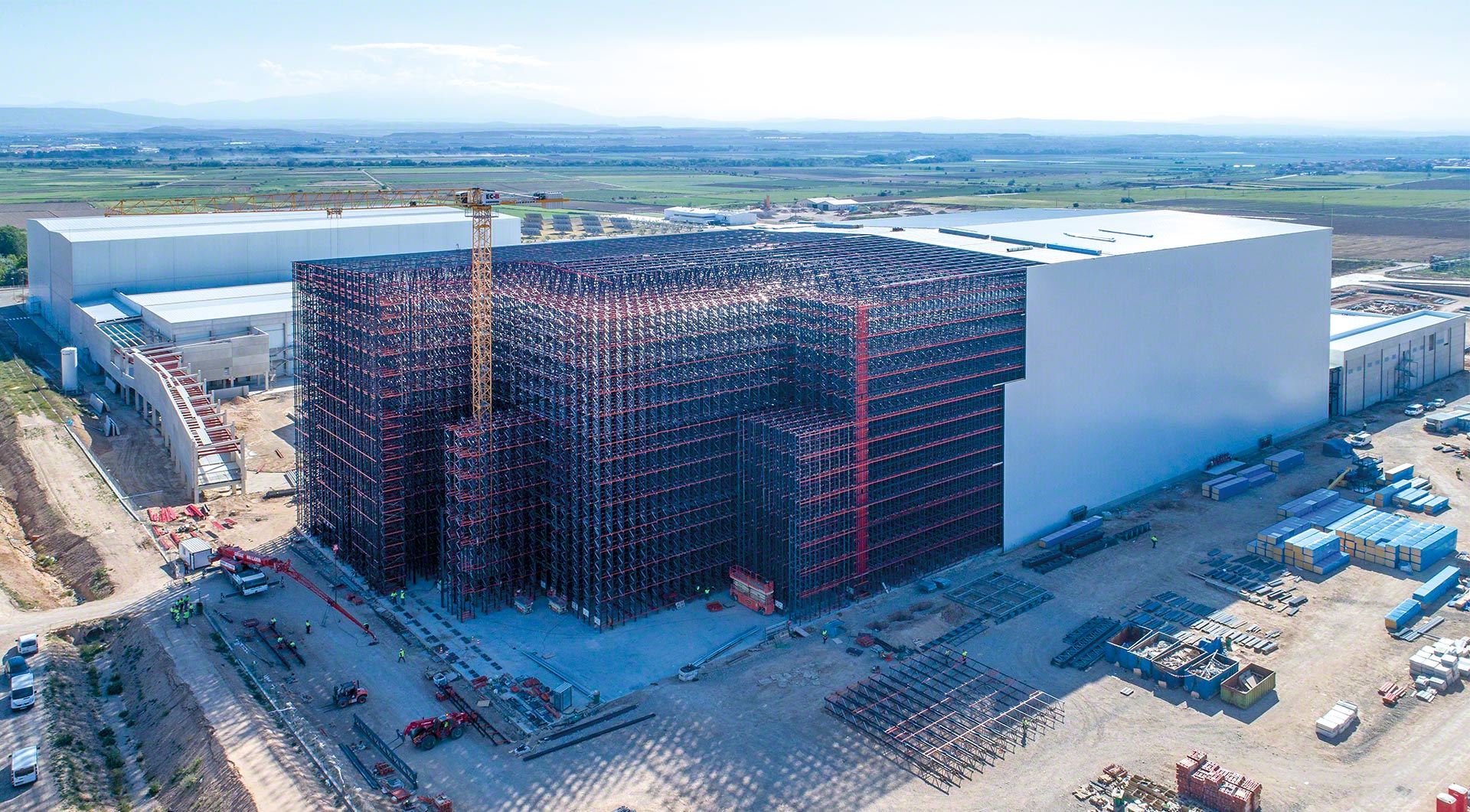
Congelados de Navarra at the forefront of cold storage solutions
A benchmark logistics center in the food industry due to its innovative and intelligent automation systems
A benchmark logistics center in the food industry due to its innovative and intelligent automation systems