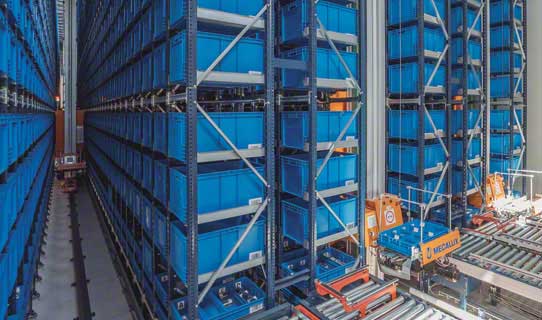
The new Grégoire-Besson distribution centre guarantees fast, accurate order preparation
The combination of three storage systems lets merchandise be organised according to their characteristics and demand, streamlining order picking tremendously.
The combination of three storage systems lets merchandise be organised according to their characteristics and demand, streamlining order picking tremendously.