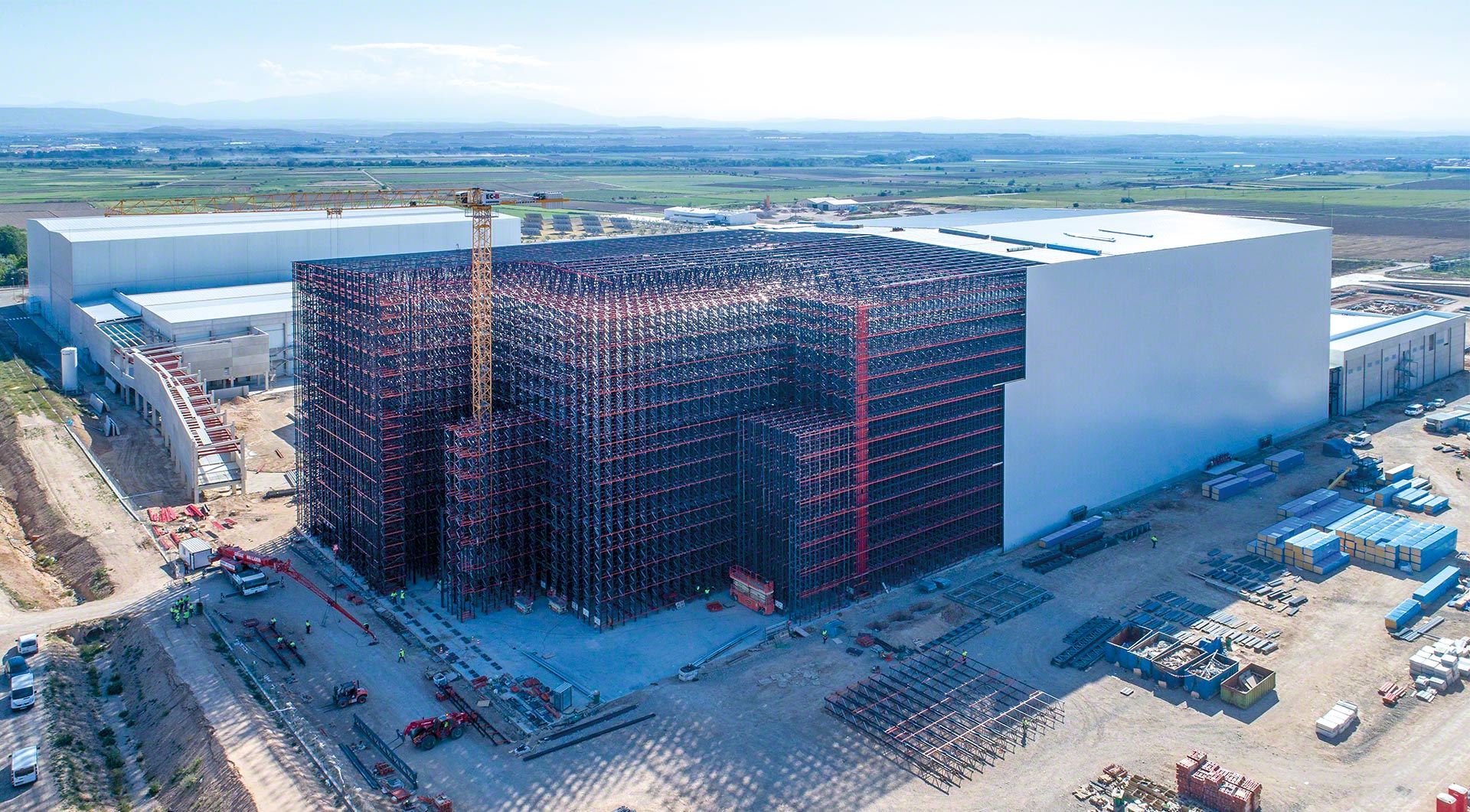
Automation of Maverick Laboratories' logistics centre
an automated clad-rack warehouse, live racking, a sequencing buffer for pallets and 45 blocks of pallet racks. Combined storage solution
an automated clad-rack warehouse, live racking, a sequencing buffer for pallets and 45 blocks of pallet racks. Combined storage solution