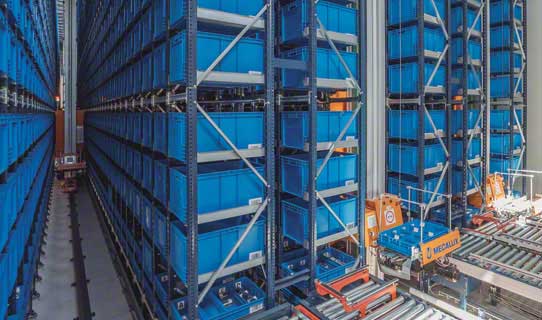
Sam Outillage: A high-throughput warehouse
Thanks to this new, modern and productive warehouse, SAM Outillage has optimised its logistics processes and boosted its throughput and storage capacity.
Thanks to this new, modern and productive warehouse, SAM Outillage has optimised its logistics processes and boosted its throughput and storage capacity.