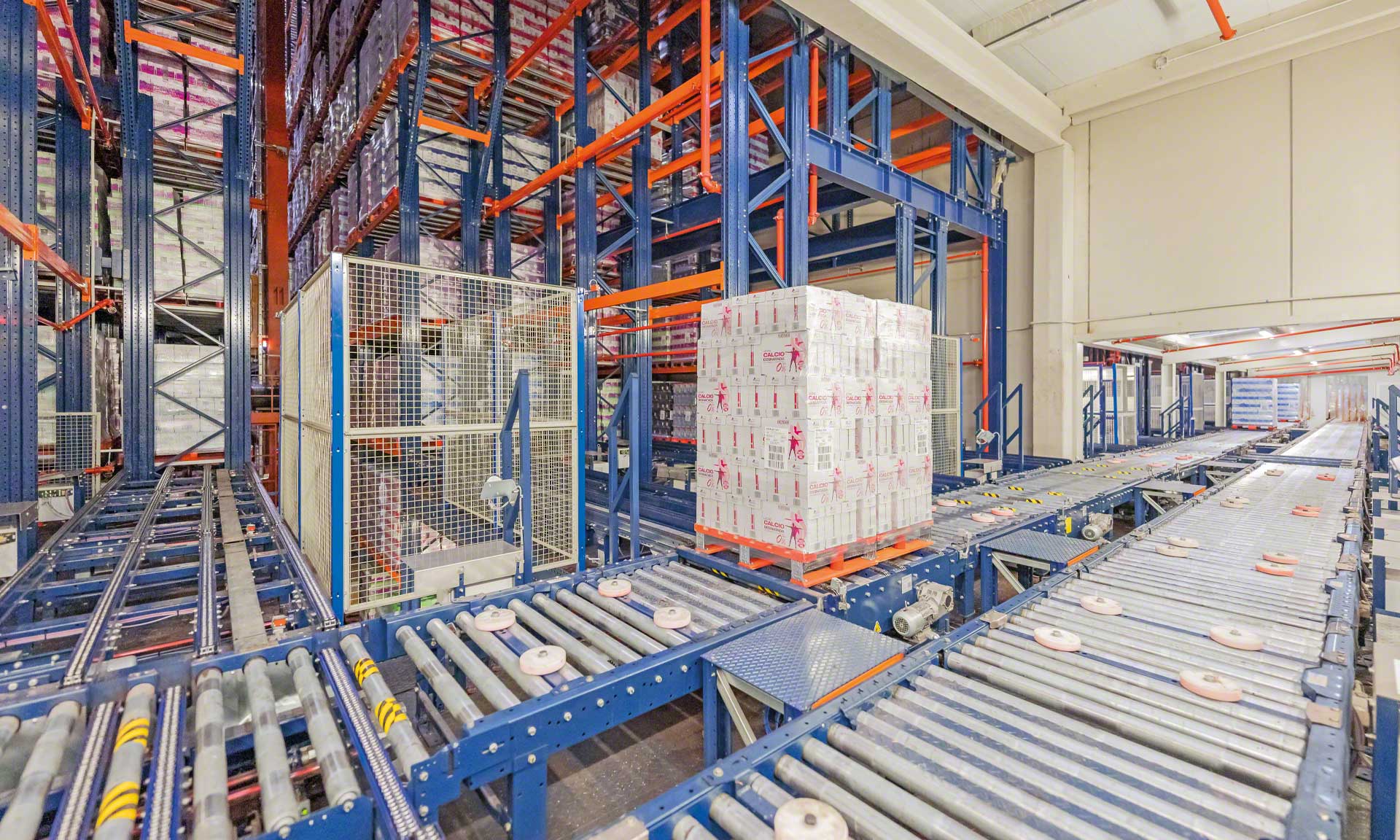
Esnelat automates its logistics operations with two AS/RS for milk products
Esnelat, part of the Iparlat dairy group, automates its logistics operations to support the production of over 300 litres of milk a year.
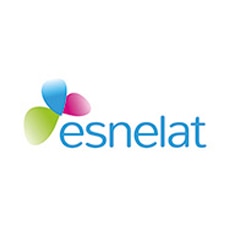
Esnelat, part of the Iparlat Group, has installed two automated warehouses in its production plant in Urnieta, Spain. Through logistics automation, Esnelat can efficiently handle the annual production of more than 300 million litres of milk.
Esnelat: dairy company feeding the future
Esnelat belongs to the Iparlat Group, a dairy business founded in 1953 from the merging of farmers’ cooperatives in Spain’s Basque Country and Navarre regions. The company offers a wide variety of healthy goods, ranging from milk products to vegetable drinks and coffee pods. All its items are produced and packaged with state-of-the-art technology in the company’s four production plants in Spain. Since 2004, Iparlat has been a milk supplier for Spanish supermarket chain Mercadona.
- Founded in: 1995
- Annual production: 300 million litres of milk
CHALLENGES
|
SOLUTIONS
|
BENEFITS
|
---|
Iparlat is a Spanish manufacturer of milk and soy drinks. Its production plant in Urnieta (Basque Country) is managed by Esnelat and specialises in milk processed at ultra-high temperature (UHT) in different formats. At its centre, the company produces lactose and lactose-free milk, cream, milkshakes and vegetable drinks.
For a company like Esnelat, food logistics involves moving, storing and shipping perishable products. Due to their attributes and composition, these items could deteriorate and thus should be consumed before a specific date. “We need to produce, store and dispatch approximately 300 million litres of milk and dairy products a year. In logistics terms, that figure amounts to 350,000 pallets annually, with their corresponding characteristics, turnovers and demand levels. Each item requires appropriate FIFO management as well as strict monitoring and traceability,” says Esteban Robles, Technical Director of Esnelat (Iparlat Group).
Mecalux has accompanied Esnelat in its logistics expansion from the start. One of the most recent projects was the construction of two automated warehouses to store pallets containing milk packaged in cartons and ready to be sent to customers.
With Iparlat’s expansion in recent decades, Esnelat has had to scale up its facilities and modernise its entire logistics infrastructure. First, the company built a warehouse featuring an automated storage and retrieval system (AS/RS) with a capacity for 9,500 pallets and connected to the production lines. Then, it implemented a second facility with an AS/RS with three aisles and double-deep racking. A few years later, it added on two more aisles. The result is a total storage capacity of 14,000 pallets between both warehouses. The two buildings are joined automatically via conveyors and lifts.
Mecalux’s Easy WMS warehouse management software orchestrates all logistics operations and controls stock in the two Esnelat facilities. Coordinated by Easy WMS, the automated storage and conveying systems prevent goods handling errors, ensure full product traceability and accelerate the business’s response times.
The need to manage rising quantities of perishable, high-turnover stock led Esnelat to invest in automated solutions that would optimise processes and minimise goods storage times. “It would be impossible to manage 350,000 pallets a year manually,” says Robles.
The entire Esnelat logistics complex has been personalised down to the last detail to meet the company’s requirements. For example, after being put into operation, the first AS/RS had to be modified to handle different unit loads in order to adapt to business changes: “The racking and the automated storage and conveyor systems were reconfigured to handle half pallets. We also have different carton formats, i.e., more unstable unit loads, so we had to shore up handling,” says Robles.
Automated storage connected to production
“The warehouses receive 1,200 pallets a day on average from the production lines and ship another 1,200 to customers,” says Robles. Achieving this high number of movements is only possible with the help of AS/RS. Operations in both facilities are fully automated: from the time the pallets with finished goods leave production until they arrive at the dispatch area.
The two Esnelat AS/RS are clad-rack warehouses. That is, they are formed by the 25-metre-tall pallet racks themselves, which serve as the storage system and support the structure. The external part consists of the cladding and a safety slab. The first warehouse built is connected to the production line outputs via a transfer car. This automatic vehicle transports the finished goods to the conveyors feeding into the AS/RS. With a surface area of 1,500 m², the AS/RS has five stacker cranes. These machines operate inside the storage aisles, removing and depositing products following orders from Easy WMS. The second facility also stores finished goods, in any of its five aisles.
A 4.5-metre-high roller conveyor joins the two buildings, automatically moving all the finished products. The advantages of this solution are that it saves the company time and improves its efficiency when transporting finished goods. Moreover, it avoids manual product handling.
The racks in both AS/RS are double-deep (with two pallets stored in each location, one behind the other), providing a greater storage capacity. To handle two pallets per storage level, the stacker cranes incorporate telescopic forks. These can reach the pallet in the second position of the racking. Automating Esnelat’s logistics centre has struck a balance between agility and storage capacity.
Warehouse digitisation
With such a demanding supply chain, another everyday challenge Esnelat faced was goods control. Therefore, to locate its products quickly, the company implemented Mecalux’s Easy WMS warehouse management software program in its two facilities. This system supervises and optimises everything that happens in the distribution centre, from the moment goods are received until orders are shipped. Products are managed in line with the first in, first out (FIFO) strategy.
The traceability enabled by Easy WMS is essential for a food company like Esnelat. It helps to identify and strictly monitor the status of its goods and all the stages they go through until reaching end customers.
The Mecalux software supervises and optimises all warehouse processes:
- Goods receipt. Products leave production stretch-wrapped and labelled. Easy WMS identifies the pallets the moment they cross the checkpoint and verifies that they meet the requirements established for storage in the AS/RS.
- Product storage. Once the pallets arriving from production are identified, Easy WMS sorts them into batches. It uses algorithms to assign a location to each pallet. The software comprehensively controls all goods, providing real-time information on their status. The WMS knows all the details on the products, e.g., size, batch, weight, characteristics, production and expiry dates, and inspection checks undergone.
- Order dispatch. Activity in Esnelat’s dispatch area is frenetic. Every day, around 1,200 pallets are shipped to customers. To carry out this operation efficiently, a large area has been set up in the complex to organise the goods to be distributed. As they leave the AS/RS, the pallets are sorted onto four automatic outbound conveyors. Easy WMS allocates each pallet a conveyor according to its order or transport route (i.e., pallets to be delivered along the same route will be placed on the same conveyor). This optimal organisation of the dispatch area has enabled Esnelat to ship products faster and without errors.
High-bay, integrated logistics
The priority of a food company such as Esnelat is to store goods in the right environmental conditions to preserve the properties of the food and ensure the health of consumers.
Esnelat’s supply chain stands out for its efficiency, productivity, speed, and safety in food handling. Automation is key for Esnelat’s logistics operations. It ensures maximum throughput and meets the company’s logistics needs with a single aim: to process, store, and dispatch around 300 million litres of milk and dairy products per year.
Automation has brought a number of benefits to our logistics processes. It gives us high reliability in producing, storing and shipping around 300 million litres of milk and dairy products a year. It also ensures effective stock control and full traceability of our 14,000-plus pallets.
Gallery
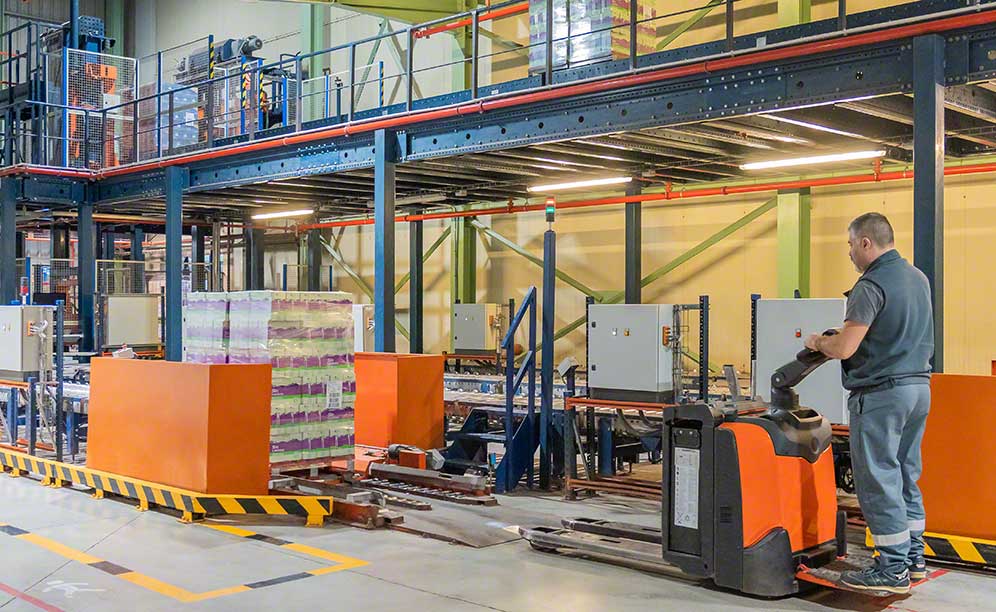
Esnelat uses AS/RS in its logistics centre
Ask an expert