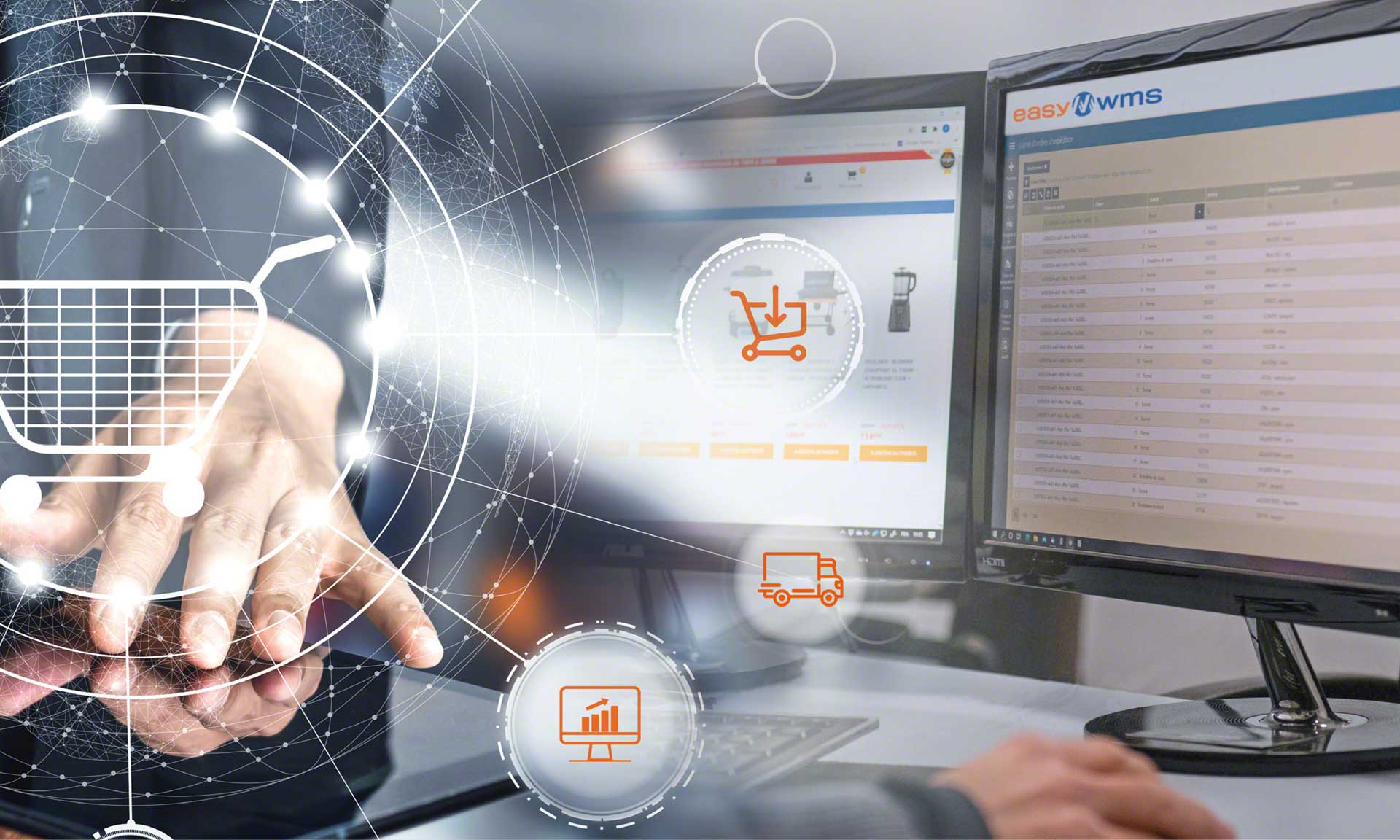
A logistics revolution for online sales
NEXECOM organises its warehouse operations with Easy WMS
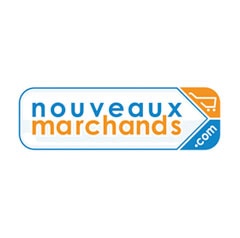
NEXECOM, an e-commerce retailer specialising in home goods, has launched a business strategy designed to double its turnover in the next five years. To do so, it has upgraded the IT system of its installation in Gémenos, France, with the aim of optimising operations and having full control over its thousands of SKUs. Aided by Easy WMS — the warehouse management system from Mecalux — and three of its additional modules, (WMS for Ecommerce, Multi Carrier Shipping Software and Supply Chain Analytics Software), the company has tripled the productivity of its logistics installation, from completing 100 lines/hour to now handling 300 lines/hour.
Continuous change
Transformation and evolution are the two concepts that best describe NEXECOM. In 2006, after successfully marketing video games and films on eBay, two childhood friends opened nouveauxmarchands.com, an e-commerce firm dedicated to home goods such as coffee makers, blenders, kitchen robots, irons, vacuum cleaners and portable air conditioners and heaters, among other items.
Since it was created, the company has continued to expand and, at the same time, renew itself. NEXECOM Managing Director Laurent Censier explains, “A rapidly growing e-commerce business has to modernise its warehouse every two to three years, more or less, to adapt to new market changes.”
In that vein, in 2019, it opened a new 5,000 m2 facility in the town of Gémenos (close to Marseille) where it manages thousands of SKUs in a wide variety of sizes. All orders are distributed to customers from there as well as from another subcontracted warehouse in Montpellier. This change posed an enormous challenge from a logistics point of view, as it forced the company to work with a larger number of SKUs with several seasonal peaks.
Initially, all operations in the installation in Gémenos were managed by means of an in-house developed ERP with a very basic warehouse management function. This entailed a huge risk of errors occurring, as well as insufficient productivity that proved to be a problem as the number of SKUs and orders grew. In the words of Laurent Brutto, Director of Operations at NEXECOM, “It was becoming more and more complicated to decide where to store the products, which slotting strategy to apply and, in particular, how to find the merchandise afterwards.”
Laurent Censier adds, “If we really wanted to strive for excellence, we had to optimise the organisation of our warehouse. With that in mind, we decided to equip our operators with a tool that would help them to avoid mistakes and be more efficient while leveraging order prep and space in the facility.”
Thus, NEXECOM decided to implement a warehouse management system (WMS). After comparing various options, it chose Easy WMS from Mecalux. “We opted for this solution because it was developed by a renowned company in the logistics sector and it’s a step ahead of its competitor’s systems. Plus, Mecalux’s technical team was by our side during the entire project, answering all our questions and helping us to find the ideal solution for our needs,” emphasises Laurent Censier.
NEXECOM has implemented Easy WMS and three modules that expand its features. Thus, according to Laurent Censier, “The software will evolve along with us and adapt to our requirements.” The modules in question are WMS for Ecommerce, Multi Carrier Shipping Software and Supply Chain Analytics Software.
Improved warehouse organisation
Laurent Censier highlights, “Customer satisfaction is our top priority. For that reason, we have to eliminate any possibility of error.” Organising an installation is the first step to providing good service. To this end, the centre has been divided into two working areas in which products of similar characteristics are stored. One section houses bulky items generally weighing over 15 kg (dishwashers, refrigerators, washing machines and cookers). The other accommodates small products such as electric toothbrushes and DIY tools.
Easy WMS is the software that governs all processes in this warehouse, from location assignments to order preparation.
To assign each product a slot, Easy WMS incorporates rules and algorithms that enable it to make the right decision. Hence, for example, items with a higher demand level are deposited in the most accessible areas, making them easy to locate when required. All products are duly identified and monitored from the moment they arrive at the installation. According to Laurent Brutto, “We now know the location of the goods in real time, which helps us to enhance quality in stock control.”
Additionally, the WMS organises the work in a logical way, getting the most out of operators and optimising the time allocated to picking. Easy WMS distributes the tasks to the employees and guides them through the facility at all times, telling them which products to locate, where to find them, how many of them to pick, etc. Not only does the system provide exact instructions to prevent human error, but it also designs operator routes to guarantee as little travel as possible.
The workers use radiofrequency terminals to communicate with the WMS in real time (to receive orders and confirm that they have been executed). “The system interface is extremely intuitive and user-friendly. When we have a new operator on staff, they receive a radiofrequency terminal, basic training with the warehouse manager, and in merely 15 minutes, they’ve learnt how to prepare an order. There’s no doubt: with the implementation of Easy WMS, we’ve professionalised operator work, and tasks are now distributed more appropriately. After seeing the benefits we’ve obtained with this work system, we’d never go back to the old way of doing things,” notes Laurent Brutto.
At the NEXECOM warehouse, the three Easy WMS modules intervene and supervise tasks as follows:
WMS for Ecommerce
This is specifically designed to facilitate picking for orders from the NEXECOM website. The software takes into account two particular features of this installation that directly impact the operation: on the one hand, the management of thousands of SKUs of varying sizes and characteristics and, on the other, the daily preparation of a multitude of orders, each made up of few lines.
WMS for Ecommerce has made order prep much faster and efficient. NEXECOM used to handle 100 lines per hour. This figure has now tripled, rising to 300 lines/hour. To achieve this, WMS for Ecommerce has simplified all warehouse operations, particularly foods receipt and picking, “with the objective of dispatching more orders in less time,” says the Managing Director.
To start with, in the receiving area, all products are identified as they arrive. They are then sorted based on whether they can be stored or whether they form part of an incomplete order. “Although this process requires time, we’ve gained in accuracy,” enthuses Laurent Brutto.
As for order preparation, WMS for Ecommerce designates orders as single-unit or multi-unit.
This classification helps to streamline order distribution and eliminate the possibility of error. According to Laurent Censier, “The error rate is practically non-existent.” Single-unit orders, for example, can be dispatched more quickly; once the operators have picked the items from the racks, they send them directly to the packaging area to be labelled and shipped.
As for multi-unit orders, they are prepared by area. The operators, assigned to a specific zone and product type, travel up and down the corresponding aisles, picking the SKUs that make up each order directly from the racks. They follow an order grouping method that consists of collecting products that make up various orders on the same run. These goods must then be sorted and arranged by order.
Multi Carrier Shipping Software
The last step before loading the orders onto the delivery lorry comprises packaging them, labelling them and printing the necessary documentation for the carrier.
First, Multi Carrier Shipping Software organises the goods packaging process, sending precise instructions to operators on how to do this (telling them, for instance, whether an order should be packaged in a single parcel or in more than one).
Then, it generates and prints a label for each order. The WMS knows the agency to which it will be distributed, so it creates a personalised label for each order. This label includes, among other details, the tracking number used by customers to monitor their orders.
Lastly, one of the advantages of Multi Carrier Shipping Software is that it allows the warehouse to communicate automatically and effectively with the transport agencies that deliver NEXECOM’s orders: Mondial Relay, GLS, DB Schenker and UPS.
Therefore, the carriers are given in advance all the information they need to make the delivery, such as the orders to pick up, the number of parcels and the destination.
Supply Chain Analytics Software
NEXECOM’s priority is to have agile, modern and intelligent logistics systems to rise to the challenge it has taken on. Laurent Censier explains, “In 2019, we implemented a very aggressive business development strategy to double our turnover within five years. To achieve this, we’ve decided to extend our product range and expand on an international level. All of these changes will affect our logistics operations. They’ll have a marginal impact on our warehouse, though, because we’ll be prepared for them, thanks to Easy WMS.”
So, how is this possible? The answer lies in data analysis. In order for the supply chain to be flexible and adapt quickly to market changes, first, it is necessary to know in-depth how it works and understand the operations that make goods movements possible.
The Supply Chain Analytics Software module is designed to help the company to achieve these objectives by getting the most out of the facility. This application provides useful data on the main warehouse activities with the aim of carrying out strategic improvements that boost productivity.
This software incorporates indicators that check the status of the installation at a glance (entries, exits, order preparation, storage capacity, etc.). Using all of these data, the warehouse manager sorts the information on what is occurring in the facility to then make the best logistics decisions.
MODULE | NEEDS | SOLUTION |
---|---|---|
WMS FOR ECOMMERCE |
|
Sort products received into two main categories: those that can be stored and those forming part of an order pending preparation, whether single-unit or multi-unit. |
MULTI CARRIER SHIPPING SOFTWARE |
|
Manage the order packaging process and — through integration with the main transport agencies that deliver NEXECOM’s orders — generate labels and personalised documentation for each carrier. |
SUPPLY CHAIN ANALYTICS SOFTWARE |
|
Incorporate predefined and comprehensive control panels that include the majority of functionalities to take into account in an installation. |
Expansion and new projects
“To continue growing, we need to take on other projects.” This affirmation from NEXECOM’s Managing Director perfectly sums up the business philosophy of this e-commerce retailer, a company unafraid to innovate and with the goal to expand.
Both Mecalux’s warehouse management software and additional modules have greatly increased the efficiency of all operations in NEXECOM’s facility and enabled the firm to monitor its thousands of SKUs more accurately.
In terms of the change this has brought about for the form’s logistics operations, Laurent Censier explains, “The COVID-19 pandemic was a stress test for our installation. During the lockdown, we broke sales records, forcing us to prepare a larger number of orders; thus, we were able to assess the performance of Easy WMS.” Fortunately, Easy WMS will accompany NEXECOM as it grows.“We know it will help us to meet our growth target for the next five years,” adds Censier.
NEXECOM has a very clear vision for the future: to serve an increasing number of customers, thanks to its orderly, efficient and productive warehouse. Easy WMS will help it to meet that objective.
We’re thrilled with Mecalux’s software and particularly with the company’s technical team, which answered all our questions and helped us to find the ideal solution for our needs. Easy WMS has reduced times and errors in order prep, so we’re convinced it will facilitate our growth objectives.
Advantages for NEXECOM
- Tripled number of orders: NEXECOM has gone from handling 100 lines/hour in order preparation to 300 lines every hour.
- Error reduction: Easy WMS carries out strict control of all the goods and guides operators preparing orders at all times. This has helped lower the error rate to practically zero.
- Growth and expansion: the warehouse management system adjusts easily to changes within NEXECOM, such as increased demand.
Gallery
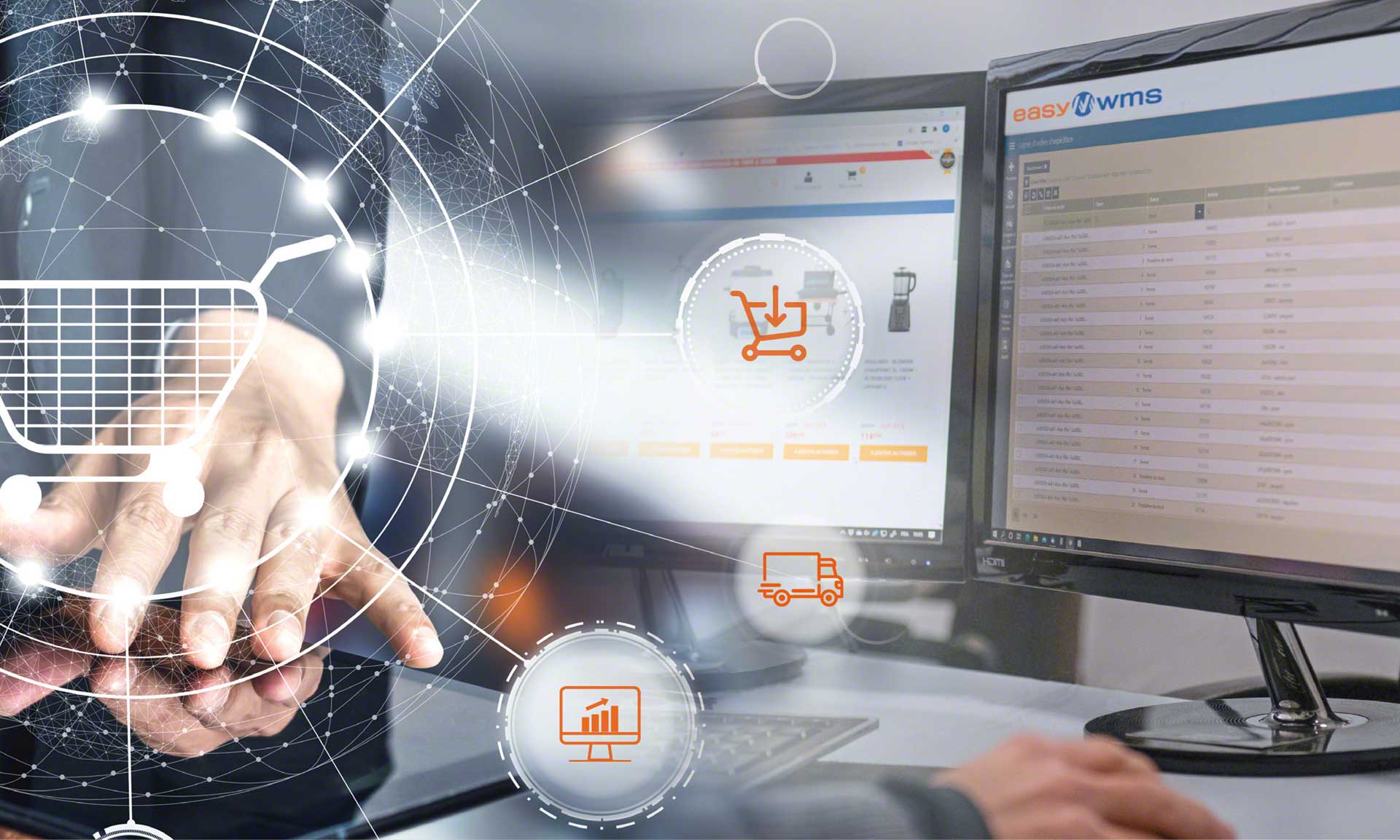
Easy WMS controls NEXECOM's thousands of SKUs at its warehouse in France
Ask an expert