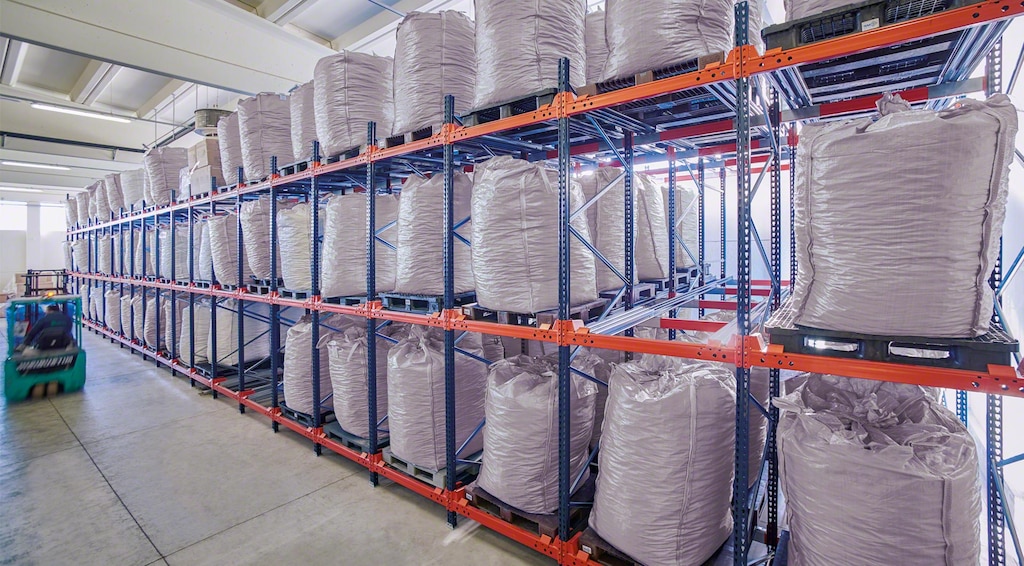
Push-Back Pallet Racking
High-density storage system for pallets that increases warehouse capacity and reduces handling times.
The product
Push-back racking: storage by accumulation saves time and space
Push-back pallet racking is a high-density storage solution for housing several pallets deep with a different SKU in each channel. It works by accumulation: the load is pushed along rails mounted on a slight slope.
The push-back system is extremely agile. The forklift does not enter the racking, and goods are accessed from a single working aisle. This solution is based on the LIFO (last in, first out) goods management method.
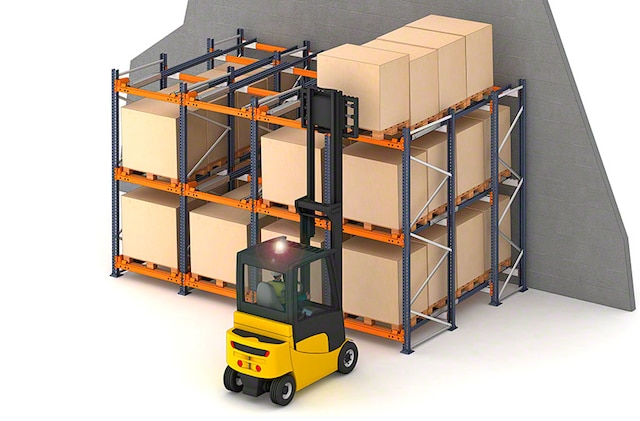
Push-back racking advantages
- Space savings: doing away with intermediate aisles makes better use of the available surface area and increases storage capacity.
- Time gained: forklifts do not enter the racking, and operations are carried out from a single aisle. This significantly streamlines loading and unloading.
- Multiple SKUs: each storage channel can house a different SKU, making it possible to diversify the products stored.
- Low-to-high temperatures: the carts in the racking are prepared to work at temperatures ranging from -30 °C to 40 °C.
- Operational safety: the locking devices, stops, pallet centralisers, and other elements ensure safe and easy storage and retrieval manoeuvres.
- Low maintenance: the system requires very little maintenance, while its components ensure high strength and durability.
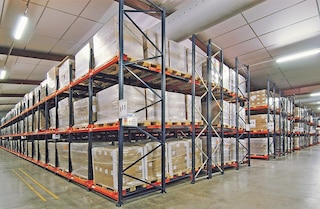
In addition to being very practical, with these racks, we’ve eliminated aisles and streamlined storage tasks
Applications of push-back pallet racking systems
Extremely flexible solution adaptable to different types of warehouses
Push-back racking is the perfect system for companies with medium-turnover palletised goods or with a small variety of SKUs and few pallets per SKU. It is also ideal for facilities that need to leverage their available surface area.
How does a push-back rack system work?
Set of carts or rollers for loading and unloading pallets smoothly and safely
Push-back racking works according to a simple movement mechanism involving carts (trolleys) or rollers. This mechanism leverages and balances two opposing forces: the pushing force to place the pallets in the storage channel and the force of gravity to facilitate their removal.
Testimonials
Case studies
See more case studiesPush-back rack configurations
Different structural options to suit the logistics needs of each facility
Mecalux’s push-back pallet racking with carts can store 2 to 4 pallets in depth, while the variant with rollers can accommodate 4-plus pallets.
Components of push-back pallet racking systems
Mecalux’s push-back racking stands out for its top quality across manufacturing processes, materials used and the finishes of the different components. This commitment to excellence ensures the utmost stability, strength and durability of the installations.
Although they share several common elements found in other types of metal pallet racking (e.g., frames and beams), what sets the push-back system apart is its rails and carts.
Push-back pallet racking is equipped with a set of specific components to ensure streamlined, risk-free loading and unloading operations. These elements ensure the safety of the operators, the goods, and the storage system.
Catalogues
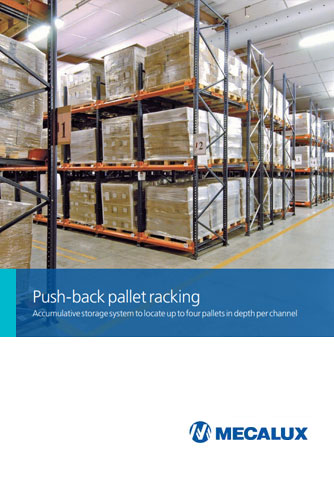
Push-back pallet racking (catalogue)
Accumulative storage system for housing several pallets in depth
Download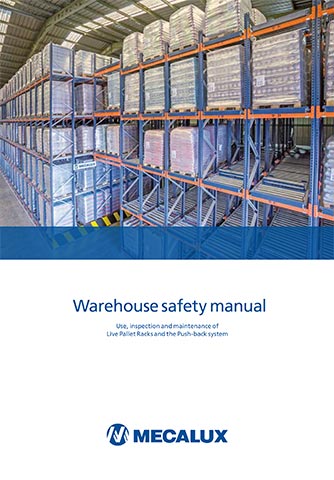
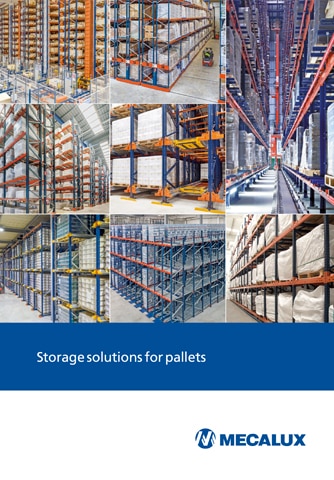
FAQs
Push-back pallet racking consists of high-density structures that eliminate interior aisles and allow up to 4 pallets to be stored by accumulation per channel. They increase warehouse capacity while reducing the surface area occupied by the storage system. Pallets are placed on a set of carts or rollers that are pushed along a series of rails mounted at a slight incline. They get their name from the forklift’s action of pushing back the pallets already in the racking to make room for a new one. The front part of the rack is the lowest part, so when goods are removed, the pallets at the back move forward one position by gravity, leaving the entrance to the channel occupied once again. With this type of racking, loading and unloading takes place in a single working aisle. Therefore, operations follow the LIFO (last in, first out) principle.
Although push-back racks are compatible with any type of product, they’re especially ideal in certain circumstances. For instance, they’re perfect for storing medium-turnover palletised goods with 2 or more pallets per SKU and that are managed via the LIFO method. Additionally, push-back pallet racking systems are also routinely employed in facilities with few SKUs and few pallets per SKU. They’re also an excellent option for housing fast-moving consumer goods (FMGCs) thanks to the speed they bring to loading and unloading manoeuvres. Likewise — as with all high-density storage solutions — these racks are an optimal solution for businesses that need to maximize their available surface area to expand their warehouse capacity.
The main difference between the two systems lies in the inventory management strategies used in each case. Push-back racking is based on the LIFO (last in, first out) principle since goods are accessed from a single working aisle. Pallet flow racking, on the other hand, has a loading and an unloading aisle, so its operations are governed by the FIFO (first in, first out) principle.
The push-back rack is a simple high-density storage system that allows a different SKU to be housed in each channel. Moreover, as the forklifts load and unload goods from a single working aisle, they do not enter the structure, reducing manoeuvring times and making operations safer. Nevertheless, these racks are limited by the depth and height of the channels. The system can be configured with 4 to 6 pallets deep (depending on the variant chosen — carts or rollers) and a maximum height of 7.5 m. If you require greater capacity or height, Mecalux has several other high-density solutions. One such system is the Pallet Shuttle, whose storage channels can exceed 40 m in depth.
Push-back pallet racking that uses the variant with carts and rails can house a maximum of 4 pallets per channel. In the version with rollers, on the other hand, the maximum number of pallets is 6. And that depth can be even greater if the weight of the pallet allows it.
Mecalux has set the maximum height of its push-back racks at 7.5 m, provided it works with suitable handling equipment. This is because the height is conditioned by the forklifts used.
The width of the channels — i.e., of the beams — is equal to the front dimension of the pallet including the load plus 150 mm (75 mm on each side).
In the carts and rails variant, the forklift handles the pallets from their wider side, introducing them in the racking with their bottom deckboards positioned perpendicularly. This way, they are securely supported (crosswise) on the carts and rails. In the roller variant, on the other hand, pallets are handled from the narrow side, with the bottom deckboards resting perpendicularly on the rollers to facilitate their movement.
In a push-back rack, each storage channel is allocated to a single SKU. As the channels are managed independently, each of them can contain different SKUs. This offers an advantage over drive-in racking, in which all channels of a lane are assigned to the same SKU.
Theoretically, any forklift model can work with push-back racking, although it’s important to take into account certain aspects. For instance, the rigidity and resistance of the forklift’s mast to the pushing force will condition the number of pallets per channel. This is because the forklift is responsible for applying the force required to push the pallets stored in the channel when introducing a new one. Additionally, as the height increases, the mast must be stronger: its components will wear more, and the forklift will be more difficult to control when removing pallets.
Ask an expert