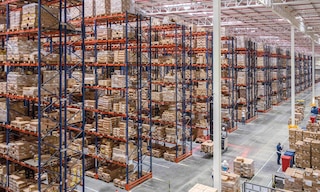
Pallet rack guide
Pallet racking is a storage solution that accommodates the products companies need to supply their customers.
There’s a diverse range of pallet racking on the market to meet even the most complex and demanding storage requirements. So, how do you choose the ideal solution for your warehouse? By considering factors such as the capacity or agility you want to achieve, available floor space, product variety and the project cost.
What is pallet racking?
Pallet racks are structures designed to house palletised goods on rows of horizontal shelving spanning multiple levels in height. Their distribution in the warehouse forms a set of aisles where operators with forklifts — or automatic handling equipment — store and retrieve materials from the racking positions.
When it comes to stock management, there are several methods and criteria you can employ. Although it’s possible to put pallets directly on the floor or stack them on top of each other, pallet racking improves the organisation of warehouse space. Pallet racking is typically seen in companies with products shipped to different destinations, ensuring efficient inventory distribution.
What components do pallet racks have?
In terms of construction, many pallet racking components are the same for all storage systems. These are the basic pallet rack parts:
- Frame. Metal structure made up of two vertically positioned uprights joined together.
- Shim. Metal component placed under uprights to level uneven flooring.
- Anchor bolt. Part that secures the racking to the floor slab. It’s selected based on the type of floor and stresses that the entire structure must withstand.
- Beam. Horizontal profile used to hold the pallets. It’s attached to the frame by means of connectors or endplates welded at its ends.
Depending on the solution you choose (shelving, direct-access racking, high-density systems) and the type of product to be stored, you can incorporate additional profiles and specific accessories. These include crossbars, shelves (wire mesh, metal or wooden) and supports for cylinders and coils.
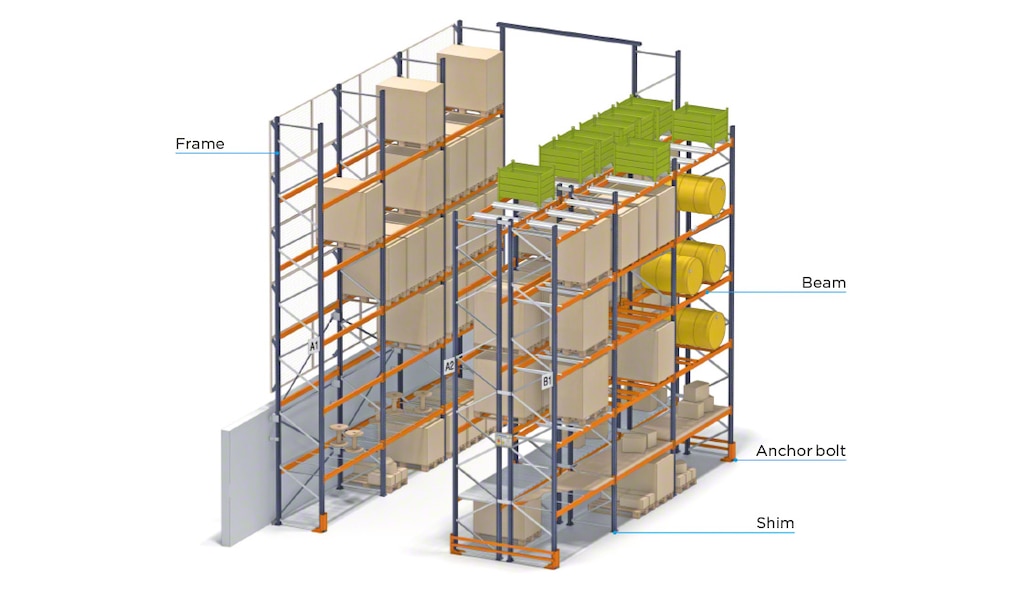
What advantages do the various types of pallet racks offer?
Pallet racking generally falls into two main subcategories: those that allow direct access to products and high-density systems.
The benefit of direct-access systems is that they facilitate product handling and ensure optimal storage space occupancy. Within this category are:
- Single-deep selective pallet racking. These racks stand out for their versatility. They feature accessories and add-ons to adapt the storage locations to any type of unit load, with different sizes and characteristics.
- Double-deep adjustable pallet racking. Racks are placed one behind another to increase storage capacity without sacrificing direct access to products.
- Cantilever racking. This is designed to hold bulky goods with variable lengths, such as profiles. It enables operators to handle this merchandise easily and visually monitor each item.
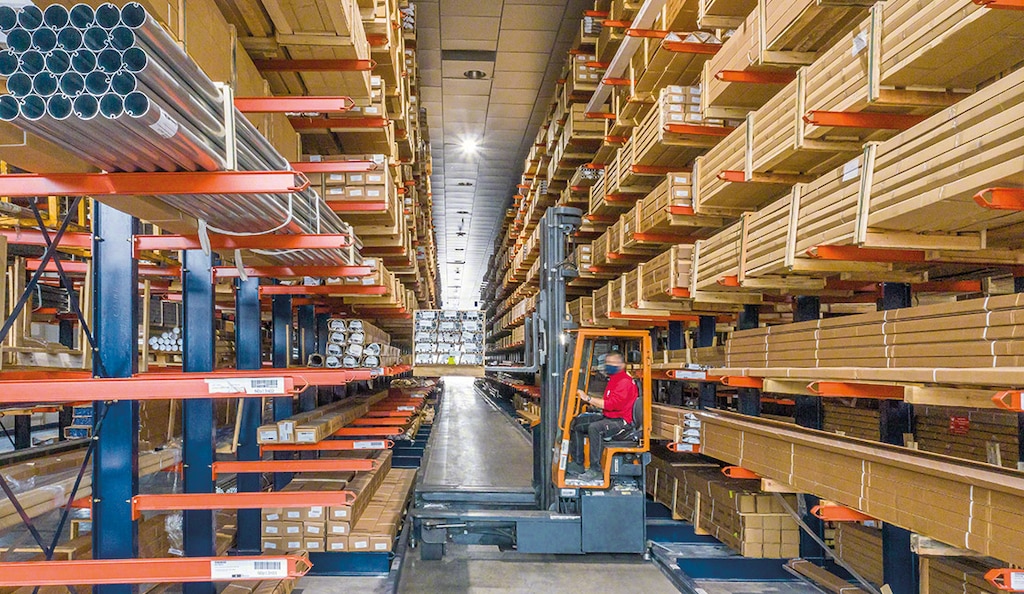
One of the primary advantages of high-density systems is that they offer a higher surface area occupancy, thus providing more storage capacity.
- Mobile racking (Movirack). These racks reduce the minimum number of working aisles required, accommodating more products without forfeiting direct access.
- Drive-in/drive-through racking systems. These make the most of available space, both horizontally and vertically.
- Pallet flow racking. This system features slightly sloped storage channels with rollers. Pallets are loaded on the higher side and slide by gravity to the opposite end. This ensures flawless product turnover according to the FIFO method (first in, first out).
- Push-back pallet racking. This racking also works in line with the gravity flow principle, but pallets are inserted and removed from the same end. This system facilitates and expedites the entry and exit of loads from their locations.
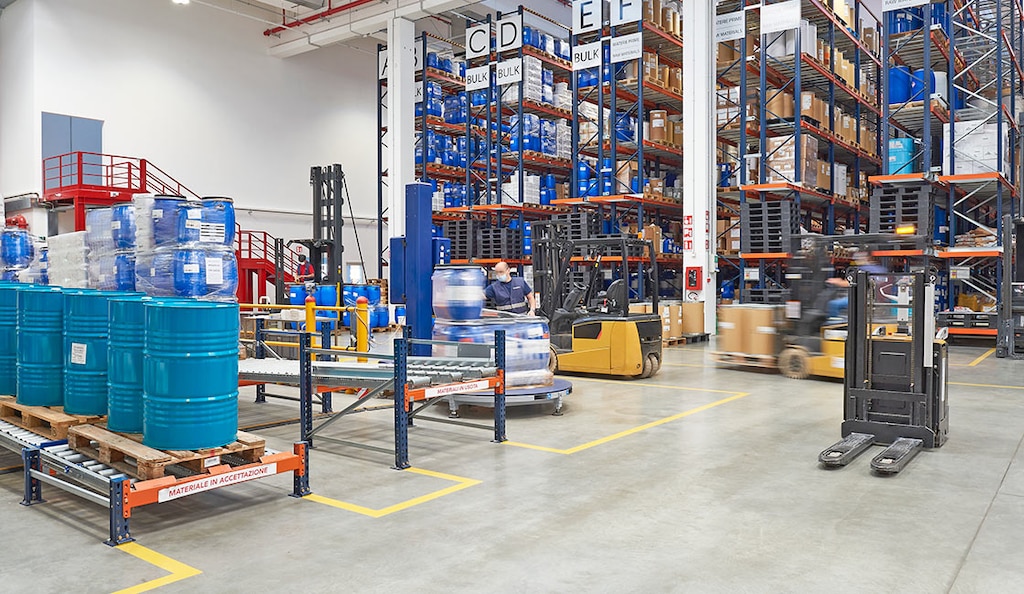
Pallet racking can also be automated by incorporating automatic handling equipment, which stores and retrieves products from their locations autonomously.
- Stacker cranes. These machines load and unload pallets from their positions. They can operate with single- and double-deep racking as well as pallet flow racking.
- Pallet Shuttle. A motorised shuttle is inserted into the storage channels, depositing each of the pallets in the deepest available space. This system increases storage capacity and agility while speeding up entries and exits.
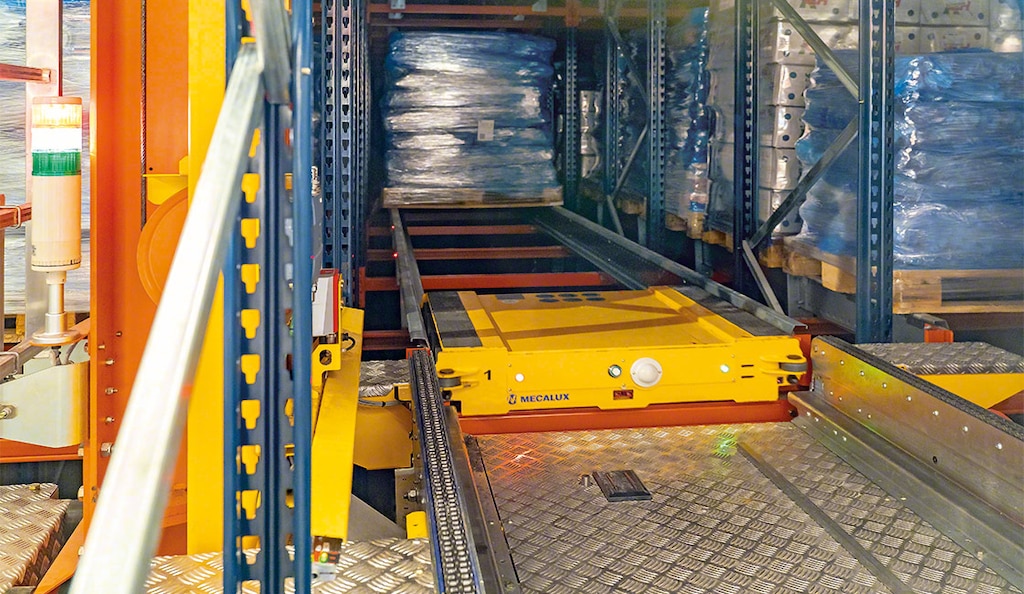
How do you select the right pallet racking?
The design and dimensions of your pallet racks will depend largely on variables such as the characteristics of your products, their weight and their handling position. Another factor is the handling equipment that will insert and remove the loads.
When choosing the ideal system, the racking should be versatile enough to adapt to different load types. This is why the components and even the materials used to make them are subjected to rigorous tests and quality controls to predict their behaviour.
Similarly, the regulations of each country come into play. These govern key aspects like safety and load capacity, ensuring storage in accordance with quality and security standards.
Exploring the possibilities of pallet racking
Pallet racks are an essential tool in warehouse management and business logistics. They provide an excellent organisation of space and goods while making operations more agile.
When selecting the most suitable solution, it’s important to consider factors such as available floor space and target storage capacity. Pallet racking is crucial for any company seeking to maximise its warehouse throughput. At Mecalux, we’re backed by more than 55 years of experience researching and developing logistics solutions for businesses in all sectors. Be sure to get in touch. We’ll help you find the best storage system to organise your logistics operations.