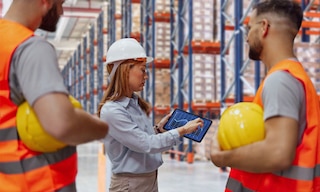
Warehouse Management Solutions
At Mecalux our goal is to assist you with the three key factors in logistics operations: inventory control, order management & organisation of human resources to reach your objectives.
-
-
Quality KPIs: Examples and application
-
Fire suppression with oxygen reduction systems
-
The cold chain in logistics
-
Cryogenic storage: Housing materials at -150 °C
-
SLAM in robotics: Industrial applications
-
Contract logistics: Entrusting operations to a strategic partner
-
Carbon footprint: Definition, calculation and how to reduce it
-
Logistics functions: What they are and how to optimise them
-
Logistics coordinator: Role and responsibilities
-
Lean methodology: Principles and business examples
-
Supply chain: What is it and how do you design one for your business?
-
Kaizen: The art of changing for the better in business
-
Warehouse SOP: What to include plus a sample
-
Capillary distribution: Optimising last-mile delivery
-
The logistics department: Functions and responsibilities
-
5PL providers: Strategic end-to-end partners
-
TIMWOODS and its importance for logistics
-
Consignment inventory and its impact on logistics
-
Pallet recycling and sustainability