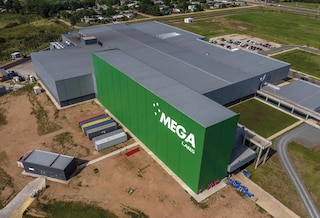
Pharma logistics: insights and challenges
Pharma logistics is in full swing after reaching a turnover of 69 billion dollars in 2019. In fact, according to consulting firm Grand View Research, the pharmaceutical logistics market will experience overall growth of 3.5% every year up to 2025.
In this article, we’ll break down the major factors affecting the pharma logistics sector: national regulations, the design and equipment of warehouses for medical supplies and materials and the particular challenges involved in transporting drugs.
What’s pharma logistics all about?
Pharma logistics is responsible for storing and distributing medication, active ingredients and other biological products, from the supplier to the final point of sale. It should be noted that pharmaceutical goods require special storage conditions, which is why they’re subjected to strict controls that ensure risk-free consumption.
Below, we highlight the main characteristics of pharma logistics:
- Maximum logistics traceability and inventory control: as a preventive measure, both aspects are intended to quickly identify batches of medicinal products in the event that they’re affected by an anomaly or irregularity.
- Strict quality control: the proper storage of drugs makes it necessary to establish specific procedures and install special areas in the warehouse. Examples of this are quarantine and sterilisation zones, designed to store drugs and other medicinal products free of microorganisms.
- Storage and transportation of products under special conditions: it’s vital to avoid breaking the cold chain of vaccines and thermolabile drugs. It’s also essential to prevent the contamination and theft of medical materials.
- Adjusted delivery times: this refers to goods that are usually of high value and often require urgent delivery. As a result, achieving maximum precision in their transportation is fundamental.
Legislation affecting pharma distribution: the Drug Supply Chain Security Act (DSCSA)
The Drug Quality and Security Act (DQSA), was enacted by Congress on November 27, 2013. Title II of DQSA, the Drug Supply Chain Security Act (DSCSA), outlines steps to build an electronic, interoperable system to identify and trace certain prescription drugs as they are distributed in the United States.
The following are the major provisions of the Drug Supply Chain Security Act (DCSA). These provisions apply to manufacturers, repackagers, wholesale distributors, dispensers and third-party logistics providers as noted below:
- Product identification: manufacturers and repackagers must put a unique product identifier on certain prescription drug packages, for example, using a bar code that can be easily read electronically.
- Product tracing: manufacturers, wholesaler drug distributors, repackagers and many dispensers (primarily pharmacies) in the drug supply chain need to provide information about a drug and who handled it each time it’s sold in the U.S. market.
- Product verification: these same groups must also establish systems and processes to be able to verify the product identifier on certain prescription drug packages.
- Detection and response: they must also quarantine and promptly investigate a drug that has been identified as suspect, meaning that it may be counterfeit, unapproved, or potentially dangerous.
- Notification: they also need to establish systems and processes to notify the Food and Drug Administration and other stakeholders if an illegitimate drug is found.
- Wholesaler licensing: wholesale drug distributors must report their licensing status and contact information to FDA.
- Third-party logistics provider licensing: third-party logistics providers, those who provide storage and logistical operations related to drug distribution, need to obtain a state or federal license.
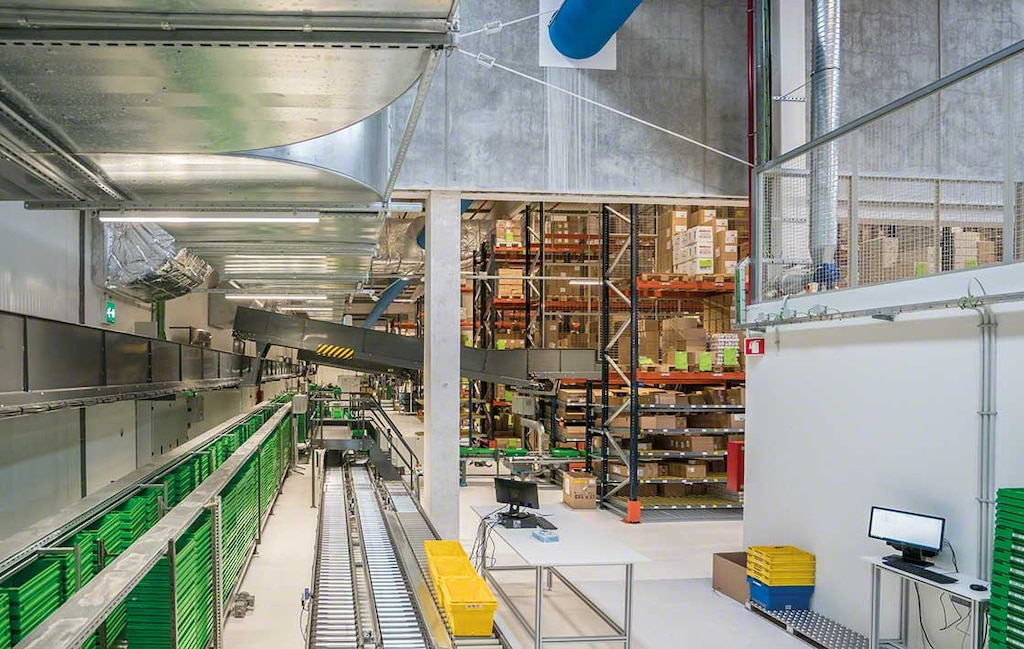
Efficient management of pharmaceutical installations
As with the storage of chemical products, safety is a must when it comes to designing pharmaceutical warehouses. The following are the key strategies being adopted by companies in the sector:
- Safe zoning and the selection of versatile storage systems
Pharmaceutical installations have to strike a balance between SKU accessibility (orders need to be delivered promptly) and maximum leveraging of space (especially in the case of cold stores or controlled-temperature warehouses). This involves an in-depth study and analysis of the warehousing zones, since their layout will affect daily operations and the safety of the goods.
For example, Mecalux equipped the installation of Ziaja, a Polish manufacturer of natural pharmaceuticals, with pallet racks combining the storage of pallets on the top with boxes at the bottom in order to carry out low-level order picking.
At other warehouses, the zoning is determined by specific storage conditions that the medical equipment must observe. At the Steris installation in France, we automated operations with conveyor circuits and stacker cranes. This improved safety in the goods sterilisation process by preventing risks stemming from manual handling of the goods.
- Optimised picking of small items
The preparation of orders containing medicinal products has the added difficulty that the goods are usually stored in small unit loads, such as boxes or trays. So, under these conditions, how can you speed up picking in pharmaceutical warehouses?
The answer lies in equipping your installation with systems that guarantee easy access to the SKUs. When picking is carried out following the product-to-person principle, two solutions commonly adopted are pick towers with conveyors for boxes and live storage for picking (used for high-turnover “A items” and usually integrated with pick-to-light devices).
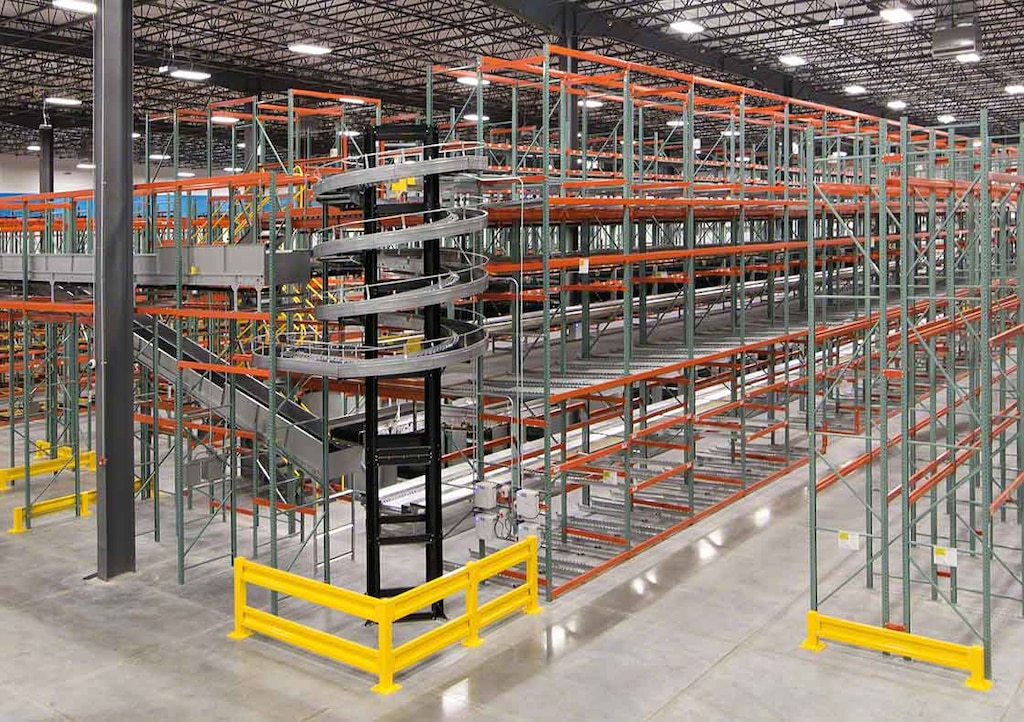
On the other hand, a warehouse management system is the solution that will make the difference in the face of such complex orders. Let’s not forget that, in pharma logistics, it’s not unusual for additional tasks, such as kit assembly or extensive quality controls, to be added to standard picking tasks.
This can be seen at the installation of US supply chain organisation ROi. Thanks to Easy WMS by Mecalux, ROi succeeded in improving efficiency by 20% in all its picking phases by drastically reducing the error rate.
- Monitoring of medicinal product stock
Taking into account the regulations affecting pharmaceutical logistics, visibility of available inventory is of paramount importance for manufacturers, distributors and points of sale. In fact, in the US, supply issues have to be reported to the FDA (US Food and Drug Administration).
Warehouse management systems help to prevent stockouts, as one of their key functionalities is to maintain real-time control of warehouse inventory. They also allow you to:
- Appropriate assignment of locations, prioritising logistics parameters such as stock turnover and expiry dates (FIFO flows).
- Automated control of stock inflows and outflows with the assistance of checkpoints.
- Organisation of picking and dispatches, based on the priority of each order.
- Information for each SKU, updated in real time. This makes it possible to locate batches very quickly.
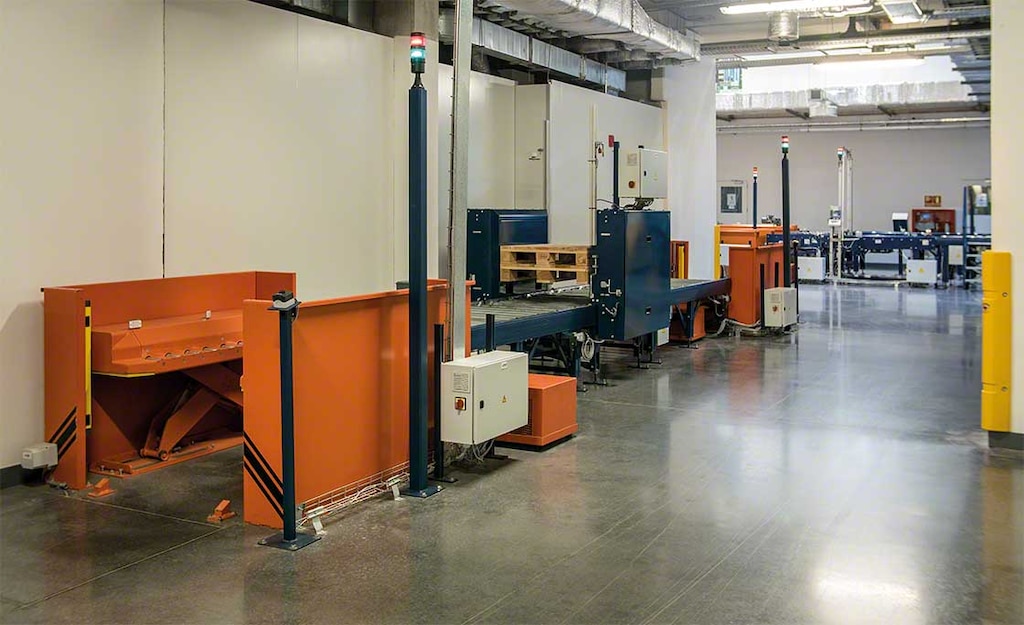
Good practices in the transportation of medicine
Risk management in the transportation of medication is crucial for keeping down costs in the pharma logistics sector. In the air transportation of thermolabile drugs alone, IATA (International Air Transport Association) estimates total losses due to storage problems at 35 billion dollars per year. Almost half of these are related to drug degradation while moving along the various links in the supply chain.
Thus, to protect the cold chain in pharma logistics, it’s fundamental to smooth out the points of friction at each stage. For instance, when exiting cold stores, SASs (security airlock systems) make sure the goods don’t experience sudden changes in temperature and that they aren’t impacted by other atmospheric factors.
Moreover, the means of transportation used to handle medication have to be prepared to maintain different temperature ranges (they can be isothermal, cold or refrigerated) with active and passive control systems. It’s also critical to monitor the humidity level, atmospheric pressure and impacts in product handling.
In this vein, developments in smart packaging are making it easier to properly store medicinal products. As a matter of fact, this sector is growing at an annual rate of 5.16%, according to data provided by the Smart Packaging Market Research Report for the 2017-2023 period. Smart packaging incorporates IoT (Internet of things) technology capable of collecting data on the condition of the medical materials and detecting improper handling of the goods.
The future of logistics in the pharmaceutical industry
The pharma logistics sector is currently undergoing significant changes, due not only to the growth it’s experiencing, but also to the regulation of the storage and transportation of medical materials.
The automation of processes and management of data with specialised supply chain software have proven to be two of the most notable pharma logistics trends. At Mecalux, we’ve worked with top companies in this sector throughout the world. Be sure to get in touch if you need personalised advice on designing or modernising your pharmaceutical warehouse.