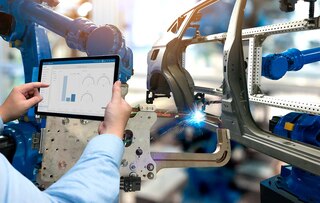
Bill of materials (BOM): your top supply chain ally
A bill of materials (BOM) is a document that defines all the essential elements for carrying out a production process. Generally speaking, the bill of materials plays a part in a product’s design, manufacture and assembly phases.
A bread maker’s bill of materials, for example, includes raw materials such as flour, yeast, and water, in addition to the specific infrastructure for producing bread, such as dough mixers and ovens.
In this article, we analyse the importance of bills of materials in the production chain, the way in which they are created and the different types of BOMs.
What’s a bill of materials or BOM?
A bill of materials is the complete list of raw materials, parts and tools needed to manufacture a particular product. BOMs should also include the components and subcomponents that make up the product, as well as the required quantities of each.
The bill of materials also incorporates the exact instructions for the manufacturing process and the product assembly sequence.
The bill of materials shouldn’t be confused with the material take off (MTO), although, at times, they’re referred to synonymously. A BOM is employed in product manufacturing, while an MTO is a similar document used in the construction sector.
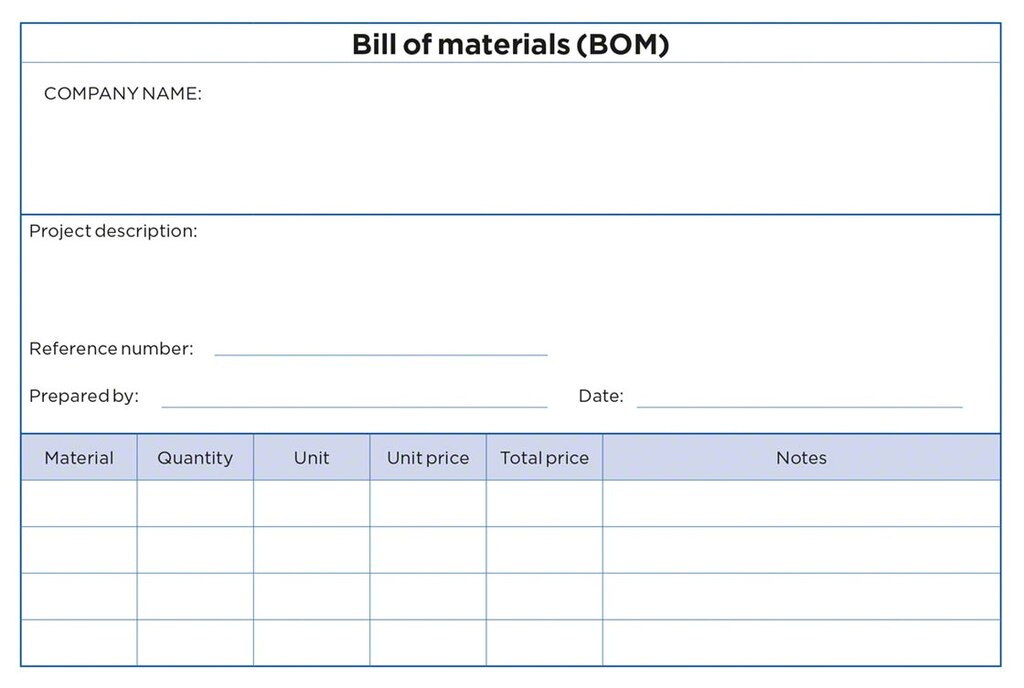
In short, a BOM is an inventory of all the indispensable elements for manufacturing a product. Nowadays, defining the BOM in detail is a key technique for cutting costs in warehouse operations.
What’s the purpose of a bill of materials?
A thorough, well-planned bill of materials ensures the proper supply of the production lines. Warehouses must adapt to demanding production cycles. To make sure the supply chain is coordinated and in sync, the first step for any manufacturer is to adequately prepare a bill of materials.
A well-defined BOM helps companies to:
- Plan purchases of raw materials: the BOM determines which raw materials should be bought to manufacture a product and in what quantities, thereby reducing costs by preventing the overstocking of these goods.
- Establish the cost of the materials: besides raw materials, there’s a cost related to the equipment used to handle those materials, from mere scissors and glue guns to sophisticated cutting machines.
- Avoid stockouts: the production plant must always be equipped with the raw material necessary to manufacture products continuously.
- Detect and minimise errors: the bill of materials sets out each and every one of the processes relating to a product’s manufacture. Following these specific instructions at every step decreases the likelihood of error and makes it easier to detect where and when incidents have occurred (product traceability).
Ultimately, a BOM is a starting point for achieving an optimised, error-free supply chain that operates at full capacity.
Design and structure of a bill of materials
The design of a BOM should be clear and concise. The precise materials used to manufacture the finished product are detailed according to a hierarchical structure: the highest level shows the finished product, while the lower levels display the components and subcomponents.
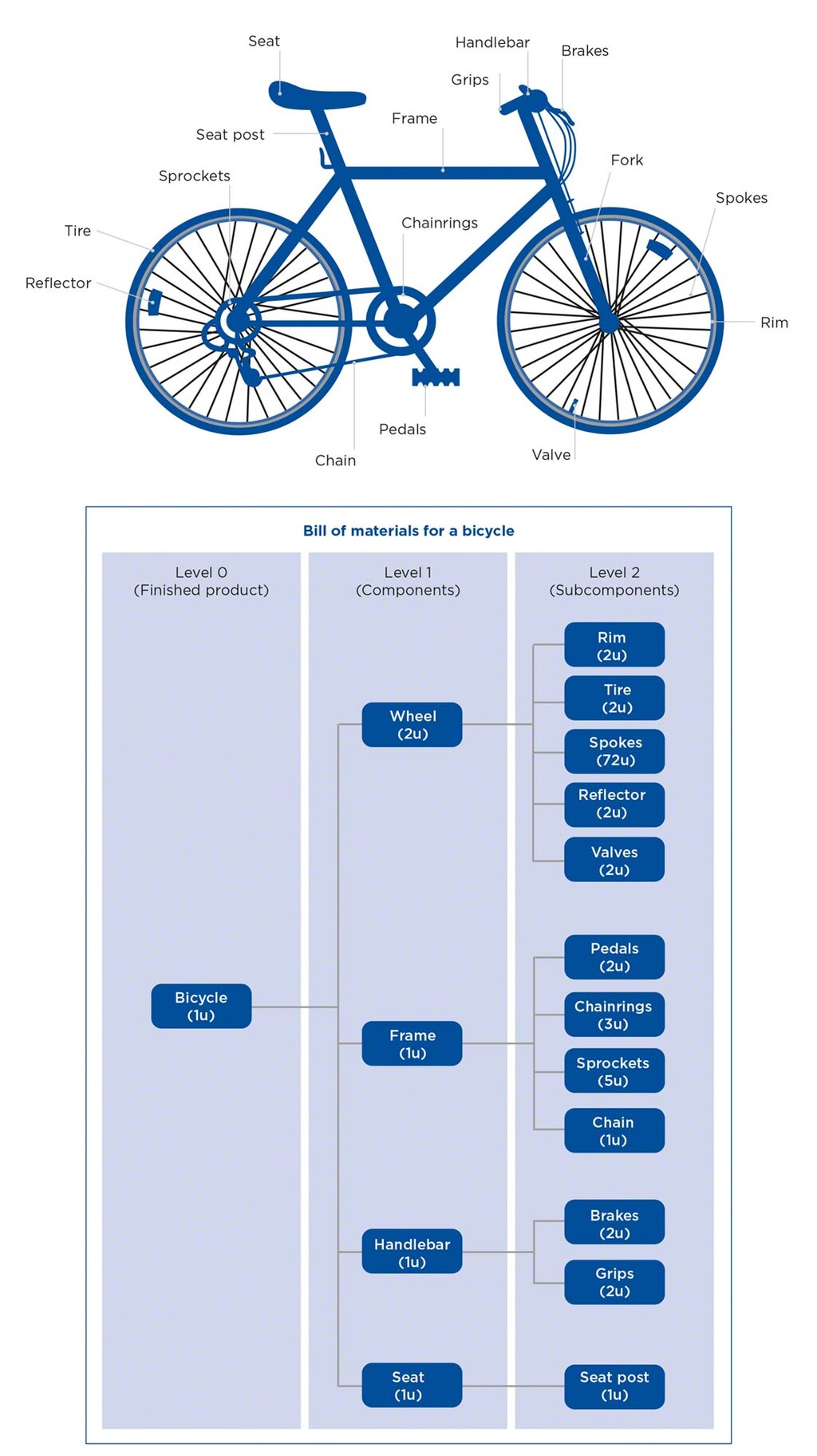
Among the most common methods of depicting a BOM, we can differentiate between two structures, based on the product’s complexity and required level of detail:
- Single-level bill of materials: consists of a non-specific BOM used for products involving a low degree of complexity. This document lists the components and the corresponding quantity required of each to manufacture the final product. An example would be the bill of materials for a table, as it is made up of only four legs, a table top, nuts and bolts.
- Multi-level bill of materials: includes various levels, with their components and subcomponents, as well as the relationship between them and their quantities. All in all, it’s a more detailed list that reflects all the material needed to manufacture a product, as shown in the BOM of a bicycle. The first level includes four components and their required quantities: the gearbox (1), wheels (2), pedals (2) and frame (1). The gearbox and frame, in turn, include subcomponents:
◦ Gearbox: sprockets (5), chainrings (3) and cables (2).
◦ Frame: brakes (2), seat (1), handlebar (1) and fork (1).
Likewise, the bill of materials contains any additional specifications that help to clarify the manufacturing process:
- Level: each material of a BOM is assigned a number corresponding to the hierarchical level of the bill of materials. Level 0 is the final product, 1 the components, 2 the subcomponents, etc. Indicating the level makes it easier to understand the BOM structure.
- ID number: every material, part, or component appearing on the bill of materials is given a number to facilitate quick and easy identification.
- Description: the BOM includes a description of each material or component that helps to better understand, identify and distinguish between the elements it contains.
- Quantity: the number of units required for each component must be specified. This is fundamental for ensuring uninterrupted production.
- Notes: any additional relevant information should be included for the benefit of all BOM stakeholders.
Types of BOMs
Various kinds of bills of materials have been adapted and personalised, according to purpose and business needs. These are the main types:
- MBOM (manufacturing bill of materials): this list contains information on all the exact parts and assemblies that go into making a product, as well as the packaging material required to send the finished item to the customer. The information in the MBOM is used to calculate when the materials should be purchased and when the production order should be issued. MBOMs help the purchasing department to define regular intervals for buying parts and to negotiate better prices with the corresponding suppliers.
- EBOM (engineering bill of materials): project engineers create this list during the design stage. EBOMs are often based on CAD (computer-aided design) or EDA (electronic design automation) drawings. They refer to the way in which a finished product was previously designed. It’s essential to draw up rigorous, exact EBOMs, especially when launching a new product; these documents guarantee the availability of the materials and parts during the manufacture of the item. It’s normal to have more than one EBOM for a product, as the design is subjected to a number of revisions.
- SBOM (service bill of materials): this document brings together the steps for installation and repair, in addition to the serviceable parts that a technical service should take into account to ensure a product’s proper functioning.
- Sales bill of materials: this list provides all the details relating to a finished product prior to its assembly and during the sales phase. In sales BOMs, both the finished product and the components appear as separate items.
In fact, a BOM could be compiled for practically any activity requiring different elements and processes, from cooking a simple stew to manufacturing a sophisticated airplane. Bills of materials are neither exclusive nor independent; that is, it’s possible to draw up more than one BOM to carry out an activity.
BOM software: ERPs and WMSs
It’s vital to use software to automatically control and monitor the proper implementation of a bill of materials.
For decades, BOMs — specifically, MBOMs (manufacturing bills of materials — were managed by systems; in other words, software was charged with planning and managing materials in order to control inventory and production. Over the years, MRP (material requirements planning) systems evolved into modern and more complete ERP (enterprise resource planning) software, which includes tools that control elements related to a product’s manufacture.
In parallel, and compatible with ERPs, are warehouse management systems (WMSs). These offer even more precise and sophisticated tools compared to ERPs to achieve greater throughput in both the production chain and the storage and supply of raw materials, semi-finished goods and finished products.
An example of this is WMS for Manufacturing, available through Mecalux’s Easy WMS. This module enables full integration of the procurement processes relating to the production line with the storage of the finished product. The result is total traceability and stock management, improved cycle times in manufacturing processes and enhanced product quality.
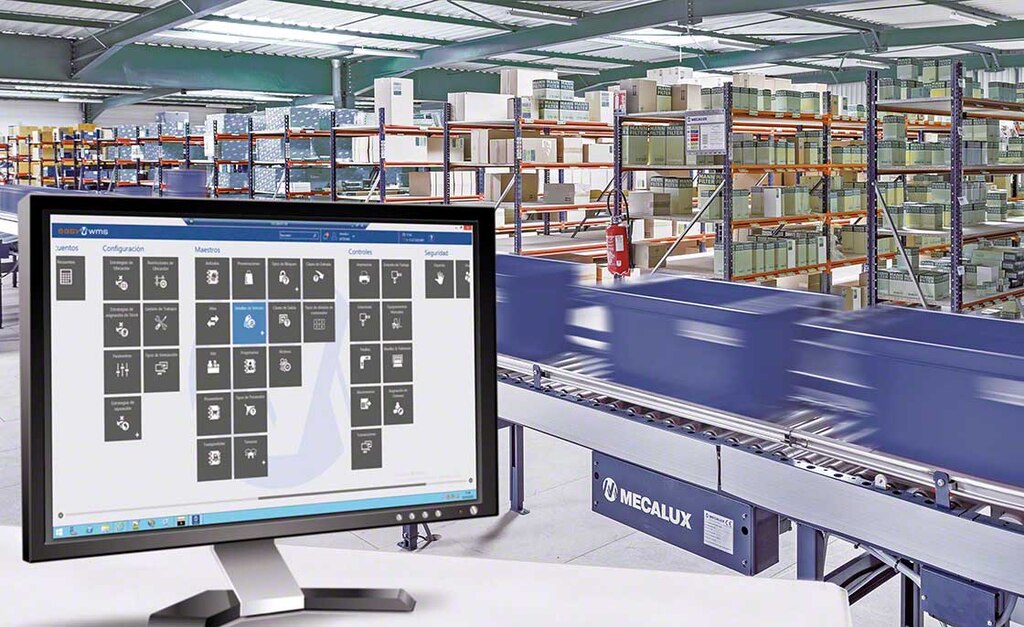
BOMs: logistics and production in sync
All elements involved in the supply chain need to be perfectly optimised and coordinated to achieve the best possible result. In terms of the production chain and logistics, it’s crucial that they work in concert, as the performance of one directly affects the other.
To do this, it’s necessary to have a detailed bill of materials that contains all the information related to the manufacture of a product and that responds to the needs of areas such as the logistics or purchasing department, for instance. In the end, we could say that a BOM is the recipe for a product: the initial and developmental stage that defines all the materials and elements that will be involved in manufacturing the final product.
To ensure effective management of the bill of materials, automation and software are two basic premises. So, don’t hesitate to contact Mecalux — a team of experts will walk you through improving processes in your warehouse.