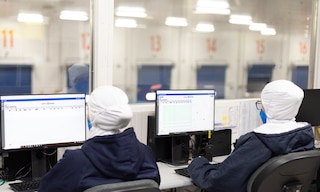
Delivery note: what is it?
A delivery note is a key document when it comes to ensuring a company’s logistics operations run smoothly. This paper lists the products to be loaded onto lorries and subsequently delivered to the final consignee. It’s especially important in warehouses with high dispatch rates.
Implementing a warehouse management system (WMS) automates the management of documents such as delivery notes once orders have been processed. By eliminating manual document management processes, you’ll avoid the risk of error and improve the level of your customer service.
A delivery note is a document that specifies a shipment’s contents. It includes the number of products, their size and their weight. In detailing the products that make up the truckload, this document simplifies goods dispatch. The delivery note identifies the assigned vehicle (by license plate, driver and carrier), the type of products and the exact merchandise. This document also lists the number of parcels with the items they contain and the ideal loading sequence to facilitate delivery.
The delivery note is handed to the carrier, who validates that the list of products on the document matches the goods loaded on the lorry. The list can also be used by customs offices as a voucher when transporting goods across borders.
What does a delivery note include?
A delivery note contains relevant information about the load. It serves both the operator who loads the goods onto the lorry and the carrier who checks the shipment contents before signing the document.
These are the data typically included in the delivery note:
- Code assigned manually or by software.
- Warehouse of origin of cargo.
- Final consignee(s) of the goods.
- Date and time of loading.
- Detailed description of the goods: contents, number of parcels, weight and exact size of each parcel.
- Weight and full size of the shipment.
You can supplement this information with additional data to further control order dispatches, such as the vehicle license plate, the transport agency and the assigned carrier. The document also incorporates the type of goods, especially in cases where transport is crucial for properly preserving the product, as in the chemical and food industries.
Likewise, the delivery note normally specifies the order distribution route. This is vital for the carrier delivering the goods and for the operator who loads the lorry, as products must be inserted in the reverse order of their distribution.
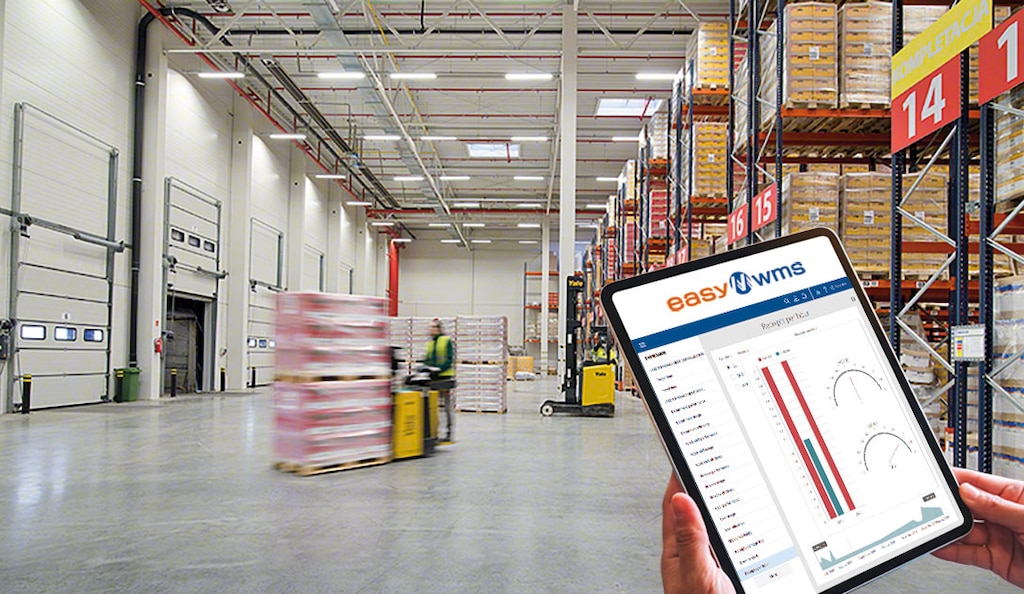
Can delivery notes be digitised?
An advanced logistics application like warehouse management software configures the delivery note to be printed automatically once the lorry loading order has been issued. The process is simple: the software is parameterised beforehand by assigning a printer to the corresponding loading dock and setting the number of copies required.
With advanced WMS software, it’s possible to configure the parameters of the loading process in advance to adapt them to the particular demands of your facility. For instance, the system can determine an assignment rule whereby the delivery note is only generated once the operator has validated the vehicle's license plate number using the RF scanner. Among other functions, the program lets you automate the creation of delivery notes by carrier, generating a list for each one.
In addition, the WMS can connect to other applications, e.g., a distributed order management (DOM) system. From the DOM program, you can access documentation such as delivery notes, waybills and other transport agency data. The DOM system also configures these documents to be printed automatically if necessary.
Logistics software for delivery notes
Swapping paper-based document management for a WMS eliminates data-entry errors and automates the generation and printing of records such as delivery notes, waybills and invoices.
During the loading process, the program acts in the creation of orders and the configuration of the operation. It allows segmentation by type of packaging, grouping by carrier and load validation, among other functions.
A software program like Easy WMS from Mecalux is the perfect tool for facilitating order fulfillment: it connects to RF scanners to guide operators in picking, replenishment and even lorry loading tasks. Moreover, it can interface with other programs such as an ERP or DOM system or carrier apps, ruling out the possibility of mistakes in goods management.
Digitisation to eliminate errors in document management
Implementing a WMS fosters efficient, productive logistics operations. Besides automating document management, the software helps operators in goods receipt, order picking and dispatch tasks. It coordinates all processes, both in manually run facilities and automated warehouses.
Easy WMS, the software from Mecalux, is a scalable, cloud-accessible program that orchestrates operations in more than 1,000 facilities in 36 countries. Interested in digitising your processes and eliminating mistakes in logistics document management? Don’t hesitate to contact us. One of our expert software consultants will work with you on the best solution for your warehouse.